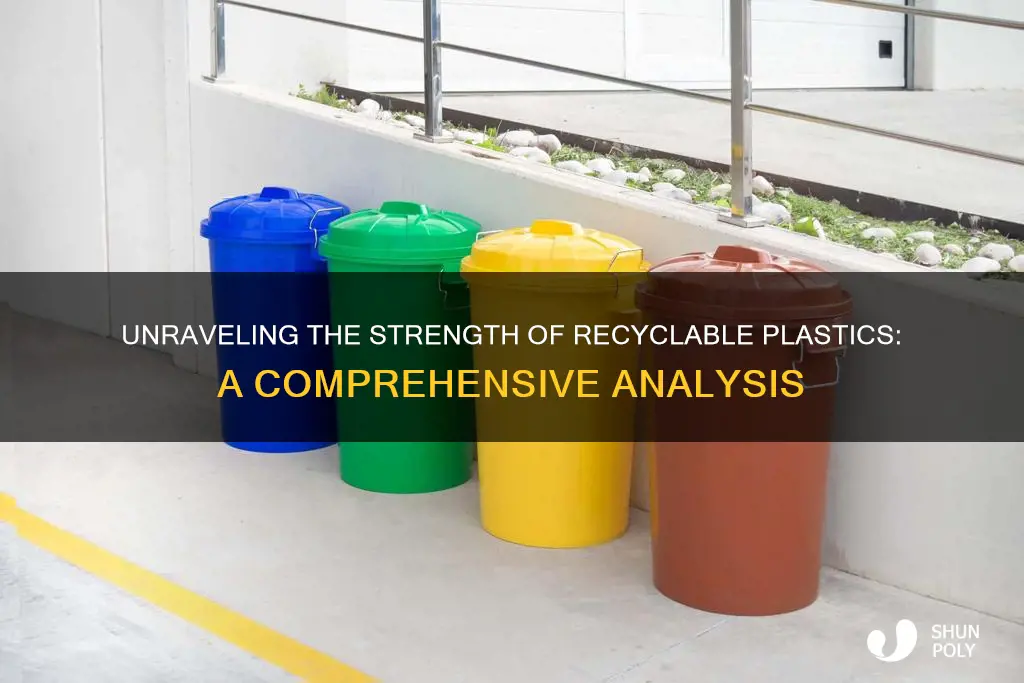
Are recyclable plastics as strong as their virgin counterparts? This question delves into the heart of sustainability and performance. While recyclable plastics are designed to be reused, concerns arise regarding their structural integrity compared to the original, non-recycled materials. This comparison is crucial as it directly impacts the effectiveness of recycling efforts and the overall quality of products made from these plastics. Understanding the strength of recyclable plastics is essential for optimizing their use, ensuring they meet the necessary performance standards, and contributing to a more sustainable future.
What You'll Learn
- Mechanical Properties: Strength, flexibility, and durability of recyclable plastics compared to virgin plastics
- Chemical Resistance: Ability to withstand chemicals without degradation or loss of strength
- Processability: Ease of molding, extrusion, and other manufacturing processes for recyclable plastics
- Environmental Impact: Strength-to-weight ratio and sustainability of recyclable plastics in various applications
- Recycling Technologies: Methods and challenges in recycling plastics to maintain their structural integrity
Mechanical Properties: Strength, flexibility, and durability of recyclable plastics compared to virgin plastics
The debate surrounding the strength and performance of recyclable plastics compared to their virgin counterparts is an important consideration in the context of sustainability and material science. While virgin plastics are known for their high initial strength and durability, the process of recycling can sometimes compromise these properties. However, recent advancements in recycling technologies and material engineering have led to significant improvements in the mechanical properties of recyclable plastics.
In terms of strength, recyclable plastics have made remarkable progress. Modern recycling processes can produce materials that are remarkably similar to their virgin counterparts in terms of tensile strength and impact resistance. For example, high-density polyethylene (HDPE) and polypropylene (PP), which are commonly recycled, can be processed to meet or even exceed the strength of their virgin forms. This is achieved through careful selection of raw materials, advanced recycling techniques, and the addition of reinforcing agents to enhance mechanical properties.
Flexibility is another critical aspect of plastic materials, especially in applications requiring bendability and resilience. Recyclable plastics have demonstrated improved flexibility due to the development of specialized recycling methods. By utilizing processes like extrusion and blow molding, manufacturers can create flexible products from recycled materials that rival the flexibility of virgin plastics. This is particularly evident in the production of plastic films, packaging materials, and flexible containers, where the ability to maintain flexibility without compromising strength is essential.
The durability of recyclable plastics is a key factor in their widespread adoption. While some concerns have been raised about the potential degradation of properties over multiple recycling cycles, significant research and development efforts have addressed these issues. Through the implementation of advanced recycling technologies, such as chemical recycling and depolymerization, it is now possible to break down and regenerate plastics without significant loss of quality. This ensures that recyclable plastics can maintain their durability, making them suitable for long-term applications and reducing the need for frequent replacements.
In summary, the mechanical properties of recyclable plastics have evolved significantly, challenging the notion that they are inherently weaker than virgin materials. Through innovative recycling processes and material engineering, it is now possible to produce recyclable plastics with comparable or even superior strength, flexibility, and durability. As the demand for sustainable alternatives grows, further advancements in recycling technologies will play a crucial role in ensuring that recyclable plastics can meet the performance requirements of various industries, ultimately contributing to a more circular economy.
Gerber's Plastic Baby Food Containers: Unraveling Recycling Potential
You may want to see also
Chemical Resistance: Ability to withstand chemicals without degradation or loss of strength
The chemical resistance of recyclable plastics is a critical factor in determining their strength and durability. When exposed to various chemicals, the ability of these materials to retain their structural integrity is essential for their long-term performance in various applications. This property is particularly important in industries where plastics are used in harsh environments or in contact with corrosive substances.
Recyclable plastics, such as those derived from polypropylene (PP) and high-density polyethylene (HDPE), are known for their excellent chemical resistance. These polymers have a unique molecular structure that allows them to form strong intermolecular bonds, making them highly resistant to chemical degradation. For instance, PP is often used in food packaging due to its ability to withstand a wide range of chemicals, including acids, bases, and solvents, without compromising its mechanical properties. Similarly, HDPE is widely utilized in containers for chemicals and pharmaceuticals because of its exceptional resistance to various solvents and oils.
The chemical resistance of plastics can be attributed to their chemical composition and molecular arrangement. The presence of long-chain aliphatic hydrocarbons in these polymers provides a protective barrier against chemical attack. This barrier prevents the penetration of chemicals, ensuring that the plastic material remains intact. Additionally, the crystalline structure of some plastics, like PP, contributes to their chemical stability by forming a protective layer that resists the intrusion of foreign substances.
In contrast, other types of plastics may not possess the same level of chemical resistance. For example, polyvinyl chloride (PVC) can be susceptible to chemical degradation when exposed to certain solvents and acids. This degradation can lead to a loss of strength and structural integrity, making it less suitable for applications requiring high chemical resistance. Therefore, understanding the chemical properties of different recyclable plastics is crucial in selecting the appropriate material for specific industrial needs.
To ensure the chemical resistance of recyclable plastics, manufacturers employ various techniques during the production process. These include adding stabilizers and modifiers to the polymer matrix, which enhance its ability to resist chemical degradation. By optimizing these processes, engineers can create plastics with improved chemical resistance, making them more versatile and reliable for a wide range of applications. This is particularly important in industries where the longevity and performance of plastic components are critical, such as in the food and beverage, pharmaceutical, and chemical processing sectors.
Can Plastic Cat Litter Jugs Be Recycled? Unraveling the Mystery
You may want to see also
Processability: Ease of molding, extrusion, and other manufacturing processes for recyclable plastics
The processability of recyclable plastics is a critical aspect of their sustainability and performance in various applications. When considering the ease of manufacturing processes for these materials, several factors come into play that influence their processability. One key factor is the molecular structure and chemical composition of the plastic. Different types of recyclable plastics, such as PET (polyethylene terephthalate) and HDPE (high-density polyethylene), have distinct properties that affect their processability. For instance, PET is known for its excellent flow characteristics, making it highly suitable for molding and extrusion processes. Its amorphous structure allows for easy chain movement, facilitating the formation of a uniform and consistent material during manufacturing. On the other hand, HDPE, with its crystalline structure, may exhibit higher melt viscosity, which can impact the ease of processing.
The processability of recyclable plastics is closely tied to their melt flow behavior. Melt flow rate (MFR) is a crucial parameter that indicates how easily a plastic material can be processed and shaped. Materials with higher MFR values are generally more processable, as they flow more readily during extrusion or molding. This property is essential for achieving precise dimensions and minimizing defects in the final products. For example, polypropylene (PP), a common recyclable plastic, often has an MFR that allows for efficient processing, making it a preferred choice for various manufacturing techniques.
In the context of molding, the ease of processing recyclable plastics is evident in their ability to fill molds quickly and uniformly. Plastics with good processability can rapidly take the shape of the mold cavity, reducing the risk of voids or imperfections. This is particularly important in injection molding, where the material's flow characteristics directly impact the quality and consistency of the produced parts. Additionally, the surface finish and dimensional accuracy of the molded parts are influenced by the plastic's processability, ensuring that the final products meet the required specifications.
Extrusion, another common manufacturing process, also benefits from the processability of recyclable plastics. The ease of extrusion is crucial for producing continuous profiles, films, or sheets. Plastics that are easy to extrude can maintain a consistent shape and dimensions throughout the process, resulting in high-quality end products. For instance, polyvinyl chloride (PVC) is often extruded to create pipes, profiles, and various packaging materials, and its processability contributes to the efficiency and reliability of this manufacturing method.
Furthermore, the recyclability of plastics is enhanced by their processability, as it allows for the development of efficient recycling technologies. Recyclable plastics that are easy to process can be effectively sorted, cleaned, and reprocessed without significant losses or quality degradation. This aspect is vital for the circular economy, ensuring that materials can be continuously reused and reducing the environmental impact of plastic production and disposal. In summary, the processability of recyclable plastics, encompassing their molecular structure, melt flow behavior, and molding/extrusion ease, is a key consideration in their overall performance and sustainability.
Recycling Plastic Sheeting: Unraveling the Process and Its Impact
You may want to see also
Environmental Impact: Strength-to-weight ratio and sustainability of recyclable plastics in various applications
The strength-to-weight ratio of recyclable plastics is a critical factor in assessing their environmental impact and sustainability. While many plastics are indeed strong, their weight can be a significant concern, especially in applications where structural integrity is essential. For instance, in the automotive industry, where lightweight materials are highly valued, the strength-to-weight ratio of plastics must be carefully considered. Polypropylene (PP) and high-density polyethylene (HDPE) are two common recyclable plastics used in this sector. PP offers excellent strength and stiffness, making it suitable for interior panels and trim, but its weight can be a drawback in certain components. HDPE, on the other hand, is known for its lightweight nature, which is advantageous for fuel tanks and exterior panels, but it may not provide the same level of structural rigidity as PP.
In contrast, polycarbonate (PC) and acrylonitrile butadiene styrene (ABS) are plastics that excel in terms of impact resistance and strength, making them ideal for applications requiring durability. However, their higher weight can be a challenge, especially in packaging and consumer goods. Here, the focus shifts to the sustainability aspect. The environmental impact of these plastics is not solely determined by their strength but also by their recyclability and the overall lifecycle of the product. For instance, polycarbonate, despite its strength, is not easily recyclable, leading to potential waste accumulation. In contrast, HDPE and PP are more readily recyclable, making them more environmentally friendly choices.
The strength-to-weight ratio also plays a pivotal role in packaging applications. In the food and beverage industry, lightweight packaging is often preferred to reduce transportation costs and carbon emissions. Here, plastics like HDPE and polypropylene are favored for their ability to provide structural integrity while keeping the weight low. However, the trade-off is that these plastics may not be as durable as their heavier counterparts, potentially impacting product protection during transit.
Sustainability in the use of recyclable plastics is a complex issue. While these plastics offer the advantage of being reusable, the process of recycling itself can be energy-intensive and may not always be economically viable. The strength-to-weight ratio, therefore, becomes a critical consideration in the design phase, where engineers must balance performance with environmental impact. For instance, in the construction industry, where structural integrity is paramount, the use of lightweight plastics might be limited, especially in load-bearing applications.
In conclusion, the environmental impact of recyclable plastics is a multifaceted issue, with the strength-to-weight ratio being a key determinant. While some plastics offer exceptional strength, their weight and recyclability can pose challenges. The automotive, packaging, and construction industries, among others, must carefully select materials that meet performance requirements while also considering the environmental consequences. As the demand for sustainable solutions grows, further research and development are necessary to optimize the use of recyclable plastics, ensuring that strength and environmental impact go hand in hand.
Eco-Friendly Blooms: Recycled Plastic's Role in Artificial Flowers
You may want to see also
Recycling Technologies: Methods and challenges in recycling plastics to maintain their structural integrity
Recycling plastics while preserving their structural integrity is a complex task that has garnered significant attention in the field of materials science and environmental sustainability. The challenge lies in maintaining the mechanical properties of recycled plastics to ensure they can perform their intended functions, especially in structural applications. Here, we delve into the various recycling technologies and the hurdles they face in achieving this goal.
One of the primary methods employed in recycling plastics is mechanical recycling, which involves physically breaking down plastic waste into smaller particles or pellets. This process is relatively straightforward but often results in a loss of material properties. The mechanical recycling process typically includes sorting, cleaning, and shredding the plastic waste, followed by granulation to produce recycled plastic pellets. While this method is cost-effective and energy-efficient, it can lead to a decrease in the strength and durability of the recycled material, making it less suitable for structural components. For instance, high-density polyethylene (HDPE) and polypropylene (PP) are commonly recycled through this process, but the resulting material may not meet the required performance standards for applications like construction or automotive parts.
To address the structural integrity issue, chemical recycling has emerged as a promising alternative. This process involves breaking down plastic polymers into their constituent monomers or small molecules using various chemical processes. One such technique is solvent-based recycling, where plastic waste is dissolved in specific solvents to separate the polymers. However, this method can be energy-intensive and may require the use of hazardous chemicals, posing environmental and safety concerns. Another chemical recycling approach is pyrolysis, which involves heating plastic waste in the absence of oxygen to produce a liquid oil and a solid char. While pyrolysis can recover valuable materials, the recycled plastic may not retain its original mechanical properties, limiting its structural applications.
Advanced recycling technologies, such as chemical recycling and depolymerization, offer more tailored solutions. Chemical recycling, as mentioned earlier, can be highly effective in breaking down specific plastic types. For instance, PET (polyethylene terephthalate), commonly used in beverage bottles, can be chemically recycled to its original monomers, allowing for the production of high-quality, structural-grade PET. Depolymerization, on the other hand, involves breaking down plastic polymers into smaller units using enzymes or specific chemicals, offering a more sustainable and environmentally friendly approach. However, these advanced methods are often more expensive and require further research to become economically viable and widely adopted.
The challenges in maintaining structural integrity during plastic recycling are multifaceted. Firstly, the thermal and mechanical processes involved in recycling can cause molecular degradation, leading to reduced strength and stiffness. Additionally, the presence of impurities and contaminants in recycled plastics can further compromise their mechanical properties. Moreover, the compatibility of recycled materials with the original polymer can be an issue, especially when trying to blend different types of plastics. Researchers and engineers are exploring various strategies to overcome these challenges, including developing new recycling processes, improving sorting and cleaning techniques, and designing plastics with better recyclability in mind.
In conclusion, recycling plastics while preserving their structural integrity is a critical aspect of sustainable materials management. Mechanical recycling, while simple, often falls short in maintaining material properties. Chemical and advanced recycling technologies offer more promising avenues, but they come with their own set of challenges. The key to success lies in continued research, innovation, and collaboration between scientists, engineers, and the plastics industry to develop efficient recycling methods that can produce high-quality, structurally sound recycled plastics. This will not only contribute to environmental sustainability but also ensure the longevity and performance of plastic products in various industries.
Unraveling NYC's Plastic Cup Recycling Mystery: What You Need to Know
You may want to see also
Frequently asked questions
Not necessarily. While the process of recycling can sometimes enhance the properties of certain plastics, it is not always the case. The strength of recyclable plastics can vary depending on the type of plastic, the recycling process, and the quality of the recycled material. Some plastics may lose strength during recycling due to degradation or contamination.
It depends on the specific plastic type. For example, PET (polyethylene terephthalate) bottles, which are commonly recycled, can often maintain their structural integrity and strength when recycled. However, other types like HDPE (high-density polyethylene) or certain polypropylene (PP) containers might not retain the same level of strength after recycling.
Yes, it is a consideration. Manufacturers often need to ensure that recycled plastics meet specific strength requirements to produce reliable and durable products. In some cases, a blend of recycled and virgin materials might be used to achieve the desired strength and performance.
Absolutely! Researchers and companies are constantly developing new methods to enhance the properties of recycled plastics. For instance, advanced recycling techniques, such as chemical recycling, can produce high-quality recycled materials with improved strength and durability, making them suitable for various applications.