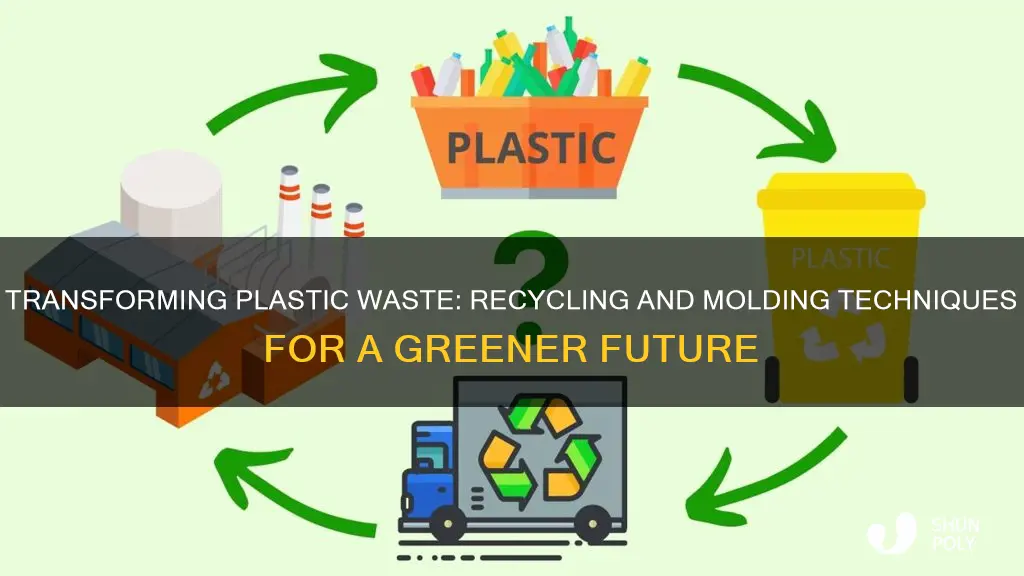
Recycling and molding plastic is an essential process in the circular economy, allowing us to transform waste plastic into new products and reduce environmental impact. It involves collecting, sorting, and processing plastic materials to create a raw material that can be used in manufacturing. The process typically begins with the collection of plastic waste, which is then sorted by type and color to ensure the highest quality of the recycled material. After sorting, the plastic is cleaned, shredded, or ground into small pieces called flakes. These flakes are then melted and molded into new shapes, creating a wide range of products, from packaging materials to automotive parts. This process not only reduces the demand for virgin plastic but also minimizes the amount of plastic waste sent to landfills or incinerators, contributing to a more sustainable and environmentally friendly approach to plastic production and consumption.
What You'll Learn
- Sorting: Separate plastics by type and color for efficient recycling
- Cleaning: Rinse and dry plastic items to remove contaminants
- Shredding: Break down plastic into small pieces for easier processing
- Melting: Heat plastic to a molten state for molding
- Molding Techniques: Use methods like injection molding or blow molding
Sorting: Separate plastics by type and color for efficient recycling
The process of recycling plastic begins with proper sorting, which is a crucial step to ensure efficient and effective recycling. Plastic recycling requires a meticulous approach to separate different types of plastics, as not all plastics are recyclable in the same way. This initial sorting process is essential to streamline the recycling stream and maximize the potential for successful recycling.
When sorting plastics, it is imperative to categorize them by their type. Common types of plastic include PET (polyethylene terephthalate), HDPE (high-density polyethylene), PVC (polyvinyl chloride), LDPE (low-density polyethylene), and PP (polypropylene). Each type of plastic has unique properties and recycling requirements. For instance, PET is widely used in beverage bottles and is generally easy to recycle, while HDPE is commonly found in milk jugs and shampoo bottles. Understanding these distinctions is key to proper sorting.
Color is another important factor in the sorting process. Plastic items often come in various colors, and this visual distinction can help in further categorizing them. For example, clear PET bottles are easily identifiable and can be grouped separately from colored PET bottles. Similarly, HDPE containers, which are typically white or translucent, can be sorted from other colored HDPE items. This color-based sorting aids in creating a more organized recycling stream.
To facilitate efficient sorting, recycling centers often provide guidelines or color-coded systems to help individuals and businesses separate plastics. These systems make it easier to identify and group plastics by type and color. For instance, a recycling center might use a red bin for PET, a blue bin for HDPE, and so on. Adhering to these guidelines ensures that the sorted plastics are more likely to be accepted by recycling facilities.
By diligently sorting plastics by type and color, you contribute to a more streamlined recycling process. This practice reduces the likelihood of contamination, where different types of plastics are mixed, which can lead to recycling inefficiencies. Proper sorting also helps in maintaining the quality of the recycled material, ensuring that it can be effectively molded into new products. In summary, sorting plastics is a fundamental step in recycling, enabling a more sustainable approach to managing plastic waste.
Unraveling the Mystery: Can Plastic Ice Cream Tubs Be Recycled?
You may want to see also
Cleaning: Rinse and dry plastic items to remove contaminants
Cleaning plastic items before recycling is an essential step to ensure the process is effective and the final product is of good quality. Here's a detailed guide on how to properly clean and prepare plastic items for recycling:
Rinsing Process: Begin by thoroughly rinsing the plastic items under running water. This initial step helps to remove loose dirt, food particles, and other contaminants that may be present on the surface. Use a gentle stream of water to avoid damaging the plastic. For heavily soiled items, multiple rinses might be necessary. It's important to scrub the plastic gently to avoid scratching or damaging the surface. You can use a soft-bristled brush or a sponge to help with this process, ensuring that no residue is left behind.
After rinsing, it is crucial to inspect the plastic items for any remaining contaminants. Check for food residue, especially in crevices or around labels, as these areas can be difficult to clean. If you notice any stubborn stains or residue, consider using a mild detergent or dish soap diluted in warm water. Apply the soapy solution to the affected areas and gently scrub again. Rinse thoroughly afterward to eliminate any soap residue.
Drying Technique: Once the rinsing and cleaning are complete, proper drying is essential to prevent water spots and ensure the plastic is ready for recycling. Start by gently patting the plastic items dry with a clean towel. Avoid rubbing vigorously, as this can create small scratches on the surface. For a more thorough drying process, use a hairdryer on a low setting. Hold the hairdryer a few inches away from the plastic to avoid overheating and potential damage. Focus the airflow on the entire surface, ensuring that all areas are dry.
In some cases, you might come across plastic items with complex shapes or those that are difficult to dry completely, such as containers with multiple compartments. For such items, consider using a soft cloth or paper towel to absorb excess moisture. Gently press the cloth against the plastic to remove water, being careful not to apply too much pressure that could distort the shape.
By following these cleaning procedures, you ensure that the plastic items are free from contaminants, which is crucial for the recycling process. Proper cleaning helps maintain the integrity of the recycling stream, reduces the risk of contamination, and ultimately contributes to the production of high-quality recycled plastic materials.
Unleash the Power of Paint Trays: Can They Be Recycled?
You may want to see also
Shredding: Break down plastic into small pieces for easier processing
Shredding is a crucial step in the recycling process of plastic, as it involves breaking down larger plastic items into smaller, more manageable pieces. This process is essential for several reasons. Firstly, it increases the surface area of the plastic, exposing more material to the recycling machinery and making it easier to process. Smaller pieces also reduce the risk of contamination, as they are less likely to interfere with the sorting and processing equipment.
The shredding process typically begins with the collection of plastic waste, which is then sorted by type and color to ensure efficient recycling. Once sorted, the plastic is fed into a shredding machine, which can vary in design depending on the specific requirements and the type of plastic being processed. Some shredders use rotating blades to cut the plastic into thin strips, while others employ a combination of cutting and tearing to produce a consistent, uniform shred.
Modern shredding technology has advanced significantly, allowing for more efficient and precise shredding. For example, some machines use a combination of knives and rollers to create a fine, consistent shred, which is ideal for recycling into new products. The shredded plastic is then conveyed to the next stage of the recycling process, where it is further processed to remove any remaining contaminants and prepare it for molding or other forms of reuse.
It is important to note that the shredding process should be tailored to the specific type of plastic being recycled. Different plastics have varying properties and melting points, so the shredding technique must be adjusted accordingly. For instance, high-density polyethylene (HDPE) and polypropylene (PP) require different shredding methods compared to low-density polyethylene (LDPE) or polyvinyl chloride (PVC). Proper shredding ensures that the recycled plastic meets the necessary quality standards for its intended use.
In summary, shredding is a vital step in the recycling and molding of plastic, as it prepares the material for further processing and ensures a higher quality end product. By breaking down plastic into small, uniform pieces, shredding increases efficiency, reduces contamination risks, and allows for the creation of new products from recycled materials. This process is a key component in the circular economy, promoting sustainability and reducing the environmental impact of plastic waste.
Recycling Plastic Storage Containers in NYC: What You Need to Know
You may want to see also
Melting: Heat plastic to a molten state for molding
Melting plastic is a crucial step in the recycling and molding process, allowing for the transformation of waste plastic into new, usable forms. This process involves heating the plastic to a specific temperature, known as its melting point, which varies depending on the type of plastic. The goal is to reach a molten state where the plastic becomes malleable and can be shaped or molded into desired products.
To begin the melting process, you'll need a specialized machine called an extruder or a plastic melting machine. These machines are designed to handle the high temperatures required for melting plastic. The plastic waste, which can be in the form of flakes, pellets, or even solid blocks, is fed into the machine. It is important to ensure that the plastic is clean and free from contaminants to maintain the quality of the final product.
The extruder or melting machine operates by applying heat and pressure to the plastic. The temperature is carefully controlled to match the specific melting point of the plastic type being processed. For example, common types of plastic like PET (polyethylene terephthalate) and HDPE (high-density polyethylene) have different melting temperatures. Accurate temperature control is essential to avoid overheating or underheating, both of which can lead to quality issues.
As the plastic reaches its melting point, it undergoes a phase change from a solid to a liquid state. This molten plastic is now ready for molding. The process involves shaping the plastic into the desired form using a mold. The mold is designed with the specific shape and dimensions of the intended product. Once the plastic is melted and in the mold, it is typically cooled to solidify and retain its shape.
Melting and molding plastic require precision and attention to detail. The temperature and duration of the melting process must be carefully managed to ensure the plastic's chemical structure remains intact. This step is fundamental in recycling and manufacturing processes, enabling the creation of new products from waste plastic, thus contributing to a more sustainable and circular economy.
Unraveling the Mystery: Can Cereal Box Liners Be Recycled?
You may want to see also
Molding Techniques: Use methods like injection molding or blow molding
When it comes to recycling and molding plastic, there are several techniques that can be employed to create various products. One of the most common and efficient methods is injection molding. This process involves injecting molten plastic into a mold, which is then shaped and cooled to form the desired object. Injection molding is highly versatile and can produce intricate and complex shapes, making it ideal for manufacturing a wide range of plastic items. The process begins with the selection of a suitable plastic material, which is then heated and softened in an extruder. The molten plastic is then injected into the mold at high pressure, filling it and taking the shape of the mold cavity. Once in the mold, the plastic is cooled and solidified, and the finished product is ejected. This method is widely used in industries such as automotive, electronics, and consumer goods due to its ability to produce high-quality, consistent parts.
Another popular molding technique is blow molding, which is commonly used for creating hollow objects like bottles and containers. This process involves two main stages: the parison stage and the blow molding stage. During the parison stage, a hollow tube of molten plastic, known as a parison, is created and inflated to the desired shape. This is done by injecting the plastic into a mold and then stretching it to form the hollow structure. In the blow molding stage, the parison is transferred to a second mold, where it is further inflated and shaped. This method is particularly useful for producing lightweight and cost-effective hollow products. Blow molding offers excellent dimensional accuracy and is often chosen for its ability to create seamless, smooth surfaces.
Both injection molding and blow molding require precise control over temperature, pressure, and timing to ensure the quality and integrity of the final product. Modern molding machines are equipped with advanced controls and sensors to monitor and adjust these parameters automatically. The choice between these two techniques depends on the specific requirements of the project, including the desired shape, size, and complexity of the plastic item. Injection molding excels in producing solid, intricate parts, while blow molding is ideal for creating hollow objects with consistent wall thickness.
In addition to these molding methods, it is essential to consider the recycling process as well. Proper recycling ensures that the plastic can be reused effectively, reducing waste and promoting sustainability. Recycling plastic involves sorting and processing the material to remove contaminants, then reprocessing it into new products. This can be achieved through various recycling techniques, such as mechanical recycling, where the plastic is shredded, washed, and melted to create new products, or chemical recycling, which breaks down the plastic into its original monomers for reuse.
By combining molding techniques with efficient recycling practices, it is possible to create a sustainable and circular economy for plastic products, minimizing environmental impact and maximizing resource efficiency. These processes are constantly evolving, with ongoing research and development aimed at improving the efficiency, sustainability, and versatility of plastic molding and recycling.
Clear Plastic Solo Cups: Unraveling the Recycling Mystery
You may want to see also
Frequently asked questions
Recycling plastic involves several steps to transform used plastic items into new products. It typically begins with the collection of plastic waste, which is then sorted based on the type of plastic (e.g., PET, HDPE, PVC). The sorted plastic is cleaned, shredded, or melted to create flakes or pellets. These raw materials can then be used to manufacture new products like bottles, containers, or even clothing.
At home, you can recycle plastic by following these steps: first, identify the type of plastic by checking the resin identification code (a number inside a triangle on the bottom of the item). Rinse the plastic to remove any food residue or dirt. Break down large items to fit into your local recycling bin. Ensure you follow your municipality's recycling guidelines for plastic types and collection schedules.
There are various molding techniques used in the plastic manufacturing industry. Injection molding is a common process where molten plastic is injected into a mold, which then cools and solidifies to form the desired shape. Blow molding is used for producing hollow objects, while compression molding is suitable for creating complex shapes with a high degree of precision. Other methods include vacuum molding and rotomolding, each with its own advantages for specific applications.
Yes, plastic can be molded into sustainable products, especially when using recycled plastic materials. Recycled plastic can be processed and molded into various forms, such as furniture, outdoor gear, construction materials, and even packaging. By utilizing recycled content, the demand for virgin plastic is reduced, leading to less environmental impact and a more circular economy. Additionally, some companies are developing biodegradable plastics derived from renewable sources, offering an eco-friendly alternative to traditional molding processes.