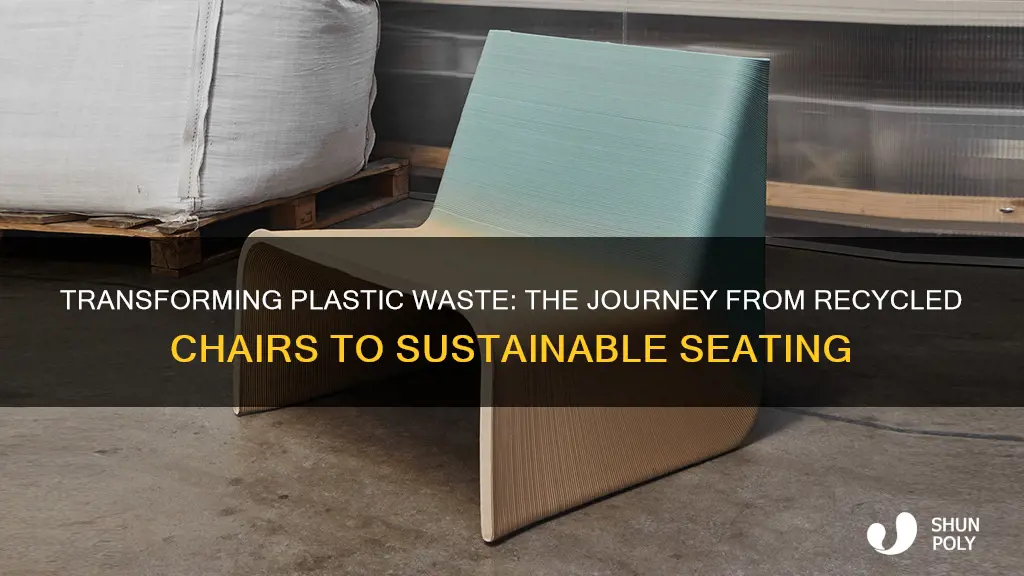
Recycled plastic chairs are an eco-friendly alternative to traditional furniture, offering durability and low maintenance. The process of creating these chairs involves several steps. First, plastic waste, such as bottles and containers, is collected and sorted. Then, the plastic is cleaned, shredded, and melted into pellets. These pellets are then heated and extruded into a continuous sheet, which is cooled and cut into smaller pieces. Finally, the plastic pieces are formed into chair frames using injection molding or blow molding techniques, resulting in sturdy and lightweight chairs that can be easily recycled again at the end of their life cycle.
What You'll Learn
- Collection: Plastic chairs are gathered from various sources, including recycling centers and consumer drop-offs
- Sorting: Materials are sorted by type and color to ensure quality and consistency in the recycling process
- Cleaning: Chairs are cleaned to remove contaminants and ensure the plastic is free from debris and residue
- Shredding/Grinding: Plastic is shredded or ground into small pieces, preparing it for the next stage of processing
- Melting and Molding: The shredded plastic is melted and then molded into new chair shapes using injection molding techniques
Collection: Plastic chairs are gathered from various sources, including recycling centers and consumer drop-offs
The process of creating recycled plastic chairs begins with the crucial step of collection, which is a vital phase in the entire recycling journey. Plastic chairs, like any other recycled product, start their transformation from various sources, ensuring a steady supply of raw materials for manufacturers.
One primary source of collection is recycling centers, which act as hubs for waste management. These centers are equipped to handle large volumes of plastic waste, including chairs, tables, and other furniture. Here, the chairs are sorted, cleaned, and prepared for the next stage of recycling. Recycling centers often have specialized equipment to break down the chairs, ensuring that the plastic is not contaminated with other materials, which is essential for maintaining the quality of the final product.
In addition to recycling centers, consumer drop-offs play a significant role in the collection process. Many communities and organizations encourage residents to donate their used plastic chairs, promoting environmental awareness and sustainability. These drop-off points can be located at local government facilities, community centers, or even private recycling companies. By providing a convenient way for individuals to contribute, consumer drop-offs ensure a diverse and widespread collection of plastic chairs, making the recycling process more accessible and inclusive.
The collection process is a critical step as it sets the foundation for the entire recycling journey. It requires efficient organization and coordination to ensure that the plastic chairs are properly sorted, stored, and transported to the recycling facilities. This step also involves educating the public about the importance of recycling and providing clear guidelines on how and where to drop off their used plastic furniture.
Once collected, the plastic chairs are transported to specialized recycling facilities, where they undergo further processing to be transformed into new products. This collection phase is a crucial link in the chain, as it directly impacts the quality and quantity of recycled plastic available for manufacturing recycled plastic chairs and other sustainable products.
Sticker Removal: A Simple Step for Plastic Recycling Success
You may want to see also
Sorting: Materials are sorted by type and color to ensure quality and consistency in the recycling process
The initial step in the recycling process of plastic chairs involves meticulous sorting, a critical phase that significantly impacts the quality and consistency of the final product. This sorting process is a meticulous art, ensuring that each piece of plastic is directed towards the appropriate recycling stream. The primary goal is to separate materials by type and color, a practice that is both essential and challenging.
In the recycling facility, workers or automated systems meticulously examine each chair, identifying the type of plastic used. Common types include polypropylene (PP), high-density polyethylene (HDPE), and polycarbonate (PC), each with unique properties and recycling requirements. For instance, PP is often used in outdoor furniture due to its durability, while HDPE is prevalent in household containers. This identification is crucial as it determines the subsequent steps in the recycling journey.
Color sorting is another critical aspect of this process. Plastic chairs can vary in color, from vibrant hues to more subdued tones, and this diversity must be managed. Advanced sorting techniques, such as near-infrared (NIR) spectroscopy, can identify different colors and types of plastic with high accuracy. This technology ensures that similar colors are grouped together, facilitating the production of consistent and aesthetically pleasing recycled products.
The sorted materials are then directed to specific processing lines. For instance, HDPE chairs might be sent to a facility specializing in producing new containers, while PP chairs could be transformed into outdoor furniture or construction materials. This targeted approach maximizes the potential of each plastic type, reducing waste and increasing the efficiency of the recycling process.
In summary, the sorting phase is a pivotal stage in recycling plastic chairs, requiring precision and attention to detail. By separating materials by type and color, recycling facilities can ensure that the recycled plastic chairs meet quality standards and contribute to a more sustainable future. This process is a testament to the intricate art of recycling, where every step is carefully planned to transform waste into valuable resources.
Eco-Friendly Fun: Recycle Plastic Toys for a Greener Future
You may want to see also
Cleaning: Chairs are cleaned to remove contaminants and ensure the plastic is free from debris and residue
The cleaning process is a crucial step in preparing recycled plastic chairs for their new life. It involves a meticulous approach to ensure the plastic is in optimal condition and ready for further processing. Here's a detailed breakdown of the cleaning procedure:
Initial Inspection and Sorting: Before cleaning, a thorough inspection of the chairs is essential. This step helps identify any significant damage, heavy contamination, or unusual materials that might require special handling. Chairs are sorted based on their color, size, and the type of plastic they are made from. This sorting process ensures that similar materials are grouped together, making the cleaning process more efficient.
Debris Removal: The first step in cleaning is to remove any loose debris and contaminants from the plastic surface. This can be achieved through various methods, including mechanical brushing or air blowers. For more intricate designs and hard-to-reach areas, a soft-bristled brush or a vacuum with a small nozzle can be used to ensure no debris remains. This step is vital as it prevents the accumulation of dirt and grime, which could affect the final product's appearance and durability.
Chemical Cleaning: After mechanical cleaning, a chemical process is often employed to eliminate stubborn contaminants. This method involves using specific cleaning agents that are safe for the type of plastic being processed. The chairs are submerged in a solution or sprayed with a chemical cleaner, allowing the agent to penetrate and dissolve any remaining impurities. Common chemicals used include detergents, solvents, and even natural cleaning agents like citrus-based solutions, which are environmentally friendly.
Rinsing and Water Cleaning: After chemical treatment, thorough rinsing is necessary to remove any residual cleaning agents. Chairs are thoroughly washed with clean water to ensure no chemical residue remains. This step is crucial to prevent any potential chemical reactions or discoloration in the final product. Water cleaning can be done using high-pressure water jets or sprayers, ensuring that all surfaces are thoroughly cleaned.
Drying and Final Inspection: Once cleaned, the chairs are carefully dried to prevent any moisture-related issues. Air drying or using low-heat blowers is recommended to avoid damage to the plastic. After drying, a final inspection is conducted to ensure no contaminants or residue are left. This inspection also includes checking for any signs of wear and tear during the cleaning process, ensuring the chairs are in pristine condition for the next stage of production.
The cleaning process is a critical phase in recycling plastic chairs, as it directly impacts the quality and longevity of the final product. By employing these detailed cleaning techniques, the chairs are prepared for further transformation, ensuring they meet the desired standards and are ready for their new purpose.
The Surprising Truth: Are Plastic Cups Recycle-Worthy?
You may want to see also
Shredding/Grinding: Plastic is shredded or ground into small pieces, preparing it for the next stage of processing
The process of recycling plastic chairs begins with the collection and sorting of used plastic items. Once sorted, the plastic chairs are prepared for the recycling process, which involves shredding or grinding the plastic into small pieces. This initial step is crucial as it prepares the plastic for further processing and ensures that it can be effectively transformed into new products.
Shredding and grinding are essential processes in the recycling chain. Plastic chairs, often made from materials like polypropylene (PP) or polyethylene (PE), are fed into a shredding machine. The machine's sharp blades cut the plastic into uniform, small pieces, typically in the form of flakes or pellets. This process is designed to reduce the size of the plastic, making it easier to handle and process in subsequent stages. The shredded plastic is then conveyed to a grinding machine, which further reduces the size of the flakes. Grinding involves using a rotating blade or a hammer mill to break down the plastic into even smaller particles, often in the form of fine powder or granulate. This step ensures that the plastic is in a consistent and manageable form, facilitating the next phase of recycling.
The shredded and ground plastic is now ready for further processing, which may include washing, drying, and sorting to remove any contaminants. This step is critical to ensure the quality of the recycled material. After cleaning, the plastic pieces are often sorted by type and color to maintain consistency in the final product. This sorting process can be done manually or through automated systems, depending on the recycling facility's setup.
Once sorted, the plastic flakes or granules are ready for the next major step in the recycling process, which could involve melting and reforming the plastic into new products, such as recycled plastic chairs. This process requires specialized equipment and techniques to transform the shredded plastic back into a usable material. The specific methods used will depend on the type of plastic and the desired end product. For example, some recycling facilities may use a process called 'pelletizing' to create solid plastic pellets, which can then be used as raw material for manufacturing new plastic chairs or other products.
In summary, the shredding and grinding process is a vital part of recycling plastic chairs, as it prepares the plastic for further processing and ensures that it is in a suitable form for the creation of new products. This initial stage sets the foundation for the entire recycling journey, contributing to a more sustainable approach to waste management and the production of eco-friendly furniture.
The Plastic Recycling Myth: Unveiling the Truth
You may want to see also
Melting and Molding: The shredded plastic is melted and then molded into new chair shapes using injection molding techniques
The process of transforming recycled plastic into chairs involves a fascinating journey from waste to new product. Once the plastic waste is collected and sorted, the journey begins with shredding. Plastic items, such as old chairs, bottles, or packaging, are shredded into small pieces, often referred to as 'flakes' or 'shreds'. This step is crucial as it prepares the plastic for the next phase, ensuring a consistent and uniform material.
The shredded plastic is then sent to a processing plant where the magic happens. Here, the plastic flakes are fed into a large machine, typically an extruder. This machine plays a vital role in the melting and molding process. The extruder heats the shredded plastic to a specific temperature, usually around 250-300 degrees Celsius, causing it to melt and become a molten mass. This molten plastic is then forced through a die, which is shaped like the desired chair form.
Injection molding is the technique used to shape the plastic. It involves injecting the heated and pressurized molten plastic into a mold cavity. The mold is designed with the specific chair shape in mind, including the frame, seat, and backrest. As the plastic is injected, it rapidly cools and solidifies, taking the form of the mold. This process is highly controlled to ensure the final product meets the required specifications.
Once the plastic has cooled and hardened, the chair is removed from the mold. This newly formed chair is now ready for further finishing touches, such as adding legs, cushions, or decorative elements. The entire process, from shredding to molding, is an efficient and sustainable way to recycle plastic, reducing waste and giving new life to old materials. This method not only creates durable and eco-friendly chairs but also contributes to a circular economy, minimizing the environmental impact of plastic production.
Dunkin' Donuts' Plastic Cups: The Recycling Conundrum
You may want to see also
Frequently asked questions
Recycled plastic chairs are primarily made from post-consumer or post-industrial plastic waste. This waste can include various types of plastic, such as PET (polyethylene terephthalate), HDPE (high-density polyethylene), or even mixed plastics. The plastic is collected, sorted, and processed to be transformed into new products.
The recycling journey starts with the collection of plastic waste from various sources. This can be from households, commercial facilities, or industrial sites. The waste is then sorted based on the type of plastic, color, and quality to ensure the recycling process is efficient and effective.
The recycling process involves several steps. First, the sorted plastic waste is cleaned and shredded into small pieces. These pieces are then melted and formed into pellets, which are like small plastic beads. These pellets are the raw material for manufacturing. The pellets are heated and extruded through a die to create a continuous sheet or strand of plastic. This strand is then cooled and cut into desired lengths, which are then used to create chair frames and other components.
Yes, the plastic strands are often injection-molded or blow-molded to create the chair's structure. Injection molding involves injecting the heated plastic into a mold, shaping it into the desired chair form. Blow molding is used for hollow objects and involves inflating a plastic tube within a mold to create the chair's shape. These processes ensure the chairs are durable and can withstand various environmental conditions.
Recycled plastic chairs offer several advantages. They are highly durable and resistant to corrosion, rust, and fading. Unlike wooden chairs, they do not require regular painting or staining. Plastic chairs are also lightweight, making them easy to move around. Additionally, the recycling process reduces the demand for virgin resources and minimizes the environmental impact associated with traditional chair manufacturing.