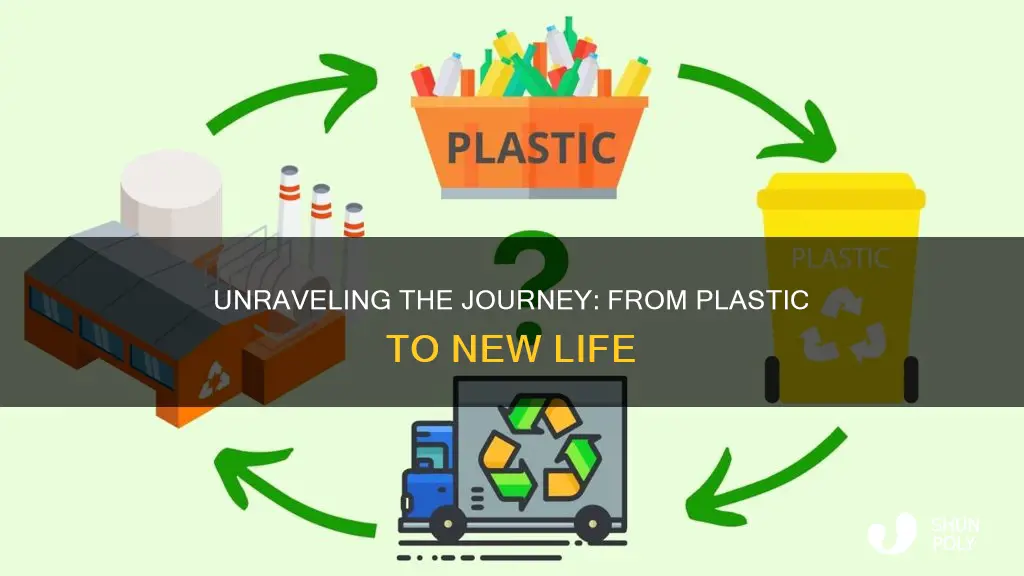
Recycling plastic is an essential process that helps reduce environmental impact and promotes sustainability. It involves collecting, sorting, and processing plastic waste to create new products. The process typically begins with the collection of plastic materials from various sources, such as households, businesses, and recycling centers. These materials are then sorted based on their type and quality, ensuring that only suitable plastics are used for recycling. After sorting, the plastic is cleaned and shredded into small pieces, which are melted and molded into new forms. This process can be repeated multiple times, transforming old plastic items into new products like furniture, clothing, and even new packaging. Understanding the recycling process is crucial for individuals and industries to contribute to a more sustainable future by reducing plastic waste and conserving resources.
What You'll Learn
- Collection: Plastic waste is gathered from various sources, including households, businesses, and recycling centers
- Sorting: Materials are separated by type and color to ensure proper processing
- Cleaning: Items are cleaned to remove contaminants and prepare for recycling
- Shredding/Grinding: Plastic is broken down into small pieces or flakes
- Melting/Reforming: These flakes are melted and reformed into new products
Collection: Plastic waste is gathered from various sources, including households, businesses, and recycling centers
The first step in the recycling process of plastic is collection, which is a crucial phase that sets the foundation for the entire recycling journey. Plastic waste is gathered from multiple sources, ensuring a comprehensive and diverse collection. This includes households, where residents play a vital role by separating their plastic waste into different categories, such as bottles, containers, and packaging. Encouraging proper waste segregation at the source is essential to streamline the recycling process and reduce contamination.
Businesses also contribute significantly to this collection process. Many companies now have recycling programs in place, providing designated bins for employees to dispose of their plastic waste. This practice not only promotes environmental responsibility but also educates employees about the importance of recycling. Additionally, businesses can organize collection drives, collecting plastic waste from their premises and nearby areas, ensuring a steady supply of recyclable materials.
Recycling centers, or material recovery facilities (MRFs), are specialized sites designed for efficient waste management. These centers employ various techniques to sort and process plastic waste. They use advanced machinery to separate different types of plastics, ensuring that each material is handled appropriately. The collection process at recycling centers involves receiving plastic waste from various sources, including local governments, businesses, and even other recycling facilities, creating a network of sustainable waste management.
Efficient collection methods are employed to ensure that plastic waste is gathered promptly and efficiently. This includes the use of specialized vehicles and containers designed to handle different types of plastics. Mobile collection units can visit households and businesses, making the process more accessible and convenient. Proper labeling and marking of collection bins also help in categorizing the waste, making it easier to process and recycle.
In summary, the collection phase is a critical step in recycling plastic, as it involves a collaborative effort from households, businesses, and dedicated recycling centers. By encouraging proper waste segregation and implementing efficient collection methods, the process becomes more streamlined and effective. This initial step sets the tone for the entire recycling journey, ensuring that plastic waste is managed sustainably and contributes to a greener environment.
Sustainable Building: Top Sources for Recycled Plastic Bricks
You may want to see also
Sorting: Materials are separated by type and color to ensure proper processing
The initial step in the recycling process of plastic is sorting, a critical phase that ensures the effective and efficient transformation of waste into new materials. This process involves a meticulous separation of plastic materials based on their type and color, a practice that is both essential and intricate. The primary goal is to create distinct streams of plastic, each tailored for specific recycling methods and end products.
In the sorting process, materials are first categorized by their resin identification codes, which are typically found on the bottom of plastic containers. These codes, ranging from 1 to 7, indicate the type of plastic, such as PET (polyethylene terephthalate) or HDPE (high-density polyethylene). For instance, PET is commonly used in beverage bottles, while HDPE is found in milk jugs and some detergent containers. Sorting by resin type is crucial because different plastics have distinct chemical structures and melting points, which affect their recyclability and the quality of the recycled material.
Beyond resin type, sorting also considers the color of the plastic. This is particularly important for clear and colored plastics, as they often have different recycling pathways. For example, clear PET bottles are highly valued in the recycling market due to their high purity and ease of processing. On the other hand, colored plastics, such as those used in yogurt cups or shampoo bottles, may have limited recycling options and could be downcycled into lower-quality products.
Advanced sorting techniques are employed to enhance the efficiency and accuracy of this process. Optical sorters, for instance, use light to identify and separate plastics based on their color and transparency. These machines can process large volumes of material quickly, ensuring that each type of plastic is isolated effectively. Additionally, manual sorting, where workers separate materials by hand, remains a vital part of the process, especially for small-scale recycling operations or for identifying more complex plastic blends.
The importance of this sorting step cannot be overstated. It is the foundation for the entire recycling process, ensuring that the right materials are directed to the appropriate recycling facilities. Proper sorting not only facilitates the production of high-quality recycled products but also reduces the environmental impact of plastic waste, contributing to a more sustainable and circular economy.
Unraveling the Mystery: Can Plastic 2 Be Recycled?
You may want to see also
Cleaning: Items are cleaned to remove contaminants and prepare for recycling
The cleaning process is a crucial step in plastic recycling, as it ensures that the material is free from contaminants and ready for further processing. This step is essential to maintain the quality and integrity of the recycled plastic, making it suitable for reuse in various applications. Here's an overview of the cleaning process:
Sorting and Separation: The first step in cleaning is often sorting and separating different types of plastic items. Plastic recycling facilities use various methods to categorize plastics based on their resin identification codes (RICs). Common types include PET (polyethylene terephthalate), HDPE (high-density polyethylene), PVC (polyvinyl chloride), LDPE (low-density polyethylene), and PP (polypropylene). Proper sorting ensures that each type of plastic is cleaned according to its specific requirements. For instance, PET bottles and containers have a different cleaning process compared to HDPE milk jugs.
Washing and Cleaning: Once sorted, the plastic items undergo a thorough washing process. This involves using specialized washing machines or systems designed for plastic recycling. The washing process aims to remove dirt, labels, glue, and other contaminants that may be present on the plastic surfaces. High-pressure water jets and brushes are commonly used to scrub the items, ensuring that no residue remains. After washing, the plastic pieces are often dried to eliminate any moisture. This step is critical to prevent contamination during the recycling process.
Contaminant Removal: Cleaning also focuses on removing specific contaminants that can hinder the recycling process or affect the quality of the recycled material. For example, removing labels and glue is essential, as these can interfere with the melting and molding processes. Facilities may use various techniques to separate labels from the plastic, such as mechanical separation or chemical treatments. Additionally, any non-plastic components, like metal caps or plastic lids, need to be removed to ensure a pure plastic stream.
Advanced Cleaning Techniques: In some cases, more advanced cleaning methods are employed to ensure the highest level of cleanliness. This includes the use of specialized chemicals to dissolve or remove stubborn contaminants. For instance, certain plastics may require the use of solvents to break down and wash away any remaining impurities. These advanced techniques are carefully controlled and monitored to ensure the safety and effectiveness of the cleaning process.
Quality Control: Throughout the cleaning process, quality control measures are implemented to ensure that the plastic items meet the required standards. This may involve visual inspections, weight measurements, and even more advanced testing methods to verify the cleanliness and purity of the recycled material. The goal is to produce high-quality recycled plastic that can be confidently used in new products.
Unraveling the Mystery: Can Starbucks Plastic Cups Be Recycled?
You may want to see also
Shredding/Grinding: Plastic is broken down into small pieces or flakes
The process of recycling plastic begins with the collection and sorting of plastic waste. Once sorted, the plastic is then shredded or ground into small pieces or flakes. This step is crucial as it prepares the plastic for further processing and transforms it into a usable material.
Shredding and grinding are mechanical processes that involve breaking down the plastic into smaller fragments. The shredded or ground plastic is often referred to as 'regrind' or 'flake'. This process is typically carried out using specialized machinery designed for plastic recycling. The equipment can vary depending on the type of plastic and the desired end product. For example, single-screw extruders are commonly used for this stage, as they can effectively melt and process the plastic flakes.
During shredding, the plastic waste is fed into the machine, which then cuts and tears it into small, uniform pieces. This process helps to reduce the volume of the plastic and makes it easier to handle and transport. The shredded plastic can range from a few millimeters to a few centimeters in size, depending on the specific requirements of the recycling facility and the intended use of the recycled material.
Grinding, on the other hand, involves a more aggressive approach where the plastic is ground into very fine particles or flakes. This method is often used for producing plastic pellets or granules, which can then be used as raw material for manufacturing new products. The grinding process ensures that the plastic is reduced to a consistent size, allowing for efficient mixing and compounding with other materials during the production of new items.
After shredding or grinding, the plastic flakes are cleaned to remove any contaminants such as dirt, labels, or non-plastic materials. This cleaning process is essential to ensure the quality and purity of the recycled plastic. The cleaned flakes are then ready for the next stage of recycling, where they can be melted, molded, or used as feedstock for various industrial processes.
Unraveling the Mystery: Can Plastic Hangers Be Recycled?
You may want to see also
Melting/Reforming: These flakes are melted and reformed into new products
The process of recycling plastic involves several stages, and one crucial step is the melting and reformation of plastic flakes into new products. This method is particularly effective for recycling plastic waste that has been sorted and cleaned. Here's an overview of this process:
When plastic waste is collected, it undergoes a sorting process to separate different types of plastics. This is essential because not all plastics are recyclable in the same way. Once sorted, the plastic waste is cleaned to remove any contaminants like labels, dirt, or non-plastic materials. The cleaned plastic is then shredded or granulated into small flakes, which are the raw materials for the melting process.
The plastic flakes are fed into a specialized machine called a plastic granulator or shredder. This machine melts the plastic flakes by applying heat and pressure. The temperature and duration of the melting process depend on the type of plastic being processed. For example, PET (polyethylene terephthalate) bottles typically require a higher melting temperature compared to HDPE (high-density polyethylene) containers. The melted plastic is then extruded through a die to form new shapes or flakes, which are cooled and solidified.
After the melting and shaping process, the new plastic products are formed. This can be done through various techniques such as injection molding, blow molding, or extrusion. In injection molding, for instance, the molten plastic is injected into a mold, taking the desired shape. Once the plastic cools and solidifies, the mold is opened, and the new product is removed. This process allows for the creation of a wide range of items, including containers, bottles, furniture, and even electronic components.
The melting and reformation process is a critical aspect of plastic recycling as it enables the transformation of waste into valuable resources. It showcases the potential for recycling to reduce environmental impact and promote a circular economy. By reusing and repurposing plastic, we can minimize the demand for virgin plastic production, which often relies on non-renewable resources. This recycling method also helps to conserve energy and reduce the amount of plastic waste that ends up in landfills or the environment.
Unraveling the Mystery: Can Plastic Bottles Be Recycled?
You may want to see also
Frequently asked questions
The initial step is collection and sorting. Plastic waste is gathered from various sources like households, businesses, and recycling centers. It is then sorted based on the type of plastic, which is crucial for proper recycling. Common types include PET (polyethylene terephthalate), HDPE (high-density polyethylene), PVC (polyvinyl chloride), LDPE (low-density polyethylene), and PP (polypropylene).
After sorting, the plastic is cleaned to remove contaminants like food residue, labels, and non-plastic materials. This cleaning process ensures that the plastic is free from impurities, making it suitable for recycling. The cleaned plastic is then shredded or granulated into small pieces or flakes, which are easier to handle and process.
The shredded or granulated plastic is melted and molded into new products. This process involves heating the plastic to its melting point and then shaping it using various techniques like injection molding, blow molding, or extrusion. The molten plastic is then cooled and solidified to form new products such as bottles, containers, furniture, and even clothing fibers.
Not all types of plastic are recyclable in the same way. As mentioned earlier, different types of plastic have distinct recycling processes. For example, PET bottles are widely recycled and can be used to make new bottles, clothing, and even car parts. However, some plastics like single-use plastic bags and straws often require specialized recycling processes and may not be accepted in regular recycling streams.
Recycling plastic offers numerous advantages. It helps conserve natural resources by reducing the need for virgin plastic production, which relies on fossil fuels and non-renewable resources. Recycling also diverts plastic waste from landfills and incinerators, preventing environmental pollution and potential harm to ecosystems. Additionally, it can create jobs and contribute to a more sustainable and circular economy.