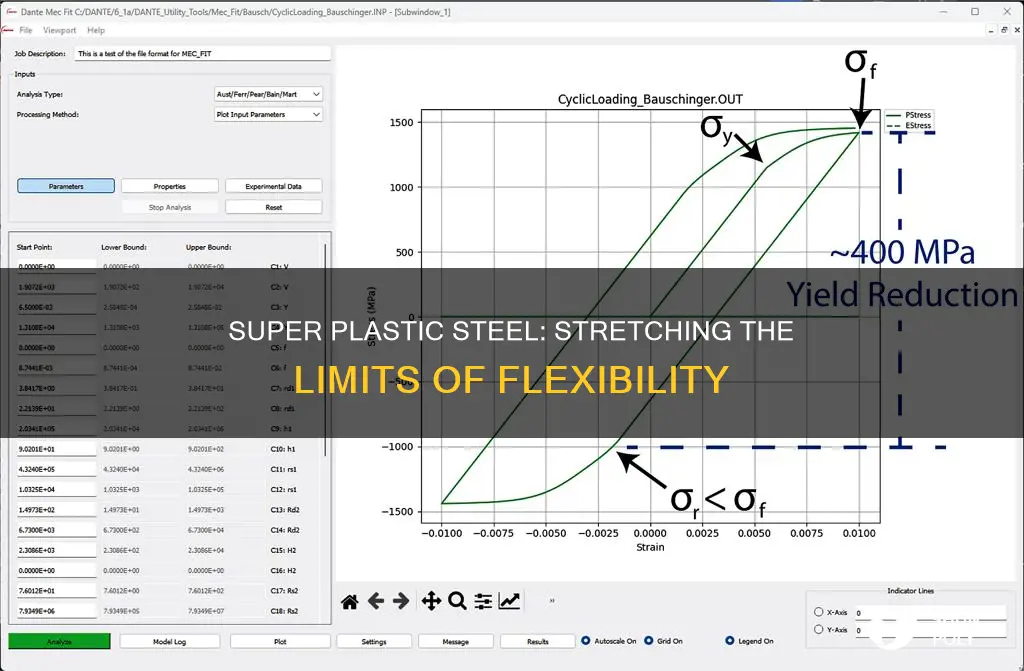
Superplastic metals can stretch by more than 200% under physical stress, and some can stretch even further. They are used in industries such as automotive and aerospace, where they are used to make strong, lightweight parts. Superplasticity is achieved at high temperatures, typically one-half of the metal's absolute melting temperature. For example, titanium is superplastic at about 900 °C and aluminium at 450–520 °C.
Characteristics | Values |
---|---|
Temperature | Metals become superplastic at high temperatures, typically one-half of their absolute melting temperature. For example, titanium is superplastic at about 900 °C and aluminium at 450–520 °C. |
Elongation | Superplastic solids can elongate under physical stress by more than 200%, and some stretch far more. |
Applications | Superplastic metals are used in the automotive industry, for example, to make strong, lightweight parts. They are also used to make biomedical gear such as prosthetics or braces. |
What You'll Learn
- Superplastic metals can stretch to a new low
- Titanium, aluminium, nickel-based alloys and stainless steels exhibit superplasticity
- Superplastic metals can be used to make strong, lightweight biomedical gear
- Superplasticity occurs at high temperatures
- Superplastic solids can elongate under physical stress by more than 200%
Superplastic metals can stretch to a new low
Superplastic metals can stretch to several times their original size without failure when heated to high temperatures. For example, superplastically formed (SPF) aluminium alloys can be stretched to several times their original size when heated to between 470 and 520 °C.
Metals become superplastic at high temperatures, typically one-half of their absolute melting temperature. For example, titanium is superplastic at about 900 °C and aluminium at 450–520 °C. The superplastic metal is soft and ductile at a temperature high enough to allow it to plastically stretch over large strains without tearing or breaking. The mechanism of superplasticity relies on the sliding of grains past each other in a creep-type deformation process together with atomic diffusion processes within the crystal structure that aid plastic flow.
Superplastic forming is a net-shape processing technology that dramatically decreases fabrication and assembly costs by reducing the number of parts and the assembly requirements. Using SPF technology, it was anticipated that a 50% manufacturing cost reduction can be achieved for many aircraft assemblies, such as the nose cone and nose barrel assemblies. The most common process for superplastic forming of sheet material is a blow-forming process similar to that used for thermoplastic polymer foils and sheets. The superplastic sheet is placed between two heated tool halves and tightly clamped between them along its outer perimeter by some mechanical device, usually a hydraulic press. Then the gas pressure on the upper side of the sheet is slowly increased. The sheet starts to stretch and slowly forms down into the tool cavity on the pressure-free side. The geometry of this lower tool cavity defines the geometry of the final part.
Superplasticity often occurs at a slow strain rate, in the order of 10−4 s−1, and can be energy-consuming. In addition, prolonged time exposed to high-operation temperature also degraded the mechanical properties of materials. There is a strong demand to increase the strain rate in superplastic deformation to the order of 10−2 s−1, called High Strain Rate Superplasticity (HSRS).
The Cost of Plastic Bags: Environmental and Monetary
You may want to see also
Titanium, aluminium, nickel-based alloys and stainless steels exhibit superplasticity
Superplasticity is a phenomenon indicating exceptional ductility that certain metals and alloys exhibit when deformed under specific conditions. Superplastic solids can elongate under physical stress by more than 200%, and some stretch far more.
Superplastic aluminium alloys are used in the automobile sector to reduce weight and minimise fuel consumption. They are used to fabricate automobile body panels and can be heated and stretched into close contact with complex die shapes to develop near-net end products such as electronics casings, automotive body panels, vehicle and transit fixtures, and more.
Superplastic metals are also used to make strong but lightweight biomedical gear such as prosthetics or braces.
Plastic's Climate Impact: Understanding the Devastating Contribution
You may want to see also
Superplastic metals can be used to make strong, lightweight biomedical gear
Superplastic metals can be stretched to a much greater degree than everyday solids without breaking. They can elongate under physical stress by more than 200%, and some stretch even further. This makes them ideal for creating strong, lightweight biomedical gear.
Superplastic metals are soft and ductile at high temperatures, which allows them to be stretched over large strains without tearing. They are used in the automotive industry to create thin yet strong metal parts. For example, Lamborghini uses superplastic metals to make car parts.
Superplastic metals can also be used to create strong, lightweight biomedical gear such as prosthetics or braces. This is because they provide exceptional strength at ambient temperature.
Various titanium, aluminium, and nickel-based alloys, as well as some stainless steels, exhibit superplasticity and are prime candidates for superplastic forming processes. For example, aluminium alloys can be deformed superplastically across a temperature range of 470-520°C and a pressure range of approximately 350-1500 kPa. This enables aluminium sheets to be heated and stretched into complex die shapes, making them ideal for creating lightweight biomedical gear.
Plastic Pallet Weight: How Much Do They Weigh?
You may want to see also
Superplasticity occurs at high temperatures
Superplastic metals can stretch by more than 200% without breaking. This makes them ideal for engineers to use when building metal parts that are thin yet strong.
Many aluminium alloys, for example, will deform superplastically across a temperature range of 470–520°C (878–968°F) and a broad pressure range of approximately 350—1500 kPa. This enables aluminium sheets to be heated and stretched into close contact with complex die shapes to develop near-net end products such as electronics casings, automotive body panels, vehicle and transit fixtures, and more.
Scientists have found that superplasticity can occur at temperatures hundreds of degrees lower than expected. This is good news for manufacturers, such as car makers, who are interested in making strong, lightweight parts from these stretchy metals.
The Plastic We Eat: A Startling Truth
You may want to see also
Superplastic solids can elongate under physical stress by more than 200%
Scientists at MIT have developed a new form of superplastic called 2DPA-1, which is two times stronger than steel under load tests, with just one-sixth the material bulk. This material has the potential to revolutionise the way we build everything from gadgets to buildings.
The development of superplastics with increased strength and flexibility offers exciting possibilities for a wide range of applications, from electronics to construction. By understanding and manipulating the molecular structure of plastics, scientists are creating materials with enhanced properties that can meet the diverse needs of modern technology and infrastructure.
While the exact elongation capacity of superplastics may vary depending on their specific composition and manufacturing process, their ability to stretch beyond 200% underscores their remarkable resilience and adaptability. This characteristic makes them highly desirable for applications where durability and flexibility are paramount.
Becoming a Plastic Surgeon: What's the Cost?
You may want to see also
Frequently asked questions
Superplasticity is the ability of a metal to elongate under physical stress by more than 200% without breaking.
Metals with superplastic properties need to be heated to high temperatures, typically one-half of their absolute melting temperature. For example, titanium is superplastic at about 900 °C and aluminium at 450–520 °C.
Superplastic metals are used in the automotive industry to make strong, lightweight parts. They are also used to make biomedical gear such as prosthetics or braces.
Various titanium, aluminium, and nickel-based alloys, as well as some stainless steels, exhibit superplasticity.