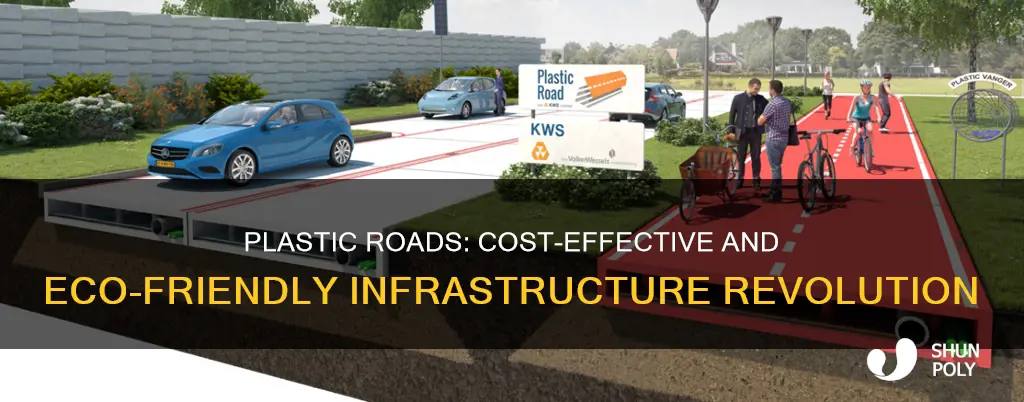
Plastic roads are made from recycled plastics, such as polyethylene terephthalate (PET or PETE), polypropylene (PP), and high- and low-density polyethylene (HDPE and LDPE). The first step in constructing them is to collect and manage the plastic material, which is then sorted, cleaned, dried, shredded, melted, and mixed with hot bitumen. In December 2019, India built 21,000 miles of roads using plastic waste, and as of 2021, the country had almost 33,700 km of plastic roadways. In the UK, a £1.6 million trial of plastic road technology was announced in January 2019, and several councils have since laid the polymers. While plastic roads have the potential to divert waste from landfills, there are concerns about their cost-effectiveness, safety, and environmental impact. For example, in Columbia, Missouri, researchers are monitoring the ditches along a plastic road to ensure that the plastic mixture isn't breaking down and leaching into the watershed.
Characteristics | Values |
---|---|
Materials | Recycled plastics, mainly polyethylene terephthalate (PET or PETE), polypropylene (PP), and high- and low-density polyethylene (HDPE and LDPE) |
Cost | Varies depending on length and amount of plastic waste used; $200,000 for 3 miles in India, £1.6 million trial in the UK |
Length | India has built 21,000 miles of plastic roads, with a total of 33,700 km of plastic roadways as of 2021 |
Environmental Impact | Potential to divert 57,803 single-use food containers and 2.5 million other plastic items per kilometre |
What You'll Learn
- Plastic roads are made from recycled plastics, including polyethylene terephthalate (PET or PETE), polypropylene (PP), and high- and low-density polyethylene (HDPE and LDPE)
- In December 2019, India built 21,000 miles of roads using plastic waste, totalling 33,700km of plastic roadways
- In January 2019, the Department for Transport announced a £1.6 million UK trial of a plastic road technology developed by MacRebur, an asphalt enhancement company based in Scotland
- State transportation officials caution that they need to determine how cost-effective the materials are and whether they’re sustainable, safe for drivers and not causing cracks, potholes or ruts
- In Columbia, Missouri, Hassinger said university researchers are monitoring the ditches along the plastic road to make sure the plastic mixture isn’t breaking down and leaching into the watershed
Plastic roads are made from recycled plastics, including polyethylene terephthalate (PET or PETE), polypropylene (PP), and high- and low-density polyethylene (HDPE and LDPE)
Plastic roads can be made entirely from modular, hollow, and prefabricated road elements made from consumer waste plastics. However, most plastic roads consist of waste plastic used to replace bitumen mixed with recycled asphalt. This type of material is sometimes referred to as Plastic Asphalt.
The cost of building plastic roads varies depending on the project. For example, in Columbia, Missouri, Hassinger said his agency originally set aside $4.8 million to repave a road with asphalt. In the UK, the Department for Transport announced a £1.6 million trial of plastic road technology. In 2021, a project in the US incurred an additional $200,000 in costs for the contractor to redo its plan and use the plastic mix in sections totalling about 3 miles.
It is worth noting that plastic roads have the potential to divert waste from landfills. For example, in India, every 1 km of road uses one million plastic bags, and the country has almost 33,700 km of plastic roadways.
Creating Custom Enamel Pins: Cost and Material Options
You may want to see also
In December 2019, India built 21,000 miles of roads using plastic waste, totalling 33,700km of plastic roadways
The process of constructing plastic roads involves collecting, sorting, cleaning, drying, and shredding plastic waste. The shredded plastic is then mixed and melted at approximately 165 °C, before being combined with hot bitumen to create a durable road surface. This method requires approximately one ton of plastic per kilometre of road, which equates to one million plastic bags.
While the use of plastic in road construction has gained traction, there are ongoing debates about its cost-effectiveness and potential environmental impact. Transportation officials are cautious about the long-term sustainability of plastic roads, particularly concerning microplastics leaching into the environment. In Columbia, Missouri, researchers are monitoring the ditches along a plastic road to assess the potential breakdown of the plastic mixture into the watershed.
The cost implications of plastic roads vary depending on the project and location. For instance, in the UK, the Department for Transport announced a £1.6 million trial of plastic road technology in 2019, while in the US, a project in Columbia, Missouri, initially allocated $4.8 million for repaving a road with asphalt. These investments reflect the ongoing exploration of plastic roads as a potential solution for waste management and road construction.
The Cost of Eco-Friendly Straws: Are They Worth It?
You may want to see also
In January 2019, the Department for Transport announced a £1.6 million UK trial of a plastic road technology developed by MacRebur, an asphalt enhancement company based in Scotland
Plastic roads are constructed using recycled plastics, primarily from common post-consumer products such as product packaging. The process involves sorting, cleaning, drying, and shredding the plastic material. The shredded plastic is then mixed and melted at around 165 °C, before being combined with hot bitumen.
The trial focused on determining whether plastic roads could offer a more cost-effective and sustainable alternative to traditional asphalt roads. It also aimed to assess the safety and durability of plastic roads, ensuring they do not cause cracks, potholes, or ruts, and can withstand freezing and scorching temperatures without breaking down.
The £1.6 million investment in the trial reflected the potential benefits of plastic roads, including the diversion of significant amounts of plastic waste from landfills and the environment. For example, in Columbia, Missouri, the state transportation agency originally set aside $4.8 million to repave a road with asphalt, but instead chose to invest in a plastic road, recognising the potential cost savings and environmental benefits. Similarly, in September 2021, a project in the US added an additional $200,000 from dedicated research funds to incorporate plastic into a 3-mile road section.
Plastic Part Production Costs: What's the Price Tag?
You may want to see also
State transportation officials caution that they need to determine how cost-effective the materials are and whether they’re sustainable, safe for drivers and not causing cracks, potholes or ruts
State transportation officials are cautious about the use of plastic roads. They need to determine how cost-effective the materials are and whether they are sustainable, safe for drivers, and do not cause cracks, potholes, or ruts. They also want to see how plastic roads stand up against freezing and scorching temperatures and ensure that microplastics in the mixture aren't causing environmental damage.
In Columbia, Missouri, researchers are monitoring the ditches along a plastic road to ensure the plastic mixture isn't breaking down and leaching into the watershed. The agency originally set aside $4.8 million to repave the road with asphalt. In 2021, a project in the US cost an additional $200,000 from dedicated research funds for the contractor to redo its plan and use the plastic mix in sections totalling about 3 miles.
In India, 21,000 miles of roads were built using plastic waste, and the country now has almost 33,700 km of plastic roadways, meaning every 1 km of road uses one million plastic bags. However, as of 2021, only 703 km of National Highways were constructed using plastic roads. In the UK, a £1.6 million trial of plastic road technology was announced in 2019.
It is estimated that one ton of plastic is needed for one kilometre of road, which has the potential to divert 57,803 single-use food containers and 2.5 million plastic bags from the waste stream. The first step in constructing plastic roads is to collect and manage the plastic material, which consists mainly of common post-consumer products such as product packaging. The most common plastics used in packaging are polyethylene terephthalate (PET or PETE), polypropylene (PP), and high- and low-density polyethylene (HDPE and LDPE). These materials are sorted, cleaned, dried, and shredded before being mixed and melted at around 165 °C. Hot bitumen is then added and mixed with the melted plastic.
The Plastic Diet: How Much Do Whales Consume?
You may want to see also
In Columbia, Missouri, Hassinger said university researchers are monitoring the ditches along the plastic road to make sure the plastic mixture isn’t breaking down and leaching into the watershed
Plastic roads are made from recycled plastics, such as polyethylene terephthalate (PET or PETE), polypropylene (PP), and high- and low-density polyethylene (HDPE and LDPE). The first step in constructing them is to collect and manage the plastic material, which consists mainly of common post-consumer products such as product packaging. The materials are then sorted, cleaned, dried, and shredded. The shredded plastic is mixed and melted at around 165 °C, before hot bitumen is added and mixed with the melted plastic.
In Columbia, Missouri, Hassinger said university researchers are monitoring the ditches along the plastic road to ensure that the plastic mixture isn't breaking down and leaching into the watershed. This is an important consideration, as state transportation officials want to ensure that microplastics in the mixture aren't causing environmental damage. Hassinger's agency originally set aside $4.8 million to repave the road with asphalt, so it will be interesting to see how the cost-effectiveness of plastic roads compares to traditional methods.
The cost of plastic roads is a key consideration for their implementation. In the UK, the Department for Transport announced a £1.6 million trial of plastic road technology developed by MacRebur, an asphalt enhancement company based in Scotland. In the US, a project that began in September 2021 incurred an additional $200,000 in costs for the contractor to redo its plan and use the plastic mix in sections totaling about 3 miles. On a larger scale, India built 21,000 miles of roads using plastic waste, with each 1 km of road using one million plastic bags.
Artificial Turf: Cost of Plastic Grass Explored
You may want to see also
Frequently asked questions
The cost of a plastic road depends on the length of the road and the type of plastic used. In 2021, a project in the US cost an additional $200,000 for a contractor to redo its plan and use the plastic mix in sections totalling about 3 miles. In 2019, the UK government announced a £1.6 million trial of a plastic road technology.
The longevity of a plastic road is currently unknown as the technology is still being trialled. However, state transportation officials are cautious about the cost-effectiveness of the materials and whether they are sustainable, safe for drivers, and do not cause cracks, potholes or ruts.
The type of plastic used in roads varies. In India, one kilometre of road uses one million plastic bags. In the UK, the plastic road technology was developed by MacRebur, an asphalt enhancement company. The first step in constructing plastic roads is to collect and manage the plastic material. The plastics involved in building these roads consist mainly of common post-consumer products such as product packaging. Some of the most common plastics used in packaging are polyethylene terephthalate (PET or PETE), polypropylene (PP), and high- and low-density polyethylene (HDPE and LDPE).
The environmental impact of plastic roads is currently being studied. In Columbia, Missouri, university researchers are monitoring the ditches along the plastic road to make sure the plastic mixture isn’t breaking down and leaching into the watershed.