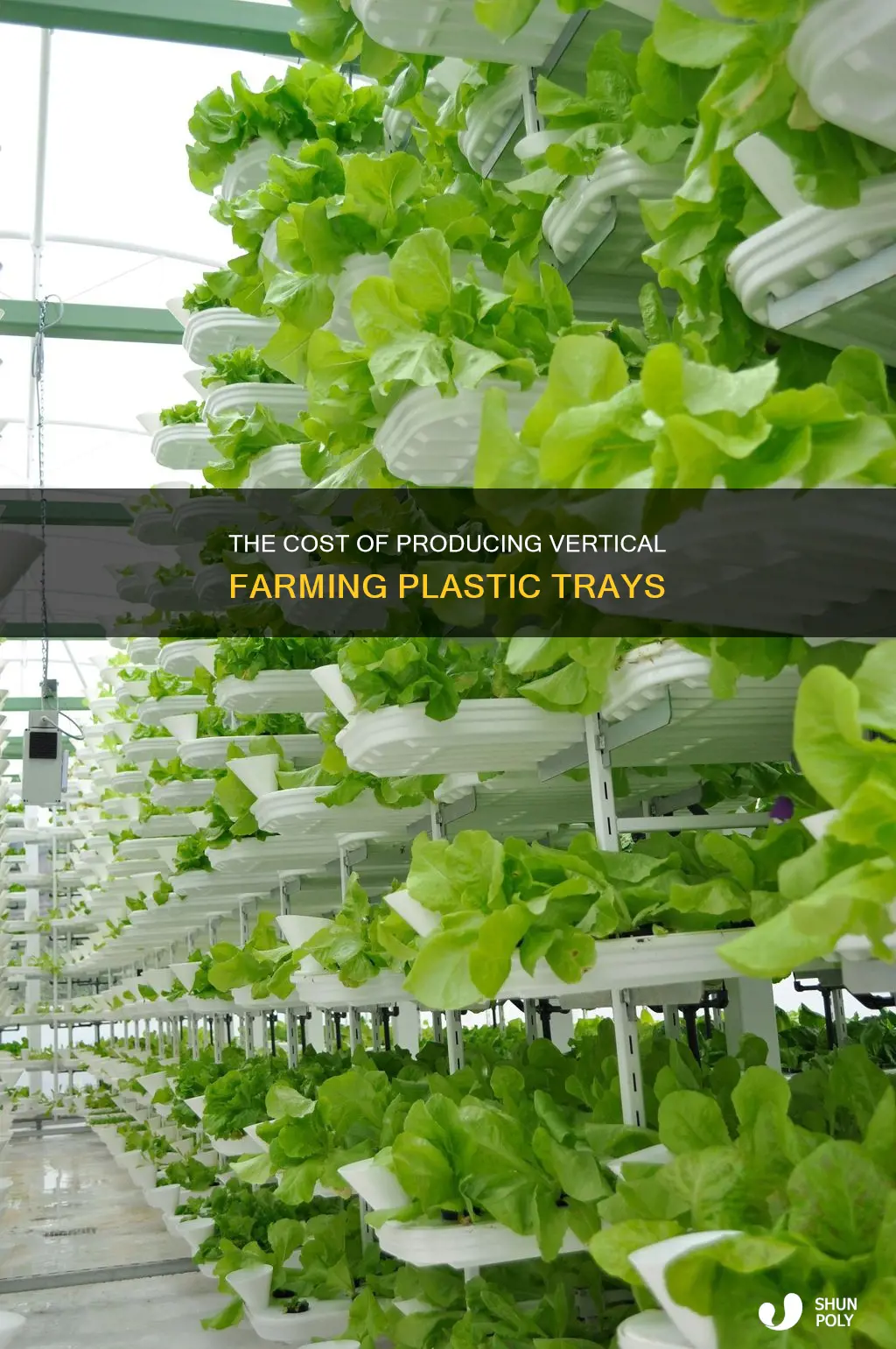
Plastic thermoforming is one of the least expensive ways of manufacturing plastic trays. The cost of producing plastic trays varies depending on the complexity of the cavity, size of the tray, and material used for the tray. The typical tooling cost for a 12 x 8 Custom Shipping Tray or ESD Tray with custom cavities is $1,500. However, there are ways to reduce costs, such as using low-cost designs or off-the-shelf plastic trays with $0 tooling costs.
Characteristics | Values |
---|---|
Cost of tooling for custom plastic trays | $1,500 |
Cost of tooling for custom plastic trays with custom cavities | $95 |
Cost of tooling for custom plastic trays with custom cavities (12 x 8) | $1,500 |
Cost of tooling for custom plastic trays with custom cavities (smaller trays) | $1,250 |
Cost of tooling for custom plastic trays with custom cavities (larger trays) | More than $1,250 |
Cost of tooling for custom plastic trays with custom cavities (complex tools) | More than $1,250 |
Cost of tooling for custom plastic trays with custom cavities (higher volume) | More than $1,250 |
Cost of tooling for custom plastic trays with custom cavities (lead time) | 2-12 weeks |
Cost of tooling for custom plastic trays with custom cavities (shipping) | Styrene and PVC are the least expensive options |
What You'll Learn
- Custom plastic trays are manufactured using the vacuum forming process
- Plastic thermoforming is one of the least expensive ways of manufacturing plastic trays
- Tooling costs vary depending on the complexity of the cavity, size of tray, and material used
- Styrene and PVC are the least expensive options for shipping trays
- A project engineer can suggest low-cost designs for custom plastic trays
Custom plastic trays are manufactured using the vacuum forming process
The cost of producing plastic trays varies depending on the complexity and size of the tray, as well as the material used. For example, the typical tooling cost for a 12 x 8 custom shipping tray with custom cavities is $1,500, while smaller trays in low-volume applications can start at $1,250. Styrene and PVC are the least expensive options for shipping trays, while ESD trays can be made disposable or reusable in anti-static, ESD, or conductive materials.
ABS Shrinkage: Understanding 3D Print Warping and Solutions
You may want to see also
Plastic thermoforming is one of the least expensive ways of manufacturing plastic trays
The typical tooling cost for a custom plastic tray is around $1,250 to $1,500, but this can vary depending on the specific requirements of the tray. Some materials, such as Styrene and PVC, are less expensive options for shipping trays.
To keep costs low, it is recommended to consult a project engineer who can suggest low-cost designs or alternative options such as foam tooling or off-the-shelf plastic trays. The lead time for custom plastic trays can also impact the overall cost, with basic and low-volume projects taking around 2-4 weeks, while more complex or higher-volume items can take up to 10-12 weeks.
Overall, plastic thermoforming offers a cost-effective solution for manufacturing plastic trays, with the ability to customise the design and material to meet specific requirements while maintaining a relatively low cost compared to other packaging processes.
ABS Plastic Shrinkage: Understanding the Science and Percentages
You may want to see also
Tooling costs vary depending on the complexity of the cavity, size of tray, and material used
The cost of producing plastic trays varies depending on the type of plastic used, the size of the tray, and the complexity of the design. The tooling cost for a 12 x 8 Custom Shipping Tray or ESD Tray with custom cavities is $1,500. However, the tooling cost for a smaller tray in a low-volume application can start as low as $1,250 and increase based on complexity and size. The type of plastic used also affects the tooling cost, with materials such as poly-carbonate and polypropylene requiring more complex tooling.
One way to reduce costs is to use a project engineer to suggest low-cost designs or alternate options like foam, which has a tooling cost of $95 for custom cavity trays. Off-the-shelf plastic trays have a tooling cost of $0. Plastic thermoforming is another cost-effective option for manufacturing plastic trays, as it is one of the least expensive ways of producing them. The process involves heating a plastic sheet and stretching it into a mold.
The lead time for custom plastic trays can vary from 2-4 weeks for basic, low-volume projects to 10-12 weeks for complex tools or higher-volume items. A full-size prototype can also be added to the process if specifications require a full-size tray for package testing or evaluation. The production tooling is then built and the first article is submitted for final approval.
The typical production mold for a plastic tray is estimated at 500,000 trays, but it is likely to last much longer. Shipping trays made from styrene or PVC are the least expensive options, while ESD trays can be made disposable or reusable in anti-static, ESD, or conductive materials.
Starbucks Plastic Cups: How Much Do They Cost?
You may want to see also
Styrene and PVC are the least expensive options for shipping trays
Custom plastic tray tooling costs can start as low as \$95 for foam custom cavity trays or $0 for off-the-shelf plastic trays. The cost of custom plastic tray moulds can also vary, starting at \$1,250 for smaller trays in low-volume applications and increasing based on complexity and size. Plastic thermoforming is one of the least expensive ways of manufacturing plastic trays, as it involves heating and stretching plastic sheets into a mould. This process is used to create plastic trays, plastic clamshells, and plastic end caps, all of which provide proper part protection during shipping.
The Cost of Plastic Tablecloths: How Much Do They Cost?
You may want to see also
A project engineer can suggest low-cost designs for custom plastic trays
For example, the typical tooling cost for a 12 x 8 Custom Shipping Tray or ESD Tray with custom cavities is $1,500. However, this cost can be reduced by using alternate materials such as foam, which has a tooling cost of $95 for custom cavity trays. Off-the-shelf plastic trays are another option with a $0 tooling cost.
Plastic thermoforming is one of the least expensive ways of manufacturing plastic trays. This process involves heating a plastic sheet and stretching it into a mold. The cost of custom plastic tray molds begins at $1,250 for smaller trays in low-volume applications and increases based on complexity and size.
To further reduce costs, a project engineer can suggest designs that optimise the number of trays produced from each production mold. A production mold is estimated to produce 500,000 trays but can last much longer. Additionally, the engineer can recommend materials such as Styrene and PVC, which are the least expensive options for shipping trays.
By considering factors such as material selection, tooling costs, and production volume, a project engineer can propose cost-effective designs for custom plastic trays, ensuring that the final product meets the required specifications while minimising overall expenses.
Recycling Rewards: Tucson's Plastic Returns
You may want to see also
Frequently asked questions
The cost of producing Verticrops plastic trays varies depending on the complexity and size of the tray, as well as the material used. The typical tooling cost for a custom plastic tray is $1,500, but this can be lower for simpler designs or off-the-shelf options.
The cost of producing Verticrops plastic trays is influenced by the complexity and size of the tray, as well as the material used. More complex designs and larger sizes can increase the tooling cost.
Common materials used for Verticrops plastic trays include poly-carbonate, polypropylene, styrene, and PVC. The choice of material can impact the tooling cost, with some materials requiring more complex tooling than others.
Yes, alternative options such as foam trays are available at a lower tooling cost of $95. Off-the-shelf plastic trays also have a $0 tooling cost.
The timing for producing Verticrops plastic trays depends on the complexity of the design and the volume of trays required. Basic, low-volume projects can be completed within 2-4 weeks, while complex or high-volume projects may take up to 10-12 weeks.