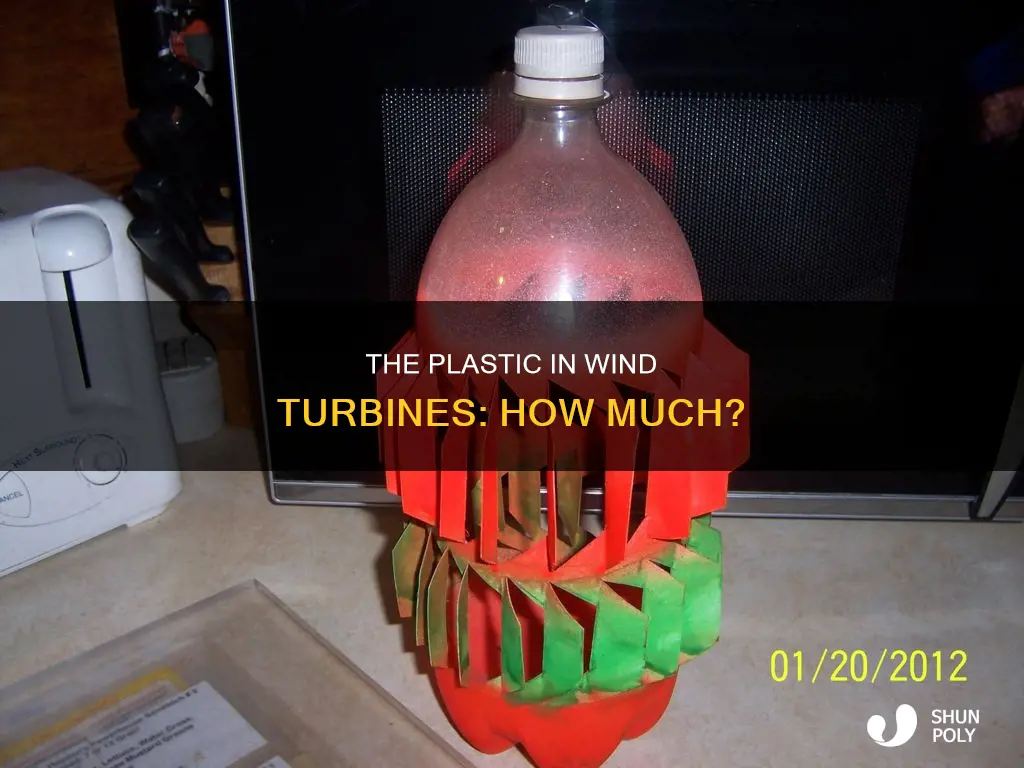
Wind turbines are an essential component of the world's transition to renewable energy sources. While they are key to fighting the climate crisis, the construction of wind turbines requires a variety of materials, including plastics. The blades of wind turbines are made of reinforced plastics, which are derived from petrochemical sources. The use of plastics in wind turbines is a double-edged sword – while it helps to generate renewable energy, it also contributes to emissions and pollution.
Characteristics | Values |
---|---|
Plastic used in wind turbines | PET (Polyethylene terephthalate), a plastic polymer commonly found in food and drink packaging |
Plastic components of wind turbines | The blades, which can be made from reinforced plastics, epoxy resin, fiberglass, and carbon fibre |
Advantages of plastic in wind turbines | Greater supply chain flexibility, improved aerodynamics, lightweight, high strength and stiffness, corrosion resistance, recyclability |
Disadvantages of plastic in wind turbines | Potential release of toxic microplastics into the environment, high energy consumption in the production of plastic fibres |
What You'll Learn
Plastic blades
Plastic is an essential component in wind turbine blades, offering numerous benefits for sustainable energy production. The use of plastic in wind turbine blades is a complex issue, with advantages and challenges that require innovative solutions.
Firstly, let's explore the benefits of using plastic in wind turbine blades. Plastic, specifically thermoplastic, is highly resistant to corrosion and lighter than aluminium or other metals. This reduced weight is advantageous as it allows the blades to spin faster, generating more energy and driving down greenhouse gas emissions. The lightweight property of plastic is further enhanced when reinforced with glass or carbon fibres, creating composite materials that are highly efficient and strong. These composite materials are also easy to recycle, which is crucial for the wind energy industry's sustainability goals.
One of the most commonly used plastics in wind turbine blades is PET (Polyethylene terephthalate), which can be recycled and is often sourced from food and drink packaging. The use of PET has increased due to its supply chain flexibility and ability to strengthen the foam sheets during the blade manufacturing process. By 2019, recyclable core materials, including R-PET, comprised almost 60% of LM Wind Power's product output, showcasing the growing adoption of recycled plastics in the industry.
However, there are also challenges associated with the use of plastic in wind turbine blades. One significant issue is the potential release of toxic substances during the blades' operation or disposal. Some blades contain epoxy compounds with Bisphenol A (BPA), which is highly toxic and banned in certain regions. As blades erode, these toxins can find their way into oceans and drinking water, posing a risk to the environment and human health. Additionally, the breakdown of plastic into micro/nanoplastics during wear and peeling further contributes to environmental concerns.
To address the plastic waste problem, companies like Vestas are developing innovative solutions. Vestas has discovered a method to break down the plastic in turbine blades into virgin-grade material, enabling recycling for new turbines instead of landfilling. However, the specifics of this technology remain undisclosed, and challenges related to the recycling process, such as the need for reinforcement with new plastic, persist.
In conclusion, plastic blades in wind turbines play a critical role in sustainable energy production, offering advantages in terms of weight reduction, corrosion resistance, and recyclability. However, the industry must continue to address the challenges associated with toxic substances and plastic waste to ensure the responsible use and disposal of these blades.
Impoverished Nations: Ocean Plastic Pollution's Unseen Culprits?
You may want to see also
Composite materials
The composite materials used in wind turbine blades are typically reinforced plastics, often fibre-reinforced plastics. The polymer base is usually epoxy resin, and the fibres provide strength and stickiness. One such example is fiberglass, which is commonly used in wind turbine blades. The use of composite materials in wind turbine blades improves the stiffness-to-weight ratio, making the blades strong and stiff without adding excessive weight. This weight reduction is important because lighter blades increase the efficiency of the turbine in generating power.
In addition to their use in blades, composite materials are also used in other components of wind turbines, such as access structures (ladders and platforms), cable management systems, and even in the generator as insulation solutions. The application of composites in these areas contributes to the overall performance and efficiency of the wind turbine system.
The choice of composite materials in wind turbines offers several advantages. Firstly, composites provide high strength and stiffness relative to their weight, which is crucial for the structural integrity and performance of the blades. Secondly, the use of composites can help reduce the cost of wind turbines. Additionally, composites offer design flexibility, allowing manufacturers to create complex and aerodynamic blade shapes that optimise power generation.
While the use of composite materials in wind turbines offers numerous benefits, there are also some challenges and considerations. One challenge is the high-cycle fatigue behaviour of composites, which refers to the ability of the material to withstand repeated load cycles without failure. This is particularly important in larger blades, where structural stiffness is critical to ensuring tip clearance and avoiding collisions with the tower.
Plastic HDPE Bales: Weight and Shipping Factors
You may want to see also
Thermoplastics
One example of a thermoplastic resin is Arkema's Elium resin, a two-part liquid reactive thermoplastic that combines the benefits of thermoset and thermoplastic resins. Elium thermoplastic resins can be used as a drop-in replacement for epoxy, reducing equipment costs and cycle time. Additionally, Elium thermoplastic blades have been found to exhibit five to seven times higher levels of structural damping than epoxy blades, leading to improved fatigue performance and increased turbine longevity.
The recyclability of thermoplastics is another significant advantage. When combined with thermal welding techniques, thermoplastic blades can be recycled at the end of their life, reducing the time, cost, and energy required for disposal. This addresses the challenges associated with the disposal of traditional wind turbine blades and aligns with the sustainability goals of the energy sector. Furthermore, the use of thermoplastics can reduce the weight of the blade root by up to 50%, which has a positive impact on transportation costs.
Overall, thermoplastics offer numerous benefits for wind turbine blades, including improved performance, reduced costs, increased longevity, and recyclability. These advantages contribute to the advancement of the wind energy market and the transition to renewable energy sources.
Sponges: A Microplastics Haven?
You may want to see also
Recycled PET
PET, or Polyethylene terephthalate, is a plastic polymer commonly found in food and drink packaging. It can be recycled and used in the production of wind turbine rotor blades. Recycled PET (R-PET) is a more sustainable alternative to balsa wood, which is traditionally used in the main laminate of a wind turbine blade. Balsa wood is light and strong but is affected by seasonality and has limited sources. R-PET, on the other hand, offers greater supply chain flexibility and helps reduce carbon dioxide emissions during the manufacturing process.
In 2014, LM Wind Power started using PET foam in the shear webs of blades, and its use has been growing since then. By 2019, the company had achieved a 30% growth in production thanks to the large volumes of PET secured, even amidst supply shortages of balsa wood. This switch to PET also helped the company maintain production during the challenges of the 2020 pandemic.
One of the key advantages of using recycled PET in wind turbine blades is its strength and stiffness-to-weight ratio. The lighter the blade, the more efficient the turbine is in generating power. R-PET also allows for the creation of specific aerodynamic blade shapes that are curved, tapered, and twisted, further enhancing the efficiency of the turbine.
Additionally, recycled PET has found a new application in wind turbine rotor blades through companies like Armacell. Armacell has set up an extrusion line at its Brampton facility in Ontario, Canada, to convert recycled PET resin into PET foam for these blades. Around 75% of Armacell's PET foam is used as the core for the blades, with approximately 50,000 PET bottles going into forming the core of a single wind turbine. Armacell estimates that its PET foam is already used in more than 30,000 rotor blades globally.
The use of recycled PET in wind turbines is an innovative way to give plastic bottles a second life and contribute to the fight against the climate crisis. While there are emissions associated with the production and processing of plastics, the renewable energy generated by wind turbines justifies their use. Furthermore, the U.S. Department of Energy (DOE) is investing in improving the recycling of wind energy technologies, aiming to increase the recycling and reuse of decommissioned wind energy equipment and materials.
Whale's Death: Plastic Pollution's Real-Life Horror Story
You may want to see also
Toxicity and environmental impact
While wind turbines are a source of renewable energy, they are not without their environmental impact. The blades of wind turbines are made of composite and plastic materials, including reinforced plastics, epoxy resin, and fiberglass. The use of these materials has raised concerns about toxicity and waste.
One of the main concerns regarding the toxicity of wind turbine blades is the presence of Bisphenol-A (BPA), a known endocrine disruptor and neurotoxin. BPA is often banned and is considered one of the most toxic man-made substances. Wind turbine blades can contain up to 40% BPA in their resin coating, and as the blades spin at high speeds, BPA microparticles can be released into the air, soil, and nearby waterways. Due to the placement of turbines in high-wind locations and their ability to generate strong winds, these toxic microparticles can travel long distances and contaminate large volumes of water.
The issue of waste in the wind energy industry has also been a challenge. While about 90% of turbines are easily recyclable, their blades are not. The blades are made from strong and durable materials, such as fiberglass and epoxy resin, which are challenging and costly to break down. Most blades end up in landfills or are incinerated, contributing to waste and pollution. However, recent technological advancements offer potential solutions to this problem. For instance, Danish wind company Vestas announced a breakthrough solution for recycling wind turbine blades without changing their design or materials. Additionally, Carbon Rivers has upcycled several blades, and researchers at the University of Michigan have developed a new resin for blades that can be recycled into various products, including new turbine blades.
The production and processing of plastics used in wind turbine blades also have environmental implications. The conversion of petrochemical sources into polymers and the high-temperature processing of fibres, such as carbon fibre, require significant energy consumption. This energy-intensive process contributes to the overall environmental footprint of wind turbine production and operation.
In summary, while wind turbines provide renewable energy, the presence of BPA in their blades raises concerns about toxicity and potential pollution of air, soil, and water sources. The waste generated from non-recyclable blades and the energy-intensive production of plastics further contribute to the environmental impact of the wind energy industry. Addressing these challenges through technological innovations, material changes, and improved recycling or upcycling processes is crucial for enhancing the sustainability of wind energy.
Plastic Surgeons: UK Earnings and Salary Insights
You may want to see also
Frequently asked questions
The amount of plastic in a wind turbine varies depending on the size and type of turbine. A 1.5-MW turbine with blades measuring 110-124 ft in length has a total blade mass of about 15,000 kg, of which approximately 75% is glass. However, newer turbines are using plastic alternatives like PET (Polyethylene terephthalate), a recyclable plastic polymer commonly found in food and drink packaging.
The type of plastic used in wind turbines is typically reinforced plastics or composite materials, which offer great strength and stiffness while being lightweight. These plastics are often fibre-reinforced, with the polymer derived from petrochemical sources and the fibres providing stickiness and strength.
Plastics are used in wind turbines because they offer advantages in terms of chemical, thermal, and mechanical properties, enabling specific blade shapes and improving overall efficiency. Thermoplastics, in particular, are highly resistant to corrosion, lightweight, and recyclable, making them suitable for onshore and offshore turbines.
Wind turbines have been found to shed toxic microplastics during operation due to wear and tear, which can have negative environmental and health impacts. The toxins within the epoxy compounds shed by the blades can contaminate oceans and drinking water, and the landfill disposal of old blades further contributes to plastic waste.
The use of plastics in wind turbines is considered beneficial as it provides renewable energy and helps fight the climate crisis. However, the production of plastic blades requires a significant amount of energy and contributes to emissions. Overall, the advantages of using plastics in wind turbines for renewable energy generation are believed to outweigh the drawbacks.