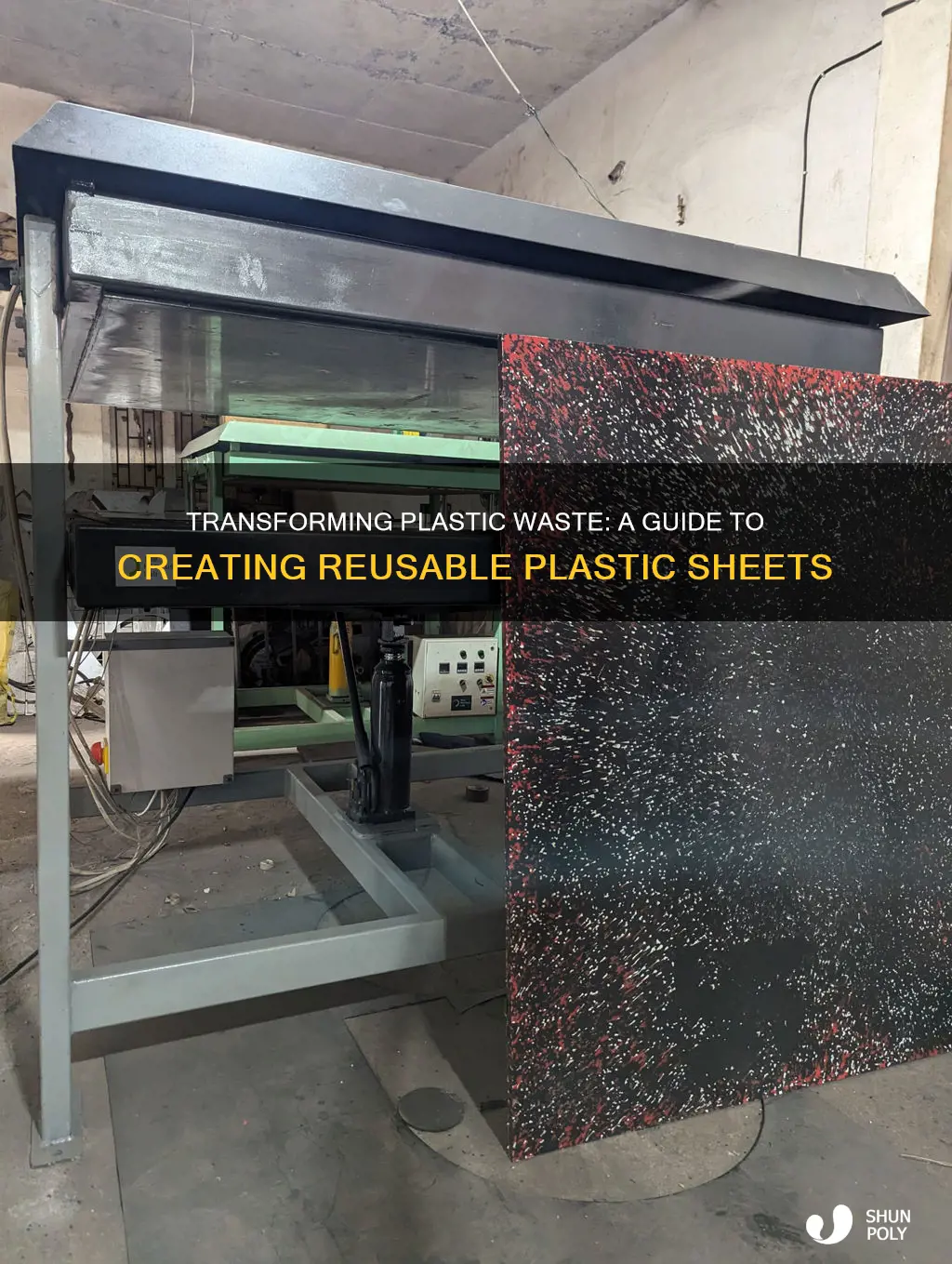
Creating plastic sheets from recycled plastic is an eco-friendly process that reduces waste and promotes sustainability. This method involves collecting and sorting plastic waste, which is then cleaned and shredded into small pieces. These pieces are melted and formed into sheets through a process called extrusion. The sheets can be used for various applications, such as packaging, construction, and furniture, offering a cost-effective and environmentally conscious alternative to traditional plastic production. This process not only reduces the demand for virgin plastic but also helps in conserving natural resources and minimizing the environmental impact of plastic waste.
What You'll Learn
Collection: Gather and sort plastic waste for recycling
The first step in the process of creating plastic sheets from recycled plastic is the collection and sorting of plastic waste. This initial phase is crucial as it sets the foundation for the entire recycling process and ensures the quality of the final product. Here's a detailed guide on how to effectively gather and sort plastic waste for recycling:
Collection: Begin by establishing a comprehensive collection system. This involves setting up designated bins or containers in various locations where plastic waste is generated. Common sources of plastic waste include households, offices, schools, and public spaces. Encourage people to separate their plastic waste into different categories, such as bottles, containers, packaging, and film plastics. Providing clear guidelines and educational materials can help ensure proper waste segregation. For instance, you can distribute colorful posters or flyers that illustrate which plastics are recyclable and how to prepare them for recycling.
Public Awareness and Engagement: Educating the community about the importance of proper waste management is essential. Organize awareness campaigns, workshops, or community events to emphasize the environmental impact of plastic waste and the benefits of recycling. By engaging the public, you can foster a sense of responsibility and encourage active participation in the recycling process. Consider distributing reusable bags or containers with recycling instructions to promote a habit of proper waste disposal.
Sorting Process: Once the plastic waste is collected, the next step is to sort it efficiently. Set up a sorting area with different stations or bins for various types of plastics. Common types of plastics used in packaging include PET (polyethylene terephthalate), HDPE (high-density polyethylene), PVC (polyvinyl chloride), LDPE (low-density polyethylene), and PP (polypropylene). Provide sorting guidelines and training to volunteers or staff to ensure accurate categorization. For example, PET bottles can be identified by their resin identification code (a triangle with a number inside) and HDPE containers by their stiffness and feel.
Manual Sorting Techniques: Manual sorting is often employed to ensure accuracy and efficiency. Train volunteers or staff to identify different types of plastics by their appearance, texture, and feel. For instance, PET bottles are lightweight and translucent, while HDPE containers are stiffer and often used for milk or detergent bottles. PVC might feel slightly different due to its chemical composition. Encourage the use of gloves to handle plastics and ensure a clean sorting process.
Advanced Sorting Methods: For larger-scale operations, consider implementing advanced sorting technologies. Optical sorters use infrared or near-infrared light to identify different plastics based on their molecular structure. These machines can separate plastics with high precision, improving the overall quality of the recycled material. Additionally, eddy current separators can be used to separate non-ferrous metals from plastics, further enhancing the sorting process.
By following these steps, you can establish an efficient collection and sorting system, ensuring that the plastic waste is properly categorized and prepared for the next stage of recycling, which involves transforming it into valuable plastic sheets. This process not only reduces environmental impact but also promotes a circular economy, where resources are reused and recycled to create new products.
Unraveling the Mystery: Can Plastic Drink Pouches Be Recycled?
You may want to see also
Shredding: Break down plastic into small pieces
Shredding is a crucial step in the process of transforming recycled plastic into usable materials, especially when aiming to create plastic sheets. This process involves breaking down larger plastic items or waste into smaller, manageable pieces, which can then be further processed and molded into various forms. The goal is to reduce the size of the plastic to a point where it can be easily handled and processed without causing damage to the machinery or equipment used in the subsequent stages of production.
To begin shredding, you'll need a shredder, which can be either a manual or an electric model, depending on the scale of your operation. For smaller-scale recycling, a manual shredder might be sufficient, as it is lightweight, easy to use, and does not require electricity. These manual shredders often feature a hand-crank mechanism that allows you to feed the plastic items into the shredder and turn the crank to grind them into smaller pieces. This method is simple and cost-effective, making it ideal for home-based recycling projects.
Electric shredders, on the other hand, are more powerful and can handle larger volumes of plastic waste. They are equipped with sharp blades that rotate rapidly, effectively reducing the size of the plastic items. When using an electric shredder, ensure that you follow the manufacturer's guidelines to avoid any accidents or damage to the machine. Always wear protective gear, such as gloves and safety goggles, to safeguard your hands and eyes from any potential hazards.
The shredded plastic will now be in a form that is more manageable and easier to work with. The size of the pieces will depend on the type of shredder used and the desired outcome. For creating plastic sheets, you will typically want the shredded plastic to be in a consistent, fine powder form. This can be achieved by further processing the shredded material through a screen or a mesh filter to separate the smaller particles from any larger fragments.
Once the plastic is shredded and reduced to the desired size, it can be collected and stored for the next steps in the recycling process. This includes cleaning and sorting the plastic to remove any contaminants, followed by the melting and molding stages, where the shredded plastic is transformed into sheets or other desired shapes. Proper shredding ensures that the subsequent processes are more efficient and effective, contributing to the overall success of your plastic recycling endeavor.
Rothy's Recycled Revolution: Unveiling the Eco-Friendly Footwear
You may want to see also
Melting: Heat and melt the shredded plastic
The process of transforming recycled plastic into plastic sheets involves a crucial step: melting the shredded plastic. This step requires careful attention to detail and the use of appropriate equipment to ensure the quality and consistency of the final product. Here's a detailed guide on how to melt and prepare the shredded plastic for sheet formation:
Melting Equipment and Setup:
To melt the shredded plastic, you'll need a specialized machine known as a plastic granulator or a melt blender. These machines are designed to handle the high temperatures required for plastic melting. The process begins by feeding the shredded plastic into the granulator's feeding mechanism, which ensures an even distribution of the material. The machine then heats the shredded plastic to its melting point, which varies depending on the type of plastic. For example, common plastics like PET (polyethylene terephthalate) and HDPE (high-density polyethylene) have different melting temperatures. It's essential to set the machine's temperature accordingly to avoid overheating or under-melting.
Melting Process:
Once the shredded plastic is fed into the granulator, the machine's heating element comes into play. The heat is applied uniformly to the plastic, causing it to melt and become a viscous liquid. This process requires precise control to ensure the plastic reaches the desired consistency. Overheating can lead to the formation of unwanted byproducts and affect the final sheet's quality. On the other hand, under-melting may result in brittle sheets. Therefore, monitoring the temperature and adjusting it as needed is crucial. Some machines offer temperature control panels or digital displays to facilitate this process.
Safety Considerations:
Working with melted plastic requires strict adherence to safety protocols. Always wear appropriate personal protective equipment, such as heat-resistant gloves and safety goggles, to protect yourself from potential burns or splashes. Ensure that the melting area is well-ventilated to prevent the inhalation of plastic fumes, which can be harmful if inhaled over prolonged periods. Additionally, have a fire extinguisher nearby as a safety measure.
Quality Control:
During the melting process, it's essential to inspect the plastic's consistency. The melted plastic should have a smooth, uniform appearance without any visible impurities or unmelted pieces. If any undissolved plastic is noticed, it may indicate that the melting temperature was too low or that the shredding process was not thorough enough. In such cases, additional shredding or re-melting might be necessary to ensure a consistent product.
Post-Melting Handling:
After the plastic has been melted and cooled slightly, it can be poured into molds or shaped as desired to create the plastic sheets. This step requires careful handling to avoid contamination or damage to the melted plastic. Proper cooling and handling techniques will be discussed in the next section to ensure the plastic sheets are formed successfully.
Fredericksburg, TX: Unveiling the Plastic Recycling Mystery
You may want to see also
Molding: Form the molten plastic into sheets
The process of molding molten plastic into sheets is a crucial step in the production of plastic sheets from recycled materials. This method allows for the creation of flat, uniform plastic sheets, which can then be used for various applications, such as packaging, signage, and construction. Here's a detailed guide on how to achieve this:
Mold Preparation: Begin by selecting a suitable mold that is designed to create the desired sheet size and thickness. The mold should be made of a material that can withstand high temperatures and is compatible with the type of plastic being used. Ensure the mold is clean and free of any debris or contaminants. You can use a flat mold or a custom-designed mold depending on the sheet's intended use.
Melting and Feeding: Melt the recycled plastic in a specialized machine, such as an extruder or a plasticizer. The plastic should be heated to its melting point, ensuring it becomes a viscous liquid. The molten plastic is then fed into the mold through a feeding mechanism. This can be done using a single or twin screw extruder, depending on the production scale and requirements.
Sheet Formation: As the molten plastic enters the mold, it is shaped and formed by the mold's cavities and channels. The temperature and pressure within the mold are carefully controlled to ensure the plastic takes the desired form. The mold's design will determine the final sheet's thickness and any desired patterns or textures. This step requires precision to achieve consistent sheet quality.
Cooling and Solidification: Once the plastic is molded, rapid cooling is essential to solidify the sheet. Coolant systems, such as water or air, are often used to quickly lower the temperature of the mold and the plastic sheet. This process ensures the plastic remains in its solid state and maintains the desired shape. Proper cooling is critical to prevent warping or distortion.
Sheet Ejection and Finishing: After cooling, the molded plastic sheet can be carefully ejected from the mold. Any excess material or flash can be trimmed and removed. The sheets may then undergo additional finishing processes, such as smoothing, cutting, or laminating, to meet specific requirements. This step ensures the final product is of high quality and ready for its intended use.
Molding is a precise and controlled process that requires technical expertise and specialized equipment. It is an essential phase in transforming molten plastic into functional sheets, contributing to the overall efficiency of the plastic sheet production process.
Earn Cash: US Recycles Plastic for Rewards
You may want to see also
Cooling: Allow the plastic sheets to cool and solidify
The process of creating plastic sheets from recycled plastic involves several steps, and one crucial phase is cooling. After the plastic has been heated and formed into sheets, it needs to be allowed to cool and solidify properly to ensure its structural integrity and durability. This cooling process is essential to transform the molten plastic into a stable, usable material.
When working with recycled plastic, it is important to maintain a controlled environment during cooling. The cooling process should be gradual and uniform to avoid any stress or distortion in the plastic sheets. One effective method is to place the plastic sheets in a well-ventilated area with a consistent temperature. This can be achieved by using fans or air circulators to ensure even cooling on all sides of the sheets. The temperature and duration of cooling will depend on the type of plastic and the desired thickness of the sheets. For most recycled plastics, a cooling period of several hours is recommended to allow the material to reach a stable state.
During this cooling phase, it is crucial to monitor the temperature to prevent overheating or undercooling. Overheating can lead to a loss of desired properties, while undercooling may result in a brittle material. Using a thermometer or temperature probe can help maintain the optimal cooling temperature. Additionally, ensuring proper ventilation is key to preventing the accumulation of heat, especially in enclosed spaces.
As the plastic sheets cool, they will gradually become more rigid and less pliable. This transformation is a result of the polymer chains aligning and forming a crystalline structure. The cooling process should be slow enough to allow for this alignment, ensuring the sheets are strong and less prone to deformation. Once the sheets have cooled and solidified, they can be handled and used for various applications, such as packaging, signage, or even construction materials.
Proper cooling is a critical step in the production of plastic sheets from recycled plastic, as it directly impacts the final product's quality and performance. By allowing the plastic to cool and solidify gradually, you can achieve a material that is both functional and environmentally friendly. This process ensures that the recycled plastic is transformed into a valuable resource, contributing to a more sustainable approach to manufacturing.
Unleash the Power of Plastic Paint Pots: Can They Be Recycled?
You may want to see also
Frequently asked questions
The process typically involves collecting and sorting plastic waste, which is then cleaned and shredded into small pieces. These pieces are melted and extruded through a die to create a continuous sheet. The sheet is then cooled and cut into desired sizes.
No, not all recycled plastics are suitable for this process. Common types used for sheet production include high-density polyethylene (HDPE), polypropylene (PP), and polystyrene (PS). The choice of plastic depends on the desired properties of the final sheet, such as strength, flexibility, and transparency.
Absolutely! Using recycled plastic reduces the demand for virgin plastic production, which often relies on fossil fuels. It also helps divert waste from landfills or incinerators, lowering greenhouse gas emissions and pollution. Additionally, it promotes a circular economy, where resources are reused and recycled, reducing the environmental impact of plastic production.