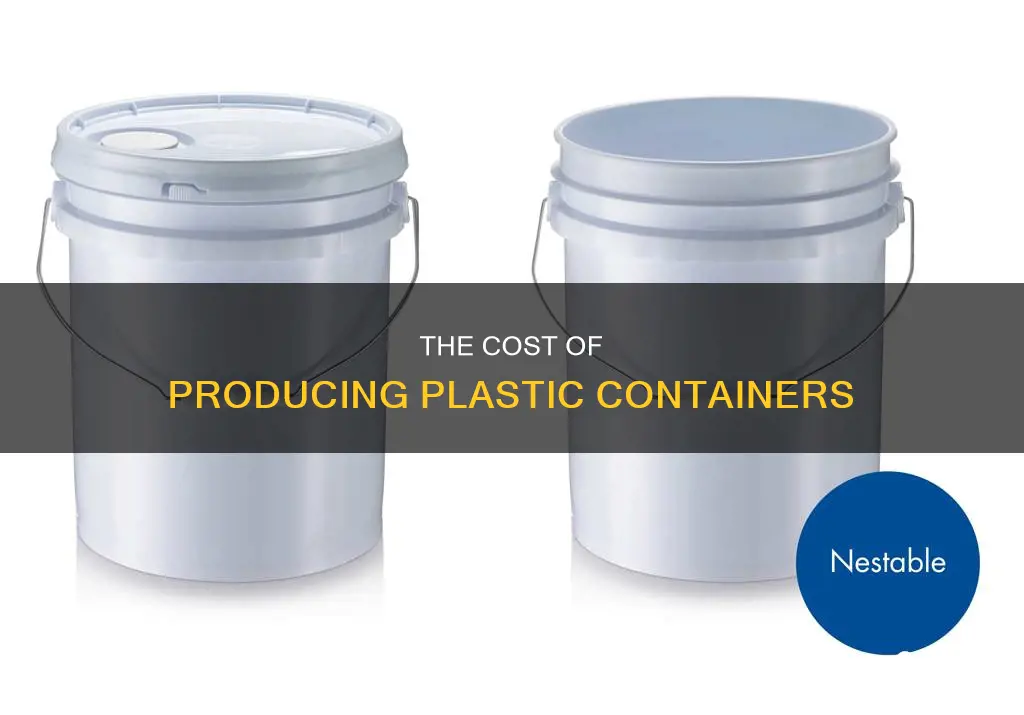
The cost of producing a plastic container depends on a range of factors, from the raw materials used to the electricity required to produce it. It also depends on the type of business producing the containers, as well as the quality of the containers and whether they are produced in-house or purchased from a supplier.
Characteristics | Values |
---|---|
Raw materials | 70% of the bottle cost |
Electricity | Variable |
High-pressure air | Variable |
Supplier costs | Variable |
Software | Variable |
What You'll Learn
Raw materials can account for up to 70% of the cost
The cost of raw materials can account for up to 70% of the total cost of making a plastic container. Other cost factors include the amount of electricity and high-pressure air needed to produce the container.
When it comes to starting a plastic container manufacturing business, there are a few key costs to consider. These include the cost of setting up an LLC, trademarks, copyrights, and patents. It is also important to invest in software and technology to help automate certain parts of the business and save on personnel costs. Additionally, you may need to spend money on inventory and setting up a website.
One way to reduce costs is to vertically integrate the blow molding process in-house. This can help to reduce quality issues and ensure that the final product looks pristine.
It is also worth considering the weight of the bottles. Bottles purchased from a supplier typically weigh more (9 or 10 grams) to ensure they arrive at the facility in good condition.
Plastic Price Per Pound: Understanding the Cost of 1000 lbs
You may want to see also
Electricity costs
The cost of making a plastic container depends on several factors, one of which is electricity. Raw materials can account for as much as 70% of the cost, but electricity is another cost factor to consider.
The amount of electricity needed to produce a plastic container depends on the manufacturing space. Each location will be different in terms of electricity, water flow, etc.
The cost of electricity also varies depending on the part of the world where the container is being produced. For example, Japan is the most expensive place to make plastic bottles at almost 4 cents a bottle, while the Middle East is much cheaper at 1.75 cents a bottle due to lower resin and fuel prices.
The type of plastic container being produced also affects the electricity costs. Most containers are injection moulded and/or blow-moulded. Blow moulds can cost $5000 - $50,000, while injection moulds are in a similar price range. After the initial investment in tooling, the cost per unit could range from $0.15 - $0.65, depending on how many bottles are made at a time.
Lucrative Prospects of Plastic Recycling: Earnings and Sustainability
You may want to see also
High-pressure air costs
The cost of making a plastic container depends on several factors, one of which is high-pressure air. High-pressure air is needed to blow the container into shape. The amount of high-pressure air required will depend on the size and shape of the container, as well as the type of plastic being used.
The cost of high-pressure air can vary depending on the source and the volume required. Compressed air can be generated on-site using a compressor, or it can be purchased from an external supplier. Generating compressed air on-site may require a significant upfront investment in equipment, but it can provide long-term cost savings for high-volume applications.
When considering the cost of high-pressure air, it is important to factor in the energy costs associated with running the compressor. Additionally, regular maintenance and servicing of the compressor should be accounted for to ensure efficient and reliable operation.
Overall, the cost of high-pressure air is an important consideration in the overall production cost of plastic containers. By evaluating the specific requirements and available options, manufacturers can make informed decisions to optimise their processes and manage costs effectively.
Plastic Pot Weights: How Much Do They Weigh?
You may want to see also
The cost of blow moulding in-house
The cost of blow moulding plastic containers in-house depends on a number of factors. The first and biggest cost factor is the raw materials used to make the containers. Raw materials can account for as much as 70% of the bottle cost.
Other cost factors include the amount of electricity needed to produce each bottle and the amount of high-pressure air needed to blow the container.
If you are considering blow moulding in-house, it is important to evaluate whether it makes financial sense for your business. There are a number of costs associated with setting up and running a plastic container manufacturer, such as the cost of software, technology, office space, and personnel.
By blow moulding in-house, you can reduce quality issues and ensure that your containers are pristine when they go out the door. This can save you money in the long run by reducing the number of returns and customer complaints.
To make an informed decision, it is recommended to seek detailed operational and financial feasibility models. These models can provide important data and help you evaluate whether blow moulding in-house is the right choice for your business.
Clear Plastic Cost: Understanding the Pricing of Transparency
You may want to see also
The cost of setting up an LLC and getting trademarks, copyrights, and patents
In addition to these production costs, there are also expenses associated with forming a business entity. Setting up an LLC, for example, may require legal fees and government filing costs. Obtaining trademarks, copyrights, and patents can also incur legal fees, application fees, and maintenance costs. These intellectual property protections are important for establishing brand recognition and safeguarding your unique designs and inventions.
The exact costs for setting up an LLC and obtaining intellectual property protections can vary depending on the jurisdiction and the complexity of your business structure. It is advisable to consult with legal professionals and business advisors to understand the specific requirements and fees applicable to your situation.
Investing in software and technology can also be a significant expense for a plastic container manufacturer. Efficient software solutions can help automate certain business processes, improve operational efficiency, and reduce reliance on expensive personnel. Additionally, consider the costs associated with establishing a website and marketing your products effectively.
Lastly, while not mandatory, renting or purchasing office space may become necessary as your business expands. This adds overhead costs but provides a dedicated space for operations, storage, and potentially, a showroom for clients.
The Cost of Biodegradable Plastic: How Much Does It Really Cost?
You may want to see also
Frequently asked questions
The cost of making a plastic container depends on a few factors, including the raw materials used, the amount of electricity used, and the amount of high-pressure air used.
The main cost factor is the raw materials, which can account for up to 70% of the bottle cost.
Yes, you will also need to consider the cost of electricity and high-pressure air, which are both necessary for the production process.
There are a few key costs associated with starting a plastic container manufacturer, including the cost of setting up an LLC, getting trademarks, copyrights, and patents, and the cost of software.