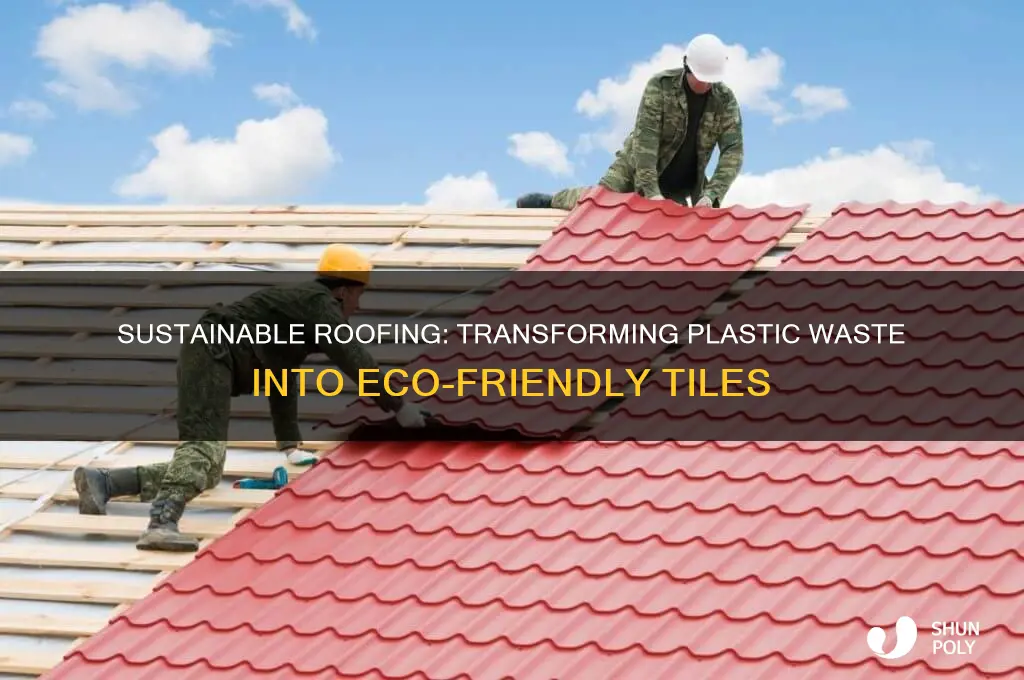
Roofing with eco-friendly materials is becoming increasingly popular, and one innovative approach is creating roof tiles from recycled plastic. This sustainable method not only reduces waste but also offers a durable and lightweight alternative to traditional roofing materials. By transforming plastic waste into roof tiles, we can significantly contribute to environmental conservation while ensuring long-lasting protection for buildings. This guide will explore the process of making roof tiles from recycled plastic, highlighting the benefits and providing a step-by-step approach to this eco-conscious roofing solution.
What You'll Learn
- Collection and Sorting: Gather and sort plastic waste for roofing tile production
- Milling and Grinding: Process plastic into fine particles for roofing tile manufacturing
- Mixing and Molding: Combine ground plastic with additives, then mold into tile shapes
- Drying and Curing: Allow molded tiles to dry and cure for strength
- Finishing and Installation: Treat tiles for durability and install on roofs
Collection and Sorting: Gather and sort plastic waste for roofing tile production
The first step in creating roof tiles from recycled plastic is to establish an efficient collection and sorting system. This process is crucial as it forms the foundation for the entire production process and ensures the quality of the final product. Here's a detailed guide on how to approach this stage:
Collection of Plastic Waste: Begin by identifying potential sources of plastic waste. This can include recycling centers, waste management facilities, or even direct collection from local communities. Set up collection points or bins in these areas, clearly labeled for plastic waste. Encourage the separation of different types of plastics to facilitate the sorting process later. It is essential to have a consistent and organized collection system to ensure a steady supply of raw materials.
Sorting Process: Once the plastic waste is collected, the sorting begins. This step requires a systematic approach to separate plastics into different categories. Here's a breakdown:
- Color Sorting: Start by sorting the plastics based on color. Roof tiles often have specific color requirements, so organizing the waste by color will make the subsequent processes more efficient.
- Type of Plastic: Identify and separate the different types of plastics. Common types used in roofing include polypropylene (PP), high-density polyethylene (HDPE), and polyvinyl chloride (PVC). Each type has unique properties, and proper sorting ensures the right plastic is used for the intended tile application.
- Size and Shape: Further sort the plastics by size and shape. This step is crucial as it helps in removing contaminants and ensures that the plastic flakes or pellets are of a consistent size, which is essential for uniform tile production.
Manual vs. Automated Sorting: Depending on the scale of your operation, you can choose between manual and automated sorting methods. For smaller-scale projects, manual sorting with trained staff can be effective. This method involves visual inspection and separation by hand. For larger operations, consider investing in automated sorting systems that use infrared or near-infrared technology to identify and separate different types of plastics based on their molecular structure.
Quality Control: As you sort, maintain a high level of quality control. This includes removing any non-plastic contaminants like metal, glass, or paper. Also, ensure that the sorted plastics are clean and free from any debris. This step is critical to the success of the roofing tile production, as contaminants can affect the durability and performance of the final product.
Efficient collection and sorting are key to a successful transition from plastic waste to roofing tiles, ensuring a steady supply of high-quality raw materials for the next stages of production.
Portland's Plastic Recycling: A Green Revolution or a Misstep?
You may want to see also
Milling and Grinding: Process plastic into fine particles for roofing tile manufacturing
The process of transforming recycled plastic into roofing tiles begins with a crucial step: milling and grinding. This step is essential as it reduces the plastic waste into a usable form for tile manufacturing. Here's a detailed breakdown of this process:
Milling: The initial stage involves feeding the collected plastic waste into a milling machine. This machine is designed to break down the plastic into smaller pieces, ensuring a consistent size and shape. The milling process can be done in two ways: dry milling and wet milling. Dry milling is more common and involves using a hammer mill to grind the plastic into a fine powder. This method is efficient and cost-effective. Alternatively, wet milling uses a combination of a hammer mill and a water bath to create a slurry, which is then further processed. The goal is to create a uniform particle size, typically in the range of 0.5 to 2 mm, ensuring that the plastic can be easily mixed with other materials during the tile-making process.
Grinding: After milling, the plastic particles are further refined through a grinding process. This step aims to achieve an even finer particle size, often in the range of 50 to 100 mesh (212 to 149 micrometers). Grinding can be accomplished using various methods, such as a ball mill or a vibratory grinder. The choice of grinding method depends on the desired particle size and the specific requirements of the roofing tile production process. The ground plastic will now have a consistent texture, making it suitable for mixing with other ingredients like clay, sand, and pigments to create the final roofing tile composition.
This milling and grinding process is a critical phase in the recycling and reuse of plastic for roofing applications. It ensures that the plastic waste is transformed into a valuable resource, contributing to sustainable construction practices and reducing the environmental impact of plastic production. By achieving a fine particle size, the plastic can be effectively combined with other materials, creating durable and eco-friendly roofing tiles.
Rothy's Recycled Revolution: Unveiling the Eco-Friendly Footwear
You may want to see also
Mixing and Molding: Combine ground plastic with additives, then mold into tile shapes
The process of creating roof tiles from recycled plastic begins with a careful selection of materials and a precise mixing and molding technique. Once you have gathered and ground the plastic waste, it's time to transform it into durable and aesthetically pleasing roof tiles.
In a well-equipped laboratory or production facility, you'll need to weigh and mix the ground plastic with specific additives. These additives play a crucial role in enhancing the material's properties. For instance, you might add a plasticizer to improve flexibility, a stabilizer to increase durability, and a colorant for a desired aesthetic appeal. The ratio of plastic to additives should be carefully calculated to ensure the final product meets the required standards. This step requires precision and an understanding of the material's behavior to achieve the optimal composition.
After the mixture is prepared, it's time to mold the plastic into tile shapes. This process involves using a molding machine or a manual technique, depending on the scale of production. The plastic is fed into the mold, which is designed to create the specific shape and size of the roof tile. The mold is typically made of a durable material that can withstand the pressure and heat of the molding process. As the plastic is injected or poured into the mold, it takes the form of the tile, including any desired textures or patterns. This step requires skill and attention to detail to ensure the tiles are uniform in quality.
The molding process can be further optimized by controlling temperature and pressure. Higher temperatures can make the plastic more pliable, allowing for easier shaping, while lower temperatures can provide better control over the final form. Pressure is also critical; too much pressure can lead to warping or distortion, while insufficient pressure may result in weak tiles. Finding the right balance is essential for producing high-quality roof tiles.
Once the molding is complete, the tiles are carefully removed from the molds and allowed to cool. This step ensures that the tiles retain their shape and strength. After cooling, the tiles can be inspected for any defects and further processed if needed. The final product is a sustainable and eco-friendly roof tile, ready to be installed and provide long-lasting protection for buildings.
Unveiling the Surprising World of Plastic Recycling: 5 Facts You Might Not Know
You may want to see also
Drying and Curing: Allow molded tiles to dry and cure for strength
Once the plastic roof tiles have been molded and shaped, the next crucial step is the drying and curing process, which is essential for ensuring the tiles' strength and durability. This phase requires careful attention to detail and a controlled environment to achieve the best results.
After the molding process, the tiles need to be left undisturbed in a well-ventilated area to allow the initial drying. This step is often overlooked but is critical to the overall success of the project. The tiles should be placed on a flat surface, ensuring they are not stacked or placed under direct sunlight, as this can lead to uneven drying. The drying process can take several hours to a few days, depending on the thickness of the tiles and the environmental conditions. During this time, it is important to monitor the tiles regularly to ensure they are not warping or developing any cracks.
After the initial drying period, the tiles must be cured to achieve their full strength. Curing is a process that hardens the plastic and ensures it becomes robust and weather-resistant. This can be done using various methods, such as:
- Natural Curing: Placing the tiles in a warm, dry environment with good air circulation. This method is cost-effective and environmentally friendly but may take longer.
- Oven Curing: Using an oven to heat the tiles, which accelerates the curing process. This method is faster but requires specialized equipment.
- Autoclave Curing: Involves placing the tiles in a high-pressure, heated environment, resulting in a rapid and thorough cure. This method is often used for large-scale production.
The curing time will vary depending on the chosen method and the specific requirements of the project. It is crucial to follow the instructions provided by the manufacturer or expert to ensure the tiles are cured adequately. Over-curing can also lead to issues, so monitoring the process is essential.
Once the tiles have dried and cured, they are ready for installation. Properly cured roof tiles will be sturdy, lightweight, and capable of withstanding various weather conditions, making them an excellent choice for eco-friendly roofing solutions.
Can You Recycle Kirkland's Plastic Egg Crates?
You may want to see also
Finishing and Installation: Treat tiles for durability and install on roofs
Once the recycled plastic roof tiles are manufactured, the finishing and installation process is crucial to ensure their longevity and effectiveness. The tiles should be treated with a protective coating to enhance their durability and resistance to the elements. A suitable sealant or coating can be applied to the surface of each tile, providing an additional layer of protection against moisture, UV rays, and general wear and tear. This treatment is especially important for plastic tiles, as they can be more susceptible to fading and discoloration over time. Consider using a UV-resistant sealant designed for outdoor applications to ensure the tiles remain aesthetically pleasing and functional for years to come.
After the treatment, the installation process can begin. Start by preparing the roof structure, ensuring it is sturdy and capable of supporting the weight of the tiles. It is recommended to use a sturdy underlayment or a specialized roof deck to provide additional support and prevent warping or sagging. Begin laying the tiles, starting from one edge of the roof and working your way across. Ensure that the tiles are securely fastened to the roof deck using appropriate fasteners, such as screws or nails, and make sure they are tightly locked in place to avoid any potential shifting.
When installing the tiles, it is essential to follow the manufacturer's guidelines and recommendations. Pay close attention to the specific instructions provided for your particular type of tile, as different designs may have unique installation requirements. Proper alignment and spacing of the tiles are critical to ensure a seamless and weather-resistant roof. Use a level to ensure that each tile is straight and even, and consider using a tile finder or a similar tool to help with alignment.
For added stability and a professional finish, consider using a tile adhesive or mastic to secure the tiles in place. This can provide an extra layer of protection against wind uplift and can be especially useful for roofs in areas prone to strong gusts. Additionally, ensure that all fasteners are properly sealed to prevent water infiltration. Once the tiles are installed, conduct a thorough inspection to identify and rectify any potential issues, such as loose fasteners or misaligned tiles.
In conclusion, the finishing and installation process is a critical phase in creating a durable and aesthetically pleasing roof using recycled plastic tiles. By applying a protective coating and following a meticulous installation procedure, you can ensure that the roof will withstand the test of time and provide a reliable barrier against the elements. Proper treatment and installation techniques will contribute to the overall success of your recycled plastic roofing project.
The Surprising Truth: Annual Plastic Cup Recycling Statistics
You may want to see also
Frequently asked questions
Using recycled plastic for roof tiles offers numerous advantages. Firstly, it reduces waste and promotes sustainability by giving new life to plastic materials that might otherwise end up in landfills or the environment. This eco-friendly approach helps conserve natural resources and lowers the carbon footprint associated with traditional roofing materials. Additionally, recycled plastic tiles are often lightweight, durable, and resistant to weathering, making them a cost-effective and long-lasting roofing solution.
Sourcing recycled plastic for roof tile manufacturing can be done through various channels. You can explore local recycling centers, waste management facilities, or even collect plastic waste from your community. Many organizations and companies specialize in collecting and processing plastic waste, making it available for manufacturers. Another option is to connect with recycling networks or platforms that facilitate the exchange of recycled materials, ensuring a steady supply of suitable plastic for your roofing project.
Several types of recycled plastic can be utilized for creating roof tiles, each with its own advantages. Common choices include high-density polyethylene (HDPE), polypropylene (PP), and polycarbonate (PC). HDPE is known for its strength and durability, making it ideal for heavy-duty roofing applications. Polypropylene offers good impact resistance and is lightweight, while polycarbonate provides excellent transparency and can be used for decorative or translucent roofing. The choice depends on the specific requirements of the project and the desired properties of the final product.
Absolutely! Recycled plastic roof tiles are designed to be versatile and can be installed over various substrates, including existing roofs. They are often lightweight, making them easy to handle and install without causing significant damage to the underlying structure. Additionally, their durability and weather resistance ensure that they can withstand the elements and provide long-term protection for your home or building. It is recommended to follow manufacturer guidelines and seek professional assistance for a successful installation.
Yes, one of the significant advantages of using recycled plastic for roof tiles is that the final product can often be recycled again at the end of its useful life. Many manufacturers use recycled content in their production processes, and the tiles themselves can be processed and transformed into new materials, completing a sustainable cycle. This closed-loop system reduces the demand for virgin resources and minimizes the environmental impact of roofing materials over time.