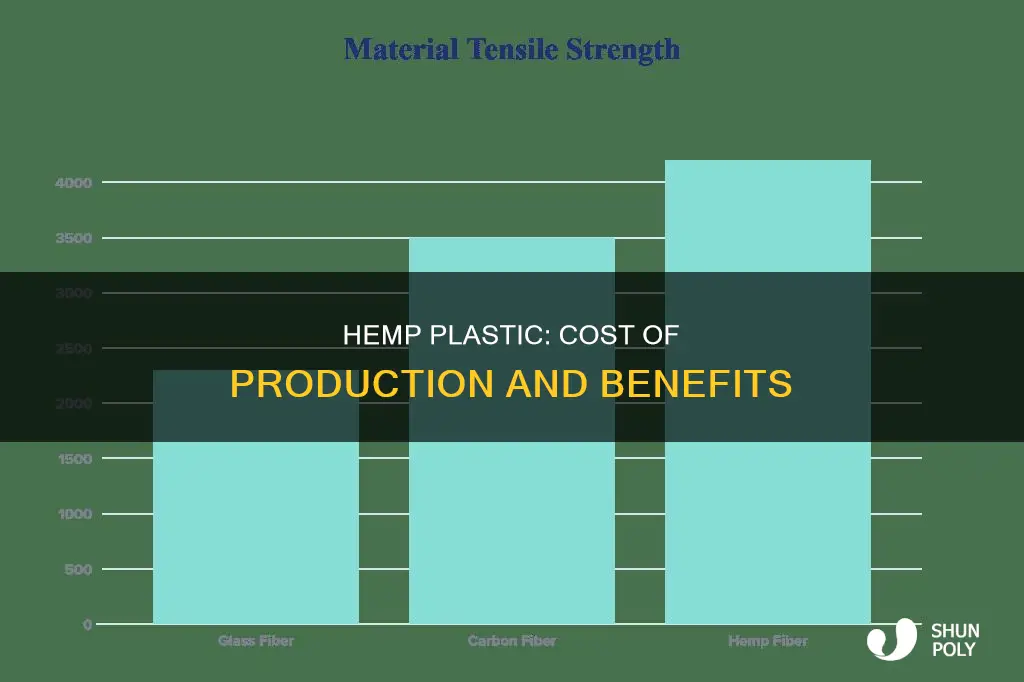
Hemp plastic is a strong, lightweight and eco-friendly alternative to traditional petroleum-based plastic. Despite the easy production process and undemanding cultivation of the plant, hemp plastic is currently more expensive to produce than traditional plastic. This is due to a lack of production infrastructure, which makes it difficult to produce hemp plastic on a large scale.
Characteristics | Values |
---|---|
Price | Higher than traditional plastic |
Production process | Requires extraction of cellulose from the plant, crushing and soaking in acid, then soaking the cellulose in water and chemical solutions to remove the acid, followed by thermal treatment |
Strength | 3.5 times stronger than traditional petroleum-based plastic |
Weight | Lighter than traditional petroleum-based plastic |
Versatility | Can be used in electronics, packaging, furniture, automotive and aircraft components |
Production infrastructure | Limited, which contributes to the higher price |
What You'll Learn
- Hemp plastic is 3.5 times stronger than traditional petroleum-based plastic
- It is also much lighter, making it extremely versatile
- Hemp plastic can be used for electronics, packaging, furniture, automotive and aircraft components
- The price of hemp plastic is higher than traditional plastic
- This is due to the lack of production infrastructure
Hemp plastic is 3.5 times stronger than traditional petroleum-based plastic
The superiority of hemp plastic over synthetic materials is so significant that Lego has declared that hemp plastic will be their main material for toy production by 2030.
The price of hemp plastic is currently higher than traditional plastic. This is due to the lack of production infrastructure for hemp plastic, as well as the advanced and large-scale production process of synthetic plastic, which keeps its price extremely low.
Despite the higher price, hemp plastic has several advantages over traditional plastic. In addition to being stronger and lighter, hemp plastic is also more eco-friendly. The hemp plant is easy to cultivate, and the production process for hemp plastic is simple. However, the price of the raw material is higher than that of traditional plastic.
While hemp plastic has many benefits, there are some challenges to its widespread adoption. One issue is that few people remember how to make paper out of hemp, as was done in the mid-1900s by Henry Ford for his line of vehicles. Despite this, the idea of making cars with hemp plastic on a mass scale is no longer far-fetched.
The Capacity of Plastic Shot Glasses Explained
You may want to see also
It is also much lighter, making it extremely versatile
Hemp plastic is 3.5 times stronger and much lighter than traditional petroleum-based plastic. This makes it extremely versatile, with applications in electronics, packaging, furniture, automotive and aircraft components. Hemp plastic is so superior to synthetic materials that Lego has declared it will be their main material for toy production by 2030.
Hemp is also an excellent paper material. Compared to wood pulp, it is much stronger and more water-resistant. It is also very cheap to manufacture, but the issue is that hardly anyone remembers how to make paper out of hemp anymore. In the mid-1900s, Henry Ford designed and manufactured an entire line of vehicles made using hemp.
The first production phase of hemp plastic involves extracting as much cellulose from the plant as possible. The hemp stems and fibres are crushed and soaked in acid. The extracted cellulose is then soaked in water and chemical solutions to remove the acid. The cellulose then undergoes thermal treatment, producing various types of material referred to as hemp plastic.
Despite the easy production process of hemp plastic and the undemanding cultivation of the plant, the price of hemp plastic is higher than traditional plastic. This is due to the advanced and large-scale production process of synthetic plastic, which makes its price extremely low. The major drawback of hemp plastic is the lack of production infrastructure, which makes the price of this raw material significantly higher than conventional plastic.
Plastic Surgery Costs: Brandon Reynolds' Pricing Guide
You may want to see also
Hemp plastic can be used for electronics, packaging, furniture, automotive and aircraft components
Hemp plastic is more expensive to produce than traditional plastic. This is because the advanced and large-scale production process of synthetic plastic makes its price extremely low. However, hemp plastic is 3.5 times stronger and much lighter than traditional petroleum-based plastic. This makes it extremely versatile, replacing any known application of petroleum-based plastic. It can be used for electronics, packaging, furniture, automotive and aircraft components.
In the mid-1900s, Henry Ford designed and manufactured an entire line of vehicles made using hemp. Although Ford was widely mocked for doing so, making cars with hemp plastics on a mass scale is no longer such a far-fetched idea. Lego, for example, has declared that hemp plastic will be their main material for toy production by 2030.
The major drawback of hemp plastic is the lack of production infrastructure. However, companies such as HempFlax are now producing hemp plastic pellets.
Lucrative Earnings of Renowned Plastic Surgeons: Unveiling the Financials
You may want to see also
The price of hemp plastic is higher than traditional plastic
Despite the easy production process of hemp plastic and the undemanding cultivation of the plant, the price of hemp plastic is higher than traditional plastic. The advanced and large-scale production process of synthetic plastic makes its price extremely low. For example, a grinder made from hemp plastic costs around $20, while the same product made from traditional plastic costs around $6.
The high price of hemp plastic is due to the lack of production infrastructure. However, the superiority of hemp plastic over synthetic materials is significant. It is 3.5 times stronger and much lighter than traditional petroleum-based plastic. This makes its use extremely versatile, replacing any known application of petroleum-based plastic, from electronics to automotive and aircraft components.
Over the years, various automotive engineers have floated the idea of making entire cars out of hemp. In the mid-1900s, Henry Ford made this dream a reality by designing and manufacturing an entire line of vehicles made using hemp. Making cars with hemp plastics on a mass scale is no longer such a far-fetched idea. Lego, for example, has declared that hemp plastic will be their main material for toy production by 2030.
The Weight of a Plastic Credit Card
You may want to see also
This is due to the lack of production infrastructure
Hemp plastic is more expensive to produce than traditional plastic due to the lack of production infrastructure. The first production phase involves extracting as much cellulose from the plant as possible. The hemp stems and fibres are crushed and soaked in acid. The next step is soaking the extracted cellulose in water and chemical solutions to remove the acid. The cellulose then undergoes thermal treatment, producing various types of material referred to as hemp plastic.
The easy production process of hemp plastic and the undemanding cultivation of the plant would suggest a low price for this raw material. However, the reality is that the price of hemp plastic is higher than traditional plastic. The advanced and large-scale production process of synthetic plastic makes its price extremely low.
Hemp is an excellent paper material and is much stronger and more water-resistant than wood pulp. It is also very cheap to manufacture, but the issue is that hardly anyone remembers how to make paper out of hemp anymore. Over the years, various automotive engineers have floated the idea of making entire cars out of hemp. In the mid-1900s, Henry Ford made this dream a reality by designing and manufacturing an entire line of vehicles made using hemp.
The superiority of hemp plastic over synthetic materials is so significant that Lego, a company producing iconic building blocks, declared that hemp plastic would be their main material for toy production by 2030. At present, the major drawback of hemp plastic is the lack of production infrastructure. Consequently, the price of this raw material is significantly higher than conventional plastic.
The Cost of Eco-Friendly Straws: Are They Worth It?
You may want to see also
Frequently asked questions
Hemp plastic is more expensive to make than traditional plastic.
The large-scale production process of synthetic plastic makes its price extremely low. Hemp plastic, on the other hand, does not have the same level of production infrastructure, which makes it more expensive.
Hemp plastic is 3.5 times stronger and much lighter than traditional petroleum-based plastic. It is also more water-resistant than wood pulp.
Hemp plastic can be used to make a wide range of products, including electronics, packaging, furniture, automotive and aircraft components, and toys.