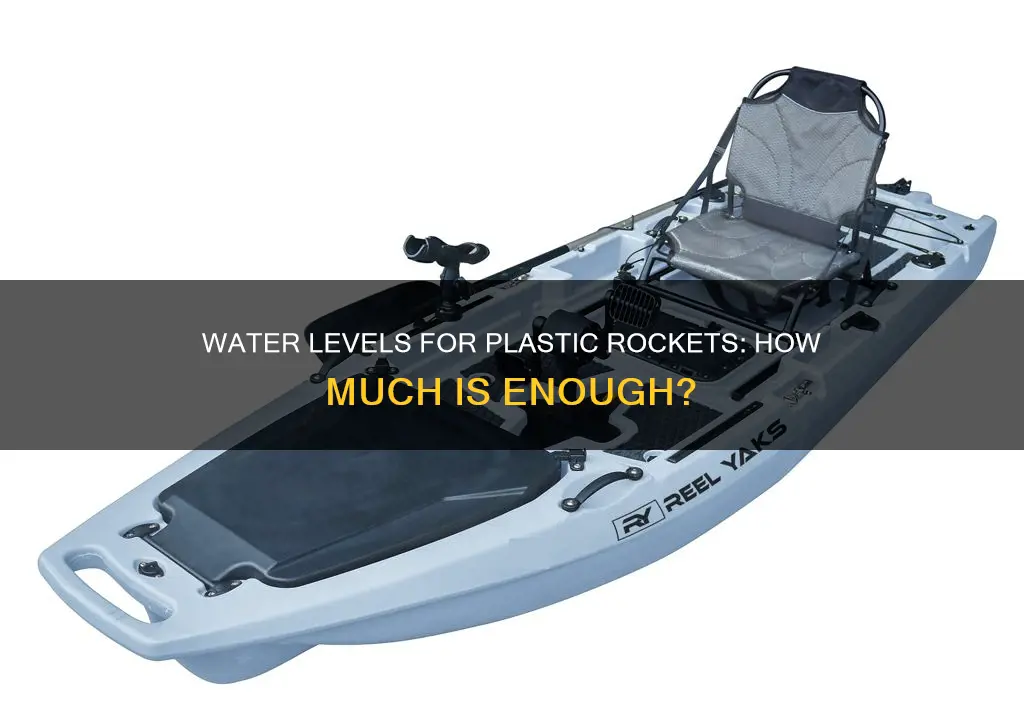
Water rockets are a fun and educational project, but how much water you should put in your plastic rocket is a tricky question. The amount of water and air in the rocket is a trade-off: too much water and it will be too heavy to accelerate and unstable; too little and it will run out of water too fast. The most effective water-air ratio is key to making your rocket soar. The water is propelled out of the rocket through a nozzle, so the nozzle design is also important.
How much water should you put in a plastic rocket?
Characteristics | Values |
---|---|
Water-to-air ratio | The most effective ratio is unknown, but it is important to avoid too much water, which will make the rocket too heavy to accelerate and lower its centre of mass, making it unstable. |
Bottle volume | 1.5 litres |
Pressure | 75 psi |
Nozzle design | The exit nozzle design is important as it determines the upwards force of the rocket. |
Water temperature | The rules for using hot water are unclear. |
Water-air ratio
The water-air ratio in a plastic rocket is a crucial factor in determining its performance and stability. The ratio needs to be carefully calibrated to ensure the rocket can achieve the desired height and direction while maintaining stability and structural integrity.
Firstly, it is important to understand the role of water in the rocket. Water acts as a propellant, providing the thrust necessary to launch the rocket skyward. When triggered, water is forced out of a hole in the cap, creating a propulsion system that propels the rocket upward. Therefore, the amount of water in the rocket directly impacts the force and duration of the thrust.
However, too much water can be detrimental. If the rocket has too much water, it may become too heavy to accelerate effectively. Additionally, an excessive amount of water can lower the centre of mass, making the rocket less stable during flight. On the other hand, too little water can cause the rocket to run out of propellant too quickly, resulting in a shorter flight time and reduced height.
To optimise the water-air ratio, several factors need to be considered. The volume and capacity of the bottle used for the rocket play a significant role. For example, a 1.5-litre bottle can typically handle a specific pressure requirement, such as 75 psi, without compromising its structural integrity. The weight of the rocket without water is also a critical factor in determining the optimal water-air ratio. Additionally, the design of the exit nozzle through which the water is expelled is crucial, as it determines the upward force and efficiency of the propulsion system.
In conclusion, achieving the ideal water-air ratio in a plastic rocket involves a delicate balance. It requires careful consideration of various factors, including bottle volume, pressure requirements, rocket weight, and nozzle design. By optimising these variables, one can maximise the performance, stability, and height of the rocket while ensuring a stable and efficient propulsion system.
The Ocean's Plastic Problem: An Environmental Crisis
You may want to see also
Cap diameter
The cap diameter of a plastic rocket is an important factor in determining the effectiveness of the water-air ratio and, consequently, the height the rocket will reach. A wider cap diameter will allow for a greater volume of water to be released when triggered, providing more propulsion and potentially increasing the height of the rocket. However, a larger cap diameter may also result in a faster release of water, causing the rocket to run out of water and propulsion earlier than desired.
On the other hand, a smaller cap diameter will release water at a slower rate, prolonging the propulsion and potentially increasing the duration of the rocket's flight. Nonetheless, a reduced volume of water exiting the cap with each trigger may result in decreased propulsion and a lower overall height.
The optimal cap diameter depends on several factors, including the desired water-air ratio, the pressure inside the rocket, and the exit nozzle design. A larger cap diameter may be advantageous if a higher water-air ratio is sought, as it allows for a greater volume of water to be released with each trigger. However, if the rocket operates at lower pressures, a smaller cap diameter might be preferable to maintain adequate propulsion while conserving water.
The exit nozzle design also plays a crucial role. A narrower exit nozzle will increase the upward force, and in this case, a larger cap diameter might be beneficial to ensure sufficient water volume is released with each trigger. Conversely, a wider exit nozzle may require a smaller cap diameter to prevent excessive water loss and maintain stability.
It is important to note that the stability of the rocket can be affected by the water level. If the rocket starts with too much water, it may become too heavy to accelerate efficiently and lower the centre of mass, making the rocket less stable. Therefore, when selecting the cap diameter, it is crucial to consider the potential impact on the water-air ratio and the overall stability of the rocket.
Recycling Efforts: How Much Plastic Really Gets Recycled?
You may want to see also
Exit nozzle design
The exit nozzle design of a rocket is critical to its performance and efficiency. The optimal nozzle design for a rocket engine is one where the exit pressure equals the ambient (atmospheric) pressure, which decreases with increasing altitude. This is because if the ambient pressure is higher than the exit pressure, the net thrust produced by the rocket decreases, and if it is lower, the thrust increases but fuel is wasted as the area ratio of the nozzle is not at its optimal level. Thus, the exit pressure of the nozzle should be at sea-level pressure when the rocket is near sea level, i.e. at takeoff. However, this nozzle design will quickly lose efficiency at higher altitudes, so for a multi-stage rocket, an overexpanded nozzle design is used for the second stage, which is more efficient at higher altitudes where the ambient pressure is lower.
The ratio of the area of the narrowest part of the nozzle (the throat) to the exit plane area is the primary factor in determining how efficiently the expansion of exhaust gases is converted into linear velocity and, therefore, the thrust of the rocket engine. The shape of the nozzle also has a modest impact on this efficiency. The nozzle's throat should have a smooth radius, and the exit angle should be as small as possible (about 12 degrees) to minimise separation problems at low exit pressures.
There are also more advanced nozzle designs, such as the single-expansion ramp nozzle (SERN) or a linear expansion nozzle, which allow the supersonic flow to adapt to the ambient pressure by expanding or contracting, thereby optimising the exit pressure for the corresponding altitude.
The exit pressure of the nozzle can be calculated using the De Laval exit velocity equation, which takes into account chamber pressure and temperature. The formula to calculate the exit exhaust velocity is:
$$V_e = \sqrt{\frac{TR}{M} \cdot \frac{2\gamma}{\gamma-1} \cdot \Biggl( 1- \bigg(\frac{P_e}{P}\bigg)^{(\gamma-1)/\gamma} \Bigg)}$$
Where:
- $V_e$ is the exhaust velocity
- $F$ is the force
- $T$ is the absolute temperature of the inlet gas
- $R$ is the universal gas constant
- $M$ is the molecular gas weight of the propellant
The Ocean's Plastic Crisis: 1950's Unseen Pollution
You may want to see also
Bottle volume
The volume of water in a plastic rocket bottle is crucial to its performance. If the bottle has too much water, it will be challenging to accelerate and will have a lower centre of mass, making it less stable. Conversely, if there is too little water, it will run out too quickly during the launch. Therefore, finding the optimal water volume is essential for a successful launch.
The ideal volume of water depends on various factors, including the size and weight of the bottle rocket, the desired altitude, and the pressure of the water. Experimenting with different volumes of water and observing the rocket's performance is one way to determine the optimal volume. Starting with a small amount of water and gradually increasing it while monitoring the rocket's stability and flight duration can help identify the ideal volume.
Another factor to consider is the ratio of water to air in the bottle. The water-to-air ratio affects the propulsion and stability of the rocket. A higher water volume can provide more propulsion but may require a larger bottle to maintain stability. On the other hand, a lower water volume can reduce the weight and increase stability but may result in shorter flight durations.
Additionally, the design of the exit nozzle plays a crucial role in determining the volume of water needed. The nozzle affects the upwards force and, consequently, the overall performance of the rocket. Different nozzle designs can impact the flow rate of water expelled from the bottle, influencing the rocket's acceleration and stability. Therefore, experimenting with various nozzle designs and water volumes can help optimise the rocket's performance.
In summary, finding the right bottle volume for a plastic rocket involves a balance between stability, propulsion, and flight duration. By considering factors such as bottle size, weight, desired altitude, and nozzle design, you can experiment with different water volumes to optimise the rocket's performance and achieve a successful launch.
Plastic Straws: How Much Do They Pollute Our Oceans?
You may want to see also
Water temperature
It is important to consider the water temperature when building a plastic rocket. While the water temperature in a plastic rocket is not explicitly stated, it is implied that the water should be at room temperature or warm. This is because the water is pressurised, and if the water were too hot, it could potentially affect the integrity of the plastic bottle. Additionally, the water should be at a temperature that allows it to be pressurised effectively.
Starting with an empty bottle and filling it with pressurised water is a recommended method. This ensures that the energy and reaction mass are in balance and run out simultaneously. It is important to note that the water will not expand, so the nozzle should not be designed to accommodate expansion. The water-to-air ratio is critical for optimising the rocket's height.
The amount of water in the rocket affects its stability. If there is too much water, the rocket may be too heavy to accelerate effectively, and its centre of mass will be lowered, making it less stable. Conversely, if there is too little water, it will run out too quickly, impacting the rocket's performance.
The ideal water-to-air ratio depends on factors such as the rocket's weight without water, the pressure (PSI), and the design of the exit nozzle. The exit nozzle is crucial as it determines the upwards force of the rocket. Therefore, the water temperature should be such that it can be pressurised effectively to achieve the desired PSI and work in conjunction with the exit nozzle design.
In summary, the water temperature in a plastic rocket should be considered in relation to the pressurisation process and the desired PSI. It should be at room temperature or warm to maintain the integrity of the plastic bottle and allow for effective pressurisation. The amount of water should be balanced to avoid affecting the rocket's stability and performance.
The Right Roof Overhang for Seamless Plastic Gutters
You may want to see also
Frequently asked questions
It is recommended to start with an empty bottle and fill it with pressurized water. This way, the energy and reaction mass run out simultaneously. However, if there is too much water, the rocket will be too heavy to accelerate and become less stable. On the other hand, too little water will cause the rocket to quickly run out of water.
The ideal water-air ratio depends on various factors, including the rocket's weight, cap diameter, and exit nozzle design. The exit nozzle is crucial as it determines the upwards force of the rocket.
It is unclear whether hot water would provide any benefits or drawbacks. It is recommended to check the rules and regulations of your specific competition or activity regarding the use of hot water in water-propelled rockets.