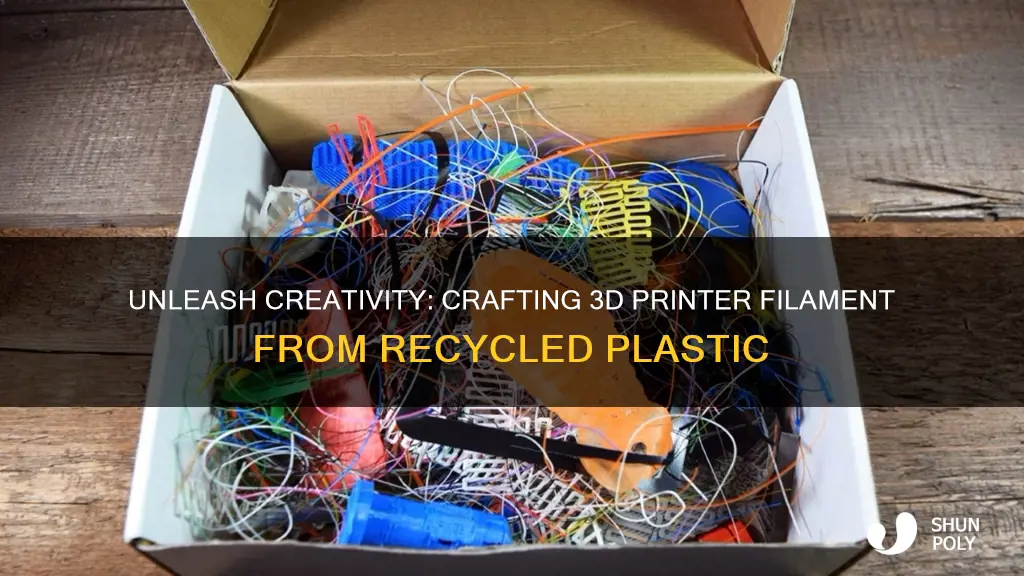
Creating 3D printer filament from recycled plastic is an eco-friendly and cost-effective way to contribute to sustainability while also allowing you to experiment with unique materials. This process involves breaking down used plastic items, cleaning and sorting them, and then extruding the plastic into a usable filament form. It's a fascinating journey that transforms waste into a valuable resource, offering a fun and educational experience for those interested in 3D printing and environmental conservation.
Characteristics | Values |
---|---|
Process Overview | Extrusion, Pelletizing, and Drying |
Materials | Recycled PET (Polyethylene Terephthalate), HDPE (High-Density Polyethylene), PLA (Polylactic Acid), ABS (Acrylonitrile Butadiene Styrene), and more |
Equipment | Extruder, Pelletizer, Dryer, and Cooling System |
Steps | 1. Collect and Sort Recycled Plastic 2. Clean and Shred the Plastic 3. Melt and Extrude the Plastic 4. Pelletize the Filament 5. Dry and Store the Filament |
Advantages | Reduces Plastic Waste, Cost-Effective, Customizable, and Environmentally Friendly |
Challenges | Material Compatibility, Filament Quality, and Consistency |
Tips | Use a Consistent Feed Rate, Maintain a Stable Temperature, and Experiment with Different Recycled Materials |
Applications | 3D Printing, Prototyping, and Customized Objects |
Safety Precautions | Wear Protective Gear, Ensure Proper Ventilation, and Follow Safety Protocols for Handling Hot Materials |
Environmental Impact | Minimizes Landfill Waste, Reduces Carbon Footprint, and Promotes Sustainable Practices |
What You'll Learn
- Sorting and Cleaning: Collect and sort plastic waste, then clean to remove contaminants
- Shredding and Granulating: Shred plastic into small pieces, then grind into fine granules
- Melting and Extrusion: Melt plastic, feed through extruder to create filament strands
- Cooling and Winding: Cool extruded filament, wind onto spools for storage
- Testing and Calibration: Test filament quality, calibrate printer settings for optimal performance
Sorting and Cleaning: Collect and sort plastic waste, then clean to remove contaminants
The first step in creating 3D printer filament from recycled plastic is meticulous sorting and cleaning of the plastic waste. This process ensures that the final product is of high quality and free from contaminants that could compromise the performance of the filament.
Begin by collecting various types of plastic waste, such as plastic bottles, containers, and packaging. It is crucial to separate these plastics by type to ensure compatibility during the filament-making process. Common types of plastic used in consumer products include PET (polyethylene terephthalate), HDPE (high-density polyethylene), and LDPE (low-density polyethylene). Each type has unique properties and melting points, so proper sorting is essential. For instance, PET is commonly used in beverage bottles and has a higher melting point compared to LDPE, which is often found in grocery bags.
Once sorted, the next step is to clean the plastic to remove any contaminants. This includes washing the plastic items to eliminate dirt, labels, and any remaining liquids. Use a gentle detergent and warm water to ensure effective cleaning without damaging the plastic. Rinse the items thoroughly to remove any soap residue, and allow them to air dry completely. This step is critical as contaminants can affect the filament's strength and appearance. For example, food residue or labels can leave a sticky residue, while dirt and grime can cause imperfections in the final filament.
After cleaning, it is beneficial to further process the plastic to ensure it is in a consistent and usable form. This may involve shredding or grinding the plastic into small pieces, ensuring a uniform size. This step helps in removing any remaining contaminants and prepares the plastic for the next stage of filament production.
Proper sorting and cleaning are fundamental to the success of creating high-quality 3D printer filament from recycled materials. These steps ensure that the raw materials are compatible, clean, and ready for the subsequent processes of extrusion and cooling, ultimately resulting in a reliable and consistent filament for 3D printing applications.
Unleash the Green Thumb: Can Plastic Pots Be Recycled?
You may want to see also
Shredding and Granulating: Shred plastic into small pieces, then grind into fine granules
To begin the process of creating 3D printer filament from recycled plastic, you'll need to start with the raw material and perform some initial processing steps. Shredding and granulating are crucial processes that transform larger plastic items into a usable form for filament production.
The first step is shredding, which involves breaking down the plastic into small, manageable pieces. This can be done using a shredder or a similar machine designed for this purpose. The goal is to reduce the size of the plastic items significantly, creating a consistent and uniform shredded material. Different types of plastic require varying shredding techniques; for example, PET bottles might need a more aggressive shredding process compared to HDPE containers. Ensure that the shredded plastic is clean and free from any contaminants to maintain the quality of the final product.
After shredding, the plastic is then granulated. Granulating is the process of further reducing the shredded plastic into even smaller particles, typically in the form of fine granules. This step is crucial as it prepares the plastic for the next phase, where it will be heated and extruded into filament. A granulator machine can be used to grind the shredded plastic into the desired granule size. The granulation process should be precise to ensure that the granules are consistent in size and shape, which is essential for the subsequent filament production.
It's important to note that the shredding and granulating process should be tailored to the specific type of plastic being used. Different plastics have unique properties, and adjusting the shredding and granulating parameters accordingly will result in a higher-quality filament. For instance, some plastics may require a more extensive shredding process to break down their molecular structure, while others might benefit from a more gentle approach to retain their inherent strength.
By following these steps, you'll have transformed recycled plastic into a usable form, ready for the next stage of filament creation, which involves heating and extrusion. This process will ultimately result in custom-made 3D printer filament, allowing you to utilize recycled materials in your 3D printing projects.
Transforming Plastic Waste: Recycling and Molding Techniques for a Greener Future
You may want to see also
Melting and Extrusion: Melt plastic, feed through extruder to create filament strands
The process of creating 3D printer filament from recycled plastic involves several key steps, with melting and extrusion being central to the manufacturing process. This method allows for the transformation of plastic waste into a usable material for 3D printing. Here's a detailed guide on how to achieve this:
Melting the Plastic: The first crucial step is to melt the recycled plastic. You can use various methods for this, such as a hot-air gun, a heat gun, or a dedicated plastic melting machine. The goal is to heat the plastic until it reaches its melting point, which varies depending on the type of plastic. For example, PET (polyethylene terephthalate) has a melting point of around 255°C (480°F), while ABS (acrylonitrile butadiene styrene) melts at approximately 230°C (446°F). It's essential to monitor the temperature carefully to ensure the plastic doesn't burn or degrade. Once melted, the plastic should be clear and homogeneous, indicating it's ready for the next stage.
Preparing the Extruder: An extruder is a critical component in this process, responsible for pushing the melted plastic through a die to create the filament strands. You can either build your own extruder or purchase a pre-made one suitable for your needs. The extruder should be able to handle the specific plastic type you're using. It typically consists of a heating element, a gear motor, and a barrel to hold the melted plastic. Ensure the extruder is properly calibrated and heated to the required temperature for the chosen plastic.
Extrusion Process: With the plastic melted and the extruder prepared, you can now begin the extrusion. Load the melted plastic into the extruder's barrel, ensuring it's centered and secure. Start the extruder and adjust the temperature if necessary. The motor will push the plastic through the die, which has a specific diameter and shape to determine the filament's dimensions. As the plastic exits the die, it will start to cool and solidify, forming a strand of filament. This strand will be fed through a winder or a take-up mechanism to collect the filament as it's produced.
Cooling and Winding: After the extrusion, the filament strand needs to cool rapidly to maintain its shape. This can be achieved by using a cooling fan or a water-cooled system. Once cooled, the filament is ready for use in a 3D printer. It's essential to wind the filament onto a spool or a suitable container to prevent tangling and ensure it remains organized.
This process allows for the creation of custom-colored and textured filaments, offering a sustainable and cost-effective solution for 3D printing enthusiasts. By following these steps, you can effectively transform recycled plastic into high-quality 3D printer filament.
India's Plastic Recycling Landscape: Unveiling the Growing Number of Companies
You may want to see also
Cooling and Winding: Cool extruded filament, wind onto spools for storage
Once the extruded filament is ready, the next crucial step is cooling and winding it onto spools for storage and future use. Proper cooling is essential to ensure the filament's stability and quality. After extrusion, the hot filament needs to be rapidly cooled to prevent it from becoming too malleable or losing its shape. This can be achieved using various cooling methods. One common approach is to direct a steady stream of cool air or even liquid nitrogen onto the extruded filament. This rapid cooling solidifies the plastic, making it rigid and easier to handle. It's important to maintain a consistent cooling temperature and airflow to avoid any warping or distortion.
When the filament is sufficiently cooled, it becomes pliable and can be wound onto spools. This process requires precision and care to ensure a neat and organized final product. Start by carefully unwinding the extruded filament from the extruder, being mindful of the direction of the unwinding to maintain its integrity. Then, gently guide the filament onto the spool, ensuring it is wound tightly and evenly. Over-tightening can cause the filament to break, while under-tightening may lead to tangling. A good practice is to wind the filament in a consistent direction, either clockwise or counterclockwise, to create a neat coil.
As you wind the filament, it's beneficial to use a mandrel or a cylindrical object to guide the process. This helps in maintaining a straight and uniform diameter for the filament. The spool should be securely attached to a flat surface to prevent any accidental unwinding. Once the filament is wound onto the spool, it's ready for storage. Ensure that the spool is kept in a dry and controlled environment to avoid moisture absorption, which can affect the filament's performance.
Proper cooling and winding techniques are vital to producing high-quality 3D printer filament from recycled plastic. These steps ensure that the filament is stable, free from defects, and ready for use in 3D printing applications. By following these instructions, you can create a reliable and consistent filament production process, contributing to the growing sustainability of 3D printing.
Apple Sauce, Plastic Dilemma: Recycling or Not?
You may want to see also
Testing and Calibration: Test filament quality, calibrate printer settings for optimal performance
When you've produced your own 3D printer filament from recycled plastic, the next crucial step is to ensure its quality and optimize the printing process. This involves a combination of testing and calibration techniques to guarantee consistent and high-quality prints. Here's a detailed guide on how to approach this:
Testing Filament Quality:
- Visual Inspection: Start by examining the filament for any visible defects. Look for signs of contamination, such as dirt, debris, or color inconsistencies. Check for any voids or bubbles that might affect the filament's strength. Ensure the filament is free from any sharp bends or kinks, as these can lead to feeding issues during printing.
- Diameter and Consistency: Measure the filament's diameter using a micrometer. Consistent diameter is crucial for proper feeding and to avoid jams. Also, check for any variations in the filament's cross-section, as this can impact the print quality.
- Material Testing: Perform material tests to assess the filament's properties. Use a material tester or a simple tensile test to measure its strength, flexibility, and elasticity. Compare these results with the desired specifications to ensure your filament meets the required standards.
- Burn Test: Conduct a burn test to check for any potential hazards. Burn a small sample of the filament and observe the flame and smoke produced. This test can help identify any flammable or toxic components in the recycled plastic.
Calibration and Printer Settings:
- Calibrate Nozzle: Adjust the nozzle temperature and flow rate settings. Start with a lower temperature and gradually increase it while monitoring the filament's behavior. Ensure the filament melts smoothly and exits the nozzle without clogging. Fine-tune the flow rate to achieve a consistent extrusion.
- Bed Adhesion: Calibrate the bed adhesion settings. Adjust the bed temperature and surface treatment to ensure the filament adheres properly. A well-calibrated bed will prevent warping and improve print quality.
- Layer Height and Infill: Test different layer heights and infill percentages to find the optimal settings. Print test cubes or samples with varying layer heights and infill to observe the structural integrity and appearance. Adjust these settings to achieve the desired balance between print speed, strength, and aesthetics.
- Retraction Settings: Configure the retraction settings to manage the filament's behavior during printing. Adjust the retraction distance and speed to prevent oozing and ensure smooth filament feeding.
- Calibrate Sensors: If your printer has sensors for filament detection, calibrate them. This ensures that the printer knows when to load new filament and when to stop printing when the filament runs out.
By thoroughly testing and calibrating your filament and printer settings, you can achieve consistent and high-quality 3D prints. This process allows you to fine-tune the printing parameters, ensuring that your recycled plastic filament performs optimally in various applications. Remember, calibration is an iterative process, and you may need to make adjustments based on the specific characteristics of your filament and printer.
The Surprising Journey of Recycled Plastic: Landfill or New Life?
You may want to see also
Frequently asked questions
Common plastics like PET (polyethylene terephthalate), HDPE (high-density polyethylene), and PLA (polylactic acid) are excellent choices. PET bottles and HDPE milk jugs are widely used for this purpose.
Start by cleaning and sorting the plastic waste. Remove any contaminants like labels or caps. Then, shred or grind the plastic into small pieces, ensuring a consistent size for better processing.
You'll need a single-screw extruder, which can be a modified 3D printer or a dedicated extruder machine. This equipment will melt and push the plastic through a die to create the filament.
While it's possible to experiment with printing filament on a 3D printer, it's not the most efficient method for large-scale filament production. Dedicated extruder machines are generally preferred for consistent results.
Maintain a clean workspace and use high-quality plastic pellets for better results. Calibrate your extruder regularly, and consider using a heated bed to ensure the plastic doesn't cool too quickly during the extrusion process.