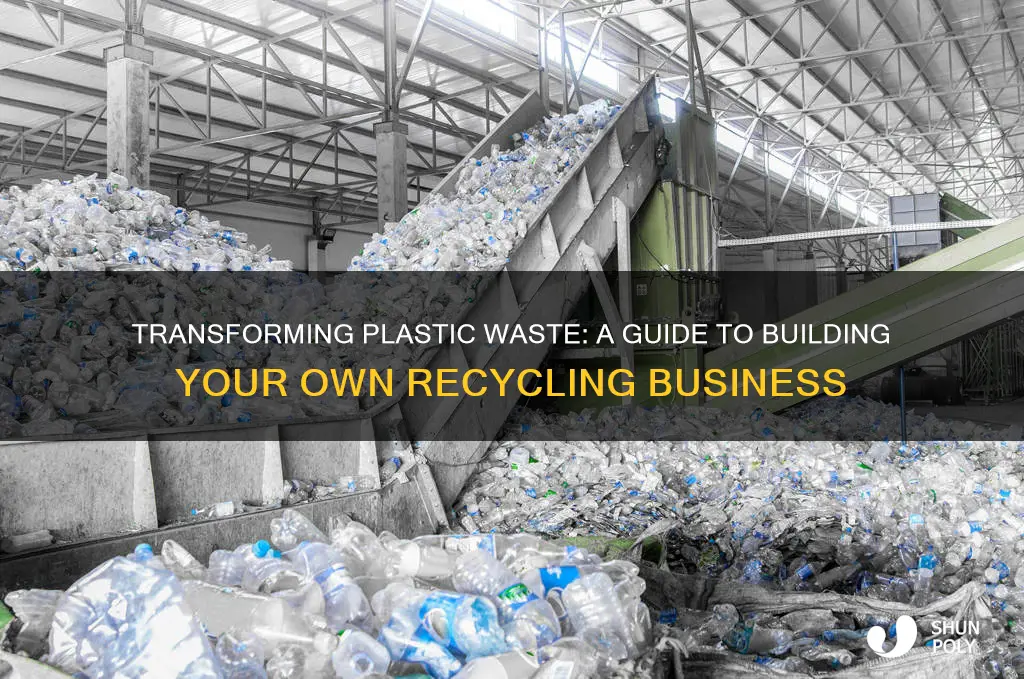
Creating a plastic recycling shop is a valuable venture that contributes to environmental sustainability. This guide will outline the essential steps to establish a successful plastic recycling business. It will cover the initial planning phase, including market research, identifying the target area, and securing the necessary permits and licenses. The process will then delve into the practical aspects, such as setting up a collection system, sourcing and sorting plastic materials, and implementing efficient recycling processes. Additionally, it will discuss marketing strategies to attract customers and promote the shop's services, ensuring a comprehensive approach to building a thriving plastic recycling enterprise.
What You'll Learn
- Source Materials: Identify and collect plastic waste from local sources
- Sorting: Implement a system to sort plastics by type and color
- Cleaning: Develop a process to clean and prepare plastic for recycling
- Milling/Grinding: Break down plastic into smaller pieces for processing
- Melting and Molding: Melt and mold plastic into new products
Source Materials: Identify and collect plastic waste from local sources
To establish a successful plastic recycling shop, the first crucial step is to identify and source plastic waste effectively. This involves a strategic approach to waste collection and management, ensuring a steady supply of raw materials for your recycling process. Here's a detailed guide on how to source plastic waste:
- Local Waste Management Facilities: Begin by contacting your local waste management authorities or recycling centers. These facilities often have a network for collecting various types of waste, including plastics. They can provide information on the types of plastic they accept and the collection schedules. Setting up regular collections from these sources ensures a consistent supply of plastic waste. For instance, you might arrange for weekly or bi-weekly pickups of plastic recyclables from the facility's drop-off points or designated collection areas.
- Community Engagement: Engage with your local community to raise awareness about plastic waste and encourage participation in recycling efforts. Organize events, such as neighborhood clean-up drives, where residents can bring their plastic waste. You can also set up collection points in public spaces, like parks or community centers, making it convenient for people to contribute. Providing clear guidelines on the types of plastic accepted and offering incentives for active participation can significantly boost your collection efforts.
- Industrial and Commercial Sources: Explore opportunities to collect plastic waste from local industries and businesses. Many manufacturing companies generate plastic scrap during production, which can be a valuable source of raw materials. Reach out to local factories, plastic manufacturers, or even grocery stores and supermarkets to establish partnerships. You can negotiate collection agreements, ensuring a regular supply of plastic waste from these sources. For example, you might collect plastic packaging, containers, or even discarded machinery parts from industrial sites.
- Residential Waste Streams: Target residential areas by collecting plastic waste from households. Many homeowners and renters are unaware of proper plastic waste segregation, leading to a mix of recyclables and non-recyclables in their trash. You can offer a collection service where residents separate their plastic waste and provide it to you. This approach not only ensures a steady supply but also educates the community about responsible waste management.
- Plastic Waste from Construction Sites: Construction and renovation projects generate a significant amount of plastic waste. Contact local construction companies, contractors, or building sites to collect their plastic scraps. This can include items like plastic pipes, insulation materials, or even discarded packaging. Establishing relationships with these sites can provide a consistent and diverse source of plastic waste.
By implementing these strategies, you can create a robust network for collecting plastic waste, ensuring that your recycling shop has a steady supply of source materials. This foundation is essential for the long-term success and sustainability of your plastic recycling business.
Australia's Plastic Recycling Journey: From Waste to New Life
You may want to see also
Sorting: Implement a system to sort plastics by type and color
Implementing an efficient sorting system is crucial for the success of your plastic recycling shop. Here's a detailed guide on how to set up an effective sorting process:
Design a Sorting Area:
- Dedicate a specific area in your shop exclusively for sorting. Ensure it's well-lit, spacious, and equipped with sturdy tables and shelves for organizing materials.
- Consider using color-coded bins or containers to visually separate different types of plastics. This makes the sorting process faster and more intuitive for your team.
Educate Your Staff:
- Provide comprehensive training to your employees on plastic identification. They should be able to distinguish between common plastic types (e.g., PET, HDPE, LDPE, PP, PS) based on their knowledge and visual aids.
- Create a simple reference guide or chart that outlines the characteristics of each plastic type, including color, shape, and common uses.
Sorting Techniques:
- Manual Sorting: Train your staff to manually separate plastics into categories. This involves using their hands and tools like tweezers or brushes to carefully pick up and place items into the appropriate bins.
- Conveyor Belt System: For higher volumes, consider installing a conveyor belt system with sensors. Sensors can detect the type of plastic and direct it to the correct bin, streamlining the process.
- Color Sorting: As mentioned earlier, color-coding is a powerful tool. Assign specific colors to different plastic types and consistently use those colors throughout your sorting area.
Implement Quality Control:
- Randomly sample items from the sorted piles and inspect them for accuracy. This ensures that the sorting system is functioning effectively and helps identify any potential issues.
- Encourage employees to be meticulous and consistent in their sorting efforts.
Continuous Improvement:
- Regularly review and evaluate your sorting system's performance. Analyze data on the types and quantities of plastics processed to identify areas for improvement.
- Stay updated on the latest advancements in plastic recycling technology and consider implementing new methods to enhance efficiency and accuracy.
Unveiling the Journey: From Circuit Boards to New Life
You may want to see also
Cleaning: Develop a process to clean and prepare plastic for recycling
Creating an efficient plastic recycling shop involves a meticulous cleaning process to ensure the quality and purity of the recycled materials. Here's a detailed guide on developing an effective cleaning procedure:
Sorting and Categorization: Begin by meticulously sorting the collected plastic waste. Different types of plastics have unique properties and recycling requirements. Separate plastics based on their resin identification codes (e.g., PET, HDPE, PVC) and color. This initial step is crucial as it allows for targeted cleaning and processing. For instance, dark-colored plastics may require different cleaning methods compared to clear or translucent ones.
Initial Cleaning: Implement a two-stage cleaning process. First, remove any non-plastic contaminants like labels, caps, or attached packaging. This can be done manually or with the help of specialized machines. After this initial separation, rinse the plastics to eliminate any remaining dirt, food residue, or chemicals. Use a high-pressure water spray or a mechanical washing system to ensure thorough cleaning. For particularly soiled items, consider using a detergent solution and a scrubbing process to break down and remove stubborn grime.
Advanced Cleaning Techniques: For a more comprehensive clean, employ advanced methods. This might include using ultrasonic baths, which utilize high-frequency sound waves to dislodge contaminants from the plastic's surface. Alternatively, chemical cleaning can be applied, where specific solvents or detergents are used to dissolve and remove impurities. The choice of cleaning agent depends on the type of plastic and the nature of the contamination. For instance, oils and greases might require a different approach than food-soiled plastics.
Drying and Quality Control: After cleaning, ensure the plastics are thoroughly dried to prevent moisture-related issues during the recycling process. Use air blowers or conveyer systems to remove excess water. Implement a quality control check at this stage to identify any remaining contaminants or damaged items. This step is vital to maintain the integrity of the recycled material.
Final Preparation: Once cleaned and dried, the plastics can be shredded or granulated, depending on the desired end product. This final preparation step ensures that the material is ready for the recycling machinery and meets the required specifications for the intended application.
Sweden's Plastic Recycling Revolution: A Green Nation's Guide to Waste Management
You may want to see also
Milling/Grinding: Break down plastic into smaller pieces for processing
Milling and grinding are essential processes in the recycling of plastic, as they enable the breakdown of larger plastic items into smaller, more manageable pieces, which is crucial for further processing and material recovery. This step is fundamental to the entire recycling chain, ensuring that the plastic can be effectively sorted, cleaned, and transformed into new products. Here's a detailed guide on how to approach this critical phase:
Equipment and Techniques:
- Milling: Milling machines, often referred to as granulators, are the primary tools for this process. These machines use rotating blades or rollers to shear and grind plastic materials. There are various types of granulators, including single-shaft, double-shaft, and three-shaft models, each designed for specific applications. For example, single-shaft granulators are suitable for softer plastics, while double-shaft granulators handle more challenging materials like polypropylene (PP) and high-density polyethylene (HDPE).
- Grinding: Grinders, often used in conjunction with mills, employ a different mechanism. They typically feature a rotating drum with sharp blades or teeth that tear and shred the plastic. Grinders are particularly effective for breaking down plastic waste into very fine particles, which is beneficial for producing plastic pellets or flakes.
- Screen Size: The size of the screen or mesh on the milling and grinding equipment is a critical factor. Smaller screen sizes result in finer particles, which are essential for certain applications. For instance, a 1/8-inch screen is commonly used for producing plastic pellets, while a 3/8-inch screen might be used for larger plastic flakes.
Process Overview:
- Collection and Sorting: Begin by collecting various plastic waste streams, ensuring they are sorted by type (e.g., PET, HDPE, PP) and color. This step is crucial for efficient milling and grinding.
- Cleaning: Plastic waste often contains contaminants like dirt, labels, and non-plastic materials. Cleaning is essential to remove these impurities, ensuring the quality of the recycled material. This can be done through washing, air separation, or other methods.
- Shredding (Optional): For some applications, especially when dealing with larger plastic items, a preliminary shredding step might be necessary. This reduces the size of the plastic before milling and grinding, making the subsequent processes more efficient.
- Milling and Grinding: Place the sorted and cleaned plastic into the milling machine. Adjust the machine settings, including speed and screen size, to achieve the desired particle size. For grinding, feed the plastic into the grinder, ensuring it's fed evenly to avoid overloading.
- Quality Control: Regularly check the output to ensure the plastic is milled or ground to the required specifications. This might involve using a sieve or screen to separate the desired particle size from the fines.
- Drying (if required): Depending on the application, dried plastic can be more desirable. After milling or grinding, the plastic may need to be dried to remove any remaining moisture, which can affect the final product's quality.
Safety and Maintenance:
- Always prioritize safety when operating milling and grinding equipment. Ensure proper ventilation, especially when dealing with certain plastics that may release fumes.
- Regular maintenance of the machines is essential to prevent breakdowns and ensure consistent performance. This includes cleaning, lubricating, and replacing worn-out parts.
By following these steps and utilizing the right equipment, you can effectively break down plastic into smaller pieces, setting the stage for successful plastic recycling and the creation of valuable, reusable materials.
The Evolution of Plastic Recycling: A Sustainable Revolution
You may want to see also
Melting and Molding: Melt and mold plastic into new products
The process of melting and molding plastic is a crucial step in creating new products from recycled materials. Here's a detailed guide on how to achieve this:
Melting Plastic:
Start by gathering the plastic waste you intend to recycle. Common types of plastic suitable for recycling include PET (polyethylene terephthalate), HDPE (high-density polyethylene), and PVC (polyvinyl chloride). Sort the plastic by type to ensure compatibility during the melting process. Clean and dry the plastic to remove any contaminants or debris. This step is essential to ensure the quality of the final product.
Use a specialized melting machine designed for plastic recycling. These machines can be purchased or rented, and they come in various sizes depending on your production scale. Load the sorted and cleaned plastic into the machine, ensuring it is in small, uniform pieces for even melting. The machine will heat the plastic to its melting point, which varies depending on the type of plastic. For example, PET typically melts around 250-270°C (482-518°F), while HDPE melts at a slightly lower temperature.
As the plastic melts, it will form a viscous liquid. Stir or agitate the molten plastic to ensure a homogeneous mixture, especially if you are recycling a mixture of different plastics. This step helps eliminate air bubbles and ensures the final product has a consistent quality.
Molding and Shaping:
Once the plastic is melted and well-mixed, it's time to shape it into new products. This is where your creativity and the choice of molds come into play. Here's a general process:
- Select Molds: Choose molds suitable for the type of product you want to create. Molds can be custom-made or purchased from suppliers, and they come in various shapes and sizes. Consider the complexity of the product and the desired quantity to determine the appropriate mold size.
- Prepare the Mold: Ensure the molds are clean and dry. You may need to apply a release agent to prevent the plastic from sticking to the mold.
- Pour and Pack: Carefully pour the molten plastic into the molds, filling them to the desired level. For more intricate shapes, you might need to use a vacuum former or a compression molding machine to ensure proper filling.
- Cooling and Setting: Allow the plastic to cool and set according to the mold manufacturer's instructions. This process solidifies the plastic, giving it its new shape.
- Eject and Finish: Carefully remove the molded product from the mold. You may need to use a mold release agent to ease the process. Post-processing techniques like trimming, sanding, or painting can be applied to achieve the final desired product.
Melting and molding plastic requires precision and attention to detail. It is an art and a science, allowing you to transform recycled plastic waste into valuable, usable products. This process is a key component of your plastic recycle shop, enabling you to create a sustainable and profitable business while reducing environmental impact.
Garland's Plastic Recycling: Unveiling the Truth Behind Number 6
You may want to see also
Frequently asked questions
The initial phase involves extensive market research and understanding the local demand for recycled plastic products. Identify the types of plastics that are commonly discarded in your area and assess the potential for creating a sustainable business.
Building a network with local businesses, manufacturers, and waste management companies is crucial. Establish partnerships to collect plastic waste, such as from construction sites, restaurants, or retail stores. You can also set up collection points in your community to encourage residents to donate their plastic waste.
Investing in specialized equipment is vital for efficient plastic recycling. This includes shredders, granulators, and washing lines to process and clean the plastic waste. You might also consider a color sorter to separate different types of plastics, ensuring a higher-quality end product.
Focus on creating a closed-loop system by finding local manufacturers or businesses that can utilize your recycled plastic products. Develop relationships with potential buyers and offer a consistent supply of high-quality recycled materials. Additionally, consider selling your products online or through local markets to reach a wider customer base.