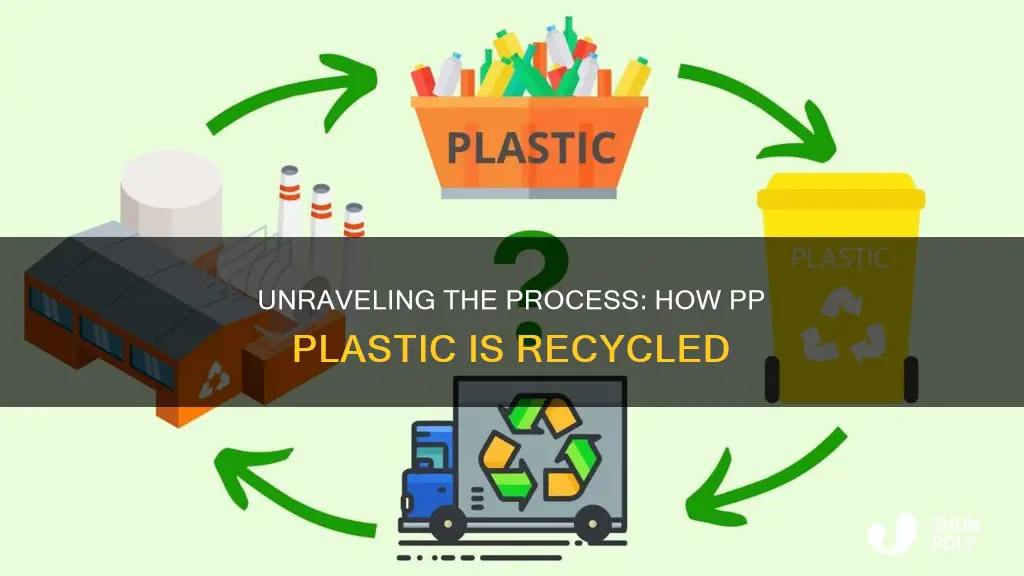
Plastic recycling is a crucial process in managing plastic waste and reducing environmental impact. One common method of recycling is the process of PP (Polypropylene) plastic recycling. PP is a versatile and widely used plastic, known for its durability and resistance to heat and chemicals. The recycling process for PP involves several steps: collection and sorting of PP waste, cleaning and shredding the plastic, and then processing it through a process called repelletizing. This process involves melting the shredded PP, removing any contaminants, and then reforming it into new pellets that can be used to create new products. Understanding the specific methods and challenges of PP recycling is essential for developing effective recycling practices and promoting a circular economy for this important plastic material.
What You'll Learn
- Collection: Plastic waste is gathered from various sources, including recycling bins and collection centers
- Sorting: Materials are sorted by type (PET, HDPE, etc.) using advanced machinery
- Cleaning: Contaminants are removed to ensure high-quality recycled plastic
- Shredding: Plastic is shredded into small pieces for further processing
- Melting and Molding: The shredded plastic is melted and molded into new products
Collection: Plastic waste is gathered from various sources, including recycling bins and collection centers
The first step in the process of recycling PP (Polypropylene) plastic is the collection of plastic waste. This initial phase is crucial as it sets the foundation for the entire recycling journey. Plastic waste is gathered from various sources, including recycling bins and collection centers, which are strategically placed in public areas, residential neighborhoods, and commercial premises. These collection points are designed to be easily accessible to the public, encouraging participation and ensuring a steady supply of plastic waste for recycling.
Recycling bins, often color-coded to indicate the type of plastic they accept, play a vital role in this process. They are placed in high-traffic areas such as offices, schools, and public spaces, making it convenient for individuals to dispose of their plastic waste responsibly. Collection centers, on the other hand, are typically larger facilities where plastic waste is brought by trucks or other vehicles. These centers are often managed by local governments or private recycling companies and serve as a central hub for the collection and sorting of plastic materials.
The collection process involves a systematic approach to ensure that PP plastic waste is separated from other types of plastics and general waste. This separation is crucial because PP plastic has specific properties and uses, and it needs to be recycled accordingly. For instance, PP is commonly used in food containers, bottle caps, and packaging materials, so it is essential to collect these items separately to maintain the quality of the recycled material.
When plastic waste is collected, it is often sorted by type and color to facilitate the recycling process. This sorting can be done manually or through automated systems, where machines separate the plastics based on their characteristics. The goal is to create a clean and consistent feed of PP plastic for recycling, ensuring that the final product meets the required standards.
In summary, the collection phase is a critical step in PP plastic recycling, as it involves gathering waste from various sources and ensuring proper segregation. By making recycling bins and collection centers easily accessible, individuals and organizations can actively contribute to the recycling process, ultimately reducing the environmental impact of plastic waste. This initial step sets the stage for the subsequent stages of recycling, where PP plastic can be transformed into new products, promoting a more sustainable approach to waste management.
Unveiling Oakland's Plastic Recycling Mystery: Does It Work?
You may want to see also
Sorting: Materials are sorted by type (PET, HDPE, etc.) using advanced machinery
The process of recycling PP (Polypropylene) plastic begins with the careful sorting of materials, a crucial step that ensures the efficiency and effectiveness of the recycling process. Advanced machinery plays a pivotal role in this stage, employing sophisticated techniques to separate different types of plastics. This meticulous sorting is essential to maintain the quality of the recycled material and to prepare it for its new life.
Modern recycling facilities utilize a variety of methods to categorize plastics. One common approach is the use of near-infrared (NIR) spectroscopy, a technology that can identify the type of plastic based on its unique infrared signature. This method is highly accurate and can distinguish between various plastic types, including PET (Polyethylene Terephthalate), HDPE (High-Density Polyethylene), and PP. The machinery is equipped with sensors that scan the incoming plastic waste, allowing for rapid and precise identification.
Once sorted, the plastics are further processed to ensure they are clean and free from contaminants. This involves removing any non-plastic materials, such as labels, caps, and other debris, which can compromise the quality of the recycled product. Advanced sorting machinery often includes optical sorters that can detect and separate different colors and types of plastics, ensuring a more comprehensive separation.
The sorted and cleaned plastics are then bunched and prepared for the next stage of recycling. Each type of plastic has specific properties and applications, so maintaining its purity is vital. For instance, PP is commonly used in food containers and packaging, so ensuring it is free from other plastics that might affect its performance is critical. The advanced machinery facilitates this process, making it an efficient and reliable part of the recycling workflow.
In summary, the initial step of sorting plastics by type using advanced machinery is a fundamental and indispensable part of PP plastic recycling. It sets the foundation for the entire recycling process, ensuring that the final product meets the required standards and can be utilized in various industries, contributing to a more sustainable and circular economy. This methodical approach showcases the sophistication and precision required in modern recycling practices.
Whole Foods Recycling: Unraveling Plastic Packing Policies
You may want to see also
Cleaning: Contaminants are removed to ensure high-quality recycled plastic
The process of recycling PP (polypropylene) plastic begins with the collection and sorting of used plastic items. These items are then cleaned to remove any contaminants, ensuring the quality of the recycled material. Cleaning is a crucial step as it helps to eliminate any impurities that could compromise the strength and durability of the recycled plastic.
One common method for cleaning PP plastic is through the use of washing machines or industrial-scale washing systems. These machines are designed to separate the plastic from any non-plastic materials, such as labels, caps, or other contaminants. The plastic items are fed into the washing machine, where they are agitated and cleaned with hot water and detergents. This process helps to break down any residual materials and ensures that the plastic is free from dirt, grease, and other impurities.
After the initial cleaning, the plastic may undergo additional processes to further refine the material. This can include air drying, where the cleaned plastic is exposed to a controlled environment to remove any remaining moisture. It is also possible to use specialized chemicals to dissolve and remove any stubborn contaminants. These chemicals are carefully selected to ensure they do not damage the plastic structure.
Once the cleaning process is complete, the PP plastic is ready for the next stage of recycling. It is often shredded or granulated to create small, uniform pieces of plastic. These pieces can then be used as raw materials for manufacturing new products, such as containers, packaging, or even new plastic items. The cleaning step is vital to achieving a high-quality recycled product, as it ensures that the final material meets the required standards and can be used in various applications without compromising performance.
In summary, cleaning is an essential part of the PP plastic recycling process, as it removes contaminants and ensures the material's quality. Through the use of washing machines and additional refining processes, the plastic is prepared for reuse, contributing to a more sustainable and circular economy. Proper cleaning techniques help to maintain the integrity of the recycled plastic, making it a valuable resource in the production of new goods.
Nevada's Plastic Recycling: A Green Revolution or a Misstep?
You may want to see also
Shredding: Plastic is shredded into small pieces for further processing
The process of recycling PP (Polypropylene) plastic begins with the collection of used PP products, such as packaging, containers, or textiles. These items are then sorted to ensure they are free from contaminants and suitable for recycling. Once sorted, the PP plastic is prepared for the shredding stage, which is a crucial step in the recycling process.
Shredding is a mechanical process where the plastic is reduced to small, uniform pieces. This is typically done using specialized machinery designed for plastic shredding. The shredding process aims to break down the plastic into a manageable size, making it easier to handle and process further. The shredded plastic is often referred to as 'shred' or 'flakes'. These small pieces are crucial as they provide a consistent feedstock for the subsequent recycling stages.
The shredding process involves feeding the PP plastic into the shredder, where it is cut and broken down. The machinery can vary, but it often includes a combination of cutting blades and rotating drums to ensure the plastic is shredded effectively. The goal is to create a consistent particle size, typically ranging from a few millimeters to a few centimeters, depending on the desired application. This size reduction is essential to ensure the plastic can be processed further without causing issues in the recycling stream.
After shredding, the plastic flakes are often cleaned to remove any remaining contaminants. This step is vital to maintain the quality of the recycled material. Cleaning processes may include washing, drying, and sometimes even magnetic separation to remove any metal or other foreign particles. The cleaned plastic flakes are then ready for the next stage of recycling, where they can be transformed into new products or used as raw material for manufacturing.
This initial shredding step is a critical phase in the recycling journey, as it sets the foundation for the subsequent processes. The shredded plastic's size and consistency are key factors in determining the success of the recycling process and the final quality of the recycled PP material. Proper shredding ensures that the plastic can be effectively sorted, processed, and transformed into new products, contributing to a sustainable circular economy.
Recycling Plastic: A Climate Change Solution or a Myth?
You may want to see also
Melting and Molding: The shredded plastic is melted and molded into new products
The process of recycling PP (polypropylene) plastic involves several stages, and one of the key methods is indeed melting and molding. This technique is a crucial step in transforming shredded plastic waste into new, usable products. Here's a detailed breakdown of this process:
Once the PP plastic has been collected, sorted, and cleaned, it is shredded into small pieces. These shredded pieces, often referred to as 'flakes' or 'granules', are then prepared for the melting process. The shredded plastic is fed into a specialized machine, typically a plastic granulator or a shredding machine, which further reduces the plastic into even smaller particles. This step ensures that the plastic is in a consistent and manageable form for the subsequent stages.
The next step is the melting process, which requires specialized equipment. The shredded PP plastic is heated to its melting point in a machine called an extruder. This machine applies heat and pressure to the plastic, softening it and transforming it into a molten state. The temperature and duration of this process are carefully controlled to ensure the plastic's quality and integrity. The molten plastic is then conveyed through a system, often a conveyor belt or a screw conveyor, to a molding area.
In the molding stage, the molten PP plastic is shaped into new products. This is achieved through a process called injection molding, which is commonly used in the plastic manufacturing industry. The molten plastic is injected under high pressure into a mold, which gives it the desired shape. The mold is typically made of metal and designed with the specific product in mind. Once the plastic solidifies within the mold, it is removed, and the process can be repeated to create multiple products. This method allows for the creation of a wide range of items, from packaging materials to automotive parts.
After molding, the final products are cooled and solidified. The cooling process is crucial to ensure the stability and strength of the new products. Once cooled, the molded parts are removed from the mold and can be further processed or packaged for distribution. This entire process, from shredding to molding, showcases the transformation of waste plastic into valuable, reusable materials, contributing to a more sustainable approach to plastic recycling.
Norway's Plastic Recycling: A Global Leader's Success Story
You may want to see also
Frequently asked questions
PP (Polypropylene) is a widely used plastic material known for its versatility and strength. Recycling PP involves several steps. First, the plastic waste is collected and sorted to ensure it is free from contaminants. Then, it is shredded or granulated to reduce its size. The shredded PP is cleaned to remove any remaining impurities, and then it undergoes a process called "recycling," where it is melted and reformed into new products. This process can be done through various methods, including injection molding, blow molding, or extrusion, depending on the desired end product.
Collecting PP plastic waste is an essential step in the recycling process. It typically begins with the proper disposal of used PP products, such as packaging, containers, and household items. Many recycling programs encourage the separation of plastics by type, so PP waste is often collected separately from other plastics. This can be done through curbside recycling programs, drop-off centers, or specialized collection events. Proper collection ensures that the PP waste is of good quality and can be efficiently recycled.
Recycled PP has numerous applications and can be transformed into various products. One common use is in the manufacturing of new packaging materials, such as containers, bottles, and food containers. It is also used in the production of textiles, including clothing, carpets, and automotive interior components. Recycled PP can be blended with other plastics to enhance its properties, making it suitable for a wide range of industrial and consumer products. Additionally, it can be utilized in construction materials, electronics, and even in the creation of 3D printing filaments.
While PP recycling is an important process, it does come with certain challenges. One issue is the potential for contamination, as PP is often mixed with other plastics or materials during its lifecycle. Proper sorting and cleaning are crucial to address this. Another challenge is the availability and consistency of PP waste. Some regions may have limited access to PP recycling facilities or face difficulties in collecting sufficient amounts of PP waste. Additionally, the recycling process itself can be energy-intensive, and the end products might not always match the quality of virgin PP, leading to potential performance limitations in certain applications.