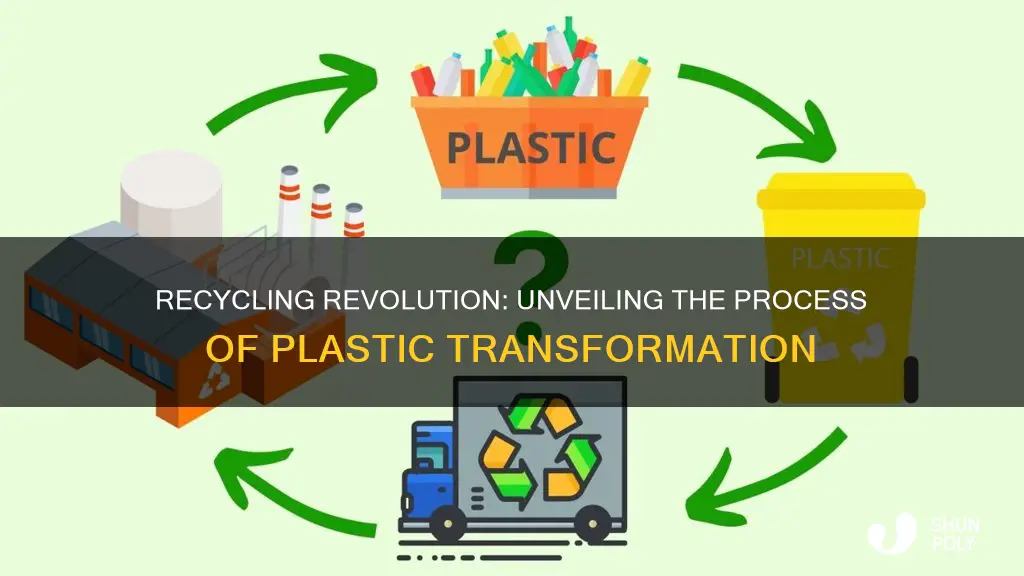
Plastics recycling is a complex process that varies depending on the type of plastic. Different types of plastics, such as PET (polyethylene terephthalate), HDPE (high-density polyethylene), and PVC (polyvinyl chloride), require distinct recycling methods. PET, commonly used in beverage bottles, can be recycled into fibers for clothing or new bottles. HDPE, found in milk jugs and some containers, is often downcycled into items like park benches or outdoor furniture. PVC, used in construction and pipes, poses challenges due to its high heat sensitivity and is typically not recyclable through standard processes. Understanding these variations is crucial for effective recycling practices and promoting a more sustainable approach to plastic waste management.
What You'll Learn
- Collection and Sorting: Separate plastics by type for efficient recycling
- Cleaning: Remove contaminants like food residue to ensure quality
- Shredding/Granulating: Break down plastics into small pieces or pellets
- Melting and Molding: Reheat and reshape plastic for new products
- Downcycling: Transform plastic into lower-quality items, reducing material value
Collection and Sorting: Separate plastics by type for efficient recycling
The first crucial step in the recycling process of plastics is the collection and sorting of these materials. This initial phase is essential as it sets the foundation for the entire recycling journey, ensuring that the end products are of high quality and meet the necessary standards. The process begins with the collection of plastic waste from various sources, including households, commercial establishments, and industrial facilities. This waste is then sorted, a critical step that requires precision and attention to detail.
Sorting plastics by type is a meticulous process that involves identifying and separating different types of plastic polymers. Common types of plastics include PET (polyethylene terephthalate), HDPE (high-density polyethylene), PVC (polyvinyl chloride), LDPE (low-density polyethylene), and PP (polypropylene). Each type of plastic has unique properties and is used in different applications, such as beverage bottles, milk jugs, pipes, shopping bags, and food containers. Proper identification is key to ensuring that these plastics are recycled correctly and efficiently.
During the sorting process, various methods can be employed to ensure accuracy. One common technique is visual inspection, where trained personnel examine the plastic items and separate them based on their color, shape, and suspected polymer type. This method is particularly useful for identifying common plastic types like PET and HDPE, which are easily recognizable due to their distinct colors and shapes. For more complex identification, advanced technologies such as near-infrared (NIR) spectroscopy can be utilized. NIR spectroscopy is a non-destructive testing method that uses light to identify the chemical composition of materials, allowing for the accurate sorting of plastics even when they are contaminated or mixed.
Another critical aspect of sorting is the separation of plastics by their resin identification codes, which are typically found on the bottom of plastic containers. These codes, ranging from 1 to 7, indicate the type of plastic used in the product. For instance, PET bottles are labeled with the number 1, while HDPE milk jugs are labeled with the number 2. Sorting by these codes ensures that plastics are directed to the appropriate recycling streams, optimizing the recycling process and reducing contamination.
Efficient collection and sorting of plastics by type are fundamental to the success of recycling efforts. This step ensures that the subsequent processes, such as cleaning, processing, and manufacturing new products, can be carried out effectively. By separating plastics at the source and during collection, recycling facilities can streamline their operations, reduce costs, and improve the overall quality of recycled materials. This attention to detail in the initial stages of recycling significantly contributes to the development of a sustainable and efficient plastic recycling system.
Unveiling the Safety of Recycled Plastic Toys: A Comprehensive Guide
You may want to see also
Cleaning: Remove contaminants like food residue to ensure quality
The process of recycling plastics begins with proper cleaning and preparation of the materials to ensure the highest quality of the final product. Cleaning is a crucial step as it involves removing any contaminants that may be present, such as food residue, labels, or other debris. This step is essential to maintain the integrity of the recycled plastic and to meet the standards required for its reuse.
When cleaning plastic waste, the first step is to sort the materials based on their type and color. Different types of plastics have varying recycling methods and compatibility, so proper sorting is essential. For instance, common household plastics like PET (polyethylene terephthalate) and HDPE (high-density polyethylene) are often separated from other plastics to ensure they can be processed effectively. This initial sorting process can be done manually or with the help of specialized equipment.
After sorting, the plastic waste undergoes a cleaning process to eliminate any food or liquid stains. This is typically done using a combination of mechanical and chemical methods. Mechanical cleaning involves physical processes such as washing, shredding, or grinding the plastic to remove visible contaminants. For example, a shredder can break down large plastic items into smaller pieces, making it easier to remove any embedded food particles. This step is crucial as it prevents the contamination of the recycled material, ensuring that the final product is of high quality and safe for further use.
Chemical cleaning is another important technique used to remove contaminants. This process utilizes specific solvents or detergents to dissolve and remove any remaining food residue or labels. For instance, a common method is to soak the plastic in a chemical solution, which helps to break down and wash away the contaminants. It is essential to follow proper safety protocols during this step to handle the chemicals correctly and ensure a safe working environment.
Once the cleaning process is complete, the plastic waste is ready for the next stage of recycling. The cleaned and sorted materials are then sent to specialized facilities where they are processed further. This may involve additional cleaning steps, melting, and reforming the plastic into new products. Proper cleaning ensures that the recycled plastic meets the required quality standards, making it suitable for various applications, from manufacturing new containers to creating durable construction materials.
CT's Plastic Recycling: Unveiling the Truth Behind the Process
You may want to see also
Shredding/Granulating: Break down plastics into small pieces or pellets
The process of shredding and granulating is a crucial step in the recycling of plastics, as it involves breaking down plastic materials into smaller, more manageable pieces. This method is particularly useful for various plastic types, including those that are challenging to process due to their size or shape. The primary goal is to reduce the size of the plastic waste, making it easier to handle and transport, while also preparing it for further recycling processes.
Shredding is the initial step, where large plastic items or sheets are fed into a shredding machine. These machines use sharp blades or rotating knives to cut and tear the plastic into smaller fragments. The shredded plastic can vary in size, from coarse pieces to fine, paper-like strips, depending on the desired outcome and the type of shredder used. This process helps to eliminate any large, bulky items that might hinder the recycling process and ensures that the plastic is reduced to a more uniform size.
After shredding, the plastic fragments are then fed into a granulator. Granulating is the process of further reducing the shredded plastic to create small, uniform pellets or granules. These machines typically use a combination of cutting and heating elements to melt and shape the plastic. The heated blades cut the plastic into even smaller pieces, resulting in a consistent and controlled size. This step is essential to produce a high-quality recycled plastic material that can be used in various applications.
The granulating process offers several advantages. Firstly, it allows for the creation of a standardized plastic product, which is crucial for manufacturing and ensuring consistency in the final recycled material. Secondly, the small size of the granules makes it easier to handle and store, facilitating the transportation and distribution of the recycled plastic. Additionally, granulating can help remove any contaminants or impurities present in the shredded plastic, improving the overall quality of the recycled product.
In summary, shredding and granulating are essential techniques in the recycling of plastics, enabling the breakdown of various plastic materials into smaller, more manageable pieces. These processes ensure that plastics can be effectively sorted, cleaned, and processed for reuse, contributing to a more sustainable approach to waste management and the conservation of resources.
Tariffs on Plastic Recycling: A Complex Global Issue
You may want to see also
Melting and Molding: Reheat and reshape plastic for new products
The process of recycling plastic through melting and molding is a crucial step in transforming used plastic materials into new products, offering a sustainable alternative to traditional manufacturing methods. This technique involves heating the plastic to a specific temperature, allowing it to become malleable, and then shaping it into new forms. The process begins with the collection and sorting of various plastic types, ensuring that only compatible materials are combined to maintain the integrity of the final product. This initial step is vital as it sets the foundation for the entire recycling journey.
Once sorted, the plastic is prepared for melting. This is typically done using specialized equipment like extruders or injection molding machines. The plastic is heated to its melting point, which varies depending on the type of plastic. For instance, high-density polyethylene (HDPE) melts at around 230°C, while polyvinyl chloride (PVC) requires a higher temperature of approximately 260°C. This precise temperature control is essential to ensure the plastic's quality and structural integrity. After melting, the plastic is often cooled and granulated to create uniform pellets, which can then be used as raw material for manufacturing.
The molding process is where the magic happens, turning the molten plastic into desired shapes. This stage involves injecting the heated plastic into a mold, which gives it the intended form. The mold can be of various designs, from simple to complex, depending on the product's requirements. Once the plastic is injected, it solidifies, and the mold is opened to reveal the newly formed product. This method is highly versatile, enabling the creation of a wide range of items, from packaging materials to automotive parts.
One of the advantages of this recycling technique is its ability to preserve the original properties of the plastic. By carefully controlling the temperature and cooling process, the recycled plastic can retain its strength, flexibility, and durability, making it suitable for various applications. Moreover, this method allows for the customization of products, as the molding process can be tailored to meet specific design and functionality needs.
In summary, the melting and molding process is a sophisticated and efficient way to recycle plastic, offering a second life to used materials. It showcases the potential for sustainable practices in the manufacturing industry, reducing waste and promoting a circular economy. With further advancements in technology and a continued focus on proper waste management, this recycling method can significantly contribute to a greener and more environmentally conscious future.
Self-Seal Envelopes: Can Plastic Strips Be Recycled?
You may want to see also
Downcycling: Transform plastic into lower-quality items, reducing material value
Downcycling is a process that involves transforming plastic waste into new materials, but with a significant trade-off: the resulting products are of lower quality and value compared to the original plastic. This method is often used as a way to give new life to plastic waste, especially when the plastic cannot be recycled through traditional methods. The process typically begins with the collection and sorting of plastic waste, ensuring that it is free from contaminants and sorted by type (e.g., PET, HDPE, PVC). This initial step is crucial as it determines the success and quality of the downcycled product.
Once sorted, the plastic can be processed in various ways. One common method is shredding or granulating the plastic into smaller pieces. These pieces are then cleaned to remove any remaining impurities. The cleaned plastic fragments are then melted and extruded into new forms. This process is often used to create new plastic products, such as:
- New Plastic Pellets: These are essentially recycled plastic flakes that can be used as raw materials for manufacturing new products. They are a lower-cost alternative to virgin plastic pellets, making them suitable for applications where the final product's quality is less critical.
- Rugs and Carpets: Plastic waste, particularly PET bottles, can be transformed into soft, colorful fibers. These fibers are then woven or tufted to create rugs and carpets, providing a unique and eco-friendly flooring option.
- Construction Materials: Downcycled plastic can be used to create new construction materials. For example, plastic waste can be mixed with aggregate and other additives to form new types of concrete, reducing the need for virgin materials.
The key advantage of downcycling is its ability to extend the life of plastic materials, preventing them from ending up in landfills or being incinerated. However, it's important to note that downcycled products generally have a shorter lifespan and may not be as durable as their original counterparts. This is because the process often involves breaking down the plastic, which can lead to a loss of molecular integrity. As a result, downcycled materials might not be suitable for applications requiring high strength or durability.
Despite the limitations, downcycling plays a vital role in the circular economy, especially for materials that are difficult to recycle through conventional means. It encourages the reuse of resources, reduces waste, and can provide economic opportunities for those involved in the collection, processing, and sale of downcycled products. However, it is essential to manage expectations and educate consumers about the differences in quality to ensure that downcycled products are used appropriately and do not compromise on performance when compared to their original, higher-quality counterparts.
Randall's Recycling: Unveiling the Plastic Waste Mystery
You may want to see also
Frequently asked questions
Plastic is a versatile material with numerous types, each identified by a unique number inside a recycling symbol. Common types include PET (polyethylene terephthalate, found in water bottles), HDPE (high-density polyethylene, used in milk jugs and some shampoo bottles), PVC (polyvinyl chloride, used in pipes and some food packaging), LDPE (low-density polyethylene, found in grocery bags), PP (polypropylene, used in food containers and bottle caps), and PS (polystyrene, known for its use in disposable cups and containers).
Recycling plastic involves several steps. First, used plastic items are collected and sorted by type. This sorting is crucial as different plastics have varying recycling methods. Then, the sorted plastics are cleaned and shredded into small pieces called flakes. These flakes are melted and reformed into pellets, which can be used to create new products. The process may involve additional steps like re-pelletizing and re-processing to ensure the recycled material meets quality standards.
Not all plastics are easily recyclable. For instance, PVC and PS (polystyrene) are often challenging to recycle due to their chemical composition and the energy-intensive processes required. Additionally, single-use plastics like shopping bags and straws made from LDPE can be recycled, but their thin nature can cause issues in recycling machines. Proper sorting and cleaning of plastics are essential to ensure they can be effectively recycled, and some recycling facilities may not accept all types of plastic due to technical limitations.