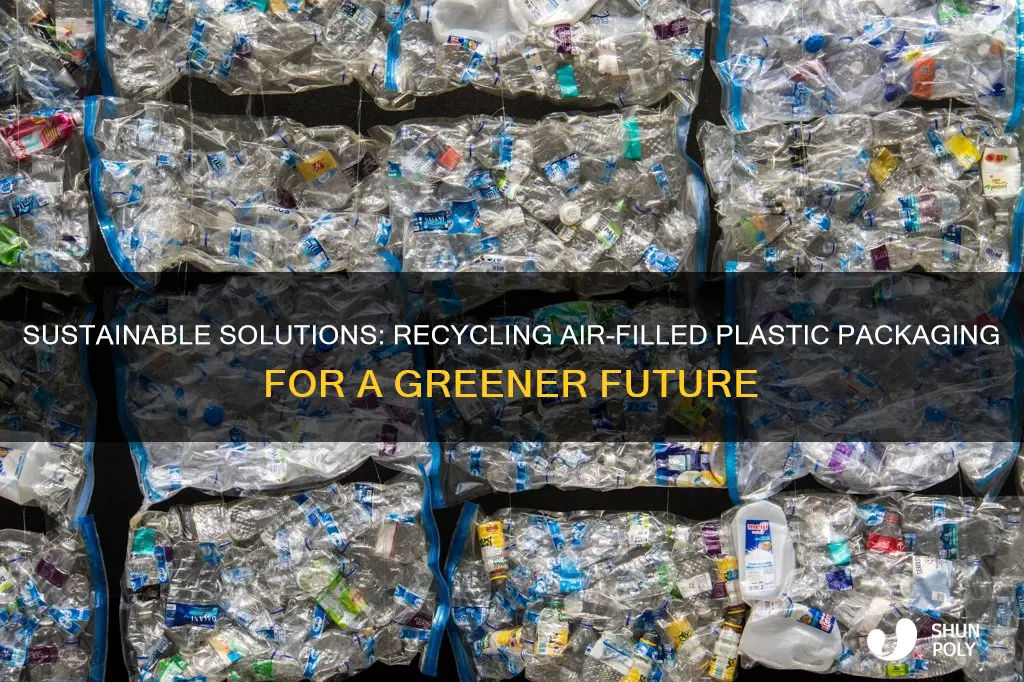
Recycling air-filled plastic packaging is an essential practice to reduce environmental impact and promote sustainability. This process involves transforming used plastic containers, such as those used for shipping and storage, into new materials. By understanding the recycling process, consumers and businesses can contribute to a greener future. The following guide will outline the steps to effectively recycle air-filled plastic packaging, including proper disposal methods, collection systems, and the potential for upcycling into new products.
What You'll Learn
Collection: Gather and sort plastic waste for recycling
The first step in the recycling process for air-filled plastic packaging is the collection and sorting of plastic waste. This initial phase is crucial as it sets the foundation for the entire recycling journey. Here's a detailed guide on how to effectively gather and sort plastic waste:
Collection:
- Identify Sources: Begin by recognizing the sources of plastic waste in your area. This includes residential areas, offices, retail stores, and any other places where plastic packaging is commonly used. For instance, you might collect from homes, local businesses, or even set up collection points at events or community centers.
- Gathering Waste: Encourage people to set aside their used plastic packaging. This can be done by providing designated bins or containers specifically for plastic waste. Make sure these bins are easily accessible and clearly labeled to promote proper waste segregation.
- Community Engagement: Involve the community in the collection process. You can organize drives or campaigns where volunteers collect plastic waste from various locations. This not only helps in gathering a large volume of waste but also raises awareness about recycling.
Sorting:
- Separate by Type: Once the collection is complete, the next critical step is sorting. Plastic waste should be sorted into different categories based on the type of plastic. Common types include PET (polyethylene terephthalate), HDPE (high-density polyethylene), PVC (polyvinyl chloride), LDPE (low-density polyethylene), and PP (polypropylene). Each type has specific recycling methods and applications.
- Use Color-Coding or Labels: Implement a color-coding system or clearly label the bins for each plastic type. For example, use blue for PET, green for HDPE, and so on. This simple method makes sorting more efficient and reduces the chances of contamination.
- Educate on Sorting: Provide guidance to the community on proper sorting techniques. You can create informative materials or conduct workshops to teach people how to identify and separate different types of plastics. This ensures that the sorted waste is of high quality and suitable for recycling.
By following these collection and sorting practices, you are taking significant steps towards recycling air-filled plastic packaging. This process ensures that the waste is managed effectively, making it ready for the subsequent recycling stages, which may involve cleaning, processing, and transforming the sorted plastics into new products.
Unveiling the Journey: From Trash to Treasure: Plastic Container Recycling
You may want to see also
Cleaning: Rinse and remove contaminants from plastic packaging
Cleaning plastic packaging before recycling is an essential step to ensure the process is effective and the final product is of good quality. Here's a detailed guide on how to properly clean and prepare plastic packaging for recycling:
Rinsing Process: Begin by thoroughly rinsing the plastic packaging under running water. Use a gentle stream of water to wash the inside and outside of the container. Ensure that you remove any visible food residue, liquid remnants, or any other contaminants. The goal is to eliminate any potential impurities that might interfere with the recycling process. For example, if the packaging contained a greasy snack, make sure to rinse it multiple times to get rid of the grease.
Scrubbing and Brushing: In some cases, a simple rinse might not be enough. If there are stubborn stains or dried-on food particles, use a soft-bristled brush or a non-abrasive sponge to gently scrub the packaging. Focus on areas where contaminants are most likely to accumulate, such as the corners, seams, and crevices. Be careful not to damage the plastic during this step.
Drying: After rinsing and scrubbing, it is crucial to dry the plastic packaging thoroughly. Moisture can attract bacteria and cause odors, which can contaminate other recyclables in the same bin. Use a clean towel or air-dry the packaging in a well-ventilated area. Ensure that the packaging is completely dry before proceeding to the next step.
Removing Non-Plastic Components: Plastic packaging often includes non-plastic parts like labels, caps, or seals. These components may have different recycling requirements and can sometimes contaminate the plastic if not removed. Carefully peel off any non-plastic labels or caps, and dispose of them appropriately. If the packaging has a sealed inner layer, make sure to open it to access the main plastic container.
Final Rinse (Optional): Depending on the level of contamination, you might consider giving the packaging a final rinse with warm water to ensure no residue remains. This step is especially useful if you are recycling a large quantity of packaging and want to maintain high standards of cleanliness.
By following these cleaning procedures, you contribute to a more efficient recycling system and help maintain the integrity of the recycled plastic materials. Proper cleaning ensures that the recycled products meet the required standards and can be used for various applications, promoting a more sustainable approach to waste management.
Unraveling the Mystery: Can Plastic Tape Dispensers Be Recycled?
You may want to see also
Shredding: Break down plastic into small pieces for processing
Shredding is a crucial step in the recycling process for air-filled plastic packaging, as it prepares the material for further processing and ensures efficient recycling. This method involves breaking down the plastic into small, manageable pieces, which can then be sorted, cleaned, and transformed into new products. Here's a detailed guide on how to shred air-filled plastic packaging effectively:
Equipment and Preparation:
- Start by gathering the appropriate shredding equipment. Industrial shredders are ideal for this task as they can handle large volumes of plastic and produce consistent results. These machines can be configured to create different-sized shreds, depending on the desired outcome.
- Sort the air-filled plastic packaging by type and color if you have a variety of plastics. This step is essential to ensure that the shredded material can be recycled effectively and to maintain the quality of the final product.
Shredding Process:
- Begin by feeding the plastic packaging into the shredder. Ensure that the material is fed evenly and at a steady rate to avoid overloading the machine.
- Adjust the shredder settings to achieve the desired particle size. For air-filled plastics, a finer shred is often preferred as it allows for better processing and recycling. Smaller shreds also increase the surface area, facilitating the removal of air bubbles and improving the material's recyclability.
- As the shredding process begins, the plastic packaging will be reduced to tiny pieces. The shredder's rotating blades will break down the material, separating it from the air bubbles. This step is crucial as it helps to eliminate the air pockets, making the plastic more compact and easier to handle.
- Monitor the shredding process to ensure that the desired particle size is achieved. Regularly check the output to prevent over-shredding, which can lead to inconsistent results and potential quality issues in the recycled material.
Post-Shredding Handling:
After shredding, the plastic material will be in a granular form, ready for further recycling processes. This shredded plastic can then be conveyed to a sorting system, where it is separated by type and cleaned to remove any contaminants. The clean, sorted plastic can be sold to manufacturers for creating new products, such as composite lumber, new packaging, or even construction materials.
Shredding is a critical step in recycling air-filled plastic packaging, as it transforms the material into a usable form, ready for the recycling stream. This process requires specialized equipment and careful monitoring to ensure the best results, ultimately contributing to a more sustainable approach to plastic waste management.
The Green Hanger Revolution: Recycle Plastic Hangers for a Greener Wardrobe
You may want to see also
Melting: Heat and melt plastic to create new materials
Melting plastic is a crucial step in the recycling process, especially for air-filled plastic packaging. This method involves heating the plastic to a specific temperature, allowing it to transform from a solid state into a liquid, and then shaping it into new forms. Here's a detailed guide on how to melt plastic for recycling:
Step 1: Sorting and Cleaning
Before melting, ensure that the air-filled plastic packaging is properly sorted and cleaned. Separate different types of plastics to facilitate the melting process. For instance, common types of plastics used in packaging include PET (polyethylene terephthalate) and HDPE (high-density polyethylene). Clean the packaging by removing any dirt, labels, or non-plastic components. This step is essential to ensure the purity of the recycled material.
Step 2: Shredding or Granulating
The plastic packaging is then shredded or granulated to reduce its size. Shredding involves cutting the plastic into small pieces, which can be done using specialized machinery. This process increases the surface area of the plastic, making it easier to melt and form into new products. Alternatively, granulating produces small, uniform pellets of plastic, which are easier to handle and melt. Both methods help in preparing the plastic for the melting stage.
Step 3: Melting Process
Melting plastic requires precise temperature control. The ideal temperature range for melting common plastics is between 230°C to 270°C (446°F to 518°F). This temperature varies depending on the type of plastic. For instance, PET melts at around 255°C (500°F), while HDPE has a melting point of approximately 129°C to 135°C (264°F to 275°F). Use a controlled heating environment, such as a melting furnace or a specialized plastic melting machine, to ensure accurate temperature management. The plastic will start to soften and eventually turn into a liquid state.
Step 4: Molding and Shaping
Once the plastic is melted, it can be molded and shaped into new products. This step involves pouring the molten plastic into molds or using injection molding machines. The temperature and time of the melting process are critical to ensure the plastic can flow easily into the desired shape. After cooling, the molded plastic can be used to create various items, such as new packaging, furniture, or even construction materials.
Melting plastic for recycling is an energy-intensive process, so it's essential to have the right equipment and expertise to handle the heat and pressure involved. Proper recycling techniques not only help in creating new materials but also contribute to reducing environmental waste and promoting a circular economy.
Sweet Tub Recycling: Unwrapping the Plastic Conundrum
You may want to see also
Molding: Form recycled plastic into new products
Molding is a crucial process in recycling and repurposing air-filled plastic packaging, allowing us to transform these materials into new, useful products. This method involves shaping and forming the recycled plastic into various desired shapes and structures, which can then be utilized in numerous applications. Here's a detailed guide on how molding can be achieved:
Collection and Sorting: The first step is to collect air-filled plastic packaging, which can include items like air pillows, bubble wraps, or other lightweight plastic packaging materials. These items are then sorted based on their type and quality. High-quality plastics are preferred for molding as they can withstand the processing temperatures and pressures involved.
Cleaning and Shredding: Before molding, the plastic packaging needs to be cleaned to remove any contaminants. This process ensures that the recycled plastic is free from dirt, dust, and other impurities. After cleaning, the plastic is shredded into small pieces or flakes. This step reduces the plastic into a manageable size, making it easier to handle and process.
Melting and Extrusion: The shredded plastic is then fed into a melting machine, where it is heated to its melting point. This process transforms the solid plastic into a molten state, allowing it to be shaped and molded. The molten plastic is then extruded through a die or mold, which gives it the desired shape. This step requires precise control of temperature and pressure to ensure the plastic takes the form of the mold.
Molding Process: Molding can be achieved through various techniques, including injection molding, blow molding, and compression molding. In injection molding, the molten plastic is injected into a mold, which then cools and solidifies, taking the shape of the mold. This method is versatile and can produce complex shapes. Blow molding is used for hollow products, where the molten plastic is blown into a mold to create a hollow structure. Compression molding involves heating and compressing the plastic in a mold, which is then cooled to form the desired product.
Cooling and Ejection: After the molding process, the plastic parts are allowed to cool and solidify. The cooling time depends on the material and the desired hardness of the product. Once cooled, the molded parts are carefully ejected from the mold. This step requires careful handling to avoid damage to the product.
Post-Processing and Finishing: The molded products may undergo additional finishing processes to enhance their appearance and functionality. This can include trimming excess material, adding decorative elements, or applying a protective coating. Post-processing ensures that the final product meets the required specifications and is ready for its intended use.
Molding offers a sustainable approach to recycling air-filled plastic packaging, allowing us to create new products with reduced environmental impact. By utilizing this process, we can contribute to a circular economy, reducing waste and promoting the reuse of valuable resources.
HDPE Plastic: Recycling Guide and Tips
You may want to see also
Frequently asked questions
Recycling air-filled plastic packaging involves a few steps. First, the packaging is collected and sorted based on its material and type. Then, it is cleaned to remove any contaminants or non-plastic materials. After cleaning, the plastic is shredded or granulated to reduce its size and make it easier to process. The shredded plastic is then melted and molded into new products or used as feedstock for manufacturing various items.
Not all air-filled plastic packaging is recyclable in the same way. The most commonly recycled types include polyethylene (PE) and polypropylene (PP) packaging, such as bubble wrap, air pillows, and foam sheets. These materials are widely accepted by recycling programs and can be processed into new products. However, some packaging, like polystyrene (PS) or expanded polystyrene (EPS), might have limited recycling options due to their lightweight nature and potential contamination from air bubbles.
To prepare air-filled plastic packaging for recycling, start by ensuring it is clean and dry. Remove any non-plastic components, such as tape or labels, and flatten the packaging if possible to save space. For bubble wrap or air pillows, try to collect a significant amount to make the recycling process more efficient. Flattening or rolling the packaging can also help with transportation and processing. Always check with your local recycling guidelines to understand specific requirements for different types of plastic.
Yes, recycling air-filled plastic packaging offers several environmental advantages. It helps reduce the demand for new plastic production, which often relies on fossil fuels and can have a significant environmental impact. By recycling, you contribute to conserving natural resources, reducing energy consumption, and lowering greenhouse gas emissions associated with manufacturing new plastics. Additionally, proper recycling prevents plastic waste from ending up in landfills or polluting natural habitats.