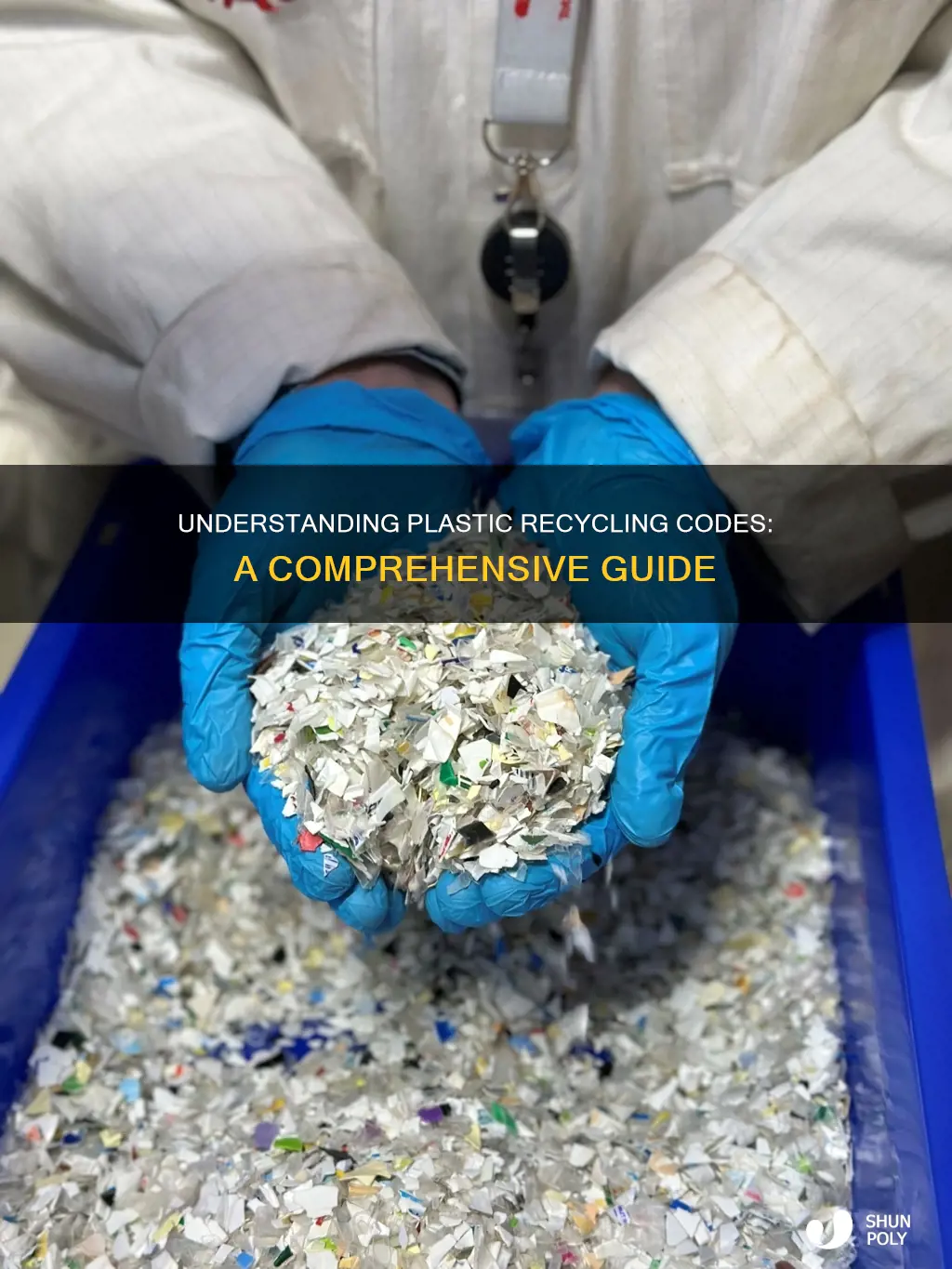
Plastic recycling is a complex process that requires careful sorting and classification of different types of plastic materials. The recycling process begins with the collection of plastic waste, which is then sorted into various categories based on their chemical composition and properties. This classification is crucial because different types of plastics have distinct recycling methods and end-uses. Common methods for rating and sorting plastics include the use of the Resin Identification Code (RIC), which is a numerical code (1-7) assigned to each type of plastic, indicating its recyclability and compatibility with specific recycling streams. Understanding these ratings is essential for effective recycling practices, ensuring that the right plastics are processed in the appropriate recycling facilities to maximize resource recovery and minimize environmental impact.
Characteristics | Values |
---|---|
Plastic Type | PET (Polyethylene Terephthalate), HDPE (High-Density Polyethylene), LDPE (Low-Density Polyethylene), PP (Polypropylene), PS (Polystyrene), PVC (Polyvinyl Chloride), and others |
Resin Identification Code | 1 (PET), 2 (HDPE), 4 (LDPE), 5 (PP), 6 (PS), 3 (PVC) |
Recycling Process | Mechanical recycling (reprocessing into new products) and chemical recycling (breaking down into raw materials) |
Common Uses for Recycled Plastic | Bottles, containers, packaging, clothing, furniture, car parts, and more |
Environmental Impact | Recycling reduces the demand for virgin plastic production, saves energy, and decreases landfill waste and pollution |
Challenges | Contamination (mixed materials), low-quality recycling, and limited infrastructure for certain types of plastic |
Consumer Awareness | Educating consumers about proper recycling practices and the importance of sorting plastics by type |
Market Demand | Growing demand for recycled plastics in various industries, including packaging, construction, and automotive |
Future Trends | Development of advanced recycling technologies, circular economy models, and improved recycling infrastructure |
What You'll Learn
- Plastic Type: Different types of plastic (e.g., PET, HDPE) have unique recycling codes and processes
- Contamination: Mixed plastics and food residue can hinder recycling, requiring careful sorting
- Quality: Plastic quality affects recyclability; some materials are more durable and reusable
- Local Regulations: Recycling guidelines vary by region, influencing accepted plastic types and preparation methods
- Market Demand: The demand for recycled plastic influences its economic viability and recycling practices
Plastic Type: Different types of plastic (e.g., PET, HDPE) have unique recycling codes and processes
Understanding the different types of plastic and their respective recycling codes is essential for effective recycling practices. Plastic is categorized into various types, each with its own unique properties and recycling methods. Here's an overview of some common plastic types and their recycling codes:
PET (Polyethylene Terephthalate): PET is widely used for beverage bottles, food containers, and packaging. It is identified by the recycling code 1. This type of plastic is highly recyclable and can be processed into new containers, fibers for clothing, or even used in carpet manufacturing. PET bottles are often clear or slightly tinted and are commonly found in the beverage industry. Recycling PET involves a process called PET bottle recycling, where the bottles are collected, cleaned, and then shredded or granulated to create new raw materials.
HDPE (High-Density Polyethylene): HDPE is commonly used for milk jugs, detergent bottles, and some shopping bags. Its recycling code is 2. HDPE is known for its strength and durability, making it suitable for various applications. This plastic type can be recycled into new containers, especially those used for personal care products and household cleaning items. The recycling process for HDPE involves melting the plastic and reforming it into new products, ensuring a closed-loop system.
PVC (Polyvinyl Chloride): PVC is a versatile plastic used in construction, plumbing, and electrical wiring. It is often identified by the recycling code 3. However, due to the presence of additives and stabilizers, PVC can be challenging to recycle. It is crucial to check local recycling guidelines, as not all facilities accept PVC. When recycled, PVC can be transformed into new construction materials, window frames, or even furniture.
LDPE (Low-Density Polyethylene): LDPE is commonly found in plastic bags, film wraps, and some food containers. Its recycling code is 4. This plastic type is relatively easy to recycle and can be processed into new bags, compost bins, or even furniture. LDPE recycling often involves a process called extrusion, where the plastic is melted and drawn into thin strands to create new products.
PP (Polypropylene): PP is used in food containers, bottle caps, and packaging. It is identified by the recycling code 5. PP is known for its heat resistance and is often used in microwave-safe containers. This plastic type can be recycled into new containers, brooms, and even battery cases. The recycling process for PP typically involves shredding, washing, and then melting the plastic to create new raw materials.
Each plastic type has its own unique characteristics and recycling requirements. It is crucial to check local recycling guidelines and ensure that items are properly sorted and cleaned before recycling. Understanding these differences empowers individuals and communities to contribute to a more sustainable and effective recycling system.
Keurig Pods: Unraveling the Plastic Recycling Mystery
You may want to see also
Contamination: Mixed plastics and food residue can hinder recycling, requiring careful sorting
Contamination is a significant issue in plastic recycling, and it can have a detrimental impact on the entire process. When plastic waste is contaminated with food residue or mixed with other types of plastics, it becomes challenging and often impossible to recycle effectively. This is because the recycling process requires specific conditions and materials to function optimally.
Mixed plastics, for instance, pose a problem as different types of plastic have unique chemical compositions and melting points. When these plastics are combined, they can interfere with the recycling machinery, leading to potential damage or reduced efficiency. For example, a mixture of PET (polyethylene terephthalate) and HDPE (high-density polyethylene) can cause issues during the sorting and processing stages, as these plastics have different properties and may not be compatible with the same recycling stream.
Food residue on plastic items is another critical concern. Organic matter, such as leftover food, grease, or oil, can attract pests and cause unpleasant odors, making the recycling process less appealing and potentially hazardous. Moreover, food residue can lead to cross-contamination, especially when different types of plastics are present. This contamination can render the entire batch of recycled material unusable or of poor quality.
To address this issue, it is essential to practice proper waste management and sorting at the source. Consumers and businesses should be encouraged to separate their plastic waste into different categories, ensuring that similar types of plastics are grouped together. For instance, all PET bottles should be placed in one bin, and HDPE containers in another. This simple act of sorting can significantly reduce contamination and make the recycling process more efficient.
Additionally, raising awareness about the importance of clean plastic waste is crucial. Educating people about the negative consequences of contamination can motivate better recycling habits. By ensuring that plastic items are free from food residue and properly sorted, we can minimize the risks associated with contamination and contribute to a more sustainable recycling system. This practice is vital for maintaining the integrity of the recycling process and ensuring the production of high-quality recycled materials.
Whole Foods Recycling: Unraveling Plastic Packing Policies
You may want to see also
Quality: Plastic quality affects recyclability; some materials are more durable and reusable
The quality of plastic plays a crucial role in its recyclability and the overall sustainability of the recycling process. Different types of plastics possess varying levels of durability and reusability, which directly impact their ability to be recycled effectively. For instance, high-density polyethylene (HDPE) and polypropylene (PP) are known for their excellent durability and are widely accepted in recycling streams. These materials can withstand multiple recycling cycles without significant degradation, making them ideal for producing new products. On the other hand, some plastics, like polystyrene (PS), are more fragile and can break down during the recycling process, leading to lower-quality end products.
The key to successful plastic recycling lies in understanding the properties of various plastic types. Polyethylene terephthalate (PET), commonly used in beverage bottles, is highly recyclable and can be recycled multiple times without losing its structural integrity. This material's ability to retain its quality through recycling is a significant advantage in the circular economy. In contrast, certain plastics, such as those used in single-use packaging, may contain additives or be mixed with other materials, making them more challenging to recycle. These complexities often result in lower recycling rates and can lead to contamination in the recycling stream.
To improve plastic recyclability, manufacturers and consumers should focus on using materials with higher durability and reusability. This approach encourages the production of long-lasting products that can be easily recycled at the end of their useful life. For example, opting for HDPE or PP containers instead of those made from less durable plastics can significantly enhance the recyclability of packaging materials. Additionally, designing products with recyclability in mind, such as using easily separable components or choosing materials with a higher recycling value, can further contribute to a more efficient recycling system.
Educating consumers about the importance of plastic quality is essential. By understanding the recyclability of different plastics, individuals can make informed choices when purchasing products. For instance, choosing items packaged in easily recyclable materials can encourage a more sustainable approach to consumption. Moreover, proper waste sorting and disposal practices can ensure that high-quality plastics are directed to recycling facilities, maximizing their potential for reuse.
In summary, the quality of plastic is a critical factor in determining its recyclability. Materials with superior durability and reusability, such as HDPE and PP, are more readily accepted in recycling processes. By recognizing the recyclability potential of different plastics and making informed choices, we can contribute to a more sustainable and efficient recycling system, ultimately reducing the environmental impact of plastic waste.
Unraveling the Mystery: Can Plastic Forks Be Recycled?
You may want to see also
Local Regulations: Recycling guidelines vary by region, influencing accepted plastic types and preparation methods
The recycling landscape is a complex one, with local regulations playing a pivotal role in determining what types of plastic can be recycled and how they should be prepared for processing. These guidelines are essential as they ensure that the recycling process is efficient, effective, and environmentally sound. Each region has its own set of rules and standards, which can vary significantly from one area to another. For instance, in some cities, all plastic packaging is accepted, while in others, only specific types are welcomed. This variation is primarily due to the diverse range of plastic materials and their respective recycling capabilities.
In many urban areas, local governments have implemented comprehensive recycling programs that include a wide array of plastic types. For example, residents might be encouraged to collect and recycle common household plastics like PET (polyethylene terephthalate) bottles, HDPE (high-density polyethylene) milk jugs, and LDPE (low-density polyethylene) shopping bags. These materials are often accepted in curbside recycling programs, making it convenient for residents to participate. However, it's crucial to note that not all plastics are created equal in terms of recyclability.
The preparation of plastic for recycling is another critical aspect influenced by local regulations. Some regions require that plastics be cleaned, dried, and free of contaminants before they can be processed. This might include removing labels, caps, and non-plastic components, as well as ensuring that the plastic is not greasy or soiled. For instance, a local recycling center might specify that PET bottles should be rinsed with water to remove any food residue, while HDPE containers should be left with their original labels intact. These guidelines are designed to maintain the quality of the recycled material and prevent contamination that could render it unusable.
Furthermore, the recycling process itself can vary by region. Some areas might have specialized facilities that can handle a broader range of plastic types, while others might focus on specific materials due to technological limitations or market demands. For instance, a region with a strong recycling infrastructure for HDPE might prioritize this material, ensuring that it is efficiently sorted, processed, and transformed into new products. Understanding these local variations is essential for residents and businesses to ensure that their recycling efforts are in line with regional standards.
In summary, local regulations significantly impact the recycling of plastic, dictating which types of plastic are accepted and how they should be prepared for recycling. These guidelines are tailored to the specific needs and capabilities of each region, ensuring that the recycling process is efficient and environmentally friendly. Residents and businesses must stay informed about these local variations to maximize their contribution to sustainable waste management.
Dirty Plastic: Can It Still Be Recycled?
You may want to see also
Market Demand: The demand for recycled plastic influences its economic viability and recycling practices
The demand for recycled plastic is a critical factor that significantly impacts the entire recycling process and the economic sustainability of the industry. When the market demand for recycled plastic is high, it creates a strong incentive for recycling operations to thrive and expand. This increased demand often leads to more efficient collection, sorting, and processing systems, as recycling facilities can justify the costs associated with setting up and maintaining these operations. As a result, the quality of recycled plastic can improve, with more consistent and standardized products being produced.
In contrast, low market demand for recycled plastic can hinder the recycling process and make it economically unviable. When the demand is insufficient, recycling facilities may struggle to generate enough revenue to cover their operational costs, leading to potential closures or reduced recycling capacity. This scenario can create a vicious cycle, as the lack of recycled plastic products in the market further diminishes the demand, making it even more challenging to establish a robust recycling infrastructure.
The economic viability of recycled plastic is closely tied to its market value. If the demand for recycled plastic is high and stable, it can command a competitive price, making the recycling process financially rewarding. This, in turn, encourages more plastic waste to be collected and processed, contributing to a more sustainable waste management system. However, when the market demand is inconsistent or low, the economic incentives for recycling may diminish, leading to a decrease in the overall recycling rate.
To address the issue of low market demand, various strategies can be employed. One approach is to increase consumer awareness about the benefits of using recycled plastic products. Educational campaigns and marketing initiatives can highlight the environmental advantages and the positive impact on local communities, encouraging consumers to choose recycled plastic items. Additionally, government policies and incentives can play a crucial role in stimulating demand. Tax benefits, subsidies, or mandatory recycling targets can be implemented to make recycled plastic more attractive to manufacturers and consumers alike.
Another strategy to enhance market demand is to diversify the applications of recycled plastic. Currently, recycled plastic is often used in lower-value products, such as construction materials or packaging. By exploring new markets and developing innovative products, the demand for recycled plastic can be expanded. For example, advancements in technology have led to the creation of recycled plastic fibers for clothing, automotive parts, and even furniture, opening up new avenues for recycling and increasing its economic viability.
Unraveling the Mystery: Can Milk Cartons with Plastic Spouts be Recycled?
You may want to see also
Frequently asked questions
Plastic recycling is often rated using a system called the Resin Identification Code (RIC), which is a series of numbers (1-7) inside a triangle on the bottom of plastic products. This code helps identify the type of plastic and its suitability for recycling.
The RIC system provides a standardized way to communicate the type of plastic. Each number corresponds to a specific type of plastic resin: 1 (PET), 2 (HDPE), 3 (PVC), 4 (LDPE), 5 (PP), 6 (PS), and 7 (Other). These codes help recycling facilities sort and process plastics efficiently.
No, the RIC number alone does not determine recyclability. While plastics with the same RIC number may be accepted in some recycling programs, others might have specific requirements. For instance, PET (1) is widely recycled, but HDPE (2) might have more limited recycling options. It's essential to check with your local recycling guidelines.
Plastics rated as '7' or 'Other' are often made from a blend of different resins and are generally not recyclable in standard recycling streams. These items are challenging to process due to their complex composition. However, some specialized recycling programs or collection events might accept these plastics for specific recycling or upcycling initiatives.