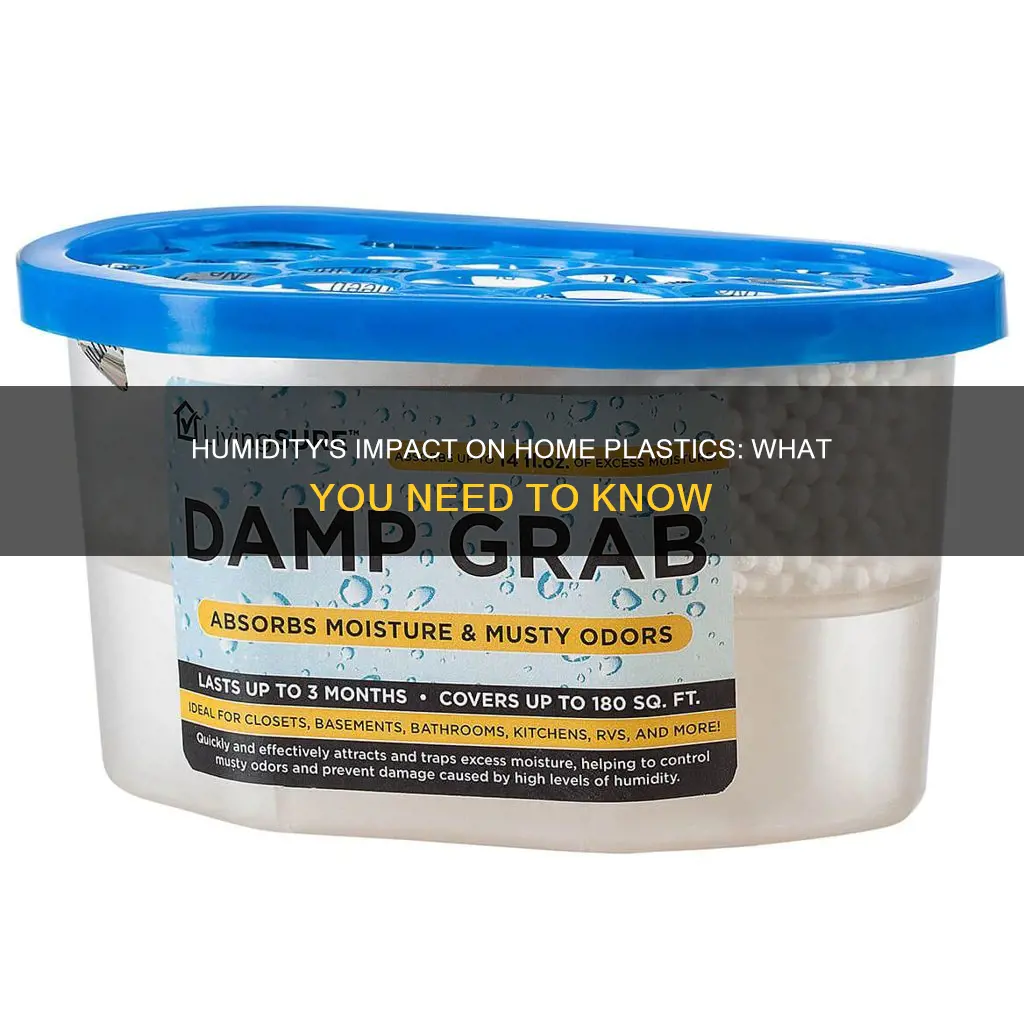
Humidity is an important factor to consider in the plastics industry, as it can have a significant impact on the production process and the final product. High humidity in the home can affect plastics, causing them to degrade over time. This is because plastics are often made from polymers, which are susceptible to photodegradation when exposed to high levels of humidity. Additionally, excessive moisture in the air can lead to water absorption in plastics, causing distortion and a shorter useful lifetime. In the plastics industry, humidity is carefully controlled to prevent these issues and maintain the quality of the end product.
Characteristics | Values |
---|---|
Effect on plastic products | Thermoset and thermoplastic products can be used in high humidity at moderate temperatures for short periods of time. However, long-term exposure to warm humidity can degrade some products. |
Effect on plastic production | Humidified air binds dust particles more quickly than dry air, reducing equipment damage and production downtime. |
Humidity control can prevent costly damage to sensitive components and disruption to production processes. | |
Maintaining a constant humidity level between 40-60% can reduce static electricity drastically in a plastic production facility. | |
Effect on workers | High humidity can cause lethargy and discomfort, while low humidity can lead to fatigue and difficulty concentrating. |
Companies that invested in humidity control systems experienced a decrease in employee absence by as much as 50% during the wintertime. |
What You'll Learn
Humidity affects the photodegradation of plastics
The interaction between humidity and temperature further complicates the understanding of how humidity affects photodegradation. At extremely high temperatures (80°C or higher), the rate of thermal-oxidative degradation surpasses that of hydrolysis, resulting in no significant increase in hydrolysis with increased humidity. However, at lower temperatures, humidity plays a more pronounced role. For example, the degradation rate of polylactic acid (PLA) plastics, a type of biodegradable plastic, is enhanced by both higher temperatures and relative humidity levels.
The effects of humidity on plastics extend beyond photodegradation. In certain cases, long-term exposure to warm humidity can result in hydrolysis, causing useful lifetimes to be significantly shorter than expected. This phenomenon can be observed in both thermoset and thermoplastic products. Additionally, humidity plays a crucial role in the plastics industry, where it is used to stabilise processes. Maintaining a relative humidity between 40-60% helps to mitigate the issues caused by electrostatic discharge and enhances productivity, employee comfort, and health.
Overall, humidity has a significant influence on the photodegradation of plastics, with varying effects depending on the specific type of plastic and the temperature conditions. The complex relationship between humidity, temperature, and degradation rates underscores the need for further research and understanding of plastic degradation in different environmental conditions.
The Ocean's Plastic Problem: How Much Have We Collected?
You may want to see also
Thermoset plastics are irreversibly damaged by humidity
Thermoset plastics are polymeric materials that undergo a permanent change in their molecular structure upon heating. This process, known as curing, results in an irreversible cross-linking reaction that enhances the material's strength, rigidity, and thermal stability. However, this same characteristic that makes thermoset plastics so valuable in various industrial applications also leads to their susceptibility to humidity damage.
When exposed to long-term warm humidity conditions, thermoset plastics can undergo a hydrolysis effect, causing them to degrade. This degradation can lead to a significant reduction in their useful lifetimes compared to what would be expected from conventional dry oven aging tests. The water absorption associated with high humidity environments can lower the glass transition temperature of thermoset plastics, resulting in distortion and irreversible damage.
The irreversible nature of thermoset plastics' curing reaction means that once they are initially heat-formed or molded, they cannot be effectively remolded or reheated. This limitation is due to the three-dimensional network structure that prevents any further molecular mobility. As a result, thermoset plastics that have been damaged or distorted due to prolonged exposure to warm humidity cannot be easily restored to their original state.
Additionally, thermoset plastics are known for their brittle fracture behavior when damaged. This characteristic further complicates the issue of humidity damage, as it can lead to the complete failure of the material. The combination of high humidity and mechanical stress can exacerbate the problem, resulting in more rapid deterioration and irreversible harm to the plastic.
To mitigate the effects of humidity on thermoset plastics, it is crucial to maintain moderate temperatures and limit exposure to high humidity conditions for extended periods. Selecting appropriate plastic formulations that exhibit good long-term resistance to humidity, such as those with water-resistant properties, can also help minimize the potential for irreversible damage. Understanding the unique characteristics of thermoset plastics and the impact of humidity is essential for effective material selection and maintenance in various applications.
The Plastic Crisis: Annual Dumping Statistics
You may want to see also
Humidity can cause distortion in plastics
Plastics are a part of our everyday lives, and they are used in a wide range of applications, from common household items to specialized industrial products. However, the presence of moisture in the air, or humidity, can negatively impact plastics, causing distortion and degradation over time. This is particularly true for hygroscopic plastics, which are materials that absorb moisture due to their chemical composition. Polyamides, for instance, form hydrogen bonds in the presence of moisture, which can be detrimental to their mechanical properties before processing.
In the plastics industry, manufacturers must take steps to control humidity to ensure the quality of their products. This is achieved through the use of humidifiers, which can provide precise and consistent humidity levels. By regulating humidity, manufacturers can prevent issues such as electrostatic discharge, which can damage equipment and slow down production. Additionally, maintaining the correct humidity level can enhance the final product's quality, as moisture absorption can interfere with the finished product's appearance and mechanical properties.
For consumers, high humidity levels in the home can also affect plastics. Prolonged exposure to warm, humid environments can lead to hydrolysis, causing plastics to distort and degrade prematurely. This is particularly noticeable in products with high water absorption rates, where the glass transition temperature is lowered, resulting in deformation.
To mitigate these issues, it is important to maintain a comfortable and healthy humidity level in the home, typically between 40-60% relative humidity. This can be achieved through the use of dehumidifiers or air conditioners, especially in particularly warm and humid climates. By doing so, consumers can help extend the lifespan of plastic items and prevent distortion caused by excessive moisture in the air.
The Dark Truth: Plastic Decomposition Timeline Revealed
You may want to see also
Humidified air protects plastic machinery from damage
Humidified air is an essential factor in protecting plastic machinery and products from damage. The plastics industry relies on stable processes, and air humidity plays a critical role in maintaining them. Firstly, a relative humidity of 40-60% helps to reduce electrostatic discharge (ESD), which can cause equipment damage and production downtime. Friction between plastics can create an electrostatic charge, but humidified air quickly binds dust particles, reducing their presence on sensitive components and surfaces. This not only protects machinery but also enhances quality assurance by decreasing the failure rate.
Additionally, maintaining the correct humidity level is crucial for the plastic production process itself. Thermosetting resins, for example, require careful control of humidity to prevent the water vapour from interacting with the resin as it solidifies when heated. Similarly, during the injection moulding process, adhering to the manufacturer's instructions regarding moisture content and drying is essential. Relative humidity plays a role here, as higher humidity can affect the moisture content of plastic granules.
Moreover, the degradation of certain plastics is influenced by humidity levels. In the case of poly(vinyl chloride) (PVC) and polylactic acid (PLA) plastics, humidity levels impact their degradation. In the case of PVC, low humidity can lead to increased CO2 evolution, while higher humidity levels can decrease it due to the catalytic effect of hydrochloric acid. For PLA plastics, an increase in both temperature and relative humidity accelerates their degradation rate.
Finally, from an employee perspective, a working environment with a relative humidity of 40-60% provides several benefits. These include increased productivity, motivation, and comfort, as well as a reduction in health-related illnesses.
Overall, humidified air is a critical factor in protecting plastic machinery and products from damage, ensuring stable processes, enhancing product quality, and providing a comfortable working environment in the plastics industry.
Ductwork Plastic Replacement: Cost, Benefits, and More
You may want to see also
Humidity can cause electrostatic discharge in plastics
Electrostatic discharge (ESD) is a common phenomenon in low-humidity environments. It occurs when two objects with opposite charges come close together, resulting in a sudden flow of electricity between them. This can happen when two surfaces come into contact and exchange electrons through friction or the triboelectric effect. While ESD may not cause serious injury, it can damage sensitive electronic components, such as computer circuits, motherboards, and processors.
Plastics are particularly susceptible to the effects of ESD. In the plastics industry, friction between plastic materials can lead to electrostatic charging, causing equipment damage and disruptions in production. To mitigate this, manufacturers use air humidification to increase the moisture content in the air. Humidified air is more conductive, allowing excess charges to dissipate and reducing the risk of sudden electrostatic discharges.
The ideal relative humidity for the plastics industry is between 40% and 60%. Below 40% relative humidity, the risk of static electricity build-up increases significantly. For example, at 20% humidity, walking across a carpeted floor can generate 35,000 volts of static electricity. However, when relative humidity is maintained above 40%, the moisture in the air provides a pathway for charges to dissipate harmlessly.
Additionally, air humidification in the plastics industry offers other benefits. It helps to bind dust particles, reducing their presence on sensitive components and surfaces. This leads to improved quality assurance and decreased equipment failure rates. Furthermore, maintaining relative humidity within the optimal range can enhance employee productivity, motivation, and comfort, while also reducing health-related illnesses.
In summary, humidity plays a critical role in preventing electrostatic discharge in plastics. By controlling and maintaining relative humidity levels, manufacturers can safeguard their equipment, optimize production processes, and create a more conducive working environment for their employees.
The Plastic Waste Crisis: How Much Do We Throw Away?
You may want to see also
Frequently asked questions
High humidity can cause plastics to distort due to water absorption. It can also cause the photodegradation of plastics, and in the case of PVC, high humidity leads to a higher rate of CO2 evolution.
Maintaining a humidity level between 40-60% can reduce static electricity and improve uniformity in plastic production.
High humidity can cause variations in the properties of plastics, including their strength, flexibility, and transparency.
Controlling humidity can prevent costly damage to equipment and sensitive components, improve product quality, and enhance worker comfort and productivity.
Adiabatic humidification systems can be used to control humidity levels in industrial settings. Steam humidifiers, such as the HygroMatik MiniSteam, are also available for direct room humidification.