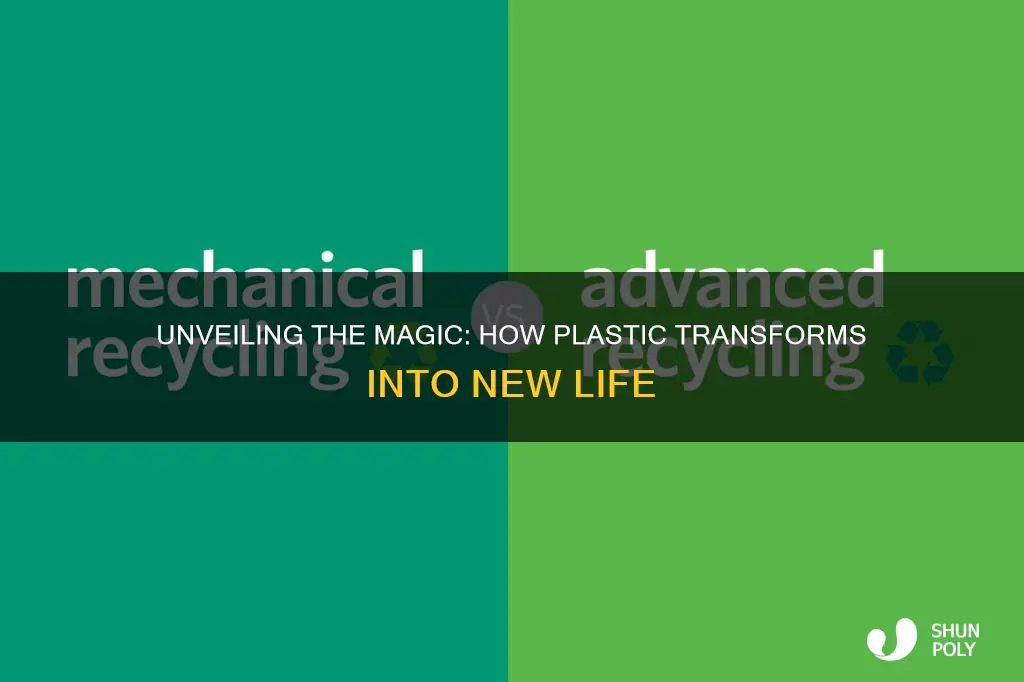
Plastic recycling is a complex process that involves several stages to transform used plastic materials into new products. It begins with the collection and sorting of plastic waste, which is then cleaned and shredded into small pieces. These pieces are further processed through a process called recycling, where they are heated and melted to form a molten mass. This molten mass is then shaped and molded into new products, such as new plastic containers or even construction materials. The entire process requires careful handling and specialized equipment to ensure the quality and purity of the recycled plastic.
What You'll Learn
Collection: Sorting and cleaning plastic waste to prepare for recycling
The process of recycling plastic begins with the collection and sorting of plastic waste, which is a crucial step to ensure the quality and efficiency of the recycling process. This initial phase involves a series of meticulous procedures to prepare the plastic for recycling.
Collection is the first step, where plastic waste is gathered from various sources such as residential areas, commercial buildings, and public spaces. This waste can include items like plastic bottles, containers, packaging materials, and even discarded electronics. It is essential to collect plastic waste separately from other types of waste to facilitate proper sorting and recycling. Local governments, waste management companies, and community initiatives often organize collection drives or provide designated drop-off points to make this process more accessible to the public.
Once collected, the plastic waste undergoes sorting, which is a critical step to separate different types of plastics. Plastic is typically identified by its resin identification code, often indicated by a number inside a triangle on the bottom of the item. Common types of plastics include PET (polyethylene terephthalate), HDPE (high-density polyethylene), PVC (polyvinyl chloride), LDPE (low-density polyethylene), and PP (polypropylene). Sorting ensures that each type of plastic is processed appropriately, as different plastics have varying recycling methods and compatibility with recycled products. Manual sorting is often done by trained personnel who carefully examine the waste and separate it into different categories. Advanced sorting techniques also utilize optical scanners and near-infrared spectroscopy to identify and separate plastics more efficiently.
After sorting, the plastic waste must be cleaned to remove contaminants and impurities. This step is crucial because plastic recycling processes are sensitive to the presence of non-plastic materials, such as food residue, labels, and other debris. Cleaning involves removing any non-plastic components, like caps, labels, and polystyrene foam, which are typically made of different materials and cannot be recycled with plastic. This process may also include washing the plastic items to eliminate any remaining dirt or residue. Advanced cleaning methods use water flotation systems to separate plastics based on their density, ensuring that only clean and dry plastic materials proceed to the recycling stage.
The sorted and cleaned plastic waste is then ready for the recycling process, which can involve various methods such as mechanical recycling, chemical recycling, or a combination of both. Mechanical recycling involves reprocessing the plastic into new products without altering its chemical structure. This process typically includes granulating the plastic into small pellets, which can then be used to manufacture new products like furniture, construction materials, or even new packaging. Chemical recycling, on the other hand, breaks down the plastic into its original chemical components, allowing for the creation of new materials with specific properties. This process is particularly useful for plastics that are difficult to recycle through mechanical means.
Australia's Plastic Recycling: A Deep Dive into the Process
You may want to see also
Shredding: Plastic is broken down into small pieces or flakes
Shredding is a crucial step in the recycling process of plastic, as it involves breaking down plastic materials into smaller, more manageable pieces. This process is designed to reduce the size of the plastic waste, making it easier to handle and process further. The shredded plastic can then be sorted, cleaned, and prepared for the next stages of recycling.
When plastic is shredded, it undergoes a mechanical transformation. The plastic items, which could be bottles, containers, or other plastic products, are fed into a shredding machine. These machines use sharp blades or rotating knives to cut and tear the plastic into tiny fragments. The shredding process aims to create a uniform size of plastic pieces, often referred to as 'flakes' or 'pellets'. This uniformity is essential for ensuring that the recycled plastic can be consistently processed and utilized in various applications.
The shredded plastic flakes are typically very small, sometimes even finer than a grain of sand. This size reduction is significant because it allows for better control over the recycling process. Smaller pieces have a larger surface area, which facilitates the removal of contaminants and impurities during the cleaning stage. Additionally, the smaller size makes it easier to melt and mold the plastic into new products, as it requires less energy to process the material.
After shredding, the plastic flakes are often sorted to separate different types of plastics. This sorting process is crucial to ensure that the recycled material meets the required standards and can be used in specific applications. For example, PET (polyethylene terephthalate) bottles and HDPE (high-density polyethylene) containers are often shredded and sorted separately due to their distinct properties and uses in the recycling market.
Shredding is a vital step that prepares the plastic for the subsequent stages of recycling, including washing, drying, and re-pelletizing. It is a mechanical process that transforms large plastic items into a valuable raw material, ready to be reborn as new products, contributing to a more sustainable and circular economy.
Unraveling the Mystery: Can Plastic Straws Be Recycled?
You may want to see also
Melting: Plastic flakes are heated to a molten state
The process of recycling plastic begins with the collection and sorting of plastic waste. Once sorted, the plastic is shredded into small flakes, which are then cleaned to remove any contaminants. These plastic flakes are the raw material for the recycling process.
The next step is melting, a crucial phase in the recycling journey. Plastic flakes are fed into a large industrial furnace or melting machine, where they are subjected to high temperatures. The specific temperature varies depending on the type of plastic being processed. For example, PET (polyethylene terephthalate), commonly used in beverage bottles, requires a temperature of around 250-270°C (482-518°F) to melt. On the other hand, HDPE (high-density polyethylene), often found in milk jugs, melts at a slightly lower temperature of about 180-220°C (356-428°F).
During the melting process, the plastic flakes undergo a transformation. As they are heated, the molecular bonds within the plastic break down, allowing the material to flow and take on a molten state. This molten plastic is then carefully controlled in terms of temperature and viscosity to ensure it can be processed effectively. The molten state is a critical stage as it prepares the plastic for the next steps in the recycling process, such as molding or extrusion.
Once melted, the plastic is often mixed with other additives to enhance its properties. These additives can include colorants, stabilizers, and fillers, which are blended into the molten plastic to create a consistent and desirable material for manufacturing new products. This step is essential to ensure the recycled plastic meets the required standards and can be used in various applications.
After melting and adding any necessary additives, the plastic is ready for the next phase of recycling. It can be extruded into new shapes, such as pellets or sheets, which can then be used to create new plastic products. This continuous process of melting, adding, and reshaping allows for the efficient recycling of plastic, reducing waste and promoting a more sustainable approach to material usage.
Recycling Plastics: Effective Methods for a Greener Future
You may want to see also
Molding: Molten plastic is shaped into new products
The process of molding is a crucial step in the recycling and transformation of plastic waste into new products. It involves the use of heat and pressure to shape molten plastic into the desired form, which can then be used to create a wide range of items. This method is particularly useful for producing complex shapes and structures that are challenging to achieve through other recycling techniques.
When plastic is ready for molding, it is typically in the form of small pellets or flakes, which are the result of collecting and sorting plastic waste. These raw materials are then fed into a machine called an extruder, which applies heat and pressure to melt the plastic. The extruder's role is to ensure that the plastic is thoroughly heated and mixed, creating a homogeneous molten mass. This process is carefully controlled to maintain the desired temperature and consistency, as it directly impacts the quality of the final product.
Once the plastic is molten, it is transferred to a molding machine, also known as an injection molder. This machine is equipped with a heated chamber and a plunger system. The molten plastic is injected into the chamber under high pressure, where it is then shaped by the mold. The mold is a critical component, as it defines the shape and structure of the final product. It is designed with specific cavities and contours to create the desired item, whether it's a car part, furniture, or packaging material.
During the molding process, the plastic is cooled and solidified as it comes into contact with the mold's surfaces. This cooling process is rapid and precise, ensuring that the plastic retains its new shape. Once cooled, the molded plastic part is removed from the mold and can be further processed or used directly. The molding process allows for the creation of intricate designs and precise specifications, making it ideal for manufacturing a vast array of products.
Molding offers several advantages in plastic recycling. It enables the production of high-quality, consistent products with minimal defects. This method is highly versatile, accommodating various plastic types and colors. Additionally, molding can be used to recycle a wide range of plastic waste, including post-consumer and post-industrial materials. The process can transform plastic scraps, bottles, and even complex electronic components into new, valuable products, contributing to a more sustainable and circular economy.
Medical Plastics and Desiccants: Unraveling the Recycling Mystery
You may want to see also
Testing: Recycled plastic is inspected for quality and purity
The process of recycling plastic involves a series of steps to ensure the material is of sufficient quality and purity for reuse. Once the plastic waste is collected, sorted, and prepared, it undergoes rigorous testing to meet the required standards. This testing phase is crucial to guarantee the recycled plastic's performance and safety in various applications.
One of the primary methods of inspection is visual examination. Trained personnel carefully analyze the recycled plastic for any visible defects, contaminants, or foreign materials. This visual assessment helps identify items like glass, metal, or other plastics that might have been mistakenly included in the collection. By removing these impurities, the recycled material can be ensured to be free from potential hazards and maintain its integrity.
In addition to visual inspection, advanced laboratory testing is employed to measure the plastic's properties. This includes assessing its melt flow index, which indicates the ease of processing the plastic. A higher melt flow index suggests a more fluid material, making it easier to mold and shape during manufacturing. Other tests might involve checking the plastic's density, color, and chemical composition to ensure it meets specific requirements. For instance, the recycled plastic should be free from heavy metals and other toxic substances, which can be determined through various analytical techniques.
The testing process also involves evaluating the plastic's performance in terms of its mechanical and physical characteristics. This includes testing its strength, flexibility, and durability. By subjecting the recycled plastic to simulated real-world conditions, engineers can assess its suitability for different applications. For example, it might be tested for its ability to withstand temperature changes, impact resistance, or its performance in various environmental conditions.
Furthermore, the testing procedures for recycled plastic often include a quality control check to ensure consistency. This involves comparing the properties of the recycled material with the original specifications and standards. Any deviations or inconsistencies are noted and addressed to maintain the high quality expected from recycled plastics. This comprehensive testing approach ensures that the final product meets the necessary criteria, providing a reliable and sustainable alternative to virgin plastic materials.
Milk Carton Recycling: Paper or Plastic? Unraveling the Mystery
You may want to see also
Frequently asked questions
Plastic recycling involves several steps to transform used plastic items into new products. It typically starts with collecting and sorting plastic waste, which is then cleaned and shredded into small pieces called flakes. These flakes are further processed to remove contaminants, and then they are melted and molded into new shapes to create recycled-content products.
Identifying plastic types is crucial for effective recycling. Common methods include checking the resin identification code (a number inside a triangle on the bottom of the item) and using visual inspection. For example, PET (polyethylene terephthalate) is often used for beverage bottles, while HDPE (high-density polyethylene) is commonly found in milk jugs. Proper sorting ensures that plastics are recycled appropriately.
Plastic recycling faces several challenges. One major issue is contamination, where non-plastic materials or food residue mix with plastic waste, making it harder to process. Additionally, not all plastics are recyclable, and some types have lower recycling rates due to technical limitations. The complexity of plastic compositions and the lack of standardized recycling systems also pose challenges in the recycling process.
You can play a significant role in plastic recycling by following these simple steps. First, familiarize yourself with local recycling guidelines to understand what types of plastics are accepted. Then, ensure proper sorting of plastic waste at home, using separate containers for different plastic types. Rinse containers to remove residue, and flatten them to save space. Finally, place your sorted and cleaned plastics in the appropriate recycling bin for collection.
Absolutely! The field of plastic recycling is constantly evolving, and several innovations aim to improve the efficiency and effectiveness of the process. Advanced chemical recycling techniques can break down plastics into their original building blocks, allowing for the creation of new materials. Additionally, researchers are exploring ways to recycle mixed plastic waste, develop biodegradable alternatives, and enhance recycling infrastructure to handle larger volumes of plastic waste.