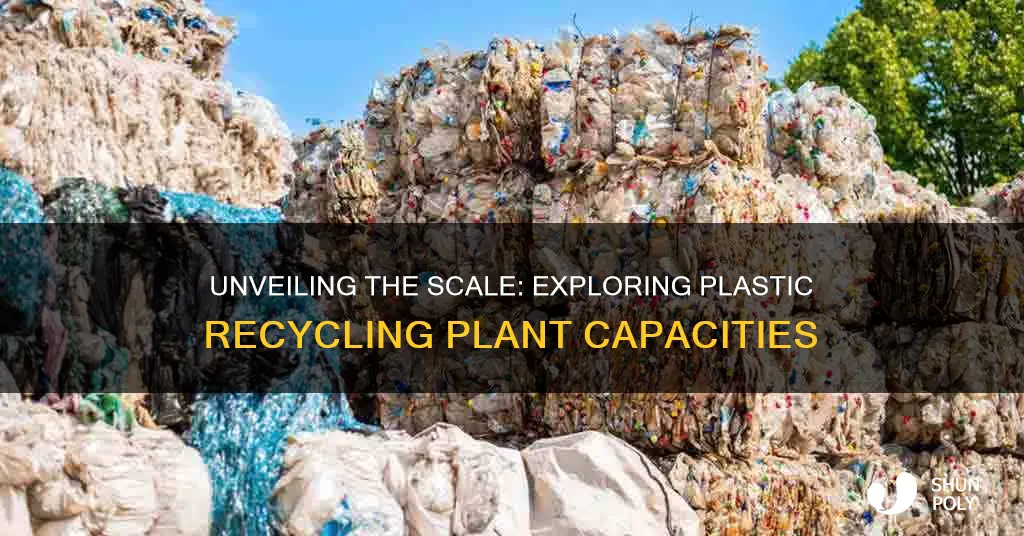
Plastic recycling plants play a crucial role in the global effort to manage and reduce plastic waste. The size and capacity of these facilities can vary significantly depending on factors such as the type of plastic processed, the scale of operation, and the desired output. From small-scale community initiatives to large industrial operations, plastic recycling plants can range from a few hundred square meters to several hectares. Understanding the dimensions and capabilities of these plants is essential to grasp their impact on the environment and the efficiency of plastic waste management.
What You'll Learn
- Plant Size: From small-scale to large industrial facilities, recycling plants vary in size
- Capacity: Daily processing capacity ranges from tons to hundreds of tons
- Equipment: Specialized machinery like shredders, sorters, and washing lines
- Location: Plants are often located near waste sources for efficiency
- Energy Use: Energy consumption varies based on plant size and technology
Plant Size: From small-scale to large industrial facilities, recycling plants vary in size
The size of a plastic recycling plant can vary significantly, ranging from small-scale operations to large industrial facilities. This variation is primarily due to the scale of the recycling process, the volume of plastic waste processed, and the specific recycling techniques employed. Understanding these differences is crucial for anyone involved in the plastic recycling industry, from investors and entrepreneurs to policymakers and environmental enthusiasts.
Small-scale plastic recycling plants are often found in local communities and are designed to handle a limited amount of plastic waste. These facilities typically process plastic through manual sorting, cleaning, and reprocessing. They might use basic machinery like shredders and granulators to break down plastic waste into smaller pieces or pellets. The output of these small-scale plants is usually directed towards local markets or used for small-scale manufacturing. For instance, a small-scale plant might supply recycled plastic pellets to a local toy manufacturer or produce plastic packaging for small businesses.
In contrast, large industrial recycling plants are designed to process vast amounts of plastic waste on a continuous basis. These facilities often have the capacity to handle several tons of plastic per day and are equipped with advanced machinery and processes. Large plants may employ automated sorting systems, advanced cleaning technologies, and sophisticated reprocessing methods. For example, they might use advanced washing systems to remove contaminants, and extrusion lines to melt and reform the plastic into new products. The output of these large plants can be directed towards a wide range of applications, including the production of new plastic packaging, construction materials, automotive parts, and even new plastic bottles and containers.
The size of the plant also influences the types of plastic it can process. Larger plants often have the capability to handle a broader range of plastic types, including those that are more challenging to recycle. This is because larger facilities can invest in more advanced sorting and processing technologies, allowing them to separate and recycle a wider variety of plastics. For instance, a large industrial plant might be able to process not only common plastics like PET and HDPE but also more specialized types like PP, PS, and even certain types of PVC.
Additionally, the size of the plant can impact the efficiency and cost-effectiveness of the recycling process. Larger plants often benefit from economies of scale, where the cost per unit of output decreases as the volume of production increases. This can make large-scale recycling more financially viable and environmentally sustainable. However, small-scale plants also have their advantages, such as being more flexible and able to adapt quickly to local needs and opportunities.
In summary, the size of a plastic recycling plant is a critical factor that influences its capacity, capabilities, and impact. From small-scale local operations to large industrial facilities, each type of plant plays a unique role in the recycling process, contributing to a more sustainable and circular economy. Understanding these variations can help stakeholders make informed decisions about investment, policy, and environmental initiatives related to plastic recycling.
The Recycling Myth: Unveiling America's Plastic Waste Crisis
You may want to see also
Capacity: Daily processing capacity ranges from tons to hundreds of tons
The daily processing capacity of a plastic recycling plant can vary significantly, typically ranging from a few tons to several hundred tons of plastic waste. This wide range is primarily due to the plant's size, technology, and the specific processes employed. Smaller, local recycling facilities often process a few tons of plastic daily, focusing on serving nearby communities and handling more specialized or challenging materials. These plants may use manual sorting and processing methods, which are less efficient but can be more cost-effective for smaller operations.
In contrast, larger, more industrial plastic recycling plants can process hundreds of tons of plastic waste daily. These facilities are often equipped with advanced machinery and automated systems, allowing for higher throughput and more efficient processing. They can handle a broader range of plastic types and can produce a more consistent output, which is crucial for supplying the market with recycled materials. The increased capacity of these plants is essential to meet the growing demand for recycled plastics in various industries.
The daily processing capacity is influenced by several factors, including the plant's design, the availability of raw materials, and the market demand for recycled plastics. Plants with higher capacities often have larger storage areas, more efficient sorting systems, and the ability to process a wider variety of plastic types. They may also have additional facilities for washing, shredding, and pelletizing the plastic, which are essential steps in the recycling process.
For instance, a typical mid-sized plastic recycling plant might process around 50-100 tons of plastic daily. This capacity allows them to serve a regional market and contribute to the circular economy by providing high-quality recycled materials. Such plants often have a combination of manual and automated processes, ensuring efficiency and consistency in their operations.
In summary, the size and capacity of a plastic recycling plant are critical considerations in the recycling process. Plants with lower daily processing capacities cater to local needs and may use simpler methods, while larger plants with higher capacities can handle more significant volumes of waste and produce a more substantial supply of recycled plastics, contributing to a more sustainable and circular economy.
Juice Carton Recycling: Unraveling the Paper-Plastic Mystery
You may want to see also
Equipment: Specialized machinery like shredders, sorters, and washing lines
The equipment used in a plastic recycling plant is a crucial aspect that determines its efficiency and capacity. Specialized machinery is designed to handle the unique challenges of processing plastic waste, ensuring that it can be effectively sorted, cleaned, and transformed into reusable materials. Here's an overview of the key equipment:
Shredders: These machines are the first line of defense in the recycling process. Shredders are powerful and robust, capable of reducing large plastic items into smaller pieces. They come in various types, including single-shaft and double-shaft shredders, each with its own advantages. Single-shaft shredders are versatile and can handle a wide range of materials, making them suitable for initial processing. Double-shaft shredders, on the other hand, offer more power and are ideal for handling dense and heavy plastic waste. The shredded plastic is then moved to the next stage, where it is sorted and prepared for further processing.
Sorters: Sorting is a critical step to ensure the quality and purity of the recycled plastic. Specialized sorters are designed to separate different types of plastics based on their material properties. One common type is the optical sorter, which uses infrared sensors to identify and separate plastics by type. These sorters can process large volumes of shredded plastic rapidly, ensuring that only the desired plastic types are collected. Other sorter technologies include near-infrared (NIR) sorters, which provide more detailed analysis, and manual sorting systems, which are used for fine-tuning and quality control.
Washing Lines: After sorting, the plastic waste needs to be thoroughly cleaned to remove contaminants and impurities. Washing lines are essential for this process. These lines typically consist of a series of conveyors and tanks filled with water or cleaning solutions. The shredded plastic is fed onto the washing line, where it undergoes a thorough cleaning process. Water jets and brushes are used to remove dirt, labels, and other debris. Some washing lines also incorporate drying mechanisms to ensure the plastic is clean and dry before the next step. This process is crucial to produce high-quality recycled plastic that meets industry standards.
The size and capacity of a plastic recycling plant will depend on the specific equipment and processes employed. Larger plants may utilize multiple shredders and sorters to handle increased volumes of waste, while also incorporating advanced washing lines to maintain efficiency. The choice of machinery and their arrangement is a critical decision, as it directly impacts the plant's productivity and the overall quality of the recycled plastic.
Unraveling Australia's Plastic Cup Recycling Mystery: What You Need to Know
You may want to see also
Location: Plants are often located near waste sources for efficiency
The strategic placement of plastic recycling plants is a critical aspect of their design and operation, primarily driven by the need for efficiency and cost-effectiveness. These plants are often strategically located in close proximity to waste sources, such as urban areas, industrial zones, or regions with high plastic production. This proximity is a key factor in optimizing the entire recycling process.
By being near waste sources, recycling plants can significantly reduce transportation costs and time. Plastic waste, often bulky and heavy, becomes more manageable when the plant is nearby. This reduces the need for extensive hauling, which can be both costly and environmentally detrimental due to the associated emissions. Furthermore, the shorter distance minimizes the risk of waste degradation during transit, ensuring that the material remains suitable for processing.
Another advantage of locating recycling plants near waste sources is the potential for a more consistent and reliable supply of raw materials. This proximity allows for a steady feed of plastic waste into the plant, ensuring a continuous production process. In contrast, plants located far from waste sources might face challenges in maintaining a consistent supply, which could lead to production delays and inefficiencies.
Additionally, the location of recycling plants can have environmental benefits. By minimizing the distance between waste collection and processing, these plants can reduce the carbon footprint associated with transportation. This is particularly important in the context of sustainability, as the recycling industry aims to minimize its environmental impact.
In summary, the location of plastic recycling plants is a strategic decision that significantly influences their efficiency and sustainability. Placing these plants near waste sources optimizes transportation, ensures a reliable supply of raw materials, and reduces the environmental impact of the recycling process. This approach contributes to a more efficient and environmentally conscious recycling infrastructure.
Unraveling Dixie Plastic Spoon Recycling: A Comprehensive Guide
You may want to see also
Energy Use: Energy consumption varies based on plant size and technology
The energy requirements of a plastic recycling plant are a critical aspect of its operation, and they can vary significantly depending on several factors, including the plant's size and the technology employed. Larger plants, which typically process higher volumes of plastic waste, generally require more energy to power their operations. This increased energy demand is often met through the use of larger machinery and more extensive processing lines, which can be energy-intensive. For instance, a large-scale recycling facility might utilize advanced sorting systems, such as optical sorters and eddy current separators, to efficiently separate different types of plastics. These systems can consume substantial amounts of electricity, especially when processing large tonnages of waste.
On the other hand, smaller-scale recycling operations may have different energy consumption patterns. These plants often focus on specialized processes, such as manual sorting or small-batch recycling, which can be less energy-intensive. However, they might still require significant energy for tasks like melting and reforming plastics, especially if they use traditional, less efficient technologies. The energy use in these smaller plants is often more localized and may be powered by on-site generators or renewable energy sources, contributing to a more sustainable operation.
Technology plays a pivotal role in determining energy consumption. Modern recycling plants often invest in energy-efficient equipment and processes, such as advanced shredders, granulators, and washing lines. These technologies are designed to minimize energy waste and maximize output. For example, some plants employ closed-loop systems that recycle water and materials, reducing the need for external energy inputs. Additionally, the adoption of automation and computer-controlled systems can optimize energy usage by ensuring that processes run at peak efficiency, reducing unnecessary energy consumption.
The size and technology of a recycling plant also influence its overall environmental impact. Larger, more technologically advanced plants may have the advantage of economies of scale, allowing them to implement more sustainable practices. They can invest in energy-efficient infrastructure, such as solar panels or wind turbines, to power their operations, thereby reducing reliance on the grid and lowering carbon emissions. Smaller plants, while potentially more energy-efficient in certain aspects, might still face challenges in implementing large-scale renewable energy solutions due to limited space and resources.
In summary, the energy use in plastic recycling plants is a complex issue, influenced by plant size and technology. Larger plants often require more energy for their operations but can also implement more sustainable practices. Smaller plants may have different energy consumption patterns, focusing on specialized processes and potentially utilizing renewable energy sources. The choice of technology is crucial, as modern, energy-efficient equipment can significantly reduce energy consumption and environmental impact, making it a key consideration for plant operators and policymakers alike.
Bic Plastic Recycling: Unraveling the Mystery of Its Sustainability
You may want to see also
Frequently asked questions
The size of a plastic recycling plant can vary significantly depending on its scale and the scope of its operations. Small-scale facilities might process a few hundred tons of plastic waste annually, while larger, more industrial plants can handle several thousand tons or even tens of thousands of tons per year. The plant's size often correlates with the volume of waste it can process, the types of plastics it can handle, and the efficiency of its recycling processes.
The space needed for a plastic recycling plant is another critical factor. A small-scale operation might occupy a few thousand square feet, while a larger plant could span several acres. The layout and design of the facility play a crucial role in determining the required space. For instance, a plant with a single processing line will need less area compared to a facility with multiple lines, sorting areas, storage spaces, and administrative offices.
Yes, modern plastic recycling technologies have made it possible to design modular or portable recycling plants. These plants are often designed with a focus on flexibility and adaptability, allowing them to be set up in various locations and scaled up or down as needed. Modular plants can be composed of pre-fabricated units that can be easily connected and disconnected, making them suitable for different recycling projects and sites. Portability is especially beneficial for mobile recycling operations or those in remote areas.