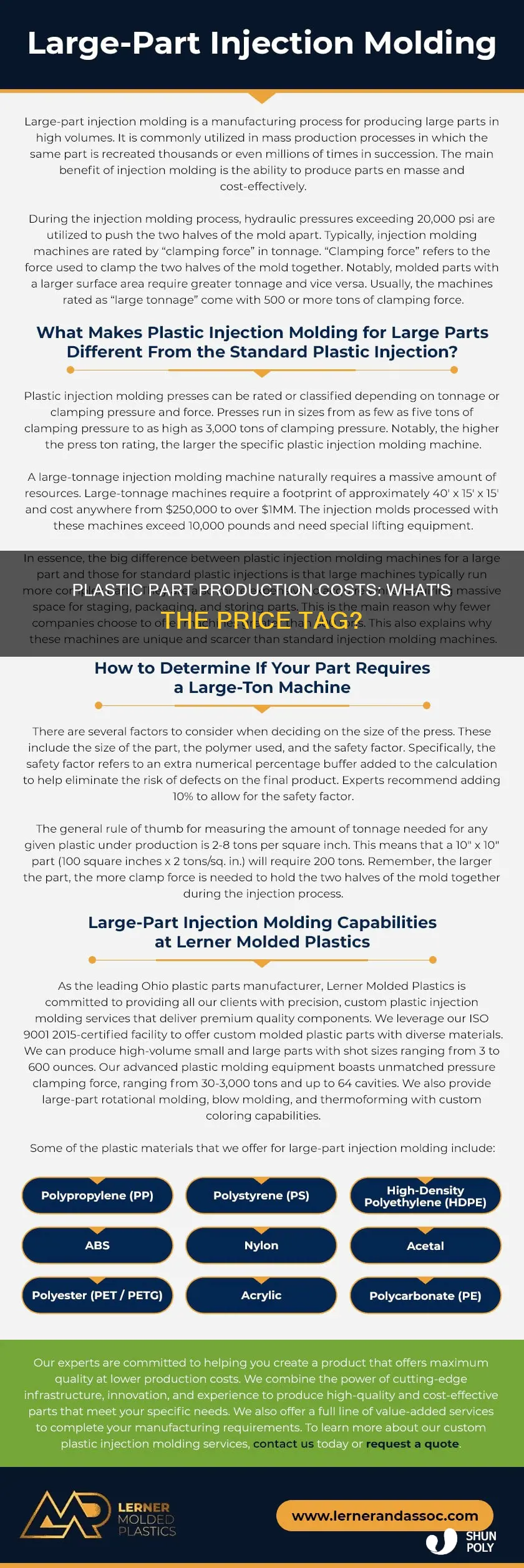
The cost of manufacturing plastic parts depends on a number of factors, including the number of cavities in the mould, the complexity of the design, and the hourly rate of the moulding machine. The price of a plastic part is also influenced by the sales forecasts and the number of setups required. Setup fees are typically charged to cover the manufacturer's expenses, rather than to make a profit.
Characteristics | Values |
---|---|
Number of cavities in the mould | The more cavities, the lower the cost per part |
Design intricacy | The more intricate the design, the higher the cost |
Type of moulding | Injection moulding is cheaper than CNC machining |
Mould cost | High |
Manufacturer's charge | Typically an hourly rate per moulding machine |
Setup fee | Typically doesn't provide profit to the manufacturer |
What You'll Learn
The number of cavities in a mold
The number of cavities in a mould is driven by sales forecasts. An 8-cavity mould will provide approximately 5 million parts per year, and a 32-cavity mould will provide approximately 20 million parts per year.
The number of cavities in a mould is an important consideration when determining the cost of manufacturing plastic parts. The more cavities a mould has, the more parts can be produced in a given amount of time. However, it is important to note that the cost of a mould with more cavities is typically higher than that of a mould with fewer cavities. Therefore, when determining the number of cavities in a mould, it is necessary to consider the balance between the desired production volume and the cost of the mould.
For example, a 32-cavity mould may provide a more attractive part price compared to an 8-cavity mould. However, investing in a large mould may not make financial sense if the production volume does not justify the cost. In some cases, it may be more feasible to fabricate multiple smaller moulds with fewer cavities to achieve the desired production volume.
The number of cavities in a mould can also impact the lead time for manufacturing plastic parts. A mould with more cavities can produce more parts in a shorter amount of time, potentially reducing the overall lead time. This is especially important when considering the time-to-market for new products or when responding to urgent customer demands.
Additionally, the number of cavities in a mould can be influenced by the geometry and shape of the parts being produced. Certain complex geometries and shapes may require multiple parts to be fabricated together, which can increase the cost and lead time. In such cases, it is important to consider the trade-off between the number of cavities and the complexity of the part design.
The High Cost of Pink Plastic: Why Blue is Cheaper
You may want to see also
The cost of the setup fee
The complexity of the design will also impact the setup fee. A complex injection mould is more costly to produce and increases the risk of part failure. Certain geometries and shapes cannot be achieved through injection moulding, requiring multiple parts to be fabricated together, which increases costs and lead times.
The hourly rate of the manufacturer will also be a factor in the setup fee. Manufacturers typically charge an hourly rate for the use of their moulding machine, which is then converted to a cost per part for the customer.
Additionally, the setup fee may include the cost of purging the old material in the moulding machine barrel. This process consumes several pounds of plastic and is necessary to ensure the quality of the final product.
Plastic Surgery: A Lucrative Career Choice?
You may want to see also
The hourly rate of the molding machine
The hourly rate of the moulding machine is the manufacturer's primary method of charging for plastic parts. However, this hourly rate is not meaningful to customers, so it is converted to a cost per part. The moulding machine hourly rate is influenced by the number of setups required, which are expensive and disruptive to normal manufacturing.
The number of setups is kept to a minimum, as they require several pounds of plastic to purge the old material in the moulding machine barrel. The setup fee charged is usually not profitable for the manufacturer, who is only seeking to cover their expenses.
The cost per part is also influenced by the number of cavities in the mould. An 8-cavity mould will provide approximately 5 million parts per year, while a 32-cavity mould will provide approximately 20 million parts per year. The 32-cavity mould may have a more attractive part price, but it wouldn't make financial sense to invest in such a large mould.
The cost of plastic parts is also influenced by the complexity of the design. A complex injection mould is more costly and increases the risk of part failure. Certain geometries and shapes cannot be achieved through injection moulding, requiring multiple parts to be fabricated together, which increases costs and lead times.
Cost Comparison: Paper vs. Plastic Straws
You may want to see also
The cost of design changes
Design changes can be easily made with a simple adjustment to the programming of the machine. However, the cost of plastic parts manufacturing increases with the intricacy of the design. A complex injection mould, for instance, is more expensive and carries a higher risk of part failure. Certain geometries and shapes cannot be achieved through injection moulding, requiring multiple parts to be fabricated together, which increases costs and lead times.
The number of cavities in a mould also impacts the cost. An 8-cavity mould can produce approximately 5 million parts per year, while a 32-cavity mould can produce 20 million parts. Although the part price per 32-cavity mould is attractive, investing in such a large mould may not make financial sense for smaller production runs.
Additionally, the setup fee charged by manufacturers typically does not generate profit but aims to cover their expenses. Manufacturers try to minimise the number of setups as they are costly and disruptive to normal manufacturing. They usually charge an hourly rate per moulding machine, which is then converted to a cost per part for the customer.
Overall, the cost of design changes in plastic parts manufacturing depends on the specific requirements and constraints of the project, with more intricate designs and larger production runs generally resulting in higher costs.
Clover Plastic Gift Cards: Cost Analysis and Benefits
You may want to see also
The cost of the plastic material
The cost of plastic material is determined by a number of factors, including the number of cavities in the mould, the complexity of the design, and the manufacturing process used.
The number of cavities in a mould directly impacts the cost of plastic parts. For example, an 8-cavity mould can produce approximately 5 million parts per year, while a 32-cavity mould can produce 20 million parts. The larger mould may have a more attractive part price, but it may not make financial sense to invest in such a large mould if the production volume does not justify it.
The design of the plastic part also affects the cost. More intricate designs with complex geometries and shapes can increase the cost of manufacturing. Certain shapes and geometries cannot be achieved through injection moulding, requiring multiple parts to be fabricated together, which increases costs and lead times.
The manufacturing process chosen also impacts the cost of plastic parts. Injection moulding, for example, may require additional fabrication to achieve tight tolerances and desired surface finishes. CNC machining, particularly CNC milling, can be a more expensive option but can produce parts with complex geometries and superior surface finishes.
Additionally, the setup costs for plastic part manufacturing can be significant. Manufacturers typically charge an hourly rate for the use of their moulding machines, which is then converted to a cost per part for the customer. The setup fee usually does not generate profit for the manufacturer but covers their expenses, as customers tend to be averse to large setup charges.
Chicken Feeders: Plastic Options for Your Flock
You may want to see also
Frequently asked questions
The cost of making a plastic part depends on a number of factors, including the number of cavities in the mold, the complexity of the design, and the hourly rate of the molding machine.
A cavity in a mold is a space that is filled with plastic to create a part. The number of cavities in a mold determines how many parts can be produced per year. For example, an 8-cavity mold can produce approximately 5 million parts per year, while a 32-cavity mold can produce approximately 20 million parts per year.
The more intricate a design is, the higher the cost of manufacturing. Complex designs may require multiple parts to be made and then fabricated together, increasing costs and lead times. Certain geometries and shapes cannot be achieved through injection molding, so alternative methods such as CNC machining may be required, which can also increase costs.
The setup fee is typically charged to cover the expenses of the manufacturer, such as purging the old material from the molding machine barrel. The setup fee does not usually provide profit to the manufacturer, and they will try to minimise the number of setups to keep costs low.