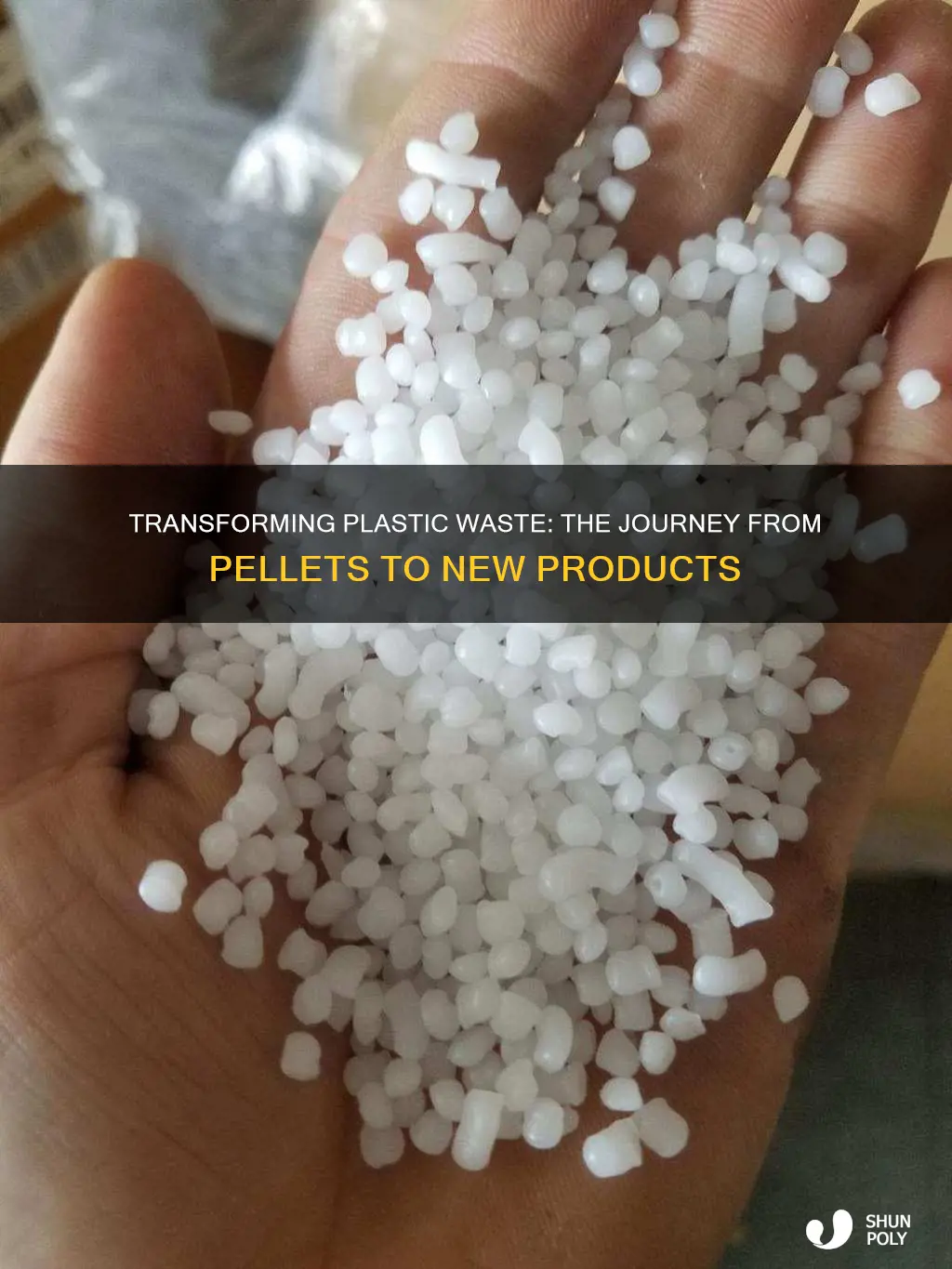
Recycled plastic pellets, also known as plastic resin pellets, are a crucial component in the manufacturing of various plastic products. These pellets are produced through a meticulous process that begins with collecting and sorting plastic waste. The waste is then cleaned and shredded into small pieces, which are further sorted and classified based on their type and color. After sorting, the plastic is washed to remove any contaminants, and the material is ground into a fine powder. This powder is then heated and extruded through a die to form small, uniform pellets. These pellets are cooled and dried, ensuring they are ready for use in the production of new plastic items, contributing to a more sustainable and circular economy.
What You'll Learn
- Collection: Plastic waste is gathered from various sources, ensuring it's clean and free from contaminants
- Sorting: Materials are sorted by type and color to facilitate the recycling process
- Shredding: Plastic is shredded into small pieces, making it easier to process further
- Melting: The shredded plastic is melted down to form a molten mass
- Pelletizing: Molten plastic is extruded and cut into small, uniform pellets for reuse
Collection: Plastic waste is gathered from various sources, ensuring it's clean and free from contaminants
The process of collecting plastic waste for recycling begins with a meticulous and organized approach to ensure the highest quality of raw materials. The collection phase is a critical step as it sets the foundation for the entire recycling process. Plastic waste is gathered from various sources, including residential areas, commercial facilities, industrial sites, and public spaces. This diverse range of sources is essential to ensure a steady and comprehensive supply of plastic materials.
Residential areas play a significant role in this process, where individuals and families contribute by sorting and separating their plastic waste. This can include items like water bottles, food containers, packaging materials, and even small plastic toys. Encouraging proper waste segregation at the source is crucial to prevent contamination and ensure the plastic is suitable for recycling. Local governments and community organizations often provide guidelines and infrastructure to facilitate this, making it easier for residents to participate.
Commercial facilities, such as offices, restaurants, and retail stores, also contribute significantly. These establishments generate substantial amounts of plastic waste daily, including packaging, food containers, and disposable items. Implementing waste management systems tailored to their specific needs is essential. This may involve providing dedicated bins for different types of plastics, ensuring that waste is sorted and stored correctly before collection.
Industrial sites, including manufacturing plants and warehouses, present unique challenges and opportunities. These facilities often produce large volumes of plastic waste, often requiring specialized collection methods. Industrial waste may include plastic scraps, packaging materials, and even larger items like machinery parts. Collaborating with industrial partners to establish efficient collection systems is vital, ensuring that plastic waste is removed promptly and efficiently.
Public spaces, such as parks, beaches, and streets, also play a role in the collection process. These areas may have unique challenges, such as managing litter and ensuring accessibility for collection vehicles. Community clean-up events and volunteer programs can be organized to engage the public in collecting and sorting plastic waste. This not only helps in gathering materials but also raises awareness about the importance of proper waste management.
Ensuring that the collected plastic waste is clean and free from contaminants is paramount. Contamination can occur during transportation or storage, leading to potential issues during the recycling process. To maintain cleanliness, collection vehicles and containers should be properly sealed and regularly sanitized. Additionally, implementing strict sorting procedures at collection centers is essential. This involves trained personnel who can identify and separate different types of plastics, ensuring that only clean and sorted materials proceed to the next stage of recycling.
Unraveling the Mystery: Can Plastic Binder Dividers Be Recycled?
You may want to see also
Sorting: Materials are sorted by type and color to facilitate the recycling process
The initial step in the recycling process of plastic pellets is sorting, a crucial phase that ensures the efficiency and effectiveness of the entire recycling chain. This process involves a meticulous and organized approach to separate different types of plastic materials, a task that is both complex and essential. The primary goal is to categorize plastics based on their resin types, a classification that is fundamental to the recycling process. This classification is typically done using a system that identifies the specific type of plastic, such as PET (polyethylene terephthalate), HDPE (high-density polyethylene), or LDPE (low-density polyethylene), among others. Each type of plastic has unique properties and is used in various applications, and proper sorting ensures that the materials can be recycled appropriately.
Color sorting is another critical aspect of this process. Plastic items come in various colors, and this step ensures that the recycling process can handle these colors effectively. Different colors often indicate different types of plastic, and this separation is vital as it allows for the creation of a more uniform and consistent product. For instance, clear PET bottles and green HDPE milk jugs are sorted separately to avoid contamination and ensure the quality of the recycled material. This color-coding system is a standard practice in recycling facilities and helps in the efficient processing of plastics.
The sorting process is typically carried out by trained personnel who use their expertise to identify and separate the materials. They may use hand-sorting techniques, where they visually inspect and manually separate the items, or they might employ advanced technologies such as near-infrared (NIR) spectroscopy. NIR systems can identify different types of plastics based on their molecular structure, providing a rapid and accurate method of sorting. This technology is particularly useful for identifying mixed-color or opaque plastics, which can be challenging to sort by hand.
In some cases, automated sorting systems are utilized, which can significantly increase the speed and accuracy of the process. These systems use a combination of air jets, water streams, and conveyor belts to separate materials based on their density and shape. For example, a plastic bottle can be separated from a plastic bag by using air to blow away the lighter bag, while the denser bottle remains in place. This automated approach is efficient and can handle large volumes of waste, making it a preferred method in many recycling facilities.
After sorting, the materials are then prepared for the next stage of recycling, which may involve cleaning, shredding, or melting, depending on the desired end product. The sorted and cleaned plastics are fed into machines that process them into small pellets, which can be used to create new products. This entire process, from sorting to pellet production, is a well-organized and intricate system that ensures the effective recycling of plastic materials, contributing to a more sustainable and environmentally friendly approach to waste management.
Plastic Planters: Can They Be Recycled?
You may want to see also
Shredding: Plastic is shredded into small pieces, making it easier to process further
The process of shredding plastic is a crucial step in the transformation of waste plastic into valuable recycled pellets. This initial stage involves breaking down larger plastic items or materials into smaller, more manageable pieces. The shredding process is designed to reduce the size of the plastic, making it easier to handle and process in subsequent steps.
When plastic is shredded, it undergoes a mechanical transformation. Large plastic items, such as bottles, containers, or even plastic-based packaging, are fed into a shredder. The shredder's powerful blades rotate at high speeds, cutting and tearing the plastic into tiny fragments. This process can be likened to finely chopping a block of wood, where the wood fibers are reduced to smaller pieces, making it more accessible for further processing.
The shredded plastic pieces are typically much smaller than the original items, often resembling tiny flakes or pellets. This reduction in size is intentional, as it prepares the plastic for the next phase of recycling. Smaller pieces have a larger surface area, which is beneficial for various downstream processes. For instance, it allows for better mixing and blending during the pelletization stage, ensuring a more homogeneous final product.
Shredding also plays a vital role in removing contaminants and improving the quality of the recycled plastic. As the plastic is shredded, any non-plastic materials or impurities become more separated from the plastic itself. This separation aids in the removal of labels, caps, or other non-plastic components, resulting in a cleaner and more pure plastic feedstock. By doing so, the shredded plastic is better suited for further processing and the creation of high-quality recycled pellets.
In summary, shredding is a critical step in the recycling process, enabling the efficient breakdown of plastic waste. It facilitates the subsequent stages of recycling, enhances the quality of the recycled material, and sets the foundation for the production of valuable recycled plastic pellets. This initial mechanical process is a key component in the journey towards a more sustainable and circular economy.
Recycling Plastic Toilet Seats: A Guide for Minneapolis Residents
You may want to see also
Melting: The shredded plastic is melted down to form a molten mass
The process of transforming shredded plastic into recycled pellets begins with the melting stage, a crucial step in the recycling journey. Once the plastic waste has been sorted, cleaned, and shredded into small pieces, it is time to melt these fragments. This melting process is carried out in specialized equipment designed to handle the unique properties of plastic.
In the melting process, the shredded plastic is fed into a large industrial furnace or a specialized melting machine. The temperature inside these machines is carefully controlled to ensure the plastic reaches its melting point without burning or degrading. The melting point varies depending on the type of plastic, but common materials like PET (polyethylene terephthalate) and HDPE (high-density polyethylene) have specific temperature requirements. For instance, PET typically melts at around 250-260°C (482-518°F), while HDPE melts at approximately 130-140°C (266-284°F).
As the shredded plastic is heated, it undergoes a phase change from a solid to a liquid state, forming a molten mass. This molten plastic is a viscous, sticky substance, often with a distinct color depending on the original plastic type. The color can range from clear to various shades of green, brown, or even black, depending on the impurities present in the feedstock. The molten mass is then carefully handled to ensure it doesn't cool and solidify prematurely, which could lead to difficulties in the subsequent steps.
During the melting process, it is essential to maintain a consistent temperature and stirring to ensure the plastic melts evenly and completely. This step requires skilled operators who can monitor the temperature, pressure, and flow of the molten plastic to achieve the desired consistency. Once the plastic is fully melted, it is ready for the next phase, where it is often extruded into pellets for easy transportation and reuse in various industrial applications.
The melting stage is a critical step in recycling plastic, as it prepares the material for further processing and ensures that the final product meets the required specifications. It is a complex process that requires precision and expertise to handle the unique challenges posed by different types of plastics.
Unraveling the Mystery: Can Plastic Rings Be Recycled?
You may want to see also
Pelletizing: Molten plastic is extruded and cut into small, uniform pellets for reuse
The process of creating recycled plastic pellets begins with the collection and sorting of plastic waste. This waste is then cleaned and prepared for the next stage. Once the plastic is ready, it is shredded or granulated to reduce its size and make it easier to handle. This step ensures that the plastic is in a consistent and manageable form before it enters the pelletizing process.
Pelletizing is a crucial step in the recycling chain, where the real transformation happens. It involves a process called 'extrusion', where the shredded plastic is heated to its molten state. This molten plastic is then forced through a small opening, or die, using a machine called an extruder. The extruder applies heat and pressure to the plastic, allowing it to flow and take the shape of the die. This process creates a continuous strand of molten plastic.
The key to successful pelletizing is the subsequent step of cutting the extruded strand into small, uniform pellets. This is typically done using a water-cooled cutting mechanism. As the molten plastic strand exits the die, it is immediately cooled by water, which solidifies the plastic and allows it to be cut into precise, consistent pellets. The cutting process requires precision to ensure that each pellet has the desired size and weight, which is crucial for their reuse in various applications.
The resulting pellets are then dried to remove any moisture and ensure they are ready for storage or further processing. These pellets can now be used as raw material for manufacturing new products, such as packaging, furniture, or even construction materials. The beauty of this process is that it gives new life to plastic waste, reducing the demand for virgin plastic production and minimizing environmental impact.
Pelletizing is an efficient and sustainable method of recycling plastic, allowing for the creation of high-quality recycled plastic pellets. This process not only reduces waste but also contributes to a circular economy, where resources are reused and repurposed, minimizing the environmental footprint of plastic production.
Cost-Effective Building: Recycled Plastic Bricks vs. Regular Bricks
You may want to see also
Frequently asked questions
The recycling process begins with collecting and sorting plastic waste. This waste is then cleaned and shredded into small pieces. These pieces are further processed through a washing and drying process to remove any contaminants. The cleaned plastic is then ground into a fine powder and fed into a pelletizing machine. This machine melts the plastic and extrudes it through a die, forming small, uniform pellets. These pellets are then cooled and can be used as raw material for manufacturing various products.
Recycled plastic pellets are an eco-friendly alternative to virgin plastic pellets. They offer several advantages. Firstly, they reduce the demand for raw materials, conserving natural resources. The recycling process also helps minimize the amount of plastic waste ending up in landfills or polluting the environment. Additionally, recycled plastic can often be processed at lower temperatures, making it an energy-efficient choice. These pellets can be used to produce a wide range of products, from packaging materials to automotive parts, contributing to a more sustainable manufacturing process.
Yes, several types of plastic are commonly recycled and transformed into pellets. These include Polyethylene Terephthalate (PET), High-Density Polyethylene (HDPE), Polypropylene (PP), and Polyethylene (PE). PET is widely used in beverage bottles and food containers. HDPE is commonly found in milk jugs and shampoo bottles. PP is known for its durability and is used in various packaging and consumer products. PE, on the other hand, is versatile and utilized in a wide array of applications, including film, containers, and pipes. The recycling process ensures that these materials can be reused, reducing the reliance on new plastic production.
Absolutely! Recycled plastic pellets have found their way into innovative manufacturing processes like 3D printing and injection molding. In 3D printing, these pellets can be used to create custom parts and prototypes, offering a sustainable and cost-effective solution. The pellets can be melted and extruded through a nozzle, layer by layer, to build complex structures. Additionally, recycled plastic can be blended with other materials to enhance its properties, making it suitable for various advanced manufacturing applications. This approach promotes sustainability and reduces the environmental impact of traditional manufacturing methods.