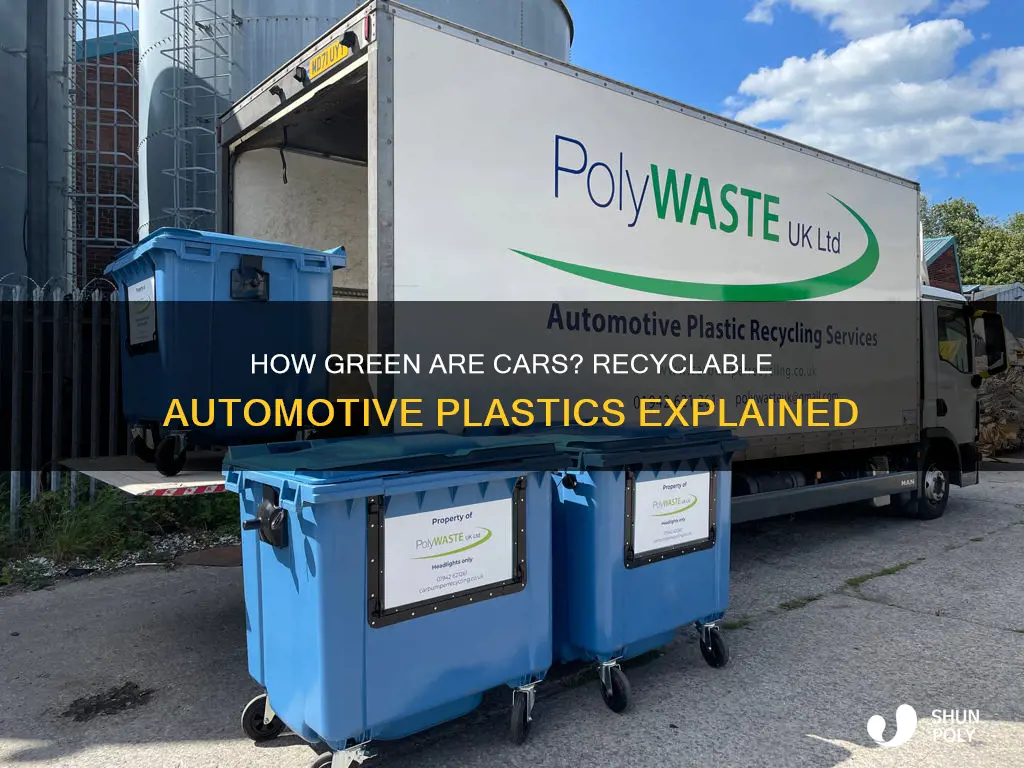
The automotive industry has long relied on plastic for its lightness, flexibility, and affordability. However, with growing environmental concerns, the focus has shifted to recycling plastics to reduce waste and carbon emissions. Recycling automotive plastics is challenging due to the complexity of car designs and the variety of materials used. Despite these challenges, several manufacturers are embracing recycled plastics, with companies like Volvo aiming for 25% recycled plastics in their manufacturing by 2025. The process of recycling automotive plastics involves dismantling, sorting, cleaning, shredding, melting, and reforming pellets for new products. This reduces landfill waste and the need for raw materials, contributing to a more sustainable future.
What You'll Learn
- Plastic recycling reduces landfill waste and the need for raw materials
- The automotive industry is working to increase the use of recycled plastics
- The recycling process: collection, sorting, cleaning, shredding, melting
- The economic and environmental benefits of recycled plastics
- The challenges of recycling automotive plastics
Plastic recycling reduces landfill waste and the need for raw materials
The automotive industry has been using plastics since its inception, and they are now essential to reducing a vehicle's weight and improving fuel efficiency. However, the use of plastics in the automotive industry has resulted in large amounts of plastic waste. Recycling plastic is crucial to reducing landfill waste and the need for raw materials.
The recycling process for automotive plastics is complex and varies across countries and companies. It typically involves several stages: collecting plastic waste, transporting it to a recycling plant, sorting plastics by type, decontamination and cleaning, shredding, melting, and reforming pellets that can be used as raw material for new products. The sorting stage is critical, as it separates recyclable plastics from other waste.
The automotive industry faces challenges in plastic recycling due to the diverse range of materials used in modern cars, making dismantling and recycling difficult. However, advancements in technology, such as injection moulding, CNC machining, and extrusion, are aiding the recycling process.
Recycling plastic reduces the need for extracting and processing raw materials, lowering the consumption of natural resources and contributing to a circular economy. It is also more cost-effective than producing new plastics from fossil fuels, as recycled plastics can be cheaper and have superior properties.
Several car manufacturers are embracing recycled plastics. For instance, Skoda uses recycled plastic components in injection moulding technology, and Renault has committed to using 30% recycled materials in its Megane II model. Volvo has pledged that 25% of the plastics used in manufacturing cars will be recycled by 2025. These initiatives demonstrate the industry's efforts to enhance sustainability and reduce the environmental impact of automotive plastic waste.
Recycling Plastic Cups: The Process and Environmental Impact
You may want to see also
The automotive industry is working to increase the use of recycled plastics
The automotive industry is facing increasing environmental and sustainability challenges. Recycled plastics are seen as a solution to limit the negative environmental and climate impacts of the industry, especially when it comes to manufacturing automotive parts. The use of plastics in automotive constructions is increasing, and their reuse has the potential to significantly reduce the carbon footprint of the industry. Recycling plastics is less energy-intensive than producing new plastics from raw materials, and it also reduces the need for extracting and processing raw materials, which helps to reduce greenhouse gas emissions.
Skoda is another automotive company that uses recycled plastic components, specifically injection moulding technology. Renault is also actively engaged in the use of recycled materials. Its Megane II model, launched at the end of 2014, has 30% of its components made from recycled materials. Renault's upcoming Scenic Etech model, to be released in 2024, will be 90% recyclable and will use plastic instead of leather for the seat upholstery. Renault has also developed a project that aims to recover polypropylene from bumpers and wheel arch coverings to produce new plastic car parts, promoting a closed-loop economy.
The Spanish car parts industry, a significant global player, is committed to the European objectives of decarbonising the economy and transport. In 2018, the sector invested 1,545 million EUR (4.2% of its turnover) in research and development of sustainable solutions, including the increased utilisation of recycled plastics. However, Renault's study highlights that recovery processes need improvement to obtain high-quality end products at competitive costs.
To facilitate the use of recycled materials in the automotive sector, AIMPLAS, the Plastics Technology Centre, has launched the SURFTOP Project. This project focuses on obtaining recycled raw materials from automotive industry waste to manufacture new parts that comply with the requirements of the automotive industry. The SURFTOP Project is funded by the Valencian Institute of Competitiveness and Innovation (IVACE+i) and the ERDF.
Chandler's Recycling Program: Does Plastic 6 Make the Cut?
You may want to see also
The recycling process: collection, sorting, cleaning, shredding, melting
The recycling process for automotive plastic, as with other plastics, involves several steps: collection, sorting, cleaning, shredding, melting, and forming new products.
Collection
The recycling process typically begins with collection. Post-consumer plastics are collected from various locations, such as curbside recycling bins, public recycling bins, or community recycling centres. In the automotive industry, plastic car parts, such as bumpers and wheel arch coverings, can be collected for recycling during vehicle maintenance or end-of-life vehicle processing.
Sorting
After collection, the plastics are sorted into different streams. This sorting can be done manually or by machines using advanced technologies. The plastics are grouped by type, colour, thickness, and usage. They are also segregated based on density, with floatation tests used to separate different types of plastics. Metals and glass may also be sorted out during this stage to prevent contamination.
Cleaning
The sorted plastics then undergo a cleaning process to remove impurities that may hinder subsequent steps. This includes removing product labels, adhesives, and food residue, and oily substances. The cleaning process typically involves rinsing with warm water and detergent solutions, ensuring that the plastics are thoroughly washed.
Shredding
Once cleaned, the plastics are ready for shredding or grinding. They are broken down into smaller-sized pieces, often called flakes or pellets, to facilitate the next steps in the recycling process. This stage is crucial, especially for plastics that are difficult to recycle, as it prepares the material for further processing.
Melting
After shredding, the plastic flakes or pellets are crushed and melted to form pallets called nurdles. The melting process allows the plastic to be transformed into a new shape to create a new product. Different classes of plastics may require specific plants or processes for this step, and the melted plastic can then be used to create various automotive parts.
Overall, the recycling process for automotive plastic involves several steps to ensure the effective reuse of materials. While challenges remain, such as improving recovery processes and reducing contamination, the automotive industry is increasingly investing in sustainable practices and incorporating recycled plastics into vehicle components.
Not All Plastic Is Recycled: Understanding Plastic's Fate
You may want to see also
The economic and environmental benefits of recycled plastics
The automotive industry is increasingly embracing recycled plastics as a solution to environmental and sustainability challenges. Recycling plastics offers significant economic and environmental benefits, which are detailed below.
Economic Benefits
- Reduced Costs: Producing plastic from virgin materials is often more expensive than using recycled plastic. By using recycled plastics, manufacturers can lower their production costs, leading to increased profitability and competitiveness.
- Energy Savings: Recycling plastic requires less energy than producing new plastic from fossil fuels. It is estimated that reprocessing 1 ton of plastic can save up to approximately 130 million kilojoules of energy.
- Job Creation: The plastic recycling industry contributes to job creation and economic growth. Recycling facilities, collection centers, and related businesses require a skilled workforce to efficiently carry out the recycling process.
- Competitiveness: Embracing plastic recycling can make businesses more competitive by reducing their reliance on virgin raw materials and lowering their environmental impact.
Environmental Benefits
- Reduced Greenhouse Gas Emissions: Recycling plastic emits fewer greenhouse gases than producing new plastic, contributing to a cleaner and more sustainable environment. Automotive plastics, in particular, help reduce vehicle weight, leading to improved gas mileage and lower CO2 emissions.
- Reduced Landfill Waste: Recycling plastics reduces the amount of waste sent to landfills. Automotive plastics already make up about 0.5% of landfill waste, and recycling can help decrease this proportion.
- Conservation of Resources: Recycling plastics conserves natural resources by reducing the need for extracting and processing raw materials. This contributes to the objectives of a circular economy.
- Improved Eco-efficiency: Recycling can decrease energy and material usage per unit of output, leading to improved eco-efficiency.
How to Properly Recycle Plastic: A Step-by-Step Guide
You may want to see also
The challenges of recycling automotive plastics
The automotive industry has used plastics since its inception, and they remain integral to the sector. Plastics are favoured for their relatively low cost, flexibility, and lightness, which reduces cars' overall weight and fuel consumption. However, the disposal of automotive plastic parts is complex due to the variety of materials used in modern cars, making dismantling and recycling challenging. This process typically involves removing individual components, separating and sorting materials, recycling or landfilling them, and managing the financial burden of recycling.
One of the primary challenges in recycling automotive plastics is the lack of uniform standards across the industry. Different countries and companies employ various methods and processes, impacting cost and efficiency. The type of plastic also influences processing difficulty and cost. For instance, recycling engineering plastics can be more expensive due to the need for effective separation and specialised facilities for disassembly, sorting, and storing.
Another challenge is ensuring that recycled plastics are free of contaminants like dirt, moisture, gasoline, oil, and glycol. This decontamination process is crucial for the reusability of recycled plastics in new or identical applications. The recycling process itself, which includes collecting, sorting, cleaning, shredding, melting, and reforming plastics, can be time-consuming and costly.
Despite these challenges, recycling automotive plastics is crucial for reducing landfill waste, the need for raw materials, and greenhouse gas emissions. It is also more economically and environmentally sustainable than producing new plastics from virgin raw materials. Automotive companies like Ford, Renault, and Toyota are increasingly committed to sustainability and recycling initiatives, with some utilising recycled plastic components in their manufacturing processes.
Big Y's Plastic Bottle Recycling: What You Need to Know
You may want to see also
Frequently asked questions
Yes, automotive plastics can be recycled. However, the process is complex and varies across countries and companies.
Recycling automotive plastics helps reduce landfill waste, the need for raw materials, and greenhouse gas emissions. It also contributes to the development of a circular economy.
One of the main challenges is the lack of uniform standards and methods for recycling automotive plastics. Additionally, the complex composition of modern cars makes dismantling and separating plastic components difficult.
The process typically involves collecting, sorting, cleaning, shredding, melting, and reforming plastic waste into pellets that can be used as raw material for new products.
Several car manufacturers are incorporating recycled plastics in their vehicles. Examples include Volvo, Skoda, Renault, Ford, and Toyota.