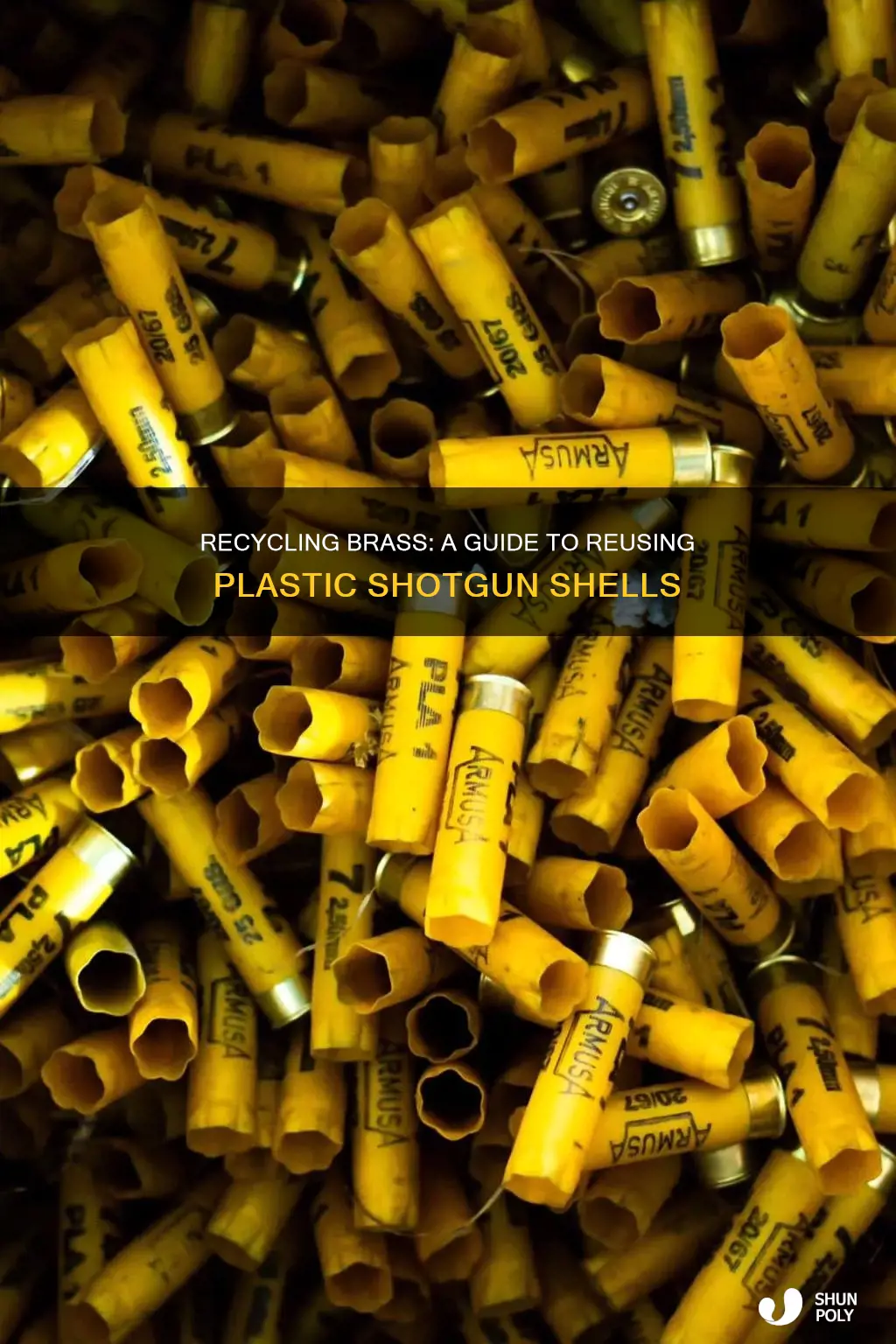
Recycling brass from plastic shotgun shells is an eco-friendly practice that can help reduce waste and promote sustainability. This process involves separating the brass casings from the plastic components of the shells, which can then be melted down and repurposed into new products. By doing so, we can minimize the environmental impact of manufacturing and dispose of shotgun shells while also contributing to a circular economy. This guide will provide a step-by-step approach to effectively recycle brass from plastic shotgun shells, ensuring a responsible and efficient recycling process.
What You'll Learn
- Collection and Sorting: Gather used shells, separate brass from plastic components
- Cleaning and Inspection: Rinse brass, remove debris, check for damage or contamination
- Melting and Alloying: Melt brass, mix with new metal, cast into new shapes
- Machining and Forming: Machine brass into new products, like jewelry or tools
- Finishing and Coating: Polish, coat, and protect the recycled brass for durability
Collection and Sorting: Gather used shells, separate brass from plastic components
The process of recycling brass from plastic shotgun shells begins with a careful and organized collection and sorting system. This initial step is crucial to ensure that the recycling process is efficient and effective. Here's a detailed guide on how to approach this:
Collection: Start by gathering used shotgun shells from various sources. This can include shooting ranges, sports clubs, or even personal collections. Encourage shooters to return their spent shells to a designated collection point. It is important to collect a significant volume to make the recycling process viable. Consider providing containers or bags for shooters to deposit their used shells, ensuring a steady supply for recycling.
Sorting and Separation: Once you have a substantial collection, it's time to sort and separate the components. This step requires attention to detail and organization. Here's a breakdown:
- Identify Components: Each shotgun shell consists of two main parts: the brass casing and the plastic (or paper) body. Familiarize yourself with the different materials to ensure proper separation.
- Manual Sorting: Begin by manually sorting the shells. Place the brass casings in one pile and the plastic components in another. This process can be done by hand or with the help of a team, ensuring a systematic approach.
- Remove Contaminants: During the sorting process, inspect the shells closely. Remove any non-brass and non-plastic items, such as spent gunpowder, wadding, or any foreign objects that may have been accidentally included. This step ensures that the recycling process is clean and efficient.
- Sub-Categorize (Optional): For more advanced recycling, you can further categorize the brass and plastic components. For instance, separate different types of brass (e.g., different calibers or brands) to potentially cater to specific recycling requirements.
By implementing a structured collection and sorting system, you lay the foundation for a successful recycling process, ensuring that the brass and plastic components are ready for the next stage of recycling or reuse. This methodical approach is essential to handle the unique challenges of recycling shotgun shell components.
Mastering the Art of Recycling: A Guide to Transforming Plastic Waste
You may want to see also
Cleaning and Inspection: Rinse brass, remove debris, check for damage or contamination
The process of recycling brass from plastic shotgun shells begins with thorough cleaning and inspection to ensure the material is ready for reuse. Here's a detailed guide on how to approach this step:
Rinsing the Brass: Start by thoroughly rinsing the brass components under running water. This initial step is crucial to remove any loose debris, dirt, or residue that may have accumulated during the shell's usage. Use a gentle stream of water to avoid forcing water into small crevices. Pay close attention to the internal threads and any small openings to ensure no contaminants remain. For more stubborn dirt, consider using a mild detergent or dish soap, but ensure it is thoroughly rinsed afterward to avoid any chemical residue.
Debris Removal: After rinsing, inspect the brass for any visible debris or particles. Plastic shotgun shells can sometimes leave small fragments of plastic or gunpowder residue. Use a soft-bristled toothbrush or a small brush to gently scrub the brass, removing any remaining debris. Be cautious not to scratch the surface, especially on the firing pin and extractor areas, as these components require precise cleaning.
Damage and Contamination Check: Carefully examine each brass component for any signs of damage or contamination. Look for bent or warped cases, as these may not function properly in a firearm. Check for any visible corrosion or rust, especially on the internal surfaces, as this can affect the performance and longevity of the ammunition. Additionally, inspect for any signs of contamination, such as oil or grease residue, which can impact the reliability of the firing process. If any significant damage or contamination is detected, it may be necessary to replace the component or perform additional cleaning steps.
During this inspection process, it's essential to maintain a clean and organized workspace to avoid cross-contamination. Ensure that all tools and brushes used for cleaning are properly cleaned and dried to prevent the introduction of new contaminants. This meticulous cleaning and inspection phase is vital to guarantee the quality and functionality of the recycled brass components.
The Truth About Plastic Recycling: Unveiling the Green Lie
You may want to see also
Melting and Alloying: Melt brass, mix with new metal, cast into new shapes
The process of recycling brass from plastic shotgun shells involves a few key steps, with melting and alloying being a crucial part of the transformation. Here's a detailed guide on how to achieve this:
Melting Brass: Begin by collecting and sorting the brass components from the shotgun shells. This includes the brass cases, which are the most valuable part for recycling. Use a small crucible or a dedicated melting pot to heat the brass. It's important to use a controlled flame or a heat source that can reach the required temperature for melting. The melting point of brass is around 900-950°C (1652-1742°F), so ensure your heat source can accurately control this temperature range. As the brass melts, it will form a liquid state, and you can use a ladle or a similar tool to collect and pour it into a mold or a designated container.
Alloying and Mixing: Once you have a batch of melted brass, you can introduce new metals to create different alloys, depending on your desired properties. For instance, adding copper can strengthen the brass, making it more durable. Here's a simple process:
- Prepare the Alloy: Measure and weigh the desired amount of new metal (e.g., copper, zinc) and add it to the melted brass. Use a precision scale to ensure accurate measurements.
- Stir and Heat: Gently stir the mixture to ensure even distribution of the new metal. You can use a heat source to maintain a specific temperature, especially if you're adding reactive metals that may require specific conditions to avoid unwanted reactions.
- Refine the Alloy: Depending on the complexity of the alloy, you might need to refine the mixture further. This could involve additional heating, stirring, or even using a furnace with precise temperature control.
Casting and Shaping: After the alloying process, it's time to cast the material into new shapes. This step allows you to create various products or components:
- Prepare Molds: Design or acquire molds that match the desired shape of your final product. Silicone molds are a popular choice for this process.
- Pour the Alloy: Carefully pour the molten brass alloy into the prepared molds. Ensure the molds are preheated to a specific temperature to facilitate proper casting.
- Cooling and Removal: Allow the alloy to cool and solidify within the molds. Once set, carefully remove the molds to reveal the newly cast brass shapes.
- Finishing: Depending on the application, you might need to perform additional finishing processes like sanding, polishing, or further heat treatment to enhance the brass's properties.
This method of recycling and reusing brass from shotgun shells not only reduces waste but also allows for the creation of new products, promoting a more sustainable approach to material management. It's a detailed process that requires precision and control, but the results can be valuable for various industrial and artistic applications.
Unveiling US Plastic Recycling Costs: A Financial Analysis
You may want to see also
Machining and Forming: Machine brass into new products, like jewelry or tools
Recycling brass from plastic shotgun shells is an eco-friendly practice that can be transformed into various useful and aesthetically pleasing items. Machining and forming techniques are essential processes to shape the recycled brass into new products, such as jewelry, decorative pieces, or even functional tools. Here's an overview of the process:
Machining the Brass: The first step is to remove the plastic from the brass casings. This can be done by carefully cutting or grinding the plastic base to expose the pure brass. Once the plastic is removed, the brass casings can be cleaned thoroughly to ensure no contaminants remain. Machining involves using precision tools to shape and refine the brass. This process can be done on a lathe, a machine that rotates the brass piece while applying cutting tools to shape it. The machinist can create smooth, rounded edges, intricate designs, or even complex shapes like gears or decorative patterns. For jewelry-making, this step is crucial to achieve the desired aesthetic and structural integrity.
Forming and Fabrication: After machining, the brass can be formed into various shapes and sizes. This process often utilizes metal forming techniques such as stamping, bending, or casting. For instance, you can create brass jewelry by cutting and bending the metal into the desired shape, such as a pendant or a bracelet. The forming process might involve using a die to press the brass into a specific shape, ensuring the material is malleable enough to work with. Alternatively, casting can be employed to create intricate designs, where molten brass is poured into a mold to take the desired form. This method is particularly useful for creating custom shapes and patterns.
Finishing and Polishing: To enhance the appearance and durability of the brass products, finishing and polishing techniques are applied. This step involves removing any remaining burrs, smoothing the surface, and adding a protective coating. Polishing the brass can give it a shiny, reflective finish, making it suitable for jewelry or decorative items. You can use various polishing compounds and techniques, such as chemical polishing or buffing, to achieve the desired level of shine and smoothness.
Creating Functional Items: Beyond jewelry, the recycled brass can be utilized to create functional tools and accessories. For example, you can machine and form brass into keychains, bottle openers, or even small tools like screwdrivers or wrenches. These items can be designed with specific functions in mind, ensuring the brass provides the necessary strength and durability. Machining can be used to create precise, ergonomic shapes, making the tools comfortable and efficient to use.
By employing these machining and forming techniques, you can transform recycled brass from plastic shotgun shells into valuable, eco-conscious products. This process not only reduces waste but also encourages creativity and resourcefulness in crafting unique and useful items. It is a sustainable approach to recycling that can inspire further exploration of material reuse in various industries.
Atlanta's Recycling Hub: Glass, Plastic, and More
You may want to see also
Finishing and Coating: Polish, coat, and protect the recycled brass for durability
The process of recycling brass from plastic shotgun shells involves not only separating the materials but also ensuring the final product is durable and aesthetically pleasing. Finishing and coating the recycled brass are crucial steps to achieve this. Here's a detailed guide on how to polish, coat, and protect the brass for long-lasting results:
Polishing the Brass: Start by cleaning the brass thoroughly to remove any dirt or debris. Use a mild abrasive such as fine sandpaper or a polishing compound specifically designed for brass. Gently rub the brass surface in a circular motion, ensuring you cover the entire area. Polishing will not only enhance the brass's natural shine but also create a smooth surface, making it more receptive to the coating. Pay attention to any sharp edges or crevices, as these areas might require extra care to avoid scratches. Consider using a polishing wheel or a small brush to reach into tight spaces and ensure an even finish.
Coating Application: After polishing, it's time to coat the brass to add protection and enhance its appearance. There are various coating options available, such as electroplating, powder coating, or clear acrylic sprays. For a professional finish, electroplating with a bright nickel or chrome coating is an excellent choice. This process involves submerging the brass in an electrolytic solution and applying an electric current, resulting in a smooth, protective layer. Alternatively, powder coating provides a durable, scratch-resistant finish and is often used for its ability to adhere well to the brass surface. If you prefer a simpler method, clear acrylic spray can be applied in multiple thin coats, allowing each layer to dry before adding the next, resulting in a smooth, glossy finish.
Protective Measures: To ensure the longevity of the coated brass, additional protective steps can be taken. Consider applying a clear, protective wax or sealant to the coated surface. This will add an extra layer of defense against corrosion and wear. For outdoor applications or highly exposed environments, consider using a rust-inhibiting primer before applying the final coat. This primer will create a barrier, preventing corrosion and ensuring the brass remains protected even in harsh conditions. Additionally, regular maintenance and re-coating can extend the life of the brass, especially if it is used frequently or exposed to the elements.
By following these finishing and coating techniques, you can transform recycled brass from plastic shotgun shells into a durable and visually appealing material. The process requires attention to detail and the right tools, but the result will be a high-quality, recycled product ready for various applications, from decorative pieces to functional hardware.
Unstain the Past: A Guide to Removing Stains from Recycled Plastic Shirts
You may want to see also
Frequently asked questions
To recycle brass from plastic shotgun shells, you can start by carefully removing the brass casing from the shell. This can be done by hand or with the help of small tools like a pair of pliers or a small hammer. Be cautious not to damage the brass during this process. Once separated, you can rinse the brass under running water to remove any remaining gunpowder residue. Then, you can place the clean brass in a designated recycling bin for metal.
Yes, proper cleaning is essential to ensure the brass is recyclable. After removing the brass, rinse it thoroughly with water to eliminate any remaining gunpowder or debris. You can use a mild detergent or dish soap to help with the cleaning process. Make sure to rinse the brass multiple times to remove any soap residue. This step is crucial to prevent contamination and ensure the brass can be recycled effectively.
Recycling the plastic part of the shotgun shell depends on your local recycling guidelines. Some recycling centers may accept plastic shotgun shell casings, but it's best to check with your local facility to confirm. If your local recycling program accepts plastic, you can rinse the plastic to remove any residue and then recycle it accordingly. However, if your area doesn't have specific plastic recycling options, consider reusing or disposing of the plastic part responsibly, ensuring it doesn't end up in landfills.