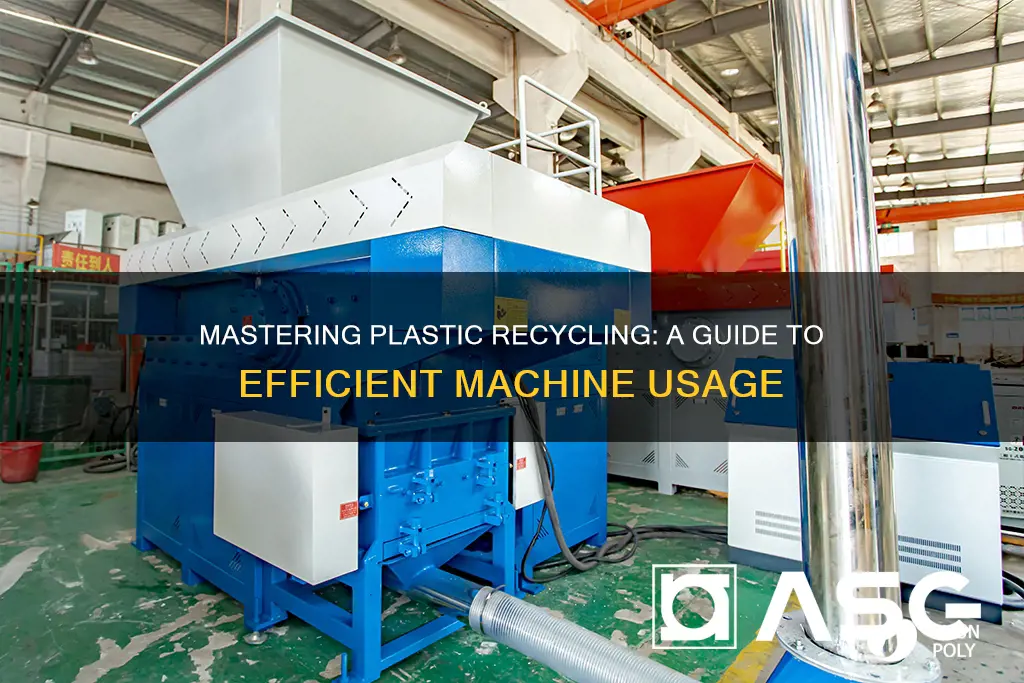
Recycling plastic is an essential process to reduce environmental impact and promote sustainability. Plastic recycling machines play a crucial role in this process by efficiently sorting, cleaning, and processing plastic waste. These machines are designed to handle various types of plastic materials, ensuring that they can be transformed into new products. Understanding how to operate and maintain these machines is vital for anyone involved in the recycling industry, as it directly impacts the quality and efficiency of the recycling process. This guide will provide an overview of the key steps and considerations involved in utilizing plastic recycling machines effectively.
What You'll Learn
- Collection: Gather plastic waste from various sources for recycling
- Sorting: Separate plastics by type and color for efficient processing
- Cleaning: Remove contaminants like labels and food residue
- Shredding: Break down plastic into small pieces for easier processing
- Melting: Heat and melt plastic to create new products
Collection: Gather plastic waste from various sources for recycling
The first step in the process of recycling plastic is collection, which involves gathering plastic waste from various sources to ensure a steady supply of raw materials for the recycling machine. This initial phase is crucial as it sets the foundation for the entire recycling process. Here's a detailed guide on how to effectively collect plastic waste:
Identify Sources: Begin by identifying potential sources of plastic waste. These can include residential areas, commercial establishments, industrial sites, and public spaces. For instance, you might collect plastic bottles, containers, packaging materials, and other plastic items from households, supermarkets, factories, and street bins. Understanding the types of plastic used in these sources is also essential, as different plastics have varying recycling requirements.
Implement Collection Systems: Develop a structured collection system to ensure a continuous supply of plastic waste. This could involve setting up designated collection points or bins in residential areas, offices, schools, and public spaces. Clearly label these bins to indicate what types of plastic they accept, such as PET bottles, HDPE containers, or clear plastic packaging. Providing separate bins for different types of plastics helps maintain the quality of the recycled material.
Engage the Community: Encourage community participation in the recycling process. Educate residents, businesses, and organizations about the importance of proper waste segregation and the benefits of recycling. You can organize awareness campaigns, workshops, or training sessions to teach people how to identify and collect recyclable plastics. By involving the community, you can create a sustainable system where everyone contributes to the collection process.
Collaborate with Waste Management Companies: Partnering with waste management companies or local authorities can significantly enhance the collection process. These organizations often have the infrastructure and expertise to collect and transport large volumes of waste. They can provide specialized collection vehicles and ensure that the plastic waste is handled and sorted efficiently. Collaborating with waste management professionals can also help in implementing a more comprehensive recycling program.
Sort and Separate: Once the plastic waste is collected, proper sorting and separation are essential. This step ensures that different types of plastics are not contaminated, which is crucial for maintaining the quality of the recycled material. Sort the collected plastics into categories such as PET (polyethylene terephthalate), HDPE (high-density polyethylene), PVC (polyvinyl chloride), and others. Each type of plastic has specific recycling processes and applications. Proper sorting also prevents contamination, which can lead to lower-quality recycled products.
By following these steps, you can establish an efficient collection system for plastic waste, ensuring a steady supply of raw materials for the recycling machine and contributing to a more sustainable approach to plastic recycling.
Unraveling the Mystery: Can Plastic Totes Be Recycled?
You may want to see also
Sorting: Separate plastics by type and color for efficient processing
The process of recycling plastic begins with meticulous sorting, a crucial step to ensure efficient and effective recycling. This initial phase involves categorizing plastic materials based on their type and color, which is essential for optimizing the recycling machine's performance. By separating plastics, you create a more streamlined system, allowing for better material recovery and reducing contamination.
When sorting plastics, it is imperative to identify the different types of polymers present. Common types include PET (polyethylene terephthalate), HDPE (high-density polyethylene), LDPE (low-density polyethylene), and PVC (polyvinyl chloride). Each type has unique properties and applications, and proper identification ensures that they are recycled accordingly. For instance, PET is widely used in beverage bottles and can be recycled into fibers for clothing or new containers. HDPE, often found in milk jugs, can be recycled into various products like outdoor furniture or composite wood.
Color separation is another critical aspect of this process. Plastic items can vary in color due to additives or dyes, and this variation needs to be considered. Recycling machines often have specific requirements for color acceptance, and separating plastics by color ensures that the machine can process them efficiently. For example, clear PET bottles are highly desirable for recycling as they can be used to produce new containers, while colored PET may have limited applications and should be sorted accordingly.
To facilitate this sorting process, it is beneficial to have a well-organized system. This could involve using different bins or containers labeled with the specific plastic type and color. For instance, have a bin for clear PET bottles, another for blue HDPE containers, and so on. This organized approach makes it easier for workers to identify and separate the plastics, reducing the chances of errors.
In addition to manual sorting, some facilities employ automated systems to enhance efficiency. These machines use sensors and algorithms to identify and separate plastics based on their type and color. Automated sorting can significantly increase the speed and accuracy of the process, ensuring that the right plastics are directed to the appropriate recycling streams. This technology is particularly useful for high-volume recycling operations.
Ottawa's Plastic Utensil Recycling: What You Need to Know
You may want to see also
Cleaning: Remove contaminants like labels and food residue
When preparing plastic for recycling, it's crucial to clean it thoroughly to ensure the process is effective and the final product is of high quality. One of the primary steps in this cleaning process is removing contaminants such as labels and food residue. These items can significantly impact the recycling process and the end product's quality.
Labels, often made of paper or a paper-like material, can be challenging to remove from plastic containers. They are typically glued to the plastic and can leave behind a sticky residue or even small paper fibers. To address this, you can start by gently peeling the label off the plastic. If the label is stubborn and doesn't come off easily, you might need to use a small tool, like a flathead screwdriver, to carefully pry it off. Be cautious not to scratch the plastic surface during this process. Once the label is removed, rinse the plastic container under running water to wash away any remaining glue or paper fibers.
Food residue, such as leftover food particles or liquid, can also be a significant issue. These residues can attract bacteria and mold, leading to unpleasant odors and potential health hazards. To clean plastic containers with food residue, start by rinsing them under warm water. This initial rinse helps to loosen and remove any loose particles. Next, use a mild detergent or dish soap and a soft brush or sponge to scrub the interior of the container. Pay attention to any nooks and crannies where food might have accumulated. After scrubbing, rinse the container thoroughly again to ensure all soap residue is removed.
For particularly stubborn food residues, you might need to use a small amount of vinegar or a specialized plastic cleaner. These can help break down the residue and make it easier to remove. Always ensure that the plastic container is completely dry before proceeding to the next step in the recycling process. Moisture can lead to mold growth and other issues, so proper drying is essential.
In summary, cleaning plastic containers for recycling involves a careful process of removing labels and food residue. This includes gentle label removal, thorough rinsing, and, in some cases, scrubbing with mild detergents. Proper cleaning ensures that the plastic is free from contaminants, ready for the recycling machine, and contributes to the production of high-quality recycled materials.
Unraveling the Mystery: Can Plastic Films Be Recycled?
You may want to see also
Shredding: Break down plastic into small pieces for easier processing
Shredding is a crucial step in the recycling process of plastic, as it involves breaking down plastic materials into smaller, more manageable pieces. This process is essential for several reasons. Firstly, it increases the surface area of the plastic, exposing more material to potential recycling processes. Smaller pieces also make it easier to handle and transport the plastic, especially when dealing with large volumes. Moreover, shredding can help remove contaminants and impurities, ensuring that the recycled plastic is of higher quality and more valuable in the market.
The shredding process typically begins with the collection of plastic waste, which can come from various sources such as household recycling bins, industrial waste streams, or dedicated plastic collection points. Once collected, the plastic is sorted by type to ensure that it can be shredded effectively. Different types of plastic have varying properties and melting points, so using the right shredding technique for each type is essential. For instance, high-density polyethylene (HDPE) and low-density polyethylene (LDPE) are commonly shredded using different methods due to their distinct characteristics.
There are several methods and machines available for shredding plastic. One common approach is using a shredding machine, which can be either a manual or automatic device. Manual shredders often involve feeding plastic into a rotating drum or blade, which then cuts and reduces the plastic to smaller pieces. These machines are typically smaller and more affordable, making them suitable for small-scale recycling operations or local communities. Automatic shredders, on the other hand, are more complex and can handle larger volumes of plastic waste. They often use multiple blades or rotating drums to ensure efficient shredding and can be integrated into larger recycling systems.
Another shredding technique is the use of granulators, which are designed to produce very fine plastic flakes or granules. Granulators work by feeding plastic into a high-speed rotating blade, which cuts the material into tiny pieces. This process is particularly useful for creating a consistent and uniform product, which is often preferred in the manufacturing of new plastic items. Granulators can be either single-shaft or double-shaft, with the latter being more efficient for certain types of plastic.
In addition to the machines, the shredding process also requires careful consideration of safety and environmental factors. Proper ventilation is essential to manage the release of plastic dust and fumes, which can be harmful if inhaled. Additionally, the shredded plastic should be stored in a dry and controlled environment to prevent contamination and maintain its quality. By following these steps and utilizing the appropriate shredding techniques, the recycling process can be optimized, leading to a more efficient and sustainable approach to managing plastic waste.
Unraveling the Mystery: Can All Plastics Be Recycled?
You may want to see also
Melting: Heat and melt plastic to create new products
The process of melting plastic is a crucial step in recycling and creating new products from used plastic materials. This method involves heating the plastic to a specific temperature, allowing it to become malleable and then shaping it into new forms. Here's a detailed guide on how to melt plastic using a machine:
Machine Preparation: Begin by ensuring you have the right equipment. A plastic recycling machine, often referred to as a plastic extruder or meltzer, is essential. These machines are designed to heat and melt plastic efficiently. The machine should have a heating element capable of reaching temperatures suitable for the type of plastic you are working with. It's important to set the temperature according to the specific plastic's melting point to avoid damage. Additionally, a cooling system is necessary to solidify the melted plastic and prepare it for further processing.
Plastic Preparation: Collect and sort your plastic waste. Different types of plastics have varying melting points and properties. Common plastics used in recycling include PET (polyethylene terephthalate), HDPE (high-density polyethylene), and PVC (polyvinyl chloride). Clean and prepare the plastic by removing any contaminants, labels, or non-plastic components. This step ensures the purity of the recycled material. Cut or shred the plastic into small pieces to increase the surface area, making it easier for the machine to process.
Melting Process: Place the prepared plastic pieces into the recycling machine. The machine will heat the plastic, typically using a combination of a heating cylinder and a heating element. The temperature and duration of heating depend on the type of plastic. For example, PET melts at around 230°C (446°F), while HDPE requires a lower temperature of about 120-150°C (248-302°F). Monitor the temperature carefully to avoid overheating, which can lead to plastic degradation. As the plastic melts, it becomes a viscous liquid, often referred to as 'melted plastic' or 'plastic resin'.
Extrusion and Shaping: Once the plastic is melted, the machine will typically extrude it through a die or a shaping tool. This step allows you to create specific forms or products. For instance, you can shape it into pellets, flakes, or even custom-designed objects. The extrusion process requires precise control over temperature and pressure to ensure the plastic takes the desired shape. After extrusion, the molten plastic is cooled rapidly, solidifying it into a new product ready for further use or sale.
Safety and Maintenance: Melting plastic involves high temperatures and potential hazards. Always follow safety protocols and wear appropriate protective gear when operating the machine. Regular maintenance of the recycling machine is crucial to ensure optimal performance and longevity. Clean and lubricate the machine's components as per the manufacturer's guidelines to prevent overheating and mechanical issues.
Unraveling the Mystery: Can Plastic Glasses Be Recycled?
You may want to see also
Frequently asked questions
Recycling plastic involves a series of steps to transform used plastic items into new products. The process typically begins with collecting and sorting plastic waste, which is then cleaned and shredded into small pieces. These pieces are melted and molded into new shapes, creating a raw material known as "pellets" or "nurdles." These pellets can be used to manufacture various products like furniture, toys, and even new plastic containers.
Before recycling, ensure that the plastic items are clean and dry. Remove any non-plastic components like caps, labels, or metal parts. Rinse the plastic containers to eliminate food residue or liquids. Flatten or break down large items to save space and make the recycling process more efficient. It's also essential to check with your local recycling center for specific guidelines on accepted plastic types.
Not all plastics are recyclable in the same way. Common recyclable plastics include PET (polyethylene terephthalate), found in beverage bottles, and HDPE (high-density polyethylene), used for milk jugs and some containers. Other types like PVC, LDPE, and PP have their own recycling streams. It's crucial to check the recycling symbol on the plastic item and look for the corresponding recycling number to ensure it is recyclable in your area.
Plastic recycling machines offer several advantages. They automate the recycling process, making it more efficient and consistent. These machines can handle large volumes of plastic waste, reducing the time and effort required for manual sorting. Additionally, they can produce high-quality recycled materials, which can be used in various industries, promoting a circular economy and reducing the demand for virgin plastic production.
When searching for a plastic recycling machine, consider factors like the type of plastic you want to recycle, the desired output, and your budget. Research different manufacturers and suppliers who offer machines tailored to your specific requirements. Look for machines with good reviews and certifications to ensure they meet industry standards. You may also want to explore rental or leasing options if you're not ready for a permanent investment.