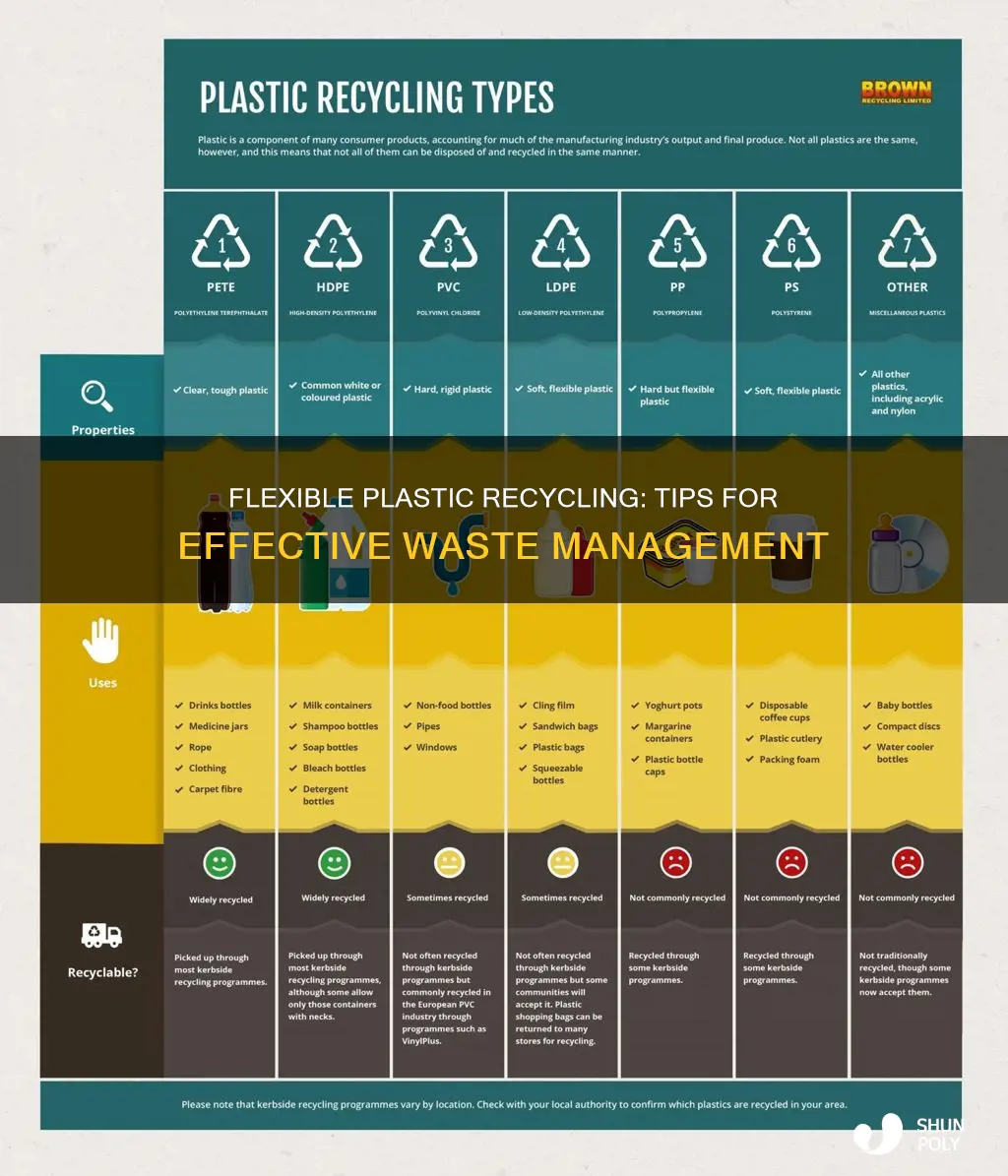
Flexible plastic, often overlooked, plays a crucial role in recycling efforts. Unlike rigid plastic, flexible materials like food packaging, shopping bags, and bubble wrap require specific recycling methods. This guide will explore the process of recycling flexible plastics, including the challenges and best practices. It will also provide tips on how to properly prepare and dispose of these items to ensure they are recycled effectively and contribute to a more sustainable future.
What You'll Learn
- Sorting: Separate flexible plastics by type and color for efficient recycling
- Cleaning: Rinse and dry to remove contaminants and ensure quality
- Shredding: Break down flexible plastics into small pieces for processing
- Melting: Heat and melt plastic to create new materials
- Re-granulation: Transform melted plastic into reusable pellets for manufacturing
Sorting: Separate flexible plastics by type and color for efficient recycling
The process of recycling flexible plastics begins with proper sorting, which is a crucial step to ensure efficient and effective recycling. This practice involves categorizing different types of flexible plastics based on their composition and color, allowing for more streamlined recycling processes. Here's a detailed guide on how to sort flexible plastics for recycling:
Identify Plastic Types: Flexible plastics can be broadly categorized into a few common types, including polypropylene (PP), low-density polyethylene (LDPE), and high-density polyethylene (HDPE). PP is often used in food containers and packaging, while LDPE is commonly found in shopping bags and film wraps. HDPE is prevalent in milk jugs and shampoo bottles. Understanding these types is essential for proper sorting.
Separate by Color: Flexible plastics also vary in color, and sorting by color is an important practice. Different colors may have distinct recycling pathways or be processed differently in recycling facilities. For instance, clear or translucent LDPE bags and film wraps can be recycled together, while black or dark-colored HDPE containers might require separate processing. Create color-coded bins or bags to make sorting easier.
Create a Sorting System: Develop a systematic approach to sorting. Designate separate bins or containers for each type of flexible plastic and color category. Clearly label these bins to ensure that everyone involved in the recycling process understands the sorting guidelines. For example, you could have a bin labeled "Clear LDPE Film" for translucent LDPE bags and another labeled "Black HDPE Containers" for dark-colored HDPE items.
Educate and Train: Provide clear instructions and education to all participants in the recycling process. This is especially important in household or community recycling programs. Teach individuals how to identify different plastic types and colors and encourage them to place items in the appropriate bins. You can also provide visual guides or posters to assist with the sorting process.
Consistency is Key: Consistency in sorting practices is vital for efficient recycling. Ensure that the sorting system is followed consistently by all contributors. This consistency will help recycling facilities process the materials more effectively, reducing contamination and improving the overall recycling rate for flexible plastics.
By implementing a structured sorting system that considers both plastic types and colors, you contribute to a more sustainable approach to recycling flexible plastics. This methodical process ensures that the recycling stream is organized, making it easier for recycling centers to process and transform these materials into new products.
Unraveling the Mystery: Can Plastic Air Mattresses Be Recycled?
You may want to see also
Cleaning: Rinse and dry to remove contaminants and ensure quality
Cleaning and preparing flexible plastic for recycling is a crucial step to ensure the process is efficient and effective. This step involves removing any contaminants and ensuring the material is clean and dry before it can be recycled. Here's a detailed guide on how to perform this task:
Rinsing: Begin by thoroughly rinsing the flexible plastic items. This process helps eliminate any food residue, dirt, or other debris that might be present. Use warm water and a gentle detergent or dish soap to create a soapy solution. The goal is to create a mild cleaning agent that can effectively lift away any contaminants. For example, if you're dealing with flexible plastic packaging, rinse it under running water to remove any visible dirt or food particles. Ensure that you clean both the inside and outside of the packaging to maintain hygiene. For smaller items like plastic bags or wraps, you can soak them in the soapy water to ensure a more thorough clean.
When rinsing, pay attention to the nozzles or openings of the plastic items. These areas can trap contaminants, so make sure to direct the water flow carefully to avoid pushing dirt further into the material. Rinsing should be done gently to prevent any damage to the plastic, especially for flexible materials that can be more prone to tearing.
Drying: After rinsing, proper drying is essential to remove any remaining moisture and ensure the plastic is ready for recycling. Start by gently patting the plastic items with a clean towel to remove excess water. Avoid rubbing or scrubbing, as this can create friction and potentially damage the material. For a more thorough drying process, you can use a hairdryer on a low setting. Hold the hairdryer a few inches away from the plastic to prevent overheating and potential warping. Focus the air on the wet areas, moving the dryer in a circular motion to ensure even drying.
For larger items or multiple pieces, consider laying them out on a flat surface to air-dry. This method is gentle and allows for proper ventilation, ensuring the plastic dries completely without the risk of moisture retention. Once dry, the plastic should feel smooth and soft to the touch, indicating that it is ready for the next step in the recycling process.
By following these cleaning procedures, you contribute to the overall quality of the recycling process, ensuring that the flexible plastic is free from contaminants and ready for its new life as a recycled product. This step is often overlooked but plays a vital role in maintaining the integrity of the recycling system.
Black Plastic Hangers: Can They Be Recycled?
You may want to see also
Shredding: Break down flexible plastics into small pieces for processing
Shredding is a crucial step in the recycling process for flexible plastics, as it prepares these materials for further processing and ensures they can be effectively recycled. This method involves breaking down the plastic into small, manageable pieces, which is essential for several reasons. Firstly, it reduces the size of the plastic, making it easier to handle and transport. Smaller pieces are more manageable and can be processed more efficiently, especially in recycling facilities that may have specific requirements for material size. This step is particularly important for flexible plastics, which can be challenging to recycle due to their unique properties.
The shredding process typically begins with sorting the flexible plastics by type and color. This initial sorting is vital to ensure that the shredded material can be recycled effectively. Different types of flexible plastics, such as those used for shopping bags, wrappings, or packaging, may have varying recycling methods and requirements. By sorting them, recyclers can optimize the shredding process and ensure that the resulting material is suitable for the intended recycling stream. For example, high-density polyethylene (HDPE) and polypropylene (PP) are commonly used for shopping bags and can be shredded into similar-sized pieces to facilitate their recycling.
Once sorted, the flexible plastics are fed into a shredding machine, which can vary in design depending on the recycling facility's needs. Some machines use rotating blades to cut the plastic into thin strips, while others employ a granulating process, turning the plastic into small, uniform pellets. The choice of shredding method depends on the desired outcome and the specific recycling process. For instance, if the goal is to create a raw material for new plastic products, a more precise shredding technique might be employed to produce smaller, consistent pieces.
After shredding, the plastic pieces are often further processed to remove any contaminants or impurities. This step ensures that the recycled material meets the required standards for its intended use. Contaminants can include labels, stickers, or other non-plastic materials that may have been attached to the original product. Removing these impurities is crucial for maintaining the quality of the recycled plastic and ensuring it can be used in various applications. Advanced recycling facilities may use advanced separation techniques, such as magnetic separation or air classification, to further purify the shredded plastic.
The final shredded plastic material can then be sold to manufacturers who use recycled content in their products or used internally within the recycling facility for creating new products. This process not only reduces the demand for virgin plastic but also contributes to a more sustainable and circular economy. By breaking down flexible plastics through shredding, we can unlock their potential for reuse, reducing waste and minimizing the environmental impact of plastic production and disposal.
Beyond Polymers: Exploring Other Recyclable Materials in Waste Streams
You may want to see also
Melting: Heat and melt plastic to create new materials
Melting plastic is a crucial step in the recycling process, especially for flexible plastics, as it allows for the creation of new materials and products. This method is particularly useful for transforming waste plastic into valuable resources, offering a sustainable approach to recycling. Here's a detailed guide on how to melt plastic for recycling:
Gathering Materials: Before beginning the melting process, ensure you have the necessary materials. You'll need a heat source, such as a heat gun or a small oven, capable of reaching temperatures suitable for melting plastic. It's important to choose a heat source that can provide controlled and consistent heat to ensure the melting process is effective. Additionally, have a mold or a shaping tool ready, as this will be used to form the molten plastic into new shapes.
Preparing the Plastic: Start by sorting and cleaning the flexible plastic waste. Remove any non-plastic components, such as labels or caps, and ensure the plastic is free from contaminants. Grinding or shredding the plastic into smaller pieces can make the melting process more efficient. This step is crucial as it increases the surface area of the plastic, allowing for better heat distribution during melting.
Melting Process: Place the prepared plastic pieces into the heat source. Use the heat gun or oven to apply heat directly to the plastic. Start with lower temperatures and gradually increase the heat as you observe the melting process. Flexible plastics typically melt at lower temperatures compared to rigid plastics. As the plastic begins to melt, ensure a steady and controlled heat application to avoid overheating or burning. The goal is to melt the plastic without degrading its quality.
Controlling Temperature and Time: Monitoring temperature and time is essential during the melting process. Overheating can lead to the degradation of plastic, resulting in a decrease in material quality. Maintain a consistent temperature within the optimal range for the specific type of flexible plastic you are working with. The melting time will vary depending on the plastic's thickness and the desired consistency. Regularly check the progress to ensure the plastic reaches the desired molten state.
Shaping and Molding: Once the plastic is melted, it can be shaped and molded into new forms. This step requires precision and the use of the prepared mold or shaping tool. Apply gentle pressure to the molten plastic and hold it in the desired shape until it cools and solidifies. This process allows for the creation of custom-made products, such as decorative items, garden ornaments, or even functional objects. Proper cooling is essential to ensure the plastic retains its shape.
Melting plastic for recycling is an art that requires practice and precision. It offers a creative way to upcycle waste, reducing environmental impact. By following these steps, you can effectively melt and recycle flexible plastics, contributing to a more sustainable future. Remember, the process may require adjustments based on the specific plastic type and your desired outcome.
Crafting a Greener Future: Transforming Plastic into Beads
You may want to see also
Re-granulation: Transform melted plastic into reusable pellets for manufacturing
Re-granulation is a crucial process in recycling flexible plastic, offering a sustainable solution to manage and repurpose this versatile material. This method involves transforming used plastic into reusable pellets, which can then be utilized in the manufacturing of new products. Here's a detailed breakdown of the process:
The recycling journey begins with the collection of flexible plastic waste. This can include items like plastic bags, film wraps, or any other flexible plastic materials that are no longer in use. Proper sorting and cleaning of these materials are essential to ensure the quality of the recycled product. After collection, the plastic waste undergoes a series of processes to prepare it for re-granulation.
The first step in the process is shredding or granulating the flexible plastic. This involves breaking down the plastic into smaller pieces or granules. Shredding machines are commonly used to reduce the plastic waste into manageable sizes. The shredded plastic is then washed to remove any contaminants, such as dirt or residual materials, ensuring a clean feedstock for the next stage.
Once the plastic is cleaned, it is fed into a specialized machine called a plastic granulator or re-granulator. This machine melts the plastic and then extrudes it through a die to create small, uniform pellets. The melting process is carefully controlled to ensure the plastic's chemical properties remain intact. The pellets produced are a reusable form of plastic, ready to be re-entered into the manufacturing cycle.
Re-granulation offers several advantages. Firstly, it reduces the volume of plastic waste, making it easier to store and transport. Secondly, the process allows for the recovery of valuable plastic resources, which can be used to produce new products. This method is particularly useful for flexible plastics, as it enables their reuse in various applications, including the manufacturing of new packaging, textiles, and even new flexible products.
In summary, re-granulation is an efficient and sustainable approach to recycling flexible plastic. By transforming melted plastic into reusable pellets, this process contributes to a circular economy, reducing waste and promoting the responsible use of resources. It is a vital step in the recycling chain, ensuring that flexible plastics can be given new life and value in various manufacturing processes.
Tennis Recycling: Unveiling the Plastic Straw Revolution
You may want to see also
Frequently asked questions
Most flexible plastics, such as those used in food packaging, shopping bags, bubble wrap, and some plastic films, can be recycled. However, it's important to check the recycling symbol on the plastic item to ensure it is recyclable in your local recycling program. Common types include LDPE (Low-Density Polyethylene) and HDPE (High-Density Polyethylene).
Before recycling, ensure that the flexible plastics are clean and dry. Remove any food residue or liquids, as these can contaminate the recycling process. Break down large items like shopping bags into smaller pieces to make them easier to handle. Flatten or roll up the plastics to save space and make them more manageable for recycling facilities.
Yes, flexible plastic packaging often contains multiple layers of different plastics, which can complicate the recycling process. Look for packaging that is made from a single type of plastic, preferably LDPE or HDPE. If the packaging has a recycling symbol with a number inside (resin identification code), ensure it matches the accepted types in your area.
Recycled flexible plastics can be transformed into various new products. For example, LDPE can be used to create new shopping bags, bin liners, or even furniture. HDPE can be recycled into containers for detergents, shampoos, or even new plastic bottles. The recycling process involves shredding, washing, and melting the plastic to create new raw materials, which are then used by manufacturers to produce new products.