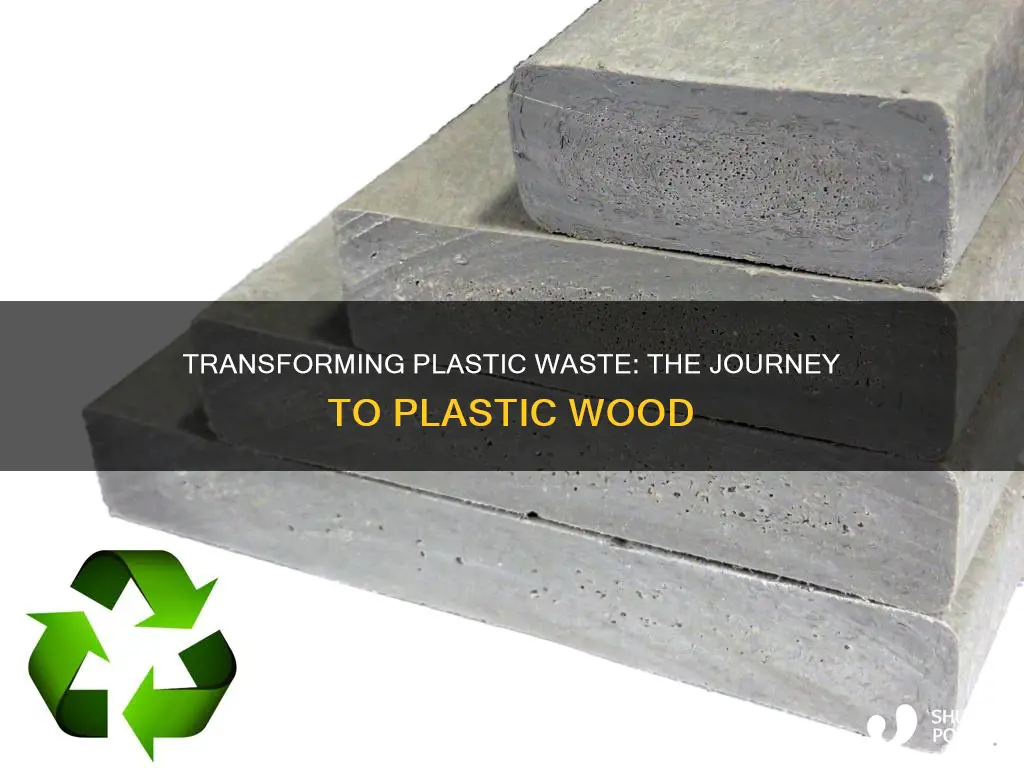
Plastic recycling plays a crucial role in transforming waste into valuable resources, and one innovative process involves recycling plastic to create wood-like products. This process begins with collecting and sorting plastic waste, ensuring it meets specific quality standards. The plastic is then shredded or granulated into small pieces, which are cleaned to remove any contaminants. Through a process called plastic-to-wood, the cleaned plastic is heated and subjected to high pressure, causing it to undergo a chemical transformation. This process results in a material that resembles wood in texture and appearance, often used for outdoor furniture, decking, and landscaping products. The recycled plastic wood offers a sustainable alternative to traditional wood, reducing the demand for virgin resources and minimizing environmental impact.
Characteristics | Values |
---|---|
Process Overview | Plastic waste is sorted, cleaned, and shredded into small pieces. These pieces are then washed to remove contaminants. The cleaned plastic is ground into a fine powder and mixed with other materials like wood flour or sawdust. This mixture is heated and pressed into a mold to create the desired shape and size of the plastic wood product. |
Types of Plastic Used | Common plastics used include polypropylene (PP), high-density polyethylene (HDPE), and polyvinyl chloride (PVC). These plastics are chosen for their durability, strength, and ease of processing. |
Recycling Methods | The process typically involves mechanical recycling, where the plastic is ground and re-formed, or chemical recycling, which breaks down the plastic into its basic components for new material creation. |
Environmental Benefits | Plastic wood products offer a sustainable alternative to traditional wood, reducing deforestation and the demand for new resources. Recycling plastic also diverts waste from landfills and oceans, contributing to a circular economy. |
Applications | Plastic wood is used in various applications, including outdoor furniture, decking, landscaping timbers, playground equipment, and even boat hulls. It provides a lightweight, durable, and weather-resistant alternative to traditional wood. |
Strength and Durability | Plastic wood products often exhibit superior strength and durability compared to natural wood, especially in outdoor applications. They are resistant to rot, insects, and UV degradation. |
Color and Customization | These products can be easily colored and customized during the manufacturing process, offering a wide range of design options. |
Cost | The cost of plastic wood products can vary depending on the type of plastic used, the manufacturing process, and the specific application. However, they often provide long-term cost savings due to their durability and longevity. |
Disadvantages | One potential drawback is the initial higher cost compared to traditional wood, and the process may not be as widely available as conventional recycling methods. |
What You'll Learn
- Collection: Plastic waste is gathered from various sources, ensuring it's clean and sorted by type
- Shredding: Plastic is broken down into small pieces, making it easier to process
- Cleaning: Impurities are removed to prevent contamination and ensure product quality
- Pelletizing: Plastic flakes are heated and extruded into uniform pellets
- Forming: Pellets are melted and shaped into wood-like products using molding techniques
Collection: Plastic waste is gathered from various sources, ensuring it's clean and sorted by type
The collection of plastic waste is a crucial step in the recycling process, as it forms the foundation for creating valuable materials like plastic wood. This phase involves a meticulous process to ensure the waste is clean, sorted, and ready for transformation.
Plastic waste collection begins with the identification and gathering of plastic materials from various sources. This includes residential areas, where individuals can separate their plastic waste, such as bottles, containers, and packaging, into different categories. Local authorities and waste management companies play a vital role here by implementing collection programs and providing designated bins or bags for residents to deposit their plastic waste. These sources are essential as they provide the raw material for recycling.
Once collected, the plastic waste undergoes a cleaning process to remove any contaminants. This step is critical to ensure the quality of the recycled material. Cleaning methods may include washing the plastic items to eliminate dirt, food residue, or labels. For example, PET bottles, a common plastic type, are often sorted and cleaned to remove any residual liquid or labels, making them suitable for recycling into new products.
After cleaning, the sorted plastic waste is prepared for the recycling process. This involves further categorization based on the type of plastic. Different types of plastics, such as PET, HDPE, and PVC, have unique properties and uses. Sorting by type is essential to ensure the recycled material meets the requirements of specific applications, like those in the construction industry for plastic wood products.
The sorted and cleaned plastic waste is then ready for processing into new products. This stage may involve shredding or granulating the plastic to create a uniform material that can be molded or formed into various shapes, including those used in plastic wood production. The collection and preparation process ensures that the recycled plastic is of high quality and suitable for creating durable and sustainable wood-like products.
Chicago's Girl Scout Plastic Trays: Are They Recyclable?
You may want to see also
Shredding: Plastic is broken down into small pieces, making it easier to process
Shredding is a crucial step in the recycling process of plastic, especially when it comes to creating plastic wood-like products. This method involves breaking down plastic waste into smaller, more manageable pieces, which significantly simplifies the subsequent processing and manufacturing stages. The shredding process is designed to reduce the size of the plastic material, making it easier to handle and transform into new products.
When plastic waste is collected and sorted, it is often in various forms, such as bottles, containers, or even mixed plastic products. The shredding machine, equipped with sharp blades or rotating drums, is used to feed these plastic items. As the plastic enters the shredder, it is cut, torn, or shredded into tiny fragments, often referred to as 'shreds' or 'flakes'. This process can be customized to produce different sizes of plastic pieces, depending on the desired outcome and the specific requirements of the recycling facility.
The shredded plastic material is then cleaned to remove any contaminants, such as dirt, labels, or other non-plastic items. This cleaning process ensures that the recycled plastic is of high quality and meets the standards for further processing. After cleaning, the shredded plastic is often dried to remove any moisture, which can affect the quality of the final product.
Once the shredded plastic is ready, it can be used in various ways. One common application is in the production of composite wood products. The shredded plastic is combined with wood fibers, binders, and other additives to create a mixture that can be pressed and formed into sheets or panels. These panels can then be used as a substitute for traditional wood in construction, furniture, or decorative applications.
Shredding is an essential step in the recycling chain as it transforms plastic waste into a usable form, making it the foundation for creating new products. This process not only reduces the volume of plastic waste but also contributes to a circular economy by giving new life to used plastic materials. By breaking down plastic into smaller pieces, recycling facilities can efficiently process and repurpose plastic waste, ultimately leading to the production of durable and sustainable plastic wood-like products.
Recycling Plastic Toys: What You Need to Know
You may want to see also
Cleaning: Impurities are removed to prevent contamination and ensure product quality
The cleaning process is a critical step in plastic recycling, especially when transforming plastic into wood-like products. This step ensures that the final product is of high quality and free from contaminants that could compromise its performance and durability. Here's a detailed breakdown of the cleaning process:
Sorting and Segregation: The initial stage involves sorting and segregating plastic waste based on type and color. This step is crucial as it helps in identifying and removing specific types of plastics that might not be suitable for wood-like product manufacturing. For instance, certain plastics may have lower melting points, making them less ideal for the process. By segregating plastics, recyclers can ensure that only the right types are used, improving the overall quality of the final product.
Washing and Cleaning: Once sorted, the plastic waste undergoes a thorough washing process. This involves using industrial-grade washing machines or systems that employ water, air, or mechanical agitation to remove any dirt, debris, or residual contaminants. The washing process helps in eliminating any impurities that might have accumulated during the collection and sorting stages. It also ensures that the plastic flakes or pellets are clean and free from any foreign matter, which is essential for the next steps in the recycling process.
De-watering and Drying: After washing, the plastic material needs to be de-watered and dried. This step is vital as it removes excess moisture that could lead to mold growth or affect the material's properties. De-watering is typically achieved through centrifugal or vacuum methods, which help in extracting water from the plastic. Following this, the material is dried using air blowers or ovens to ensure that it reaches the desired moisture content.
Milling and Grinding: In this step, the cleaned and dried plastic is processed further to create a consistent and uniform material. Milling and grinding involve breaking down the plastic into smaller particles or flakes. This process ensures that the plastic is in a suitable form for the subsequent steps, where it is melted and molded into wood-like products. The size and shape of the particles can be controlled to meet the specific requirements of the final product.
Quality Control: Throughout the cleaning process, quality control measures are implemented to ensure that the plastic is clean and free from any contaminants. This includes visual inspections, moisture content testing, and sometimes even more advanced techniques like infrared spectroscopy to identify any impurities. By maintaining strict quality control, recyclers can guarantee that the final wood-like product meets the desired standards and performs optimally.
The cleaning process is a meticulous and essential phase in plastic recycling, as it sets the foundation for the quality and performance of the final wood-like product. By removing impurities and ensuring a clean material, recyclers can produce high-quality products that are both sustainable and functional.
Plastic Film Recycling: Where to Find the Right Drop-Off Points
You may want to see also
Pelletizing: Plastic flakes are heated and extruded into uniform pellets
The process of transforming recycled plastic into wood-like products begins with the collection and sorting of plastic waste. Once sorted, the plastic is shredded or granulated into small flakes, ensuring a consistent size for efficient processing. These plastic flakes are then fed into a pelletizing machine, a crucial step in the recycling journey.
Pelletizing is an essential process that involves heating and shaping the plastic flakes. The flakes are heated to a specific temperature, typically around 180-220 degrees Celsius, depending on the type of plastic. This heat treatment is vital as it softens the plastic, making it more malleable and easier to process. The heated plastic is then extruded through a die, which shapes it into uniform pellets. This extrusion process requires precision to ensure the pellets have a consistent size and quality. The pellets are often cooled rapidly to solidify their shape, and then they are ready for further processing.
The resulting pellets are a key raw material for producing plastic wood-like products. These pellets can be used directly in manufacturing or further processed to create specific grades of plastic. For instance, they can be blended with other materials like wood flour or cellulose to enhance the product's properties, such as strength and durability. This blending process is often tailored to the desired application, whether it's for outdoor furniture, decking, or indoor decorative elements.
Pelletizing offers several advantages in the recycling process. Firstly, it reduces the volume of plastic waste significantly, making it easier to store and transport. Secondly, the uniform size of the pellets ensures consistent quality, which is crucial for manufacturing high-quality wood-like products. Additionally, the process allows for the separation of different types of plastics, enabling the production of specialized products.
In summary, pelletizing is a critical step in recycling plastic to create wood-like alternatives. It transforms plastic flakes into valuable pellets, which serve as the foundation for various applications. This process showcases the potential of recycling to create sustainable and innovative materials, offering an eco-friendly solution to the plastic waste problem.
Mr. Coffee Pots: Glass, Plastic, and Recycling Options
You may want to see also
Forming: Pellets are melted and shaped into wood-like products using molding techniques
The process of recycling plastic to create wood-like products begins with the collection and sorting of plastic waste. Once sorted, the plastic is cleaned and shredded into small pieces, which are then melted into pellets. These pellets are the raw material for the next stage of production.
In the 'Forming' stage, the melted plastic pellets are an essential component. The pellets are heated to a specific temperature, typically around 200-250°C, to ensure they are in a molten state. This temperature is carefully controlled to maintain the quality and consistency of the final product. The molten plastic is then fed into a molding machine, which is a crucial piece of equipment in this process.
Molding techniques are employed to shape the plastic into wood-like products. The machine applies pressure and heat to the plastic, forcing it into a pre-designed mold. This mold can take various shapes and sizes, depending on the desired product. For example, it could be a flat sheet to mimic wooden planks or a more complex shape to resemble wooden beams or furniture. The molding process involves precise control of temperature and pressure to ensure the plastic takes the desired form.
During the molding process, the plastic is cooled and hardened, creating a solid structure. This solidification is crucial as it gives the plastic wood-like properties, including a texture and appearance that mimics natural wood. The cooling process is carefully managed to avoid any defects or imperfections in the final product. Once the plastic has cooled and hardened, the mold is opened, and the finished product is removed.
This forming stage is a critical step in recycling plastic to create sustainable alternatives to wood. It showcases how waste plastic can be transformed into valuable, wood-like materials through advanced manufacturing techniques. The process ensures that the recycled plastic retains its strength and durability while offering a unique, eco-friendly solution for various applications, from construction to furniture.
Can Plastic Champagne Flutes Be Recycled? Unveiling the Truth
You may want to see also
Frequently asked questions
Plastic recycling for wood-like products typically involves a process called "plastic-to-fuel" or "plastic-to-oil" conversion. This process begins with collecting and sorting plastic waste, which is then shredded or granulated to reduce its size. The plastic is heated to high temperatures, often in a process called pyrolysis, where it breaks down into smaller molecules, releasing oil or gas. This oil can be further refined and processed to create a material similar to crude oil. The resulting material is then used to produce plastic wood or composite materials.
The recycled plastic, often in the form of flakes or pellets, is mixed with other materials like wood flour, cellulose, or synthetic fibers. This mixture is then heated and pressed into a mold to create a solid panel or board. The process is similar to how traditional wood-plastic composites (WPC) are made, but instead of using virgin wood, recycled plastic is utilized. This method helps reduce waste and provides an eco-friendly alternative to traditional wood products.
Yes, there are various techniques employed in the recycling process. One common method is mechanical recycling, where the plastic is cleaned, shredded, and melted to create new products. Another approach is chemical recycling, which involves breaking down the plastic at a molecular level using solvents or catalysts to produce valuable chemicals and feedstocks. These processes can be tailored to produce specific wood-like materials with desired properties.
Recycling plastic for wood-like applications offers several advantages. Firstly, it diverts plastic waste from landfills or incinerators, reducing environmental pollution. Secondly, it provides a sustainable alternative to traditional wood, which can be scarce or contribute to deforestation. Plastic wood products are often more durable, weather-resistant, and have a longer lifespan compared to conventional wood. Additionally, the process can create new job opportunities in the recycling and manufacturing sectors.
Not all plastics are suitable for this recycling process. The most commonly used plastics for wood-like products are polypropylene (PP) and high-density polyethylene (HDPE), which are known for their durability and ease of processing. However, other plastics like polystyrene (PS) and polyvinyl chloride (PVC) can also be recycled and incorporated into composite materials. The choice of plastic depends on factors such as availability, cost, and the desired properties of the final product.