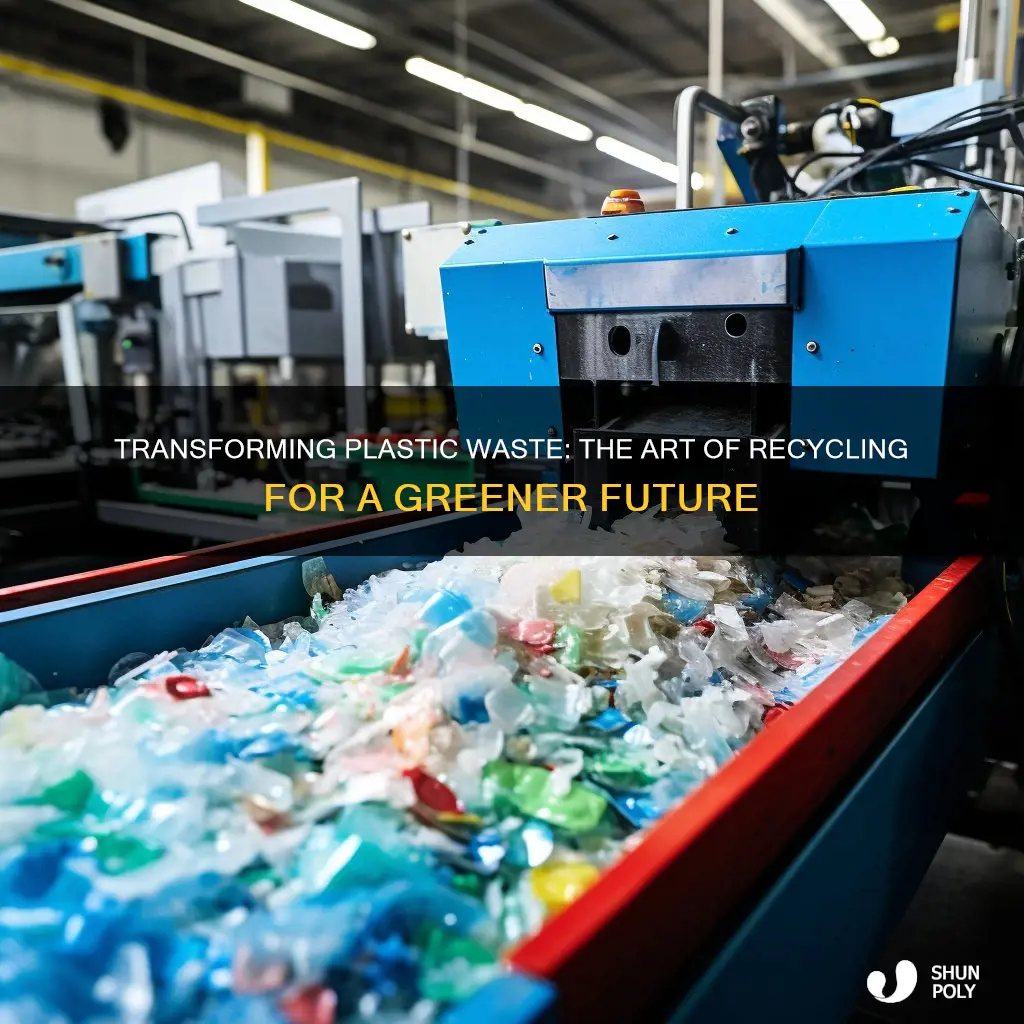
Form recycled plastic is a fascinating process that transforms waste plastic into valuable resources. It involves collecting, sorting, and processing plastic materials that have been used and discarded, giving them a new lease of life. This method not only reduces the amount of plastic waste in landfills and the environment but also contributes to a more sustainable and circular economy. The process typically begins with the collection of various types of plastic, which are then sorted and cleaned to ensure they meet the required standards. After sorting, the plastic is shredded or granulated into small pieces, which are then melted and molded into new products, such as packaging, furniture, and even construction materials. This innovative approach to recycling plays a crucial role in minimizing environmental impact and promoting a greener future.
What You'll Learn
- Collection: Sorting and gathering plastic waste from various sources
- Cleaning: Removing contaminants and impurities to ensure quality
- Shredding: Breaking down plastic into small pieces for processing
- Melting: Heating plastic to a molten state for molding
- Molding: Shaping recycled plastic into new products using different techniques
Collection: Sorting and gathering plastic waste from various sources
The process of recycling plastic begins with the collection and sorting of plastic waste, a crucial step that ensures the efficiency and effectiveness of the recycling process. This initial phase involves a systematic approach to gathering and categorizing plastic materials, which are then ready for recycling.
Once collected, the plastic waste undergoes a sorting process to separate different types of plastics. This step is critical as it determines the quality and usability of the recycled material. Common methods of sorting include manual separation, where trained personnel identify and categorize plastics based on their resin identification codes (RICs), and automated sorting systems that use optical scanners and air jets to separate plastics. Manual sorting is particularly important for ensuring that only clean and dry plastics are processed, as contaminants can significantly reduce the value of the recycled product.
The sorted plastics are then prepared for recycling by cleaning and processing them into a form suitable for manufacturing new products. This may involve shredding or granulating the plastics to create small, uniform pieces, which are then dried to remove any remaining moisture. The dried plastic flakes are further processed through washing and drying cycles to ensure they are free from impurities. This stage is crucial to producing high-quality recycled plastic that can be used in various industries.
In summary, the collection and sorting of plastic waste are fundamental steps in the recycling process, enabling the efficient transformation of discarded plastics into valuable resources. By implementing effective collection systems and employing meticulous sorting techniques, we can maximize the potential of recycled plastic, contributing to a more sustainable and environmentally friendly future.
Can Plastic Straws Transform into Dog Chews?
You may want to see also
Cleaning: Removing contaminants and impurities to ensure quality
The process of cleaning and preparing recycled plastic for further processing is a critical step to ensure the quality and usability of the material. This step involves removing various contaminants and impurities that can affect the final product's performance and appearance. Here's a detailed guide on how to achieve effective cleaning:
Sorting and Separation: Begin by sorting the recycled plastic waste based on type and color. Different types of plastics have unique properties and melting points, so separating them is essential. For instance, separate PET (polyethylene terephthalate) from HDPE (high-density polyethylene) and PVC (polyvinyl chloride). This initial sorting can be done manually or with the help of specialized equipment like optical sorters, which use sensors to identify and separate different plastic types. Proper sorting ensures that the cleaning process is more efficient and tailored to specific plastic types.
Shredding and Grinding: After sorting, the plastic waste is typically shredded or ground into smaller pieces. This step reduces the size of the plastic, making it easier to handle and clean. Shredding is useful for larger plastic items like bottles and containers, while grinding is more common for plastic flakes or pellets. The goal is to create a consistent-sized material that can be evenly processed in the cleaning stage.
Washing and Cleaning: This is the core of the cleaning process, where various techniques are employed to remove contaminants. Start with a simple wash using water to remove loose dirt, labels, and other non-plastic materials. This initial wash can be done in a washing machine or a specialized washing line. Follow this with a more thorough cleaning process:
- Ultrasonic Cleaning: This method uses high-frequency sound waves to create tiny bubbles that agitate and dislodge contaminants. It is particularly effective for removing small particles and impurities from the surface of plastic flakes.
- Chemical Cleaning: Depending on the type of plastic and the level of contamination, chemical cleaning may be necessary. This involves using specific solvents or detergents to dissolve and remove impurities. For example, acetone can be used to remove labels and stickers, while alkaline solutions can help break down grease and oil. Always follow safety protocols and wear appropriate protective gear when handling chemicals.
- Screening and Filtration: After washing, screening and filtration processes can be employed to remove any remaining small particles or contaminants. Screens with different mesh sizes can be used to separate larger debris from the cleaned plastic.
Drying and Quality Control: Once cleaned, the plastic material needs to be thoroughly dried to remove any moisture. This is crucial to prevent mold growth and ensure the plastic's stability. Air drying or using industrial dryers can be employed for this purpose. Finally, conduct quality control checks to verify the cleanliness and purity of the recycled plastic. This may include visual inspections, weight measurements, and even laboratory testing to ensure the material meets the required standards.
By following these cleaning procedures, recycled plastic can be transformed into a high-quality raw material, ready for manufacturing new products, ensuring a more sustainable and efficient use of resources.
Unraveling the Journey: From Recycled Plastic to New Beginnings
You may want to see also
Shredding: Breaking down plastic into small pieces for processing
The process of recycling plastic begins with shredding, a crucial step in transforming plastic waste into a usable form. Shredding is the initial mechanical process that reduces large plastic items into smaller, manageable pieces, preparing them for further processing and recycling. This step is essential as it increases the surface area of the plastic, allowing for more efficient separation of materials and facilitating the recycling process.
Shredding machines, often referred to as shredders or granulators, are designed to handle various types of plastic waste. These machines can process a wide range of plastic materials, including PET bottles, HDPE containers, and even mixed plastic streams. The shredding process typically involves feeding the plastic waste into the machine, where it is subjected to high-speed rotation, causing it to break apart into smaller fragments. The size of the shredded pieces can vary depending on the desired application and the specific requirements of the recycling facility.
There are different types of shredding techniques employed in the recycling industry. One common method is the single-shaft shredder, which uses a rotating shaft with large, sharp blades to cut and tear the plastic. This type of shredder is versatile and can handle a variety of materials, making it suitable for initial shredding processes. Another approach is the double-shaft shredder, which employs two counter-rotating shafts, providing a more robust and powerful shredding action, ideal for handling tough and fibrous plastic waste.
After shredding, the plastic is often further processed to remove any remaining contaminants and to create a consistent-sized product. This can involve additional steps such as washing, drying, and sorting to ensure the recycled plastic meets the required quality standards. The shredded plastic can then be sold to manufacturers who use it as raw material for producing new products, contributing to a circular economy and reducing the demand for virgin plastic production.
In summary, shredding is a vital step in the recycling process, enabling the transformation of plastic waste into a valuable resource. It allows for the efficient breakdown of plastic into smaller pieces, facilitating further processing and recycling. By employing specialized shredding machines and techniques, the recycling industry can effectively manage and recycle various plastic materials, contributing to a more sustainable and environmentally friendly approach to waste management.
The Surprising Truth: Should You Recycle Plastic Dishes?
You may want to see also
Melting: Heating plastic to a molten state for molding
The process of melting plastic is a crucial step in recycling and reshaping it into new forms. When you heat plastic to its melting point, it transforms from a solid state into a molten, or liquid-like, substance. This phase change allows for the manipulation and molding of plastic into various shapes and products. Here's a detailed guide on how this process works:
Understanding Plastic Composition: Before initiating the melting process, it's essential to understand the composition of the plastic you're working with. Different types of plastics have varying melting points and behaviors. Common types of recycled plastics include PET (polyethylene terephthalate), HDPE (high-density polyethylene), and PVC (polyvinyl chloride), each with its own unique properties. Knowing these characteristics will help you select the appropriate heating method and temperature.
Heating Techniques: Melting plastic typically involves the use of specialized equipment to ensure precise temperature control. One common method is using a heat gun or a hot air gun. These tools provide a concentrated heat source, allowing for the rapid melting of plastic. The temperature and duration of heating should be carefully managed to avoid overheating, which can lead to plastic degradation or burning. For larger-scale operations, industrial furnaces or ovens are employed, offering more uniform heat distribution and better control over temperature.
Melting Point and Temperature Control: Each type of plastic has a specific melting point, which is the temperature at which it transitions from a solid to a liquid state. For instance, PET melts around 230-250°C (446-482°F), while HDPE has a melting range of 120-140°C (248-284°F). Accurate temperature control is vital to ensure the plastic melts evenly and completely. Digital thermostats and temperature probes are often used to monitor and adjust the heat, ensuring the desired melting point is achieved without exceeding it.
Molding and Shaping: Once the plastic is molten, it can be poured into molds or shaped using various techniques. This step requires precision and skill to create the desired form. The molten plastic is carefully poured or injected into a mold, which is then cooled to set the shape. This process is known as molding or casting. After cooling, the plastic part is removed from the mold, revealing the newly formed object. This stage allows for the creation of a wide range of products, from simple household items to complex mechanical parts.
Safety and Environmental Considerations: Working with molten plastic requires adherence to safety guidelines. Proper ventilation is essential to prevent the inhalation of plastic fumes, which can be harmful if inhaled. Additionally, the use of personal protective equipment, such as heat-resistant gloves and aprons, is recommended to prevent burns. From an environmental perspective, it's important to note that the melting process should be energy-efficient and conducted in facilities with proper waste management systems to minimize the environmental impact of plastic recycling.
Recycling Plastic: Upcycling or Downgrading?
You may want to see also
Molding: Shaping recycled plastic into new products using different techniques
Molding is a versatile process that plays a crucial role in transforming recycled plastic into a wide array of new products. This technique involves shaping plastic materials into desired forms using various molding methods, each offering unique advantages and applications. Here's an overview of some common molding techniques used in the recycling and manufacturing industries:
Injection Molding: This is one of the most widely used processes for forming recycled plastic. It involves melting the plastic material and injecting it under high pressure into a mold cavity. The mold is typically made of steel and is designed with the desired product's shape. Once the plastic is injected, it rapidly cools and solidifies, taking the form of the mold. This method is highly efficient and can produce intricate and complex shapes with high precision. Injection molding is commonly used to create a vast range of items, from household goods to automotive parts. For instance, it can be used to manufacture plastic containers, packaging, toys, and even intricate electronic components.
Blow Molding: Ideal for producing hollow objects, blow molding is a two-step process. First, a heated, hollow tube (called a parison) is created by injecting plastic into a mold. Then, the parison is inflated within the mold to form the desired shape. This technique is particularly useful for creating large, hollow items like water bottles, fuel tanks, and various containers. Blow molding ensures a uniform wall thickness and excellent structural integrity, making it a preferred choice for products requiring strength and durability.
Compression Molding: In this process, two or more pieces of plastic are placed in a mold and then subjected to heat and pressure. The mold is then closed, and the plastic is compressed and heated until it takes the desired shape. Compression molding is often used for creating solid, uniform products like phone cases, electronic enclosures, and various automotive components. This method is advantageous for producing items with specific thicknesses and textures.
Thermoforming: A cost-effective and versatile technique, thermoforming involves heating a flat sheet of plastic until it becomes pliable, and then forming it over a mold. This process is commonly used for producing packaging, displays, and various consumer goods. Thermoforming can create products with a wide range of thicknesses and is suitable for both recycled and virgin plastics. The versatility of this method allows for the production of customized shapes and sizes, making it a popular choice for the packaging industry.
Each molding technique offers unique advantages, allowing manufacturers to tailor the process to the specific requirements of the recycled plastic and the desired end product. These methods contribute significantly to the circular economy by giving new life to plastic materials, reducing waste, and promoting sustainable manufacturing practices.
Can Plastic Drink Rings Be Recycled? Lexington, KY, Explains
You may want to see also
Frequently asked questions
Recycling plastic involves a series of steps to transform waste plastic into a reusable material. It begins with collecting and sorting plastic items based on their resin types. Then, the plastic is cleaned and shredded into small pieces called flakes. These flakes are washed to remove contaminants, and then heated and extruded to create a uniform plastic resin. This resin can be used to manufacture new products, such as furniture, containers, or even clothing.
Plastic recycling often requires separating different types of plastic due to their varying chemical compositions. Common types of plastic include PET (polyethylene terephthalate), HDPE (high-density polyethylene), PVC (polyvinyl chloride), LDPE (low-density polyethylene), and PP (polypropylene). You can usually find the resin identification code (RIC) on the bottom of plastic items, which is a triangle with a number inside. Each number corresponds to a specific type of plastic, and knowing these codes will help you recycle them correctly.
Absolutely! Recycling plastic has significant environmental advantages. By reusing plastic, we can reduce the demand for virgin plastic production, which often relies on fossil fuels and energy-intensive processes. This helps conserve natural resources and decreases the carbon footprint associated with plastic manufacturing. Additionally, recycling plastic diverts waste from landfills and incinerators, preventing potential pollution and contributing to a more sustainable and circular economy.