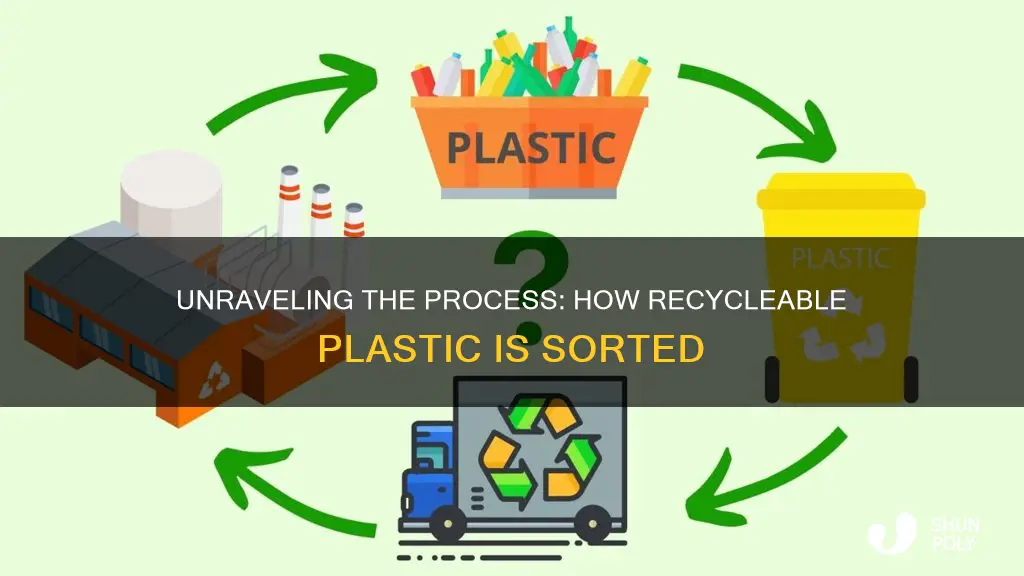
Recyclable plastic is an essential component of the circular economy, and efficient separation is key to its success. The process begins with the collection of plastic waste, which is then sorted into different types based on their resin identification codes. This initial step is crucial as it determines the feasibility of recycling and the quality of the final product. Once sorted, plastics are further processed through various methods such as washing, shredding, and melting to create new materials. Understanding these separation techniques and their impact on the recycling process is vital for optimizing the recycling chain and promoting a sustainable future.
What You'll Learn
- Sorting: Manual or automated processes to separate plastic types
- Density Separation: Using water to float or sink different plastics
- Color Sorting: Machines that separate plastics by color
- Near-Infrared (NIR) Technology: Uses light to identify plastic types
- Magnetic Separation: Removes metal contaminants from plastic streams
Sorting: Manual or automated processes to separate plastic types
The process of separating recyclable plastics is a crucial step in the recycling journey, ensuring that each type of plastic is directed to the appropriate recycling stream. This separation is typically achieved through either manual or automated methods, each with its own advantages and applications.
Manual Sorting:
Manual sorting involves human operators physically separating plastic materials. This method is often employed in small-scale recycling facilities or as a preliminary step in larger operations. Here's a breakdown of the process:
- Visual Inspection: Operators carefully examine the plastic items, identifying the type and condition of each piece. They look for signs of contamination, such as food residue or non-plastic materials, and separate them accordingly.
- Hand-Sorting: Using their hands or simple tools, workers manually pick and place plastics into designated bins or containers. This step requires skill and attention to detail to ensure accurate sorting. For example, high-density polyethylene (HDPE) bottles might be separated from polypropylene (PP) containers.
- Training and Experience: Manual sorting relies heavily on the expertise of the staff. Trained workers can quickly identify different plastic types and their unique characteristics, making this method efficient for specialized facilities.
Automated Sorting:
Automated sorting systems have revolutionized the recycling industry by increasing speed, accuracy, and efficiency. These machines are designed to handle large volumes of plastic waste and can be customized to suit specific recycling needs.
- Conveyor Belts and Sensors: Automated systems often use conveyor belts to transport plastic items. Integrated sensors and optical scanners analyze the materials, identifying plastic types based on their unique properties. For instance, infrared sensors can detect the heat signature of different plastics, allowing for precise separation.
- Air Classification: Another technique involves using air currents to separate plastics. Lightweight materials like film and bags are separated from heavier items, ensuring a more efficient sorting process.
- Advantages: Automation reduces the risk of human error and increases productivity. These machines can process a large amount of waste in a short time, making them ideal for high-volume recycling operations. Additionally, automated systems can be programmed to learn and adapt, improving their accuracy over time.
The choice between manual and automated sorting depends on various factors, including the scale of the recycling operation, available resources, and the desired level of precision. Manual sorting is valuable for small-scale initiatives and can be an educational process for communities, teaching the importance of proper plastic waste management. In contrast, automated systems are more suitable for large-scale recycling centers, where speed and efficiency are critical.
Unleash the Power of Plastic: Can Lego Pieces Be Recycled?
You may want to see also
Density Separation: Using water to float or sink different plastics
Density separation is a crucial process in the recycling of plastic waste, especially when dealing with a mixture of different types of plastics. This method takes advantage of the varying densities of various plastic materials, allowing for their separation through the use of water. Here's a detailed explanation of how it works:
When recyclable plastic is collected, it often contains a mix of various plastic types, such as PET (polyethylene terephthalate), HDPE (high-density polyethylene), PVC (polyvinyl chloride), and others. These plastics have different molecular structures, which result in distinct densities. The process begins by creating a dense solution, typically by dissolving a specific salt, like sodium chloride (table salt), in water. The salt acts as a buoyancy agent, allowing plastics to either float or sink based on their density.
Plastics with lower densities will float on the surface of the salt solution, while those with higher densities will sink. This simple yet effective principle is the foundation of density separation. For instance, PET, commonly used in beverage bottles, has a lower density and will float, while HDPE, found in milk jugs and some containers, has a higher density and will sink. By carefully monitoring the buoyancy of each plastic type, recyclers can separate them efficiently.
The process involves placing the mixed plastics into the salt solution and observing their behavior. Over time, the plastics will separate, forming distinct layers based on their densities. This method is particularly useful for large-scale recycling operations as it enables the quick and accurate sorting of various plastic types. After separation, the floating and sinking plastics can be collected, dried, and then sent for further processing, such as pelletizing or manufacturing new products.
Density separation using water is a cost-effective and environmentally friendly approach to plastic recycling. It eliminates the need for complex chemical processes and reduces the reliance on manual sorting, making it an efficient method for large volumes of plastic waste. This technique has been instrumental in improving the quality of recycled plastics and has contributed significantly to the advancement of sustainable recycling practices.
Chicago's Girl Scout Plastic Trays: Are They Recyclable?
You may want to see also
Color Sorting: Machines that separate plastics by color
The process of recycling plastic waste is a complex and crucial step in sustainable waste management. One of the critical steps in this process is the separation of different types of plastics, which is often done by color. This method, known as color sorting, is an efficient way to streamline the recycling process and ensure that each plastic type is recycled appropriately.
Color-sorting machines are designed to identify and separate various plastic materials based on their color. These machines use advanced optical sensors and algorithms to detect the unique colors of different plastics. The process begins with a conveyor belt system that feeds the plastic waste into the machine. As the waste moves along the belt, the optical sensors analyze the color of each piece of plastic. These sensors can identify a wide range of colors, from clear and transparent to various shades of blue, green, and even specialized colors like black or brown.
Once the color is detected, the machine uses mechanical arms or air jets to separate the plastic into different streams. Each stream is directed towards a specific collection area or bin, labeled with the corresponding color. For example, all clear plastics might be directed to one bin, while green plastics are sorted into another. This color-coded separation ensures that the plastics are recycled in a way that aligns with their specific properties and potential end-uses.
The efficiency of color-sorting machines is remarkable. They can process a large volume of plastic waste in a short time, often handling several tons of material per hour. This rapid processing capability is essential for recycling facilities, especially those dealing with a high turnover of waste. Moreover, these machines can be integrated into a closed-loop system, where the separated plastics are then sent for further processing, such as washing, drying, and pelletizing, to produce recycled plastic pellets ready for manufacturing new products.
Color sorting is a critical step in the recycling process, ensuring that each type of plastic is treated appropriately and efficiently. It allows for the optimization of recycling streams, reducing contamination and improving the quality of recycled materials. As technology advances, these machines continue to evolve, becoming more precise and capable of handling a broader range of plastic colors, further enhancing the effectiveness of plastic recycling efforts.
James City County's Plastic Lid Recycling: Unlocking the Potential
You may want to see also
Near-Infrared (NIR) Technology: Uses light to identify plastic types
Near-Infrared (NIR) technology is a powerful tool in the recycling industry, offering an efficient and accurate method to identify and separate different types of plastic. This innovative technique utilizes light, specifically near-infrared light, to analyze the chemical composition of materials, making it an invaluable asset in the recycling process. By employing NIR, recyclers can quickly and precisely determine the type of plastic, enabling them to sort and process it accordingly.
The process begins with feeding the recyclable plastic into the NIR machine, which emits a beam of near-infrared light onto the material. This light interacts with the plastic, causing it to emit a unique spectrum of light. Each type of plastic has a distinct absorption and reflection pattern when exposed to this light, allowing for identification. For instance, high-density polyethylene (HDPE) and polypropylene (PP) have characteristic absorption peaks that differentiate them from other plastics.
The NIR technology then analyzes these spectral signatures, creating a detailed profile of the plastic's composition. This profile is compared against a vast database of known plastic types, ensuring accurate identification. The system can distinguish between various grades of the same plastic, such as HDPE-A and HDPE-B, by recognizing subtle differences in their light absorption. This level of precision is crucial for effective recycling, as it ensures that each plastic type is sorted into the appropriate recycling stream.
One of the key advantages of NIR technology is its speed and efficiency. It can process large volumes of plastic waste rapidly, providing immediate results. This real-time analysis enables recyclers to make quick decisions, optimizing the sorting process and reducing manual labor. Moreover, NIR machines are designed to be non-destructive, meaning the plastic is not damaged during the identification process, allowing for further processing or reuse.
In summary, Near-Infrared technology revolutionizes the recycling of plastic by providing an advanced method of identification. Its ability to quickly and accurately determine plastic types is a significant step towards improving recycling efficiency and ensuring proper waste management. With NIR, the recycling industry can move towards a more sustainable future, effectively managing and reusing plastic materials.
Can Igloo Plastic Thermos Be Recycled? Unveiling the Truth
You may want to see also
Magnetic Separation: Removes metal contaminants from plastic streams
Magnetic separation is a crucial process in the recycling industry, particularly when it comes to separating metal contaminants from plastic streams. This method is highly effective in ensuring that the recycled plastic is free from any metallic impurities, which can otherwise compromise the quality of the final product. The process involves the use of powerful magnets to attract and remove metal particles from the plastic waste, making it an essential step in the recycling chain.
The process begins with the collection of recyclable plastic materials, which are then sorted and fed into a specialized magnetic separator. These separators are designed to handle various types of plastic and can be customized to accommodate different recycling streams. As the plastic waste enters the machine, it is guided through a series of magnetic fields, where the metal contaminants are targeted. Metal particles, regardless of their size or shape, are attracted to the magnetic fields and are pulled away from the plastic. This separation is based on the fundamental principle that metals are magnetic, while plastics are not.
The magnetic separator's design plays a critical role in its efficiency. It typically consists of a series of drums or belts with embedded magnets. As the plastic material moves through the separator, the metal contaminants are attracted to the magnets and adhere to them. This ensures that the metals are effectively separated from the plastic stream. The separated metal particles can then be collected and disposed of appropriately, while the clean plastic material continues through the recycling process.
One of the advantages of magnetic separation is its ability to handle a wide range of metal types. It can effectively remove ferrous metals (such as iron and steel) and non-ferrous metals (like aluminum and copper) from the plastic waste. This versatility is crucial in recycling streams where different types of metals are present alongside plastic. By using powerful magnets, the process can efficiently capture and separate these metals, ensuring a thorough purification of the plastic material.
Furthermore, magnetic separation is a non-destructive process, meaning it does not damage the plastic itself. This is essential to maintain the integrity of the recycled plastic, ensuring it can be used for various applications without compromising its quality. After the magnetic separation, the clean plastic can be further processed through washing, drying, and pelletizing to produce reusable plastic materials. This entire process contributes to a more efficient and sustainable recycling system, making magnetic separation an indispensable tool in the recycling industry.
Unraveling the Mystery: Can Plastic Forks Be Recycled?
You may want to see also
Frequently asked questions
The process of separating recyclable plastic begins with the collection of plastic waste from households and businesses. This waste is then sorted based on the type of plastic it contains. Common types of plastic include PET (polyethylene terephthalate), HDPE (high-density polyethylene), and LDPE (low-density polyethylene), each with its own unique properties and uses. Specialized equipment, such as optical sorters and air classifiers, are used to identify and separate these different types of plastic. Optical sorters use light to detect the color and type of plastic, while air classifiers use air currents to separate materials based on their density. Once separated, the plastic can be processed further to create new products.
One of the main challenges in separating recyclable plastic is the presence of contaminants. Plastic waste often contains non-plastic materials like food residue, labels, and other debris, which can interfere with the recycling process. Additionally, some plastics are more challenging to recycle than others due to their chemical composition. For example, mixed plastics or those with complex structures might require more advanced sorting techniques. Another issue is the lack of standardized recycling systems, where different regions or countries may have varying recycling processes and accepted plastic types, making it difficult to establish a consistent separation method.
Yes, several innovative approaches are being developed to enhance the efficiency and accuracy of plastic separation. One such method is the use of artificial intelligence (AI) and machine learning algorithms. These technologies can analyze large amounts of data from sorting facilities and identify patterns to improve the separation process. For instance, AI-powered cameras can inspect plastic items for quality and type, ensuring proper sorting. Another innovative technique is the development of advanced sorting machines that use near-infrared (NIR) spectroscopy. NIR spectroscopy can identify different types of plastics based on their molecular structure, providing a more precise and rapid sorting process. These advancements aim to increase recycling rates and improve the overall sustainability of plastic waste management.