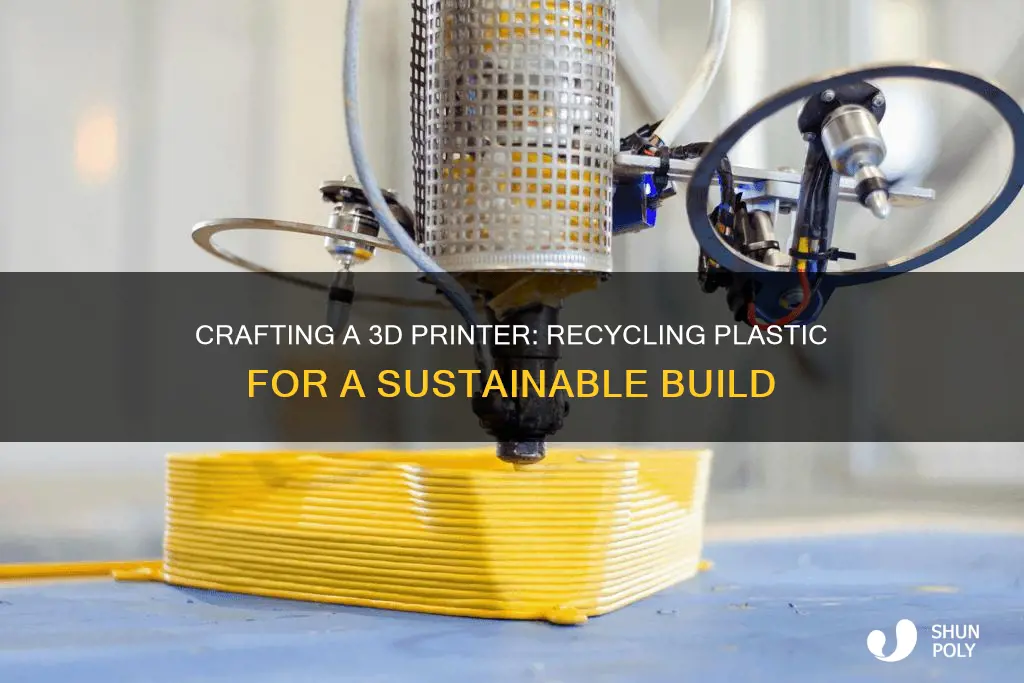
Creating a 3D printer at home using recycled plastic is an innovative and sustainable project that can be both rewarding and educational. With the right materials and a bit of creativity, you can build a functional 3D printer that will help reduce waste and open up new possibilities for creating and prototyping. In this guide, we'll explore the step-by-step process of building a 3D printer from scratch, focusing on using recycled plastic as the primary material. From understanding the components and design principles to sourcing and preparing the plastic, we'll cover everything you need to know to get started on this exciting DIY project.
What You'll Learn
Materials: Collect and prepare recycled plastic for 3D printing
When embarking on the journey of creating a 3D printer at home using recycled plastic, the first crucial step is to gather and prepare the right materials. This process involves sourcing and processing plastic waste to ensure it meets the standards required for 3D printing. Here's a comprehensive guide on how to collect and prepare recycled plastic for your DIY 3D printer project:
Collecting Recycled Plastic:
Start by identifying sources of plastic waste that can be safely used for 3D printing. Common household items like water bottles, milk jugs, and food containers are excellent candidates. Look for plastics labeled with recycling codes 1, 2, 4, or 5, as these are generally more compatible with 3D printing processes. You can collect these items from your own household, local recycling centers, or even organize a collection drive in your community. Ensure that the plastic is clean, dry, and free from contaminants like food residue or labels.
Sorting and Categorizing:
Once you have a collection of recycled plastic, it's essential to sort and categorize it. Different types of plastic have varying melting points and properties, which can affect the quality of your 3D prints. Separate the plastic into groups based on their type and color. For example, you might have PET (polyethylene terephthalate) from water bottles, HDPE (high-density polyethylene) from milk jugs, and PLA (polylactic acid) from food containers. This sorting process will make it easier to process and print with specific materials.
Cleaning and Shredding:
Before using the recycled plastic, it needs to be cleaned and prepared. Start by washing the plastic items to remove any remaining dirt or contaminants. Rinse them with water and ensure they are completely dry. Then, shred or grind the plastic into small, uniform pieces. This step helps in reducing the size of the plastic, making it easier to feed into your 3D printer's extruder. You can use a blender or a dedicated plastic shredder for this purpose. Aim for a consistent particle size to ensure even heating and feeding during the printing process.
Melting and Extrusion (Optional):
For more advanced users, you can take the process a step further by melting the shredded plastic and extruding it. This method allows for greater control over the material's properties and can be useful for creating custom filaments. You'll need a hotend and an extruder to melt and push the plastic through a nozzle. This step requires careful temperature control and precision, ensuring that the plastic is heated to the optimal temperature for printing.
Storage and Organization:
Proper storage is essential to maintain the quality of your recycled plastic. Store the sorted and prepared plastic in airtight containers or bags to prevent moisture absorption and contamination. Label each container with the type of plastic and its source. This organization will make it easier to manage your materials and ensure that you have the right plastic readily available for your 3D printing projects.
By following these steps, you'll be well-prepared to utilize recycled plastic for your 3D printer, contributing to a more sustainable and environmentally friendly printing process.
Strawberry Containers: Are They Recyclable? Unveiling the Truth
You may want to see also
Design: Create or modify 3D models for printing
When designing 3D models for your home-built printer, it's crucial to consider the specific requirements of your machine and the materials you plan to use, especially when working with recycled plastic. Here's a step-by-step guide to help you create or modify 3D models for printing:
- Choose the Right Software: Select a 3D modeling software that suits your skill level and the complexity of your projects. Popular options include Blender, Autodesk Fusion 360, and SketchUp. These programs offer a range of tools for modeling, texturing, and preparing files for 3D printing. For beginners, Blender is a great free option with a large community and extensive tutorials.
- Design Considerations:
- Layer Height and Infill: Determine the layer height, which affects the print time and quality. Thinner layers (e.g., 0.1-0.2 mm) produce higher-quality prints but take longer. Infill density, the percentage of the model's volume that is solid, is crucial for structural integrity. For recycled plastic, consider a higher infill percentage to ensure strength.
- Support Structures: Complex designs with overhangs or intricate details may require support structures to prevent warping and ensure proper adhesion during printing. You can design these supports within your model or use software plugins to generate them automatically.
- Bed Adhesion: Ensure your model has a good adhesion to the print bed. This can be achieved by adding a small brim or raft, especially for models with a flat base. These features provide additional material for the printer to adhere to, reducing the chances of warping.
File Preparation:
- Export Settings: Export your 3D model in a format compatible with your 3D printer's slicing software, such as STL or OBJ. Ensure the file is optimized for printing, with proper scaling and unit settings.
- Slicing Software: Use slicing software to convert your 3D model into a series of thin layers and generate G-code, which is the language your printer understands. Popular slicing software includes Cura, Simplify3D, and PrusaSlicer. These programs also allow you to adjust print settings like temperature, speed, and bed adhesion.
Modify and Experiment:
- Iterative Design: 3D printing often involves an iterative process. Print a prototype, inspect it, and make necessary modifications to the model. This might include adjusting layer height, infill density, or support structures.
- Material Considerations: Recycled plastic may have unique properties, such as varying densities or color inconsistencies. Experiment with different settings to optimize print quality and material usage.
Print and Post-Processing: Once you've finalized your design and settings, print your model. After printing, remove supports and perform any necessary post-processing, such as sanding, painting, or adding finishing touches to achieve the desired result.
Unraveling the Mystery: Can Plastic Butter Containers Be Recycled?
You may want to see also
Hardware: Assemble and calibrate 3D printer components
When it comes to building a 3D printer at home using recycled plastic, the hardware assembly and calibration process is a crucial step to ensure the printer's functionality and accuracy. Here's a detailed guide on how to approach this task:
Component Assembly: Start by gathering all the necessary parts you've sourced or manufactured. This includes the frame, which forms the backbone of your printer, and various mechanical parts such as the extruder, hot end, stepper motors, and the print bed. Carefully assemble these components, ensuring that each part is securely attached and aligned. Use appropriate fasteners like screws and nuts, making sure to tighten them to the recommended specifications to avoid any wobbling or instability. Pay close attention to the placement of the extruder, as it needs to be level and positioned correctly for the plastic filament to be fed accurately.
Electronics Setup: The electronics board is a critical component that controls the printer's operations. Connect the stepper motors to the board, ensuring the correct wiring for each motor's direction and speed control. Solder the hot end and any other sensors to the board, following the manufacturer's instructions. Double-check all connections to prevent short circuits or malfunctions. It is essential to test the electronics setup by powering it on and verifying that the motors respond as expected.
Calibrating the Printer: Calibration is a critical process to ensure the printer's accuracy and quality of prints. Begin by leveling the print bed; this can often be done by adjusting screws or knobs provided with the printer. Use a straightedge or a laser level to ensure the bed is perfectly flat. Next, calibrate the extruder by heating the hot end and feeding a small amount of filament through it. Measure the extrusion length and adjust the filament drive gear if necessary to achieve the desired filament flow. Calibrate the stepper motors by testing their movement in each axis (X, Y, and Z) and ensuring they move accurately and smoothly.
Fine-Tuning and Testing: After the initial assembly and calibration, it's essential to fine-tune the printer's performance. Adjust the bed adhesion settings to ensure the printed objects adhere properly to the bed. Test print a few samples to check for any issues, such as warping, layer shifting, or poor filament flow. Make adjustments to the nozzle temperature, bed temperature, or printing speed as needed to optimize the print quality.
Remember, building a 3D printer at home requires patience and attention to detail. Take your time during the assembly process, and don't rush the calibration steps to ensure a well-functioning printer. With proper care and adjustments, your recycled plastic 3D printer will be ready to create amazing models and designs.
Unraveling the Plastic Recycling Mystery: A Simple Guide
You may want to see also
Software: Choose and set up slicing software for printing
When it comes to creating a 3D printer at home using recycled plastic, software selection and setup are crucial steps. Slicing software is essential for converting your 3D model files into instructions that the printer can understand, layer by layer. Here's a guide on choosing and setting up the right slicing software:
Choosing the Right Slicing Software:
Start by researching and selecting a slicing software that suits your needs and skill level. Popular options include Cura, Simplify3D, and PrusaSlicer. These programs are widely used and offer a range of features to accommodate different 3D printing requirements. Look for software that supports your 3D modeling software (e.g., Blender, Fusion 360) and has a user-friendly interface. Consider factors such as ease of use, community support, and the availability of tutorials or documentation to help you get started.
Key Features to Look For:
- Auto-Leveling and Bed Adhesion: Modern slicing software often includes auto-leveling features that help you set up your print bed accurately. This is crucial for ensuring your prints adhere to the bed and don't warp or shift.
- Material Profiles: Different plastics require specific settings. Look for software that allows you to define material profiles, including properties like density, shrink rate, and layer height. This ensures accurate scaling and printing of your models.
- Support Structures: For complex designs, support structures are essential to prevent warping and ensure structural integrity. Slicing software should offer automatic support generation or allow you to customize support settings.
- Filament Management: Keep track of your filament inventory with software that provides filament management tools. This helps you stay organized and ensures you have the right materials for your prints.
Setting Up the Software:
Once you've chosen your slicing software, it's time to set it up for your 3D printer. Here's a general process:
- Install and Launch: Download and install the software on your computer. Launch the application and familiarize yourself with the interface.
- Connect to the Printer: Use the provided USB cable or Wi-Fi connection to link your computer to the 3D printer. This allows the software to communicate with the printer.
- Import Your Model: Open your 3D model file (e.g., STL, OBJ) in the slicing software. You can import it from your local storage or use online 3D model repositories.
- Slicing Settings: Adjust the slicing settings according to your chosen material and printer specifications. This includes setting the layer height, infill density, support structures, and other print parameters.
- Preview and Adjust: Use the software's preview feature to visualize the sliced model. Make any necessary adjustments to ensure the print is optimized.
- Export G-Code: After finalizing the settings, export the sliced model as G-code, a language that the 3D printer understands. This file contains the instructions for the printer to follow during the printing process.
Remember, each slicing software may have slightly different interfaces and settings, so it's essential to explore the software's documentation or online tutorials to understand its specific features and capabilities. With the right software setup, you'll be well on your way to creating high-quality 3D prints using recycled plastic.
Chicago's Plastic Recycling: Unraveling the 7-Number Mystery
You may want to see also
Maintenance: Regularly clean and maintain the printer for optimal performance
Regular maintenance is crucial to ensure the longevity and optimal performance of your 3D printer, especially when using recycled materials. Here's a guide on how to keep your printer in top shape:
Cleaning the Printer: Start by establishing a regular cleaning routine. After each print job, inspect the printer's components. Remove any excess filament or debris from the nozzle and the bed. Use a small brush or compressed air to gently clean the nozzle and remove any built-up material. Pay attention to the extruder and ensure it is free from any blockages or filament residue. Regularly wipe down the printer's exterior with a soft cloth to prevent the accumulation of dust and debris.
Nozzle Maintenance: The nozzle is a critical component, and its care is essential. Over time, the nozzle can become clogged or damaged, leading to poor print quality. Use a nozzle cleaning tool or a small brush to remove any debris or built-up material. Consider using a nozzle cleaning solution to dissolve any stubborn blockages. It is recommended to perform a nozzle replacement or cleaning every few print sessions to maintain optimal performance.
Bed Leveling and Calibration: Proper bed leveling is essential for accurate prints. Regularly inspect the printer bed and adjust the leveling screws to ensure a flat and even surface. Calibrate the printer's sensors and motors to improve accuracy. This process might require software adjustments, and it's a good practice to consult the printer's manual for specific calibration instructions.
Filament Management: Proper filament handling is key to preventing clogs and maintaining print quality. Store your filament in a dry and sealed environment to avoid moisture absorption. Regularly inspect the filament spools for any signs of damage or contamination. When loading filament, ensure it is properly fed into the extruder and aligned correctly.
Routine Inspections: Implement a maintenance checklist to ensure you don't miss any critical steps. This checklist can include nozzle inspection, bed cleaning, filament replacement, and overall printer health assessment. Regular inspections will help identify potential issues early on and allow for prompt action.
By following these maintenance practices, you can ensure that your 3D printer operates efficiently and consistently, even when using recycled materials. Regular care will contribute to the printer's longevity and enhance the overall quality of your 3D printing projects.
Unraveling the Process: How Recycleable Plastic is Sorted
You may want to see also
Frequently asked questions
When building a 3D printer at home, it's best to use materials that are durable, lightweight, and easy to work with. Recycled plastic, such as ABS (Acrylonitrile Butadiene Styrene) or PLA (Polylactic Acid), is an excellent choice. ABS is known for its strength and impact resistance, making it suitable for structural parts. PLA, on the other hand, is biodegradable and has a lower melting point, which can be advantageous for certain components. You can also consider using other recycled materials like PET (Polyethylene Terephthalate) bottles or HDPE (High-Density Polyethylene) containers, but ensure they are clean and free from contaminants.
Preparing recycled plastic for 3D printing involves a few steps to ensure it is in a usable form. First, collect and clean the plastic waste, removing any contaminants like food residue or labels. Then, shred or grind the plastic into small pieces to facilitate the melting process. For ABS, you can use a filament extruder to melt and extrude the plastic into a continuous filament. For PLA, you can also extrude it or consider using a 3D printer that can directly use the shredded plastic as feedstock. Properly drying and storing the extruded filament is essential to maintain its quality.
Building a 3D printer at home with recycled plastic can present some challenges. One common issue is ensuring consistent material properties, as recycled plastic may vary in quality and composition. This can lead to uneven prints or structural weaknesses. Calibration and fine-tuning of the printer's settings are crucial to achieving the best results. Additionally, managing the temperature and extrusion rate during printing is essential, especially when using different types of recycled plastics. Proper maintenance of the printer, such as regular cleaning and nozzle care, is also vital to prevent clogs and ensure high-quality prints.
Yes, design considerations are essential when using recycled plastic to maximize the material's potential. The design should account for the specific properties of the recycled plastic, such as its strength, flexibility, or melting point. For structural parts, consider using a lattice or honeycomb pattern to distribute stress more efficiently. Also, ensure that the design is optimized for the printer's capabilities and the chosen material's limitations. It's a good practice to test and iterate on designs to understand how the recycled plastic behaves under different conditions.