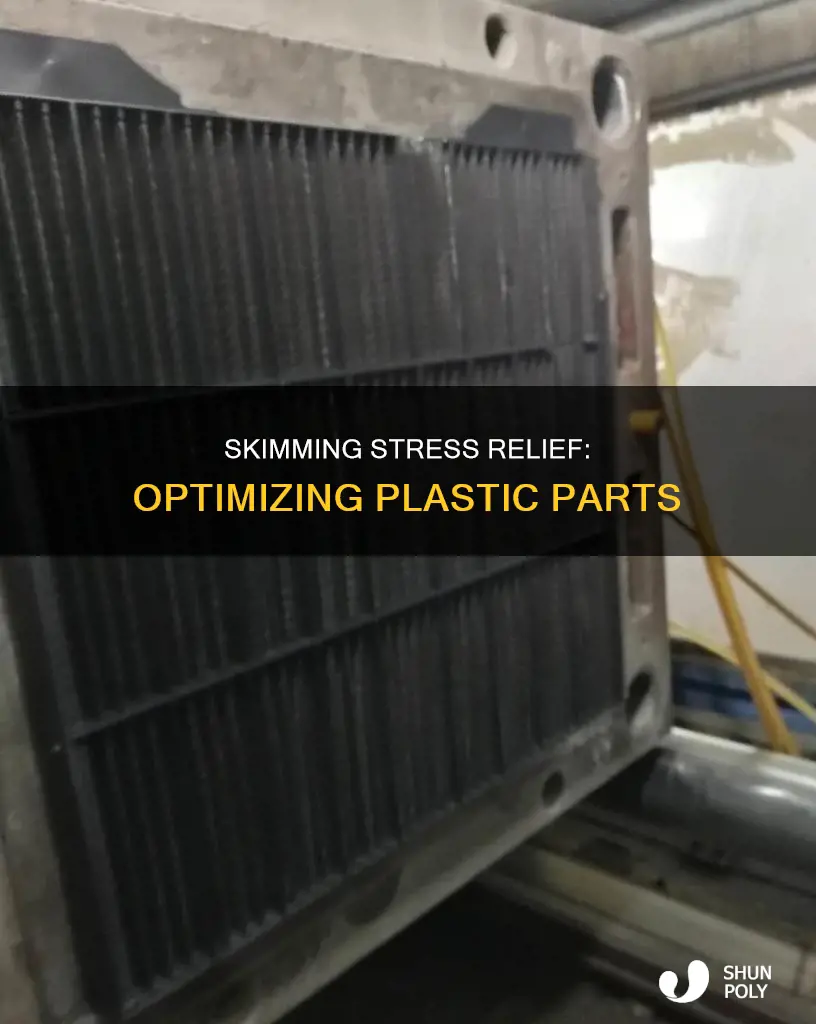
Residual stress is an issue in all injection-moulded plastic parts, and this can lead to part failure or reduced performance. One way to relieve stress in plastic parts is through a process called annealing, which involves heating the plastic to just below its softening point and then allowing it to cool slowly. This process relieves internal stresses in the material and improves its mechanical and thermal properties. The amount of heat and time required for annealing depends on the type of plastic being treated. While annealing is a well-known method for relieving stress in plastics, some people are interested in exploring other methods, such as using vibration. However, heat is the most common method for relieving stress in plastic parts.
What You'll Learn
Annealing: a heat treatment to change plastic properties
Annealing is a heat treatment process used to change the properties of plastic materials. It is employed to relieve internal stresses that can lead to reduced performance or failure of plastic parts. The process involves heating the plastic above its recrystallization temperature, allowing its structure to become finer and more uniform, before letting it cool back down.
During the conversion of resins to finished parts or stock shapes, various factors such as heating, pressures, and cooling contribute to the development of internal stresses in plastic materials. These stresses can cause issues like warping, twisting, cracking, and unexpected changes in dimensions. Annealing helps to reduce these stresses, thereby enhancing the mechanical and thermal properties of the plastic.
The annealing process for plastics involves slowly heating a polymer part to a temperature slightly below its softening point. This temperature is controlled and maintained for a specific duration, depending on the type of plastic being treated. The heating occurs in a controlled environment, such as a specially designed oven, and the final part of the process is allowing the material to cool back down.
Some plastics, like TORLON and ULTEM, benefit significantly from post-machining annealing. TORLON, for instance, can require more than seven days in special ovens for proper annealing. Additionally, plastics that undergo extensive machining, such as applications of PEEK, may need intermediate annealing steps to maintain tight tolerances and flatness.
The benefits of annealing high-performance plastics are notable. Clear plastics like polycarbonate and polysulfone can achieve improved chemical resistance, and annealing minimizes the occurrence of stress craze marks. Annealing also enhances the wear resistance of plastics like Torlon. By relieving residual stresses, annealing helps plastic parts conform to higher tolerances and improves their dimensional stability.
Plastic Consumption: Marine Life's Unhealthy Diet
You may want to see also
Residual stress: issues and causes
Residual stress in plastic parts is a significant issue that can lead to part failure or reduced performance. It is caused by the inherent internal stresses developed during the conversion of resins to finished parts or stock shapes through injection moulding. This process involves heating, pressures, and cooling, which can result in residual stresses that compromise the strength of a polymer part. Thin-walled parts, for example, tend to have higher residual stress as the polymer chains are frozen in a stretched-out or stressed state.
The problems caused by residual stress can be compounded by aggressive chemicals, leading to premature failure. Therefore, it is essential to relieve these stresses through a process called annealing, which involves heat treatment. Annealing reduces the hardness of the material and increases ductility, enhancing the mechanical and thermal properties of the plastic part. It is a controlled process where the polymer part is heated to a temperature slightly below its softening point, held at that temperature for a specific duration, and then allowed to cool slowly back to room temperature. The temperature and duration of the process depend on the type of plastic being annealed.
While annealing is a well-known method for relieving stress in plastics, it is important to maintain precise temperatures and timing control to achieve the desired results. Additionally, the use of vibration as a stress relief technique for plastics has been questioned, with most professionals stating that they have never encountered it. However, unintentional stress relief in acrylic can be achieved by wiping machined, stressed surfaces with isopropyl alcohol.
Overall, the issues and causes of residual stress in plastic parts are complex and require careful consideration during the design, moulding, fixturing, and part performance stages. By understanding and managing residual stress, manufacturers can improve the quality and longevity of their plastic products.
China's Plastic Waste Import: Who Pays the Price?
You may want to see also
Injection moulding: the process and its issues
Injection moulding is a manufacturing process that involves injecting molten material into a mould or mold. It is a highly versatile process that can be used to create precision parts with complex and intricate shapes in a variety of materials, including metals, glass, elastomers, and various plastics. The process is widely used in construction, engineering, and component parts manufacturing industries due to its quality finish and simple process.
The first step in injection moulding is mould-making. The mould is typically made of metal, such as steel or aluminium, and is precision-machined to form the features of the desired part. The mould can have either a single cavity or multiple cavities, which allow for the production of multiple parts in one injection cycle. Once the mould is designed and built, trials are performed to predict defects and determine the appropriate specifications for the injection process.
The injection moulding process begins with feeding raw plastic material, typically in the form of granules or pellets, into a hopper. The material is then heated to a highly molten state and injected under high pressure into the mould cavity. The molten plastic cools and solidifies, taking on the shape of the mould cavity. Finally, the moulded part is extracted from the mould and undergoes post-processing steps such as removing surplus material, finishing the surface, and heat treating, painting, or electroplating if necessary.
While injection moulding is a widely used and effective process, it does have some issues. One common problem is residual stress in the moulded parts, which can lead to part failures after the parts have been shipped and are in use. This stress can be relieved through a process called annealing, which involves heating the material above its recrystallization temperature to change its structure and make it easier to machine. Other issues with injection moulding include high initial costs due to mould tool expenses and long lead times due to the need for prototypes and iterations.
The World's Annual Garbage Production: A Startling Overview
You may want to see also
Machining: the role of temperature and tools
Machining is a process that involves the use of tools and equipment to cut, shape, and finish materials, such as metal or plastic, into desired shapes and sizes. The role of temperature and tools in machining, especially when it comes to relieving stress in plastic parts, is crucial and interconnected.
Plastic parts often experience internal or residual stress during the manufacturing process due to factors such as heating, cooling, pressures, and the use of certain tools. This stress can lead to part failure, reduced performance, warping, twisting, and other undesirable dimensional changes. Thus, stress-relieving techniques, such as annealing, are essential to improving the overall quality and longevity of the final product.
Annealing is a heat treatment process that helps to relieve stress in plastic parts. It involves slowly heating a plastic part to a temperature slightly below its softening point, holding it at that temperature, and then allowing it to cool slowly back to room temperature. This process reduces internal stress by changing the structure of the material, making it more ductile and uniform. The specific temperature and duration of the annealing process depend on the type of plastic being treated.
The use of proper tools during machining can also impact the amount of stress in plastic parts. For example, using dull or worn tools, drilling deep holes, uneven thickness reduction, and removing a significant volume of material can all contribute to residual stresses. Additionally, maintaining the temperature below the deformation point is crucial, especially when working with acrylic or other brittle plastics.
Furthermore, the choice of machining tools can influence the effectiveness of stress-relieving techniques. For instance, computer-controlled annealing ovens are used to precisely control the temperature and timing during the annealing process, ensuring the desired results. Additionally, tools such as polarizers can be used to visually detect internal stresses in transparent plastic materials by observing changes in refractive index and polarization.
The Cost of Plastic Veneers: How Much Do They Cost?
You may want to see also
The benefits of annealing high-performance plastics
Annealing is a process that treats high-performance plastics with heat to make them easier to machine. It involves heating the material above its recrystallization temperature and maintaining that heat for a specific amount of time. This changes the properties of the material, increasing ductility and reducing hardness, making it easier to work with.
Additionally, annealing can be used as an intermediate process before machining to relieve stress built up during the initial stages of processing. This is especially beneficial for parts that require high dimensional stability and must resist stress cracking during use. The process can also be applied to completed products to address internal stresses introduced during the injection molding process, such as uneven cooling and flow-induced orientation.
Furthermore, annealing improves the chemical and wear resistance of plastics. It also facilitates the movement of polymer chains, allowing them to align and pack more orderly into crystalline structures, which enhances their strength and stiffness. Annealing can be particularly useful for engineering plastics like ULTEM and TORLON, where proper annealing can require several days in special ovens.
The Ocean's Plastic Crisis: Every Minute Matters
You may want to see also
Frequently asked questions
Skimming or skim plastering is a method used to plaster a wall. It entails plastering with a thin coat and is usually applied to a wall with existing plaster to smoothen the surface area.
Residual stress in plastic parts can be relieved through the process of annealing. Annealing is a heat treatment that changes the properties of a material to make it easier to machine. It increases ductility and reduces hardness.
Skimming can improve the overall quality of a product by reducing the chances of cracking, warping, and twisting. It also enhances the mechanical and thermal properties of a material.