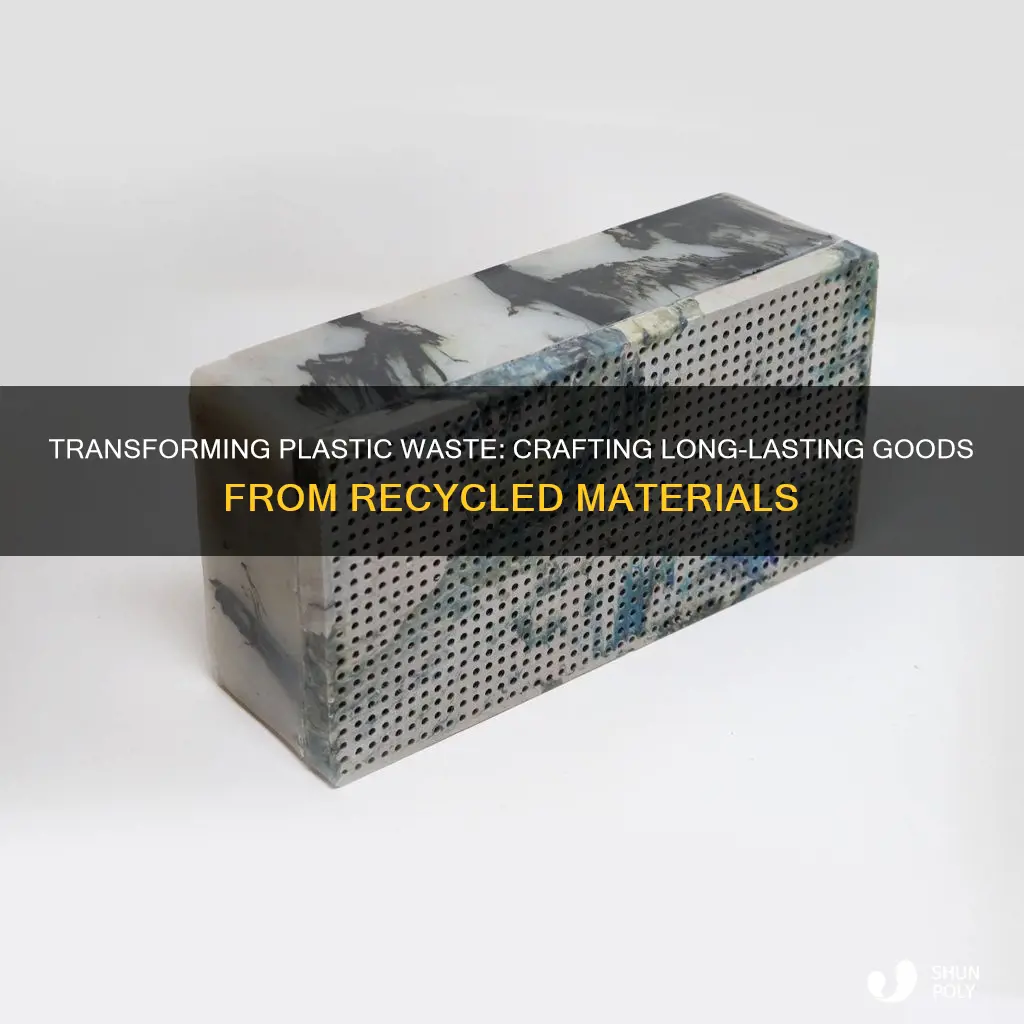
Recycling plastic into permanent, durable products is a crucial step towards a more sustainable future. It involves transforming waste plastic into high-quality materials that can be used to create long-lasting goods, reducing the need for new raw materials and minimizing environmental impact. This process begins with collecting and sorting plastic waste, ensuring it is clean and free from contaminants. The sorted plastic is then shredded or granulated into small pieces, which are melted and molded into new shapes. Advanced recycling techniques, such as chemical recycling, can break down plastic into its original building blocks, allowing for the creation of new, high-quality products. By embracing these methods, we can turn plastic waste into valuable resources, contributing to a circular economy and a more sustainable world.
What You'll Learn
- Sorting and Collection: Separate plastic types, collect, and ensure clean, dry materials
- Cleaning and Shredding: Remove contaminants, shred plastic into small pieces for processing
- Melting and Molding: Heat and mold shredded plastic into new shapes and forms
- Reinforcement and Compounding: Add fillers and additives to enhance strength and durability
- Final Assembly and Finishing: Assemble parts, apply coatings, and complete product manufacturing
Sorting and Collection: Separate plastic types, collect, and ensure clean, dry materials
The first crucial step in the process of recycling plastic into permanent and durable products is proper sorting and collection. This initial phase is fundamental as it sets the foundation for the entire recycling journey, ensuring that the materials are suitable for the next stages of processing and manufacturing. Here's a detailed guide on how to approach this:
Sorting Plastic Types: Plastic recycling requires a meticulous sorting process to separate different types of plastics. This is because not all plastics are recyclable, and even within the recyclable category, some have specific requirements. The most common types of plastics include PET (polyethylene terephthalate), HDPE (high-density polyethylene), PVC (polyvinyl chloride), LDPE (low-density polyethylene), and PP (polypropylene). Each of these has unique properties and applications. For instance, PET is widely used in beverage bottles, while HDPE is commonly found in milk jugs and shampoo bottles. Understanding these distinctions is key. You can use color-coding or labeling systems to categorize plastics, making the sorting process more efficient. For example, clear PET bottles can be one color-coded group, while HDPE containers can be another, ensuring that they are directed to the appropriate recycling streams.
Collection and Cleaning: Once sorted, the plastic materials need to be collected and prepared for recycling. This involves ensuring that the plastics are clean, dry, and free from contaminants. Contaminants such as food residue, labels, or other non-plastic materials can compromise the quality of the recycled product. Start by removing any non-plastic components like caps, labels, and rings from the bottles. These can often be recycled separately. Rinse the plastic containers to eliminate any remaining liquids or food particles. It's important to use a gentle detergent and warm water for this process, ensuring that no chemicals remain on the plastic. After rinsing, allow the containers to air dry completely. Proper drying is essential to prevent moisture-related issues during the recycling process. For larger-scale operations, consider using industrial-grade washing machines designed for plastic recycling.
Organizing Collection Points: Establishing an efficient collection system is vital. Set up designated collection points in various locations, such as homes, offices, schools, and public spaces. These points should be easily accessible and clearly labeled as plastic recycling bins. Encourage people to sort their plastic waste at the source, making it more convenient for them to contribute. For residential areas, consider providing bags or containers specifically for plastic recycling, ensuring that residents know which plastics to include. In commercial settings, you might collaborate with businesses to set up collection systems, especially in industries that generate significant plastic waste.
Educating the Community: Educating the public about the importance of proper sorting and collection is an essential aspect of this process. Many people are unaware of the different types of plastics and their recycling requirements. Provide clear guidelines and resources to help them understand the recycling process. This can be done through community workshops, online tutorials, or even simple posters and flyers placed in public spaces. By raising awareness, you can ensure that more people actively participate in proper plastic waste management.
In summary, the sorting and collection process is a critical phase in recycling plastic into durable products. It requires attention to detail, proper education, and efficient systems to ensure that the materials are of high quality and suitable for the recycling stream. By implementing these practices, you contribute to a more sustainable approach to plastic waste management.
Unraveling the Recycling Mystery: Do Plastic Straws Get a Second Life?
You may want to see also
Cleaning and Shredding: Remove contaminants, shred plastic into small pieces for processing
The process of recycling plastic into permanent and durable products begins with meticulous cleaning and shredding, a crucial step to ensure the quality and longevity of the final product. This initial phase is all about removing any contaminants and preparing the plastic for further processing.
Cleaning: The first step in this process is to thoroughly clean the plastic waste. This involves removing any dirt, debris, or other foreign matter that might be present. Contaminants can include food residue, labels, or any other non-plastic materials. A common method for cleaning is washing the plastic with water and detergents, ensuring that all traces of impurities are eliminated. For more effective cleaning, some facilities use advanced techniques like flotation or air classification to separate contaminants from the plastic. It is essential to ensure that the cleaning process is thorough to prevent any unwanted substances from affecting the durability of the recycled product.
Shredding: Once the plastic is clean, the next step is shredding. Shredding is the process of breaking down the plastic into small, uniform pieces. This is typically done using specialized machinery designed for plastic recycling. The shredded plastic, often referred to as 'flakes' or 'granules', are then sorted by color and size. This sorting process is crucial as it allows for the creation of consistent and high-quality recycled materials. The shredded plastic can now be further processed into various forms, such as pellets or sheets, which can be used to manufacture new products.
The cleaning and shredding process is a critical phase in plastic recycling as it sets the foundation for the entire recycling journey. By removing contaminants and reducing the plastic to a manageable size, this step ensures that the recycled material is of high quality and can be used to create durable, long-lasting products. This process also significantly reduces the volume of plastic waste, making it more manageable and environmentally friendly.
Unraveling the Mystery: Can No. 6 Plastic Be Recycled?
You may want to see also
Melting and Molding: Heat and mold shredded plastic into new shapes and forms
The process of transforming shredded plastic into durable, permanent products involves a technique known as melting and molding. This method is a crucial step in recycling plastic and creating new, useful items. Here's a detailed guide on how to achieve this:
Melting Process: Begin by gathering your shredded plastic waste, which can include items like water bottles, food containers, or any other plastic debris. The first step is to melt the plastic, and this can be done using a specialized machine called a plastic extruder or a simple heat source like a hot plate or oven. The goal is to reach the plastic's melting point, which varies depending on the type of plastic. For example, common plastics like PET (polyethylene terephthalate) and HDPE (high-density polyethylene) have different melting temperatures. It's essential to heat the plastic evenly to ensure a consistent melt. Once melted, the plastic is in a viscous liquid state, ready for the next phase.
Molding and Shaping: After melting, the real transformation begins. You'll need to pour or inject the molten plastic into a mold, which is a crucial step in shaping the material. The mold can be made of metal or a durable plastic, and its design will determine the final shape of the product. When using a mold, the melted plastic is carefully poured in, and then the mold is closed, trapping the plastic inside. Heat and pressure are then applied to solidify the plastic around the mold's shape. This process is called 'molding' or 'injection molding' for more complex shapes. The duration of this step depends on the size and complexity of the product, but it typically takes a few minutes.
Once the plastic has cooled and hardened within the mold, it can be carefully removed, revealing the new product. This method allows for the creation of a wide range of items, from simple household objects to complex machinery parts. The key advantage of this process is the ability to produce durable, long-lasting goods that can be used for various applications.
Safety and Considerations: It's important to note that working with melted plastic requires proper safety gear and precautions. Gloves, heat-resistant aprons, and eye protection are essential to avoid burns and potential plastic fumes. Additionally, ensure you have adequate ventilation in the workspace to minimize inhaling any harmful particles.
This melting and molding technique is a fundamental part of the recycling process, enabling the transformation of waste plastic into valuable, reusable products, thus contributing to a more sustainable and circular economy.
Black Plastic DVD Cases: Can They Be Recycled?
You may want to see also
Reinforcement and Compounding: Add fillers and additives to enhance strength and durability
To enhance the strength and durability of recycled plastic products, reinforcement and compounding techniques are employed. These methods involve adding fillers and additives to the plastic material, which can significantly improve its mechanical properties. Here's a detailed explanation of this process:
Filler Addition: Fillers are non-plastic materials that are incorporated into the polymer matrix to reinforce the plastic. Common fillers include calcium carbonate, talc, clay, and wood flour. When added in controlled amounts, these fillers provide several benefits. Firstly, they increase the density and stiffness of the plastic, making it more rigid and less prone to deformation. This is particularly useful for applications requiring structural integrity, such as construction or automotive parts. For example, adding calcium carbonate fillers to polypropylene (PP) can create a composite material with improved impact resistance and dimensional stability.
The process of filler addition involves carefully selecting the filler material based on its compatibility with the plastic resin. Different fillers have varying effects on the material's properties. Some fillers, like calcium carbonate, are known for their ability to enhance impact resistance and reduce material cost. Others, such as carbon fiber or glass fiber, provide exceptional strength and stiffness but may increase the overall cost of the product. The filler content and type are determined by the desired performance characteristics of the final product.
Additive Effects: Additives play a crucial role in modifying the behavior and properties of recycled plastics. These can be categorized into several types, each serving a specific purpose. One common type is processing aids, which include plasticizers, lubricants, and antioxidants. Plasticizers, such as phthalates, are added to increase flexibility and ease of processing, making the plastic more pliable. Lubricants reduce friction during processing, improving the flow characteristics of the material. Antioxidants, as the name suggests, prevent oxidation and degradation of the plastic, ensuring its longevity.
Another important class of additives is stabilizers, which are essential for maintaining the stability and color of the plastic over time. UV stabilizers, for instance, protect the material from degradation caused by sunlight, making it suitable for outdoor applications. Additionally, flame retardants are added to enhance fire safety, especially in electrical or furniture applications. These additives are carefully chosen and combined to achieve the desired performance and functionality of the recycled plastic product.
By incorporating fillers and additives, the mechanical properties of recycled plastic can be significantly improved. This includes increased tensile strength, impact resistance, and dimensional stability. These enhanced properties make the material more suitable for a wide range of applications, from consumer goods to industrial components. The process of reinforcement and compounding allows for the creation of durable and long-lasting products from recycled plastic, contributing to a more sustainable and circular economy.
Unraveling the Mystery: Can All Plastic Numbers Be Recycled?
You may want to see also
Final Assembly and Finishing: Assemble parts, apply coatings, and complete product manufacturing
The final assembly and finishing process is a crucial stage in transforming recycled plastic into high-quality, durable products. This phase involves meticulous craftsmanship and attention to detail to ensure the end product meets the desired standards. Here's an overview of the steps involved:
Assembly: Begin by carefully laying out all the components, ensuring they are organized and easily accessible. This step is particularly important when dealing with complex products. Each part should be inspected for any defects or damage, and any necessary adjustments or modifications should be made. For instance, if you're manufacturing a water bottle, you might need to assemble a base, a middle section, and a cap. Precision is key here; every component must fit together seamlessly to guarantee the product's functionality and longevity.
Welding and Bonding: Depending on the design, welding or bonding techniques may be employed to join the plastic parts. For example, in the case of a plastic container, you might use ultrasonic welding to fuse the base and sides, ensuring a strong and permanent bond. This process requires specialized equipment and skilled operators to ensure the integrity of the product.
Coating and Finishing: After assembly, the product often undergoes a coating process to enhance its durability and appearance. This could involve applying a protective layer to prevent scratches or impact damage. For instance, a clear, UV-resistant coating can be applied to outdoor furniture made from recycled plastic to ensure its longevity. Additionally, finishing techniques such as polishing or texturing can be used to create a desired aesthetic and improve the product's overall appeal.
Quality Control: Throughout the final assembly and finishing process, rigorous quality control checks are essential. Each product should be inspected for any defects, ensuring it meets the required standards. This includes checking for proper alignment, smooth surfaces, and consistent color. Any deviations from the desired outcome should be addressed promptly to maintain high-quality standards.
Packaging and Distribution: Once the final product is assembled, coated, and inspected, it is ready for packaging. Proper packaging ensures the product remains protected during transportation and storage. Finally, the finished product is distributed to retailers or directly to consumers, making it accessible to those who appreciate sustainable and durable goods. This stage completes the journey from recycled plastic to a high-quality, ready-to-use item.
Can Plastic Bubble Wrap Be Recycled? Unraveling the Mystery
You may want to see also
Frequently asked questions
The initial phase involves collecting and sorting plastic waste. This process ensures that different types of plastics are separated, as not all plastics are suitable for the same recycling methods. Common types include PET (polyethylene terephthalate) and HDPE (high-density polyethylene), which are widely recycled.
To achieve durable products, the recycling process should involve advanced techniques. One such method is 'chemical recycling' or 'feedstock recycling', where plastic waste is broken down into its base chemicals, which can then be repurposed into new materials. This process often results in a higher-quality, more consistent product. Additionally, using a closed-loop recycling system, where the recycled material is continuously reused, can enhance the durability of the final product.
Absolutely! Recycled plastic can be transformed into a wide range of items, including furniture, construction materials, automotive parts, and even clothing. For instance, rPET (recycled PET) is commonly used to create new bottles, but it can also be processed into fibers for textiles, offering a more sustainable alternative to traditional fabrics. Another innovative application is in 3D printing, where recycled plastic pellets are used to create custom, durable parts with various shapes and sizes.