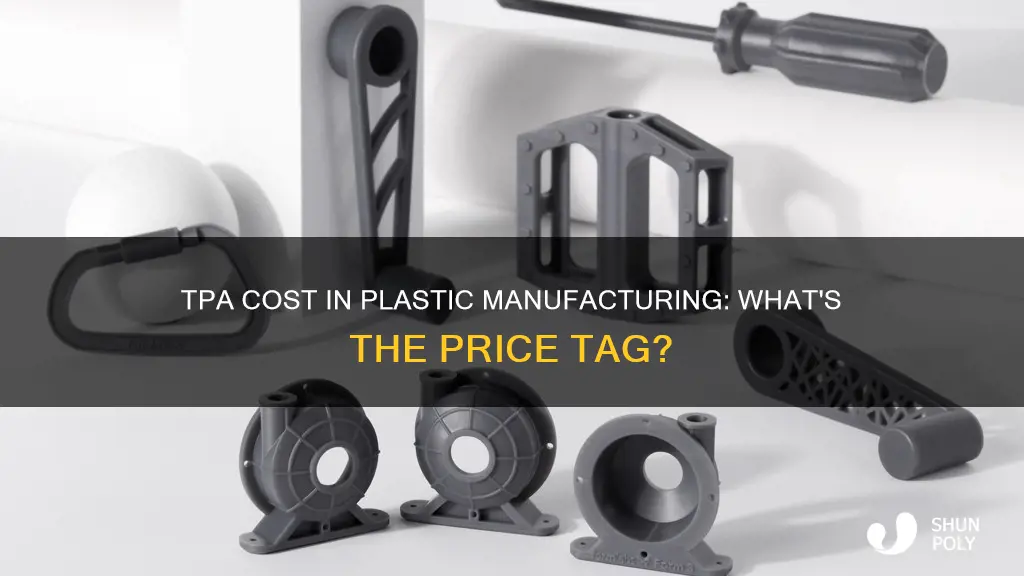
Terephthalic acid (TPA) is an organic compound used to manufacture polyethylene terephthalate (PET) resins and polyester fibres and films. It is also used in the production of adhesives, lubricants, paint additives, solvents, plasticizers, textiles, and electronics. The cost of TPA for plastic manufacturing depends on a variety of factors, including the type of plastic, availability, lead time, labour costs, and the techniques required to produce specific parts.
Characteristics | Values |
---|---|
TPA used for | Manufacturing of light-coloured, high-strength, solvent-free adhesives |
TPA used for | Production of polyethylene terephthalate (PET), which is used to make beverage bottles, food containers, and other packaging materials |
TPA used for | Manufacturing of industrial goods, such as adhesives and sealant chemicals, lubricants, intermediates, paint additives, solvents, plasticizers, textiles, electronics, etc. |
TPA used for | Intermediate in the production of oligomeric TPA esters |
Cost factors | Type of plastic, availability, and lead time |
Cost factors | 'Scrap Rate' percentage (amount of material lost from manufacturing setup) |
Cost factors | Sheet size |
Cost factors | Labour costs |
Cost factors | Volume |
Cost of plastic
The cost of plastic manufacturing depends on a variety of factors. The hourly rate of the moulding machine can be around $130 per hour, and this may or may not include the cost of plastic. The number of cavities in the mould is another factor, as the cost per part decreases as the number of cavities increases. The type of plastic, its availability and lead time will also factor into the total cost of materials used. A 'Scrap Rate' percentage is calculated to estimate the amount of material that will be lost from the manufacturing setup, and this will also impact the cost. Sheet size is calculated before ordering materials to ensure the plastic is large enough to fit the mould and the thermoforming machine. Labour costs are calculated depending on the techniques required to make a specific part, and some parts may require specialised techniques or tooling that add to the total cost of production.
Plastic's Carbon Footprint: How Much is Too Much?
You may want to see also
Cost of labour
The cost of labour in plastic manufacturing depends on the techniques required to make a specific part. Some parts may require specialised techniques or tooling that add to the total cost of production. The hourly rate for a moulding machine is around $130/hr, and the cost of labour is often included in this rate. However, some manufacturers charge the customer for plastic separately. The cost of labour can also be affected by the number of cavities in the mould, as the injection moulding cost per part decreases as the number of cavities increases. This is because the cycle time, or the time required to complete all stages of the injection moulding process, is reduced when there are more cavities.
Plastics are a cost-effective material for manufacturing, especially as the volume of production increases. This is because the consistency of parts and the wide range of mechanical properties available through plastic material selection drive down costs. The type of plastic, availability, and lead time all factor into the total cost of materials, which can impact the overall cost of labour. To estimate the amount of material lost from the manufacturing setup, a 'Scrap Rate' percentage is calculated. Sheet size is also considered to ensure the plastic is large enough to fit the mould and the thermoforming machine, which can affect the labour required.
Plastic Surgeons in Ohio: High-Paying Medical Career
You may want to see also
Cost of machinery
The cost of machinery for plastic manufacturing depends on several factors. The type of plastic, availability, and lead time all factor into the total cost of materials used. Some plastics are more difficult to form than others, so a 'Scrap Rate' percentage is calculated to estimate the amount of material lost during the manufacturing setup. Sheet size is also calculated before ordering materials to ensure the plastic is large enough to fit the mould and the thermoforming machine.
Labour costs are calculated next, depending on the techniques required to make a specific part. Some parts may require specialised techniques or tooling that add to the total cost of production. The number of cavities in the mould is another factor that affects cost. As the number of mould cavities increases, the injection moulding cost per part decreases.
The hourly rate for a moulding machine can vary, with some manufacturers charging $130 per hour, which may or may not include the cost of plastic.
CoolSculpting Cost: What the Plastic Surgeons' Say
You may want to see also
Cost of TPA
The cost of terephthalic acid (TPA) is influenced by several factors, including the price of raw materials, production costs, and market demand. TPA is an organic compound produced by the air oxidation of p-xylene in the presence of acetic acid (HAc). It has a wide range of applications, including the manufacturing of polyethylene terephthalate (PET) resins, polyester fibres and films, adhesives, and sealant chemicals.
The cost of TPA can vary depending on the availability and price of raw materials, such as p-xylene and acetic acid. Production costs, including labour, energy, and equipment, also play a significant role in determining the final price. Additionally, market demand and supply dynamics can influence the cost of TPA. As the demand for TPA increases, manufacturers may adjust their prices accordingly.
One of the critical applications of TPA is in the production of PET resins. PET resins are used in the manufacturing of beverage bottles, food containers, and packaging materials. The growing demand for PET products, driven by the increasing consumption of packaged goods and beverages, has a direct impact on the cost of TPA. As the demand for PET resins increases, the price of TPA may also rise due to the higher demand for this raw material.
The cost of TPA can also be influenced by the manufacturing process and the number of cavities in the mould. The hourly rate for a moulding machine can range from $130/hr and above, depending on the complexity and size of the machine. The number of cavities in the mould affects the injection moulding cost per part, as a higher number of cavities leads to a decrease in cost per part. Additionally, the type of plastic, availability, and lead time impact the total cost of materials used in plastic manufacturing.
The Weight of Raw Plastic: How Much Does it Weigh?
You may want to see also
Cost of manufacturing
The cost of manufacturing plastic parts depends on several factors. One of the main considerations is the type of plastic being used, as some plastics are more difficult to form than others. This can impact the 'Scrap Rate'—the amount of material lost during the manufacturing setup. The availability and lead time of the plastic will also factor into the total cost of materials.
Another key cost driver is the number of cavities in the mold. Injection molding machines work by injecting molten plastic into a mold with multiple cavities, each of which produces a single part. As the number of cavities increases, the injection molding cost per part decreases. This is because the machine can produce more parts in a single cycle, spreading the fixed costs of operating the machine over a larger number of parts.
Labor costs are another important consideration. Some parts may require specialized techniques or tooling that add to the total cost of production. The hourly rate for operating an injection molding machine can vary, and some manufacturers include the cost of plastic in this rate, while others charge it separately.
Finally, the volume of production can also impact the cost of manufacturing plastic parts. Plastics tend to become more cost-effective as the volume increases, due to economies of scale. This is one of the reasons why plastics are often used in high-volume manufacturing, in addition to their consistency and versatility.
Plastic Wrap Car Protection: Cost and Benefits
You may want to see also
Frequently asked questions
The cost of TPA for plastic manufacturing depends on a variety of factors, including the type of plastic, availability, and lead time.
The cost of TPA for plastic manufacturing is influenced by factors such as the volume of production, the number of cavities in the mold, and the complexity of the part being manufactured.
Plastics are a cost-effective option for high-volume manufacturing due to their consistent part quality and wide range of mechanical properties. As the volume of production increases, the cost per unit typically decreases.
Yes, there may be additional costs such as labour, specialised tooling, and the 'Scrap Rate' percentage, which estimates the amount of material lost during the manufacturing process.