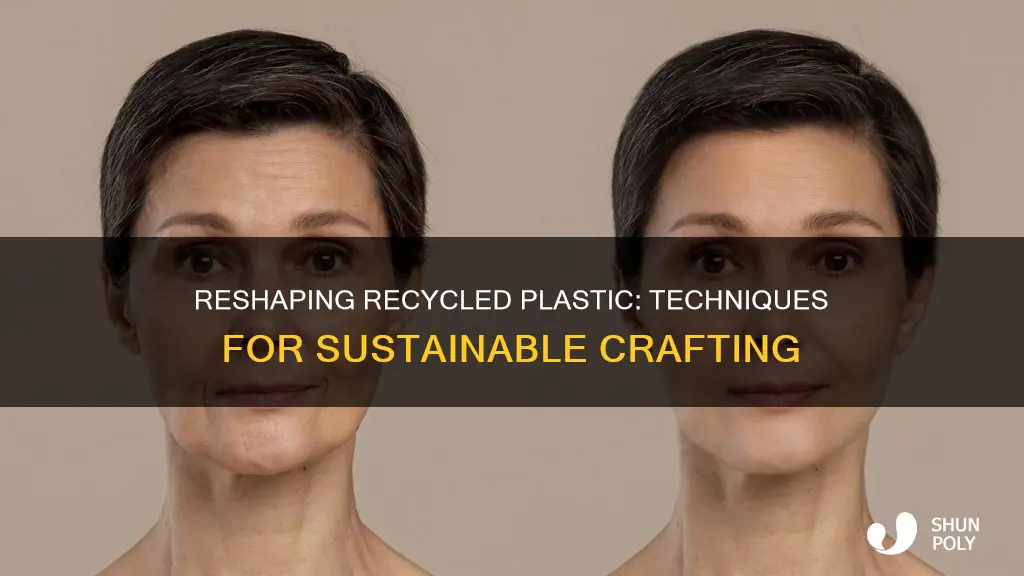
The plastic pollution crisis is an ongoing issue that requires radical innovation, ambitious policies, and significant investment to address. The European plastics industry is adapting to meet the challenge of reducing waste and carbon emissions, as outlined in the report ReShaping Plastics: Pathways to a Circular, Climate Neutral Plastics System in Europe. This report offers a roadmap for achieving net-zero carbon emissions by 2050 and emphasizes the need for collaboration between industry, government, and civil society. While systemic change is necessary, individuals can also play a role by reshaping recycled plastic at home. Various methods, such as melting plastic in oil, using a double boiler, or employing the Precious Plastic technique, can transform recycled plastic into new objects. These approaches not only reduce plastic waste but also contribute to environmental sustainability.
Characteristics of reshaping recycled plastic
Characteristics | Values |
---|---|
Techniques | Precious Plastic, Extrusion, Plastic Smithing |
Raw Materials | Plastic bags, Plastic containers, PET bottles, Plastic flakes |
Tools | Open-source machines, Ovens, Carjacks, CNC mills or lathes |
Temperature | LDPE melts at 248°F, Cooking oil boils at 350°F |
Benefits | No fumes, Pollution reduction, Carbon neutrality, Climate change mitigation |
Challenges | Plastic fumes, High temperature, Deployment of solutions |
What You'll Learn
Shredding and melting plastic bags
Once the plastic has melted and becomes tacky, it can be removed from the heat and blended to ensure the different bag lumps stick together. At this stage, it can be placed into a mold to form the desired shape. For example, a salsa container can be used as a wheel mold, and a wine bottle can create a hole in the middle. If a smooth and non-oily surface is desired, wax can be used instead of oil. It is also possible to use a constant temperature hot surface without any oil or wax if the temperature can be guaranteed to remain around the melting point.
Another method for reshaping plastic bags involves stuffing a box with shredded plastic bag pieces and compressing them with C-clamps. A steel box with a lid is preferable, as it can be difficult to remove the plastic from a wooden box. The box is then baked at 450 degrees for 40 minutes, and the clamps are re-tightened before cooling. This method may not produce a uniformly fused plastic block, but it does not require the use of oil or wax.
It is important to note that these processes should be approached with caution, as they involve working with hot materials and potential hazards. It is always recommended to prioritize safety and use the appropriate protective equipment when attempting any plastic reshaping methods.
Recycling Plastic in Winter, GA: A Guide
You may want to see also
Using a double boiler to melt plastic
To reshape recycled plastic, you can use a double boiler to melt the plastic. A double boiler is a set of two pots, one stacked and locked on top of the other. The bottom pot is partially filled with water, which is heated to a boil. The heat from the hot water in the bottom pot transfers to the top pot, which contains the plastic to be melted. This indirect heat source is ideal for melting plastic as it provides gentle, even heat that can be easily controlled to prevent scorching or burning.
When melting plastic with a double boiler, it is important to consider the type of plastic being used. Different plastics have different melting points, so knowing the type of plastic will help determine the appropriate temperature for melting. For example, LDPE (low-density polyethylene), which is commonly used for plastic bags, has a melting point of 248°F. Using a thermometer to monitor the temperature of the double boiler can help ensure that the plastic is heated to the correct temperature without overheating.
To set up a double boiler, you can use a pot and a bowl that fits securely on top of the pot. The bowl should be large enough to hold the plastic you plan to melt, and it should have a flat bottom that sits evenly on the pot. Fill the pot with water, ensuring that the water level is below the bottom of the bowl to prevent boiling water from splashing into the bowl. Heat the water to a boil, then place the plastic to be melted into the bowl and allow it to heat up gradually.
It is important to note that melting plastic can release harmful chemicals, so it is crucial to work in a well-ventilated area and take appropriate safety precautions. Additionally, some types of plastic may not be safe for melting, such as those that contain BPA or other toxic chemicals. It is always a good idea to research the specific type of plastic you are working with to understand any potential risks.
Recycling Plastic: Is Type 5 Plastic Recyclable?
You may want to see also
Extrusion of plastic flakes
Plastic extrusion is a high-volume manufacturing process that involves the homogeneous melting of a thermoplastic material. The raw compound material is commonly in the form of nurdles (small beads, often called resin) or flakes. The plastic flakes are fed into the hopper of an extruder and then move through the feed-throat to the barrel, which is heated. The heat, along with the rotation of a screw within the barrel, transforms the plastic from a solid to a molten state. The molten plastic is then pushed through a die, which shapes the plastic into the desired form. The plastic retains the shape of the die as it cools and hardens.
The desired extrusion temperature is rarely equal to the set temperature of the barrel due to viscous heating and other effects. Therefore, a heating profile is set for the barrel, with three or more independent PID-controlled heater zones that gradually increase the temperature from the rear to the front. This allows the plastic beads to melt gradually as they are pushed through the barrel and lowers the risk of overheating, which may cause polymer degradation. The intense pressure and friction within the barrel also contribute extra heat.
The product is then cooled, which is usually achieved by pulling the extrudate through a water bath. For products such as plastic sheeting, the cooling is achieved by pulling it through a set of cooling rolls. For films and very thin sheeting, air cooling can be effective as an initial stage.
The type of die used in the process depends on the complexity of the desired shape. Annular dies are the simplest, relying on the polymer melt channeling around the entire cross section of the die before exiting. Spider dies consist of a central mandrel attached to the outer die ring via a number of "legs", which produces a more symmetrical flow than annular dies, but also a number of weld lines that weaken the film.
Streamlined Plastic Recycling: Single Stream's Impact
You may want to see also
Using CNC mills or lathes to create moulds
To create a mould using a CNC mill or lathe, one must first design the mould using computer-aided design (CAD) software. This design is then translated into tool paths and sequences that the CNC machine will follow to cut and shape the mould. The CNC machine uses cutters such as end mills and drill bits to gradually remove material from the block until the desired shape is achieved.
When creating a mould for recycled plastic, it is important to consider the unique properties of the plastic and the specific requirements of the mould. For example, the mould may need to be treated with a heat-resistant and corrosion-resistant coating to withstand the high temperatures and pressures of the plastic injection process. Additionally, the mould may need to be polished or sanded to create a smooth surface and ensure the final product has a clean finish.
CNC mills or lathes can be used to create moulds for both small and large objects, depending on the size and capabilities of the machine. For example, the Precious Plastic Injection machine, a popular option for creating products from recycled plastic, has a maximum width for moulds of 28cm. If a larger mould is required, it may be necessary to send the design to a CNC cutting company, which can be more expensive and time-consuming.
Overall, using CNC mills or lathes to create moulds for recycled plastic is a precise and versatile option that allows for the creation of complex shapes and detailed features. With the right tools and knowledge, individuals can create high-quality products from recycled plastic, contributing to environmental sustainability and promoting the reuse of plastic materials.
Recycling Guide: Plastic FedEx Envelope
You may want to see also
The role of the European plastics system in reshaping plastic
The European plastics system plays a crucial role in reshaping plastic and addressing the challenges of climate change mitigation and circularity. The ReShaping Plastics report by SYSTEMIQ offers a comprehensive roadmap for the industry to achieve climate neutrality by 2050. This report, based on scientific methodology and market data, outlines various scenarios and interventions to reduce plastic pollution and transition to a circular, net-zero emissions plastics system.
One of the key objectives of the report is to foster collaboration between the industry, public sector, and civil society. It emphasizes the need for evidence-based conversations and shared solutions to address the complex challenges of the European plastics system. The report quantifies the economic, environmental, and social implications of different strategies, providing a data-driven model to guide decision-making.
The report focuses on four critical sectors: packaging, household goods, automotive, and construction. It presents six system change scenarios, prioritizing actions to meet circularity and climate goals. Achieving a fully circular and climate-neutral plastics system requires radical innovation, ambitious policies, and significant capital investment. The report underscores the importance of cooperation and the development of innovative technologies to reduce greenhouse gas emissions and decouple plastic from fossil fuel feedstocks.
Additionally, the report highlights the potential gains of different approaches to reaching net-zero, emphasizing the need for a combination of strategies such as reduction, reuse, substitution, and recycling. It also recognizes the importance of waste logistics and collection in Europe, differentiating it from the global context where littering is a more prominent issue. The findings provide a measuring tape to evaluate the effectiveness of upcoming laws and industry commitments in tackling plastic pollution.
The European plastics industry is already taking steps towards positive change, with organizations like Plastics Europe working with partners to deliver new systems thinking, mindset changes, and eco-design innovations. The ReShaping Plastics report serves as a call to action for European stakeholders, urging them to adapt and accelerate their transition towards a sustainable and circular plastics system.
How Green Are Peanut Butter Jars?
You may want to see also
Frequently asked questions
The ReShaping Plastics report is an independent report developed by SYSTEMIQ and commissioned by Plastics Europe. It evaluates the progress of the European plastics system in addressing the challenges of climate change mitigation and circularity. The report also assesses the potential of different approaches to help achieve the EU's net-zero carbon emissions and circularity goals by 2050.
The report finds that a fully circular, net-zero carbon emissions plastics system in Europe is possible. However, it will require significant innovation, ambitious policies, and capital investment. It highlights the need for cooperation between industry, government, and civil society to achieve these goals. The report also emphasizes the importance of reducing, reusing, substituting, and recycling plastic materials.
The Precious Plastic project, started by Dave Hakkens, is a collection of open-source machines designed for recycling and reusing thermoplastics. It involves shredding plastic waste into flakes, which can then be used to create new objects through processes like 3D printing or moulding.
One method is to collect plastic bags, shred them, and melt them in oil or wax. This allows you to mould the plastic into your desired shape. Another technique involves exploiting the properties of blow-moulded PET bottles, which can act like shrink wrap when heated with hot air or dipped in hot water.
One challenge is the need for radical innovation and systemic change to achieve a fully circular and climate-neutral plastics system. Additionally, there may be technical challenges in moulding and casting plastic into desired shapes, especially for custom or complex designs.