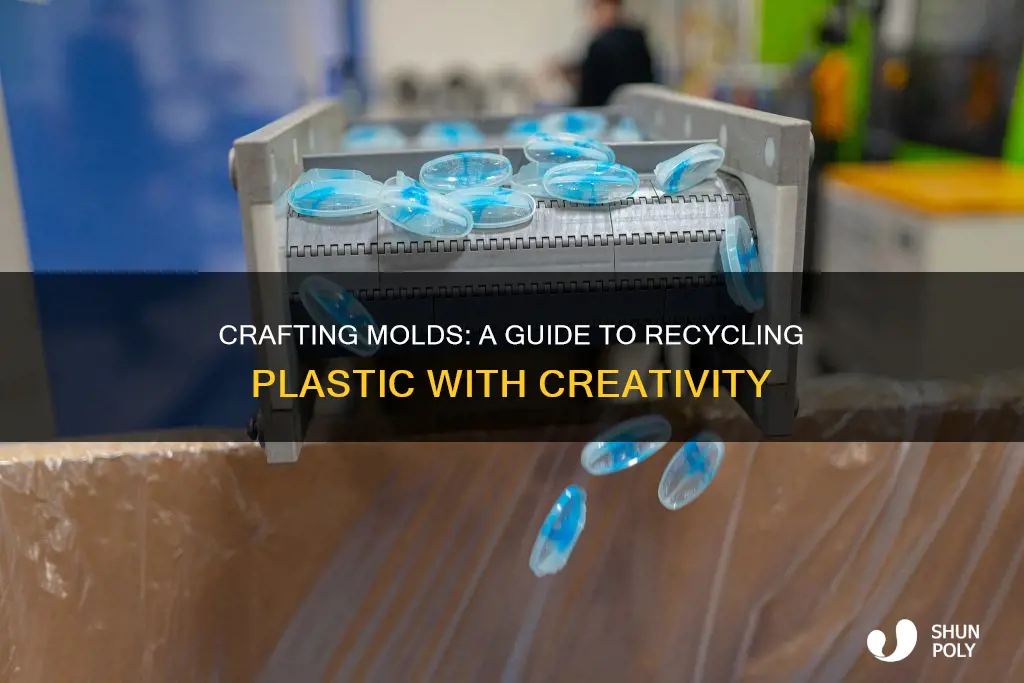
Creating molds for recycling plastic products is an innovative way to promote sustainability and reduce waste. This process involves designing and crafting reusable templates that can be used to shape and form recycled plastic into new products. By making molds, you can transform discarded plastic items into valuable resources, such as furniture, garden decorations, or even new packaging. This method not only reduces the environmental impact of plastic waste but also encourages a circular economy, where materials are reused and repurposed, creating a more sustainable future.
What You'll Learn
- Design and Planning: Create a blueprint for your mold, considering material and structural integrity
- Material Selection: Choose appropriate materials for your mold, considering cost, durability, and ease of use
- Casting Techniques: Explore various casting methods like injection, compression, or vacuum molding for optimal results
- Demolding and Finishing: Learn techniques to safely remove the plastic part from the mold and refine its surface
- Maintenance and Repair: Understand how to maintain and repair molds to extend their lifespan and ensure consistent quality
Design and Planning: Create a blueprint for your mold, considering material and structural integrity
When designing a mold for recycling plastic products, it's crucial to prioritize both material and structural integrity to ensure the process is efficient and the final product is of high quality. Here's a detailed guide on how to create a blueprint for your mold:
- Define the Product and Material: Start by clearly understanding the plastic product you aim to recycle. Consider its shape, size, and the specific type of plastic it is made from. Different plastics have varying melting points and properties, so selecting the right material for your mold is essential. For instance, if you're recycling PET (polyethylene terephthalate), you'll need to choose a mold material that can withstand the temperature and chemical properties of this plastic.
- Blueprint Creation: Begin sketching or using computer-aided design (CAD) software to create a detailed blueprint. This step involves translating your vision into a technical drawing. Include precise measurements and specifications for the mold's dimensions, including the cavity and core areas where the plastic will be injected. Ensure that the design accounts for the desired thickness of the recycled product and any specific features or textures you want to incorporate.
- Consider Mold Construction: Decide on the type of mold construction, which can be categorized as permanent, semi-permanent, or disposable. Permanent molds are durable and reusable, making them suitable for high-volume production. Semi-permanent molds offer some reusability but may require adjustments. Disposable molds are cost-effective but less durable. Choose the construction method based on your project's requirements and budget. For instance, if you're recycling small, intricate parts, a disposable mold made from foam or wax might be suitable.
- Drafting and Engineering: Pay close attention to the engineering aspects of your design. This includes designing the mold's cooling system, which is vital for controlling the cooling rate of the injected plastic. Proper cooling ensures the material solidifies evenly, preventing warping or defects. Additionally, consider the mold's ejection system, which should facilitate the easy release of the recycled product without causing damage. Drafting and engineering software can assist in creating these intricate details.
- Material Selection: The choice of mold material is critical for long-term success. Common mold-making materials include aluminum, steel, and various types of plastics. Consider factors such as cost, durability, and ease of manufacturing. For instance, aluminum molds are lightweight and offer good thermal conductivity, making them suitable for low-volume production. Steel molds provide excellent strength and durability, ideal for high-volume recycling operations.
- Testing and Iteration: Mold design is an iterative process. After creating your blueprint, it's essential to test and refine your mold. Build a prototype and conduct trials to identify any issues, such as poor material flow, warping, or difficulty in ejection. Use these insights to make necessary adjustments to your design and repeat the testing process until you achieve the desired results.
By following these steps and paying meticulous attention to design and planning, you can create a robust mold for recycling plastic products, ensuring efficient production and high-quality outcomes. Remember, a well-designed mold is the foundation for successful plastic recycling and manufacturing.
Mr. Coffee Pots: Glass, Plastic, and Recycling Options
You may want to see also
Material Selection: Choose appropriate materials for your mold, considering cost, durability, and ease of use
When it comes to creating molds for recycling plastic products, the choice of materials is a critical aspect that can significantly impact the success and efficiency of your project. Here's a detailed guide on material selection, focusing on cost, durability, and ease of use:
Plastic Materials:
- Acrylic (PMMA): Acrylic is a popular choice for mold-making due to its transparency, ease of casting, and reasonable cost. It offers good detail reproduction and is relatively easy to work with. However, it may not be as durable as some other options.
- Polyethylene (PE): PE is a versatile and cost-effective material. It is commonly used for disposable molds and can handle a wide range of temperatures. Its ease of use makes it ideal for beginners.
- Polypropylene (PP): PP is known for its excellent durability and impact resistance. It is often used in injection molding and can withstand high temperatures. While it might be more expensive, its longevity makes it a valuable investment.
- Silicone Rubber: Silicone is a versatile material that provides excellent detail reproduction and flexibility. It is ideal for creating reusable molds and can withstand various temperatures. The initial cost might be higher, but its durability and reusability make it a cost-effective long-term solution.
Considerations for Material Selection:
- Cost: Evaluate your budget and choose materials accordingly. Acrylic and PE offer more affordable options, while PP and silicone provide higher-end solutions.
- Durability: Consider the expected lifespan of your mold. If you plan to reuse the mold multiple times, opt for durable materials like PP or silicone. For one-time use or prototyping, acrylic or PE might suffice.
- Ease of Use: Assess your skill level and the complexity of the mold design. Materials like acrylic and PE are user-friendly and require less technical expertise. Silicone, while versatile, may demand more practice for precise casting.
Additional Tips:
- Experiment with different materials to find the best fit for your specific recycling project.
- Consider the type of plastic you are recycling and its compatibility with various mold materials.
- For intricate designs, you might want to invest in a more durable material to ensure the mold's longevity.
- Always test and refine your mold design to optimize the material choice.
Recycling Plastic Utensils in NYC: What You Need to Know
You may want to see also
Casting Techniques: Explore various casting methods like injection, compression, or vacuum molding for optimal results
When it comes to recycling plastic products and creating molds, understanding different casting techniques is crucial for achieving optimal results. Here's an exploration of various casting methods:
Injection Molding: This is one of the most common and versatile casting techniques. It involves injecting molten plastic into a mold cavity under high pressure. The process begins with heating the plastic material to its melting point, then it is fed into a barrel with a plunger. The plunger pushes the plastic through a nozzle, which is then directed into the mold. Once the plastic solidifies, it is ejected from the mold, creating the desired shape. Injection molding is highly efficient and can produce intricate and complex parts with high precision. It is widely used for mass production due to its ability to handle large volumes and a wide range of materials. To create molds for recycling, you can design the mold with specific cavities to replicate the desired plastic product. The process requires precise control of temperature, pressure, and injection speed to ensure proper filling and minimal defects.
Compression Molding: This technique is often used for producing solid, symmetrical parts with a uniform thickness. In compression molding, the plastic material is placed in a mold cavity and then compressed under heat and pressure. The mold is typically a two-part assembly, with the plastic material placed between the two halves. The mold is then closed, and the plastic is heated and compressed simultaneously, causing it to flow and fill the cavity. After cooling, the part is ejected from the mold. Compression molding is advantageous for creating large, flat, or sheet-like products. For recycling, you can design molds with specific dimensions to replicate the recycled plastic's intended form. This method is particularly useful for producing items like phone cases, tablet covers, or decorative panels.
Vacuum Molding (Vacuum Forming): This casting technique utilizes the power of suction to shape plastic sheets. It starts with a flat sheet of plastic, which is heated to make it pliable. The heated sheet is then placed over a mold, and a vacuum is applied to suction the plastic onto the mold's surface. This process allows the plastic to conform to the mold's shape. Once cooled, the plastic part is removed from the mold. Vacuum molding is excellent for producing hollow or slightly textured items. For recycling, you can create molds with specific contours to replicate the desired recycled plastic product's shape. This method is commonly used for manufacturing items like signs, packaging, and even automotive components.
Each casting technique offers unique advantages and is chosen based on the specific requirements of the project. Injection molding provides precision and versatility, compression molding is suitable for uniform parts, and vacuum molding excels at shaping hollow items. Understanding these methods will enable you to select the most appropriate technique for your recycling endeavor, ensuring optimal results in creating molds for recycled plastic products.
Unveiling the Plastic Truth: Recycled Food for Animals
You may want to see also
Demolding and Finishing: Learn techniques to safely remove the plastic part from the mold and refine its surface
Demolding is a critical step in the process of creating recycled plastic products, as it involves safely extracting the plastic component from the mold without causing damage to either the part or the mold itself. This process requires careful planning and execution to ensure the quality and integrity of the final product. Here are some techniques to guide you through demolding and finishing:
- Choose the Right Mold Release Agent: Prior to pouring the plastic, select a suitable mold release agent that will facilitate easy demolding. Silicone-based release agents are commonly used as they provide excellent lubrication and can withstand the high temperatures involved in plastic molding. Apply a thin, even layer of the release agent to the mold surfaces to ensure the plastic part can be released without sticking.
- Allow Adequate Cooling Time: After the plastic is poured and the mold is closed, allow sufficient time for the material to cool and solidify. The cooling time will depend on the type of plastic and the mold design. Ensure the mold is not overfilled, as this can lead to excessive pressure and potential damage during demolding. Proper cooling ensures that the plastic part is firm enough to handle without warping or breaking.
- Demolding Techniques: When the plastic part is ready, carefully open the mold to initiate the demolding process. Here are a few methods:
- Slow and Gentle: Carefully pry the mold apart, starting from the edges of the part, using a flat-edged tool or a knife. Work slowly to avoid applying excessive force, which can distort the part.
- Tap and Turn: If the part is still slightly tacky, gently tap the mold to loosen any remaining material. Then, carefully turn the mold to release the part from the bottom or side release tabs.
- Heating the Mold: In some cases, gently heating the mold can make demolding easier, especially with more rigid plastics. Use a heat gun or a hairdryer on a low setting, applying heat to specific areas to soften the plastic slightly before attempting to release it.
- Post-Demolding Inspection: Once the plastic part is free from the mold, inspect it for any defects or imperfections. Check for warping, flashing (excess material), or any damage caused during the demolding process. Use a sharp knife or a fine-grit file to smooth out any rough edges or surfaces.
- Finishing and Refinement: To refine the surface of the plastic part, consider the following:
- Sandblasting: This process involves propelling small abrasive particles onto the surface to remove imperfections and create a smooth finish. Sandblasting can be particularly useful for removing mold marks and creating a consistent surface.
- Chemical Polishing: Certain chemicals can be used to polish and smooth plastic surfaces. This method is often used for high-precision applications and can provide a mirror-like finish.
- Heat Bending: For curved or shaped parts, heat bending can be employed to refine the surface. Apply heat to specific areas and gently bend the part to the desired shape, allowing it to cool and set in the new position.
Remember, demolding and finishing require practice and precision to master. Take your time, and always prioritize safety when handling sharp tools and heated materials. With these techniques, you can produce high-quality recycled plastic products while ensuring the longevity of your molds.
Unraveling the Mystery: Can Plastic Detergent Containers Be Recycled?
You may want to see also
Maintenance and Repair: Understand how to maintain and repair molds to extend their lifespan and ensure consistent quality
Maintaining and repairing molds is crucial for ensuring the longevity of your recycling process and maintaining product quality. Here's a guide to help you understand the process:
Regular Cleaning and Inspection: Start by implementing a rigorous cleaning routine. After each use, thoroughly clean the molds using a mild detergent and warm water. This prevents the buildup of plastic residue, which can harden over time and affect the mold's performance. Pay close attention to intricate details and hard-to-reach areas. Regularly inspect the molds for any signs of wear and tear, including cracks, chips, or warping. Early detection can prevent further damage and costly repairs.
Preventative Maintenance: Taking preventative measures is key to mold longevity. Apply a thin layer of a suitable mold release agent to the mold's surface before each use. This reduces friction and prevents plastic buildup, making it easier to remove the finished product. Additionally, consider using a mold conditioner to maintain the flexibility and integrity of the mold material. Conditioners can help prevent cracking and ensure the mold's durability over multiple cycles.
Repair Techniques: When repairs are necessary, act promptly to minimize further damage. For minor cracks, use a specialized epoxy resin to fill and seal the defect. Ensure the resin is compatible with the mold material and follow the manufacturer's instructions for application. For more significant damage, consider replacing the affected part or section of the mold. This might involve removing the broken piece, cleaning the area, and then carefully reattaching or replacing it with a new, identical part.
Heat and Pressure Management: Molds often experience heat and pressure during the recycling process. Monitor and control these factors to prevent warping or distortion. Use a controlled heating system and ensure the molds are properly insulated to maintain a consistent temperature. Apply pressure evenly and avoid excessive force, especially when dealing with delicate or intricate designs.
Regular Calibration: Calibrate your molds periodically to ensure precision and consistency. This process involves adjusting the mold's dimensions and alignment to match the desired product specifications. Use precision measuring tools and compare them against a known standard. Regular calibration will help maintain the mold's accuracy and reduce the risk of producing defective products.
Kohl's Plastic Hanger Recycling: A Green Initiative for a Sustainable Future
You may want to see also
Frequently asked questions
The choice of material depends on the specific application and the type of plastic you are working with. Common materials for molds include aluminum, steel, and silicone rubber. Aluminum and steel molds are durable and can withstand high temperatures, making them suitable for injection molding or blow molding. Silicone rubber molds are flexible and ideal for creating intricate shapes, especially when you need to demold delicate parts.
Designing a mold for recycling plastic bottles involves considering the specific requirements of the process. First, you need to determine the desired output, such as the size and shape of the recycled plastic pieces. Then, create a mold cavity that matches the shape of the plastic bottle, ensuring it has the necessary drainage or ejection systems. Consider using a 3D modeling software to design the mold, allowing for precise adjustments.
To achieve high-quality recycled plastic products, follow these tips:
- Use high-quality, clean plastic materials to minimize impurities.
- Ensure proper cooling and curing of the plastic in the mold to avoid defects.
- Implement a rigorous cleaning process for the mold to remove any residual plastic or contaminants.
- Regularly maintain and inspect the mold to identify and fix any issues promptly.
- Test the recycled products for strength and durability to ensure they meet the required standards.