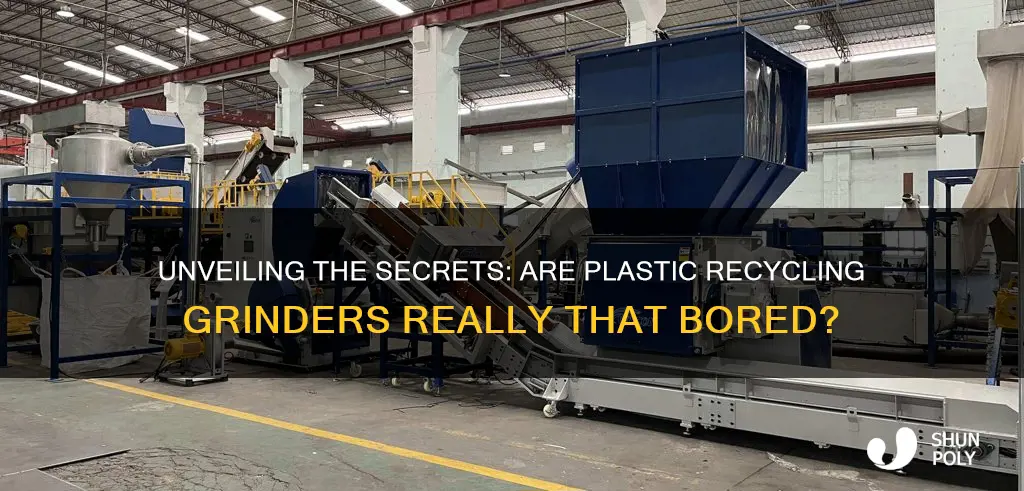
Are boring plastic recycling grinders? Well, that's a curious question! While the term boring might suggest a lack of excitement, plastic recycling grinders play a crucial role in the recycling process. These machines are designed to grind and shred plastic waste, breaking it down into smaller pieces that can be processed further. Despite their seemingly mundane function, these grinders are essential for recycling facilities to efficiently sort and process plastic materials, contributing to a more sustainable future. So, while they may not be the most glamorous, these grinders are far from boring in their contribution to environmental conservation.
What You'll Learn
- Plastic Grinder Efficiency: Grinder performance, capacity, and processing speed
- Recycling Grinder Maintenance: Cleaning, lubrication, and troubleshooting techniques for grinders
- Plastic Grinder Safety: Operator training, safety protocols, and emergency procedures
- Grinder Noise and Vibration: Noise reduction, vibration control, and operator comfort
- Plastic Grinder Cost Analysis: Cost-benefit analysis, energy consumption, and operational expenses
Plastic Grinder Efficiency: Grinder performance, capacity, and processing speed
When evaluating the efficiency of plastic grinders, several key factors come into play, primarily focusing on performance, capacity, and processing speed. These aspects are crucial in determining how effectively a grinder can handle the task of breaking down plastic materials, ensuring optimal output and minimizing downtime.
Grinder Performance: This refers to the machine's ability to grind plastic materials efficiently and effectively. High-performance grinders are designed to handle a wide range of plastics, from rigid to flexible, and can process materials at a consistent rate without compromising quality. The performance is often measured by the grinder's ability to reduce the size of the plastic feedstock to a specified mesh size or particle size distribution. For instance, a grinder might be rated for a specific throughput, such as 100 kg/hour, indicating its capacity to process 100 kilograms of plastic per hour under optimal conditions.
Capacity: Capacity is a critical consideration, especially in industrial settings where large volumes of plastic waste need to be processed. A grinder's capacity is determined by its design and power, and it should be able to handle the expected volume of plastic waste without overloading. For example, a 500-liter capacity grinder can process up to 500 liters of plastic waste before requiring maintenance or emptying. The capacity should be chosen based on the scale of the operation, ensuring that the grinder can meet the production demands without becoming a bottleneck.
Processing Speed: The speed at which a grinder can process plastic materials is another essential efficiency metric. This includes the time taken to grind a batch of plastic and the overall cycle time, from feeding the material to producing the final ground product. Faster processing speeds are desirable, especially in high-volume recycling operations, as they reduce the time required for material handling and increase overall productivity. For instance, a grinder might be advertised as having a processing speed of 2 minutes per batch, indicating that it can quickly and efficiently grind a specified amount of plastic waste.
In summary, the efficiency of a plastic grinder is a multifaceted concept, encompassing performance, capacity, and processing speed. Each of these factors plays a significant role in determining the overall effectiveness of the grinding process. By carefully considering these aspects, users can select the most suitable grinder for their specific needs, ensuring efficient and cost-effective plastic recycling operations.
3D-Printed Homes: The Future of Sustainable Housing?
You may want to see also
Recycling Grinder Maintenance: Cleaning, lubrication, and troubleshooting techniques for grinders
Recycling grinders are essential machines in the plastic recycling industry, but they require regular maintenance to ensure optimal performance and longevity. Proper care and maintenance can prevent costly downtime and extend the life of these machines. Here, we delve into the critical aspects of recycling grinder maintenance, focusing on cleaning, lubrication, and troubleshooting techniques.
Cleaning:
Maintaining a clean recycling grinder is paramount to its efficiency and longevity. Over time, plastic materials, fibers, and contaminants accumulate in the grinder, leading to reduced performance and potential damage. Here's a breakdown of the cleaning process:
- Routine Cleaning: Implement a regular cleaning schedule to prevent the buildup of debris. This typically involves shutting down the machine, disconnecting the power source, and using a scraper or spatula to remove any visible plastic residue from the grinder's interior. Pay close attention to the cutting blades, as they are prone to accumulating material.
- Solvent Cleaning: For more stubborn deposits, use a suitable solvent like acetone or mineral spirits. Apply the solvent carefully, ensuring it doesn't come into contact with electrical components. Allow the solvent to dissolve the plastic residue, then wipe it away. Always follow safety guidelines when handling chemicals.
- Water Jet Cleaning: For larger grinders, consider using a water jet cleaning system. This method involves high-pressure water streams to flush out accumulated materials. Ensure the water pressure is controlled to avoid damage to the grinder's components.
Lubrication:
Proper lubrication is vital to minimize friction and wear on the grinder's moving parts. Here's how to maintain lubrication:
- Regular Lubrication: Schedule regular lubrication sessions to keep the grinder's bearings, gears, and other moving parts well-oiled. Use a high-quality industrial lubricant suitable for plastic recycling applications. Apply the lubricant to all relevant points, ensuring an even coating.
- Bearing Maintenance: Focus on the grinder's bearings, as they are susceptible to wear. Regularly inspect the bearings for any signs of damage or wear. Replace worn-out bearings promptly to prevent further issues.
- Oil Change: Periodically change the lubricant to maintain its effectiveness. Over time, lubricants can break down and become contaminated, leading to increased friction and potential damage. Follow the manufacturer's guidelines for the recommended lubrication intervals and types.
Troubleshooting and Maintenance Techniques:
Identifying and resolving issues promptly is crucial to prevent major breakdowns. Here are some troubleshooting tips:
- Regular Inspections: Conduct routine inspections to identify potential problems. Check for unusual noises, vibrations, or changes in performance. Inspect the grinder's housing for any signs of damage or wear.
- Temperature Monitoring: Keep an eye on the grinder's temperature. Excessive heat can indicate issues with the motor, bearings, or lubrication. Addressing temperature-related problems promptly can prevent severe damage.
- Unclogging: Plastic clogs can occur, especially in smaller grinders. Use a plunger or a specialized tool to clear blockages. Never use metal objects, as they can damage the grinder's blades.
- Blade Sharpening: Over time, the grinder's blades may become dull. Inspect the blades regularly and sharpen or replace them as needed. Dull blades can lead to inefficient cutting and increased wear on the machine.
In summary, maintaining a recycling grinder involves a combination of regular cleaning, proper lubrication, and proactive troubleshooting. By following these maintenance practices, recycling facilities can ensure the longevity and reliability of their grinders, ultimately contributing to a more sustainable and efficient recycling process. Remember, regular care can save time and money in the long run.
Black Plastic Takeout Containers: Unraveling the Recycling Mystery
You may want to see also
Plastic Grinder Safety: Operator training, safety protocols, and emergency procedures
Operator Training:
Operating a plastic grinder is a specialized task that requires thorough training to ensure safety and efficiency. All operators should undergo comprehensive training programs that cover the following aspects:
- Machine Familiarity: Operators must become intimately familiar with the plastic grinder's components, functions, and capabilities. This includes understanding the different types of grinders, their power sources, and the various settings and controls.
- Safety Procedures: Training should emphasize the importance of safety and provide detailed instructions on how to operate the machine safely. This includes demonstrating proper guarding techniques, understanding emergency stop protocols, and knowing how to handle and dispose of ground plastic materials safely.
- Maintenance and Care: Operators should be taught how to perform routine maintenance, such as cleaning, lubricating, and inspecting the grinder. They should also be aware of potential issues and know when to seek professional assistance.
- Material Handling: Proper handling of plastic materials is crucial. Training should cover the correct way to load and unload materials, ensuring they are secure and do not pose a risk of injury.
Safety Protocols:
Implementing strict safety protocols is essential to minimize risks associated with plastic grinder operations:
- Personal Protective Equipment (PPE): Operators must wear appropriate PPE, including safety goggles, gloves, and hearing protection. This equipment safeguards against potential hazards like flying debris, sharp edges, and noise.
- Machine Guarding: All moving parts and sharp edges should be properly guarded to prevent accidental contact. Guarding should be checked and maintained regularly to ensure its effectiveness.
- Ventilation and Respiratory Protection: Grinding plastic materials may release fine particles and fumes. Adequate ventilation is crucial, and operators should be trained to use respiratory protection if necessary.
- Emergency Preparedness: Operators should be trained to respond to emergencies promptly. This includes knowing how to shut down the machine in case of an accident, how to clear blockages, and how to handle any spills or fires that may occur.
Emergency Procedures:
In the event of an accident or malfunction, having well-defined emergency procedures is vital:
- Emergency Stop: Operators should know the location and function of emergency stop buttons or switches. Activating this mechanism immediately halts the machine's operation, preventing further hazards.
- Blockage Response: In case of a grinder blockage, operators must be trained to clear it safely. This may involve using appropriate tools and following specific protocols to avoid damage to the machine or injury.
- Fire Safety: Plastic materials can ignite under certain conditions. Operators should be aware of fire safety measures, including the location of fire extinguishers and the proper use of firefighting equipment.
- Medical Assistance: In the event of an injury, operators should know the procedure for summoning medical help and providing first aid until professional assistance arrives.
Regular reviews and updates to training programs are essential to keep operators informed about any changes in safety protocols and emergency procedures. This ensures that the workforce remains prepared and capable of handling the challenges associated with plastic grinder operations.
Unleashing the Power of Recycled Pet Plastic: A Sustainable Revolution
You may want to see also
Grinder Noise and Vibration: Noise reduction, vibration control, and operator comfort
The operation of plastic recycling grinders can be quite noisy and vibrate significantly, which can lead to discomfort for operators and potential long-term health issues. These machines are designed to process large volumes of plastic waste, and the process involves intense mechanical action, often resulting in high noise levels and vibrations. To address these concerns, several strategies can be employed to reduce noise and vibration, thereby improving operator comfort and safety.
Noise reduction is a critical aspect of grinder design. The primary sources of noise in these machines are the rotating blades, the motor, and the material being processed. To mitigate this, engineers can employ several techniques. One approach is to use sound-absorbing materials in the grinder's housing. These materials can include acoustic panels or foam, which help to dampen the sound by absorbing and reflecting it, reducing the overall noise level. Additionally, implementing a noise-dampening system within the motor can further reduce the noise generated by the machinery. This might involve using vibration-damping materials or adding a noise-reducing enclosure around the motor.
Vibration control is another essential consideration. Vibrations can cause fatigue and discomfort for operators, and they can also lead to structural damage over time. To combat this, engineers can design the grinder's base with a vibration-damping system. This could involve using rubber or elastic mounts to decouple the machine from the ground, reducing the transmission of vibrations. Furthermore, implementing a balanced rotor design and using vibration-absorbing materials on the machine's components can significantly decrease the overall vibration levels.
Operator comfort is a key factor in ensuring the safety and productivity of the workforce. High noise and vibration levels can lead to hearing damage, fatigue, and reduced concentration over time. To address this, operators can be provided with personal protective equipment, such as ear protection and vibration-damping gloves. Additionally, implementing ergonomic design principles in the grinder's control panel and operator interface can help reduce the physical strain on workers. This might include adjustable controls, comfortable seating, and well-designed layouts to minimize the need for excessive physical effort.
In summary, by focusing on noise reduction, vibration control, and operator comfort, plastic recycling grinder manufacturers can significantly improve the overall user experience and safety of their machines. These strategies not only benefit the operators but also contribute to a more sustainable and efficient recycling process, ensuring that the machines operate effectively while minimizing their environmental impact.
The Environmental Impact of Recycling Plastic: Is It Worth It?
You may want to see also
Plastic Grinder Cost Analysis: Cost-benefit analysis, energy consumption, and operational expenses
Plastic Grinder Cost Analysis: A Comprehensive Overview
When considering the implementation of plastic recycling grinders, a thorough cost analysis is essential to ensure the project's financial viability and long-term success. This analysis delves into various aspects, including cost-benefit assessments, energy consumption, and operational expenses, providing a comprehensive understanding of the financial implications.
Cost-Benefit Analysis:
The cost-benefit analysis is a critical step in evaluating the economic feasibility of plastic grinders. It involves quantifying the initial investment, operational costs, and potential revenue streams. The initial investment includes the purchase and installation of the grinder, which can vary based on size, capacity, and brand. Larger grinders with higher processing capacities may require a more substantial upfront investment. However, it's important to consider the long-term benefits, such as increased recycling efficiency, reduced waste, and potential cost savings in waste management. The operational costs encompass electricity consumption, maintenance, and potential labor expenses. Efficient grinders with lower energy consumption can significantly reduce operational expenses. Additionally, the potential revenue from selling recycled plastic can offset initial and operational costs, making the process economically viable.
Energy Consumption:
Energy consumption is a key factor in the cost analysis of plastic grinders. Grinders with advanced technologies and efficient designs can significantly reduce power usage. For instance, grinders equipped with variable speed drives allow for precise control over the motor speed, optimizing energy consumption. Lower energy consumption not only reduces operational costs but also contributes to a more sustainable and environmentally friendly process. It is essential to consider the energy source and its associated costs, especially in regions with varying electricity tariffs. Analyzing the energy efficiency of different grinder models can help identify the most cost-effective options without compromising performance.
Operational Expenses:
Operational expenses encompass a range of costs associated with the grinder's daily functioning. These include maintenance, repair, and potential labor costs. Regular maintenance is crucial to ensure the grinder's longevity and optimal performance. This may involve periodic cleaning, lubrication, and replacement of wear-and-tear parts. Additionally, the availability of skilled labor for operation and maintenance can impact overall expenses. It is advisable to consider the long-term operational costs and explore options for reducing these expenses, such as implementing preventive maintenance programs or investing in grinder upgrades that minimize the need for frequent repairs.
In summary, a comprehensive cost analysis of plastic grinders involves a detailed examination of cost-benefit ratios, energy consumption, and operational expenses. By carefully evaluating these factors, recycling facilities can make informed decisions, ensuring that the investment in plastic grinders aligns with financial goals and contributes to a sustainable waste management strategy. This analysis is a vital step in the decision-making process, enabling facilities to maximize the benefits of plastic recycling while minimizing financial risks.
East Lansing's 5-Star Guide to Recycling Plastic: A Green Revolution
You may want to see also
Frequently asked questions
These machines are primarily used in the recycling industry to process and grind plastic waste. They help reduce the size of plastic materials, making it easier to handle and prepare them for further recycling processes. Grinders can process various plastic types, including PET, HDPE, and PP, and are essential for creating a consistent feedstock for recycling facilities.
Boring plastic recycling grinders are specifically designed for the recycling industry and have several unique features. They often have a robust construction to handle the challenging nature of plastic materials, which can be abrasive and have varying shapes and sizes. These grinders typically have a high-speed rotating blade system and a cooling mechanism to prevent overheating during the grinding process.
The use of boring plastic recycling grinders offers several advantages. Firstly, they improve the efficiency of the recycling process by reducing the volume of plastic waste significantly. This reduction in size makes it easier to transport and store the material. Secondly, grinders help ensure a consistent and clean feedstock, which is crucial for maintaining the quality of recycled plastic products. They also help separate different types of plastics, facilitating better sorting and processing.
Yes, environmental impact is an important aspect of using boring plastic recycling grinders. These machines contribute to sustainability by reducing the amount of plastic waste that ends up in landfills or is incinerated. By processing plastic waste, grinders help conserve natural resources and reduce the demand for virgin plastic production, which often relies on fossil fuels. Proper maintenance and regular cleaning of the grinders are essential to prevent any potential environmental hazards, such as the release of fine plastic particles or contaminants.