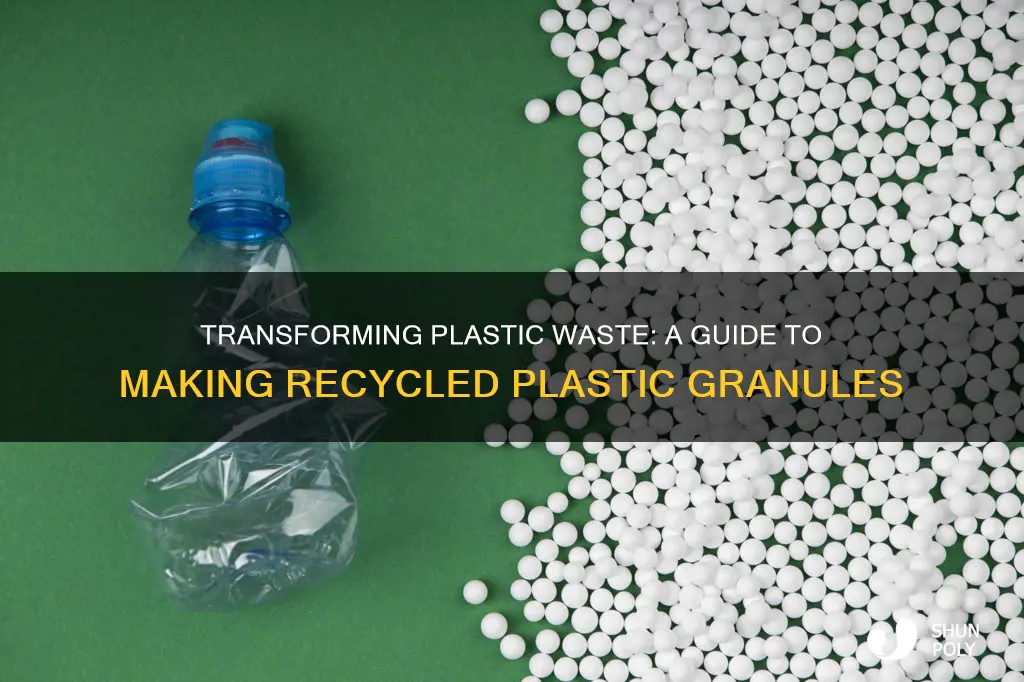
Recycled plastic granules are an essential component in the circular economy, offering a sustainable alternative to virgin plastic materials. The process of making these granules involves several steps, starting with the collection and sorting of used plastic items, which are then cleaned and shredded. The shredded plastic is next melted and extruded through a die to form small pellets or granules. These granules can be further processed and used in various industries, such as manufacturing, construction, and packaging, contributing to a more sustainable and environmentally friendly approach to plastic production.
What You'll Learn
- Collection: Gather plastic waste from various sources, ensuring it's clean and sorted
- Sorting: Separate plastics by type (PET, HDPE, etc.) for efficient processing
- Cleaning: Remove contaminants like labels, caps, and food residue
- Shredding: Break down plastic waste into small flakes or pellets
- Melting and Molding: Heat and mold the flakes into uniform granules
Collection: Gather plastic waste from various sources, ensuring it's clean and sorted
The first step in the process of creating recycled plastic granules is the collection and sorting of plastic waste. This initial phase is crucial as it sets the foundation for the entire recycling process and ensures the quality of the final product. When gathering plastic waste, it's essential to source materials from various places to increase the volume and diversity of the collection. This can include residential areas, commercial establishments, public spaces, and even industrial sites, provided that the waste is properly managed and segregated.
To begin the collection process, establish partnerships with local waste management companies, recycling centers, or community organizations. These entities often have the infrastructure and expertise to collect and sort waste effectively. They can provide guidelines on what types of plastic are accepted and how to prepare the waste for collection. For instance, they might request that plastic items are cleaned, flattened, or broken down to save space and facilitate the sorting process.
During the collection phase, it's imperative to maintain a high level of cleanliness. Plastic waste should be free from contaminants such as food residue, labels, and non-plastic materials like glass or metal. Contaminated plastic can be difficult to recycle and may even render the entire batch unusable. Therefore, ensure that all collected plastic items are thoroughly cleaned. This might involve washing them with water and soap, or using specialized cleaning agents if necessary.
Sorting the collected plastic waste is another critical aspect of this stage. Proper sorting ensures that different types of plastics are separated, which is essential for the recycling process. Common types of plastics include PET (polyethylene terephthalate), HDPE (high-density polyethylene), PVC (polyvinyl chloride), LDPE (low-density polyethylene), and PP (polypropylene). Each type has unique properties and applications, and recycling them separately can lead to higher-quality recycled products.
To sort the plastic waste, you can use a combination of manual sorting and automated methods. Manual sorting involves trained personnel who visually inspect and separate the plastics based on their type and condition. Automated sorting, on the other hand, utilizes machines like optical sorters and density separators to efficiently separate plastics. These machines can process large volumes of waste quickly and accurately, making the sorting process more efficient and cost-effective.
Grow Green: Transform Plastic into Productive Raised Garden Beds
You may want to see also
Sorting: Separate plastics by type (PET, HDPE, etc.) for efficient processing
The process of creating recycled plastic granules begins with meticulous sorting, a crucial step to ensure efficient and effective processing. Plastic waste is a diverse material, comprising various types with distinct properties, and proper sorting is essential to streamline the recycling journey. This initial stage involves categorizing plastics into their respective types, such as PET (polyethylene terephthalate), HDPE (high-density polyethylene), LDPE (low-density polyethylene), and others. Each plastic type has unique characteristics, and understanding these differences is vital for the subsequent steps.
PET, commonly found in beverage bottles, is a popular choice for recycling due to its ease of processing. It is lightweight and has a high melting point, making it suitable for injection molding and extrusion processes. HDPE, often used in milk jugs and shampoo bottles, is another valuable plastic type. Its strength and impact resistance make it ideal for various applications, including containers and packaging. LDPE, with its flexibility and softness, is prevalent in shopping bags and film applications. Sorting these plastics by type ensures that each material is processed appropriately, maximizing the potential for successful recycling.
The sorting process typically involves manual labor, where trained personnel examine the plastic waste and separate it accordingly. This method is effective for large-scale recycling operations and can be optimized with the use of color-coded bins or containers, making it easier to identify and collect specific plastic types. For instance, PET bottles can be identified by their clear or slightly tinted appearance, while HDPE containers often have a slightly thicker wall and a slight give when squeezed.
Advanced recycling facilities may employ automated sorting systems, utilizing technologies like near-infrared (NIR) spectroscopy. This method identifies plastic types by analyzing the unique light absorption patterns of different polymers. NIR spectroscopy can quickly and accurately separate plastics, ensuring a more efficient and consistent sorting process. The goal is to create a clean and sorted stream of plastics, minimizing contamination and maximizing the quality of the recycled material.
Efficient sorting by type is a critical step in the recycling process, as it sets the foundation for the subsequent stages of granule production. Proper sorting ensures that the recycled plastic granules meet the required specifications and can be utilized in various industries, contributing to a more sustainable and circular economy. By investing time and resources in this initial step, the overall recycling process becomes more streamlined and environmentally friendly.
Unraveling the Mystery: Can All Recycle Codes Mean Recyclable?
You may want to see also
Cleaning: Remove contaminants like labels, caps, and food residue
The process of creating recycled plastic granules begins with meticulous cleaning to ensure the raw materials are of high quality and ready for further processing. This cleaning step is crucial as it directly impacts the purity and usability of the final product. Here's a detailed guide on how to effectively remove contaminants like labels, caps, and food residue from plastic items:
Sorting and Pre-Cleaning: Before diving into the cleaning process, it's essential to sort the plastic waste. Separate different types of plastics to ensure efficient cleaning. For instance, remove all non-plastic items like labels, caps, and any metal or glass components. This initial sorting step saves time and resources later in the cleaning process. Once sorted, rinse the plastic items under running water to remove loose dirt and debris. This simple step helps in preventing the spread of contaminants during the cleaning process.
Chemical Cleaning: For more stubborn contaminants, chemical cleaning is an effective method. Start by soaking the plastic items in a suitable chemical solution. For example, a mixture of water and a mild detergent or a specialized plastic cleaner can be used. Allow the plastics to soak for a predetermined amount of time, which varies depending on the type of plastic and the severity of contamination. After soaking, scrub the plastics using a soft-bristled brush or a non-abrasive sponge to remove any remaining labels, caps, or food residue. Rinse the plastics thoroughly with clean water to eliminate any chemical residue.
Ultrasonic Cleaning: Ultrasonic cleaning is a modern and efficient technique to remove contaminants. Fill a cleaning tank or basin with water and add a small amount of a mild detergent or cleaning agent. Place the plastic items into the tank and turn on the ultrasonic cleaner. The high-frequency sound waves create tiny bubbles that agitate the water, effectively dislodging and removing contaminants. This method is particularly useful for intricate plastic parts or those with complex shapes. After the cleaning cycle, rinse the plastics thoroughly to ensure no chemical residue remains.
Drying and Inspection: After cleaning, proper drying is essential to prevent water spots and further contamination. Use a clean towel or air-drying method to remove excess water. Inspect the cleaned plastics to ensure all contaminants have been removed. This step is crucial to identify any remaining residue or damage that might require additional cleaning.
By following these cleaning procedures, you ensure that the plastic waste is thoroughly prepared for the next stage of the recycling process, ultimately leading to the production of high-quality recycled plastic granules. This meticulous approach to cleaning contributes to the overall sustainability and efficiency of the recycling system.
Can Plastic Blinds Be Recycled? Unraveling the Mystery
You may want to see also
Shredding: Break down plastic waste into small flakes or pellets
Shredding is a crucial step in the process of recycling plastic waste and transforming it into valuable granules. This process involves breaking down larger plastic items or sheets into smaller, more manageable pieces, typically flakes or pellets. These smaller pieces are easier to handle and transport, making them suitable for further processing and eventual reuse.
The shredding process begins with the collection and sorting of plastic waste. Different types of plastics, such as PET, HDPE, and LDPE, are sorted to ensure compatibility and ease of processing. Once sorted, the plastic waste is fed into a shredding machine, which can be either a manual or automated system. Manual shredders often involve a hand-cranked mechanism or a simple cutting blade, while automated shredders use powerful motors and specialized blades to handle the task efficiently.
In the shredding machine, the plastic waste is subjected to intense force and pressure, causing it to break apart. The machine's blades or teeth cut through the plastic, reducing it to smaller fragments. The shredding process aims to create a consistent size and shape of the plastic flakes, ensuring uniformity in the final product. The shredded plastic flakes are then separated from any remaining contaminants or debris through a process called screening, where larger pieces are removed, leaving behind the desired small flakes.
These small plastic flakes are now ready for further processing. They can be cleaned to remove any remaining impurities, washed, and dried to ensure high-quality granules. The flakes are then fed into a granulator, a machine designed to reduce the plastic flakes to even smaller particles, creating the recycled plastic granules. These granules can be used in various applications, such as manufacturing new plastic products, filling materials, or as a raw material for 3D printing.
Shredding is a critical step in the recycling process, as it enables the efficient breakdown of plastic waste, making it more accessible for further processing and reuse. It is an essential bridge between collecting plastic waste and creating valuable recycled products, contributing to a more sustainable and circular economy.
Unraveling the Plastic Recycling Mystery: Efficiency and Impact
You may want to see also
Melting and Molding: Heat and mold the flakes into uniform granules
The process of transforming recycled plastic flakes into uniform granules involves a combination of heating and molding techniques. This method is a crucial step in the recycling and repurposing of plastic waste, allowing for the creation of new products and materials. Here's a detailed guide on how to melt and mold the flakes into the desired granules:
Melting Process: Begin by setting up a melting machine or furnace specifically designed for plastic processing. The flakes, which are typically collected and sorted, are fed into the machine. The melting process requires precise temperature control. The ideal temperature range for most plastics is between 250°C and 350°C (482°F and 662°F). Higher temperatures can be used for specific types of plastic, but it's essential to maintain consistency to ensure the quality of the final product. As the flakes are heated, they will begin to soften and eventually melt into a viscous liquid. This stage demands careful monitoring to prevent overheating or underheating, which could lead to undesirable outcomes.
Once the flakes are completely melted, the molten plastic is ready for the molding phase. This step involves shaping the liquid plastic into the desired granule form. There are various molding techniques, but one common method is extrusion. In this process, the molten plastic is forced through a die or mold to create the granule shape. The die's design will determine the size and uniformity of the granules. It's crucial to ensure that the mold is well-maintained and clean to prevent contamination and maintain product quality.
Molding and Cooling: After the plastic is extruded, it needs to be cooled rapidly to solidify and maintain its shape. This is typically done by passing the molten plastic through a cooling system, such as a water bath or air cooling chamber. The cooling process must be carefully managed to avoid cracking or warping the granules. Once cooled, the plastic will be in the form of uniform granules, ready for further processing or use.
This melting and molding process is a critical aspect of recycling and upcycling plastic waste. It allows for the creation of high-quality granules that can be used in various industries, such as manufacturing, construction, and packaging. By following these steps and maintaining precise control over temperature and molding techniques, you can produce recycled plastic granules that meet specific standards and requirements.
Transforming Plastic Waste: The Journey to Recycled Benches
You may want to see also
Frequently asked questions
The process typically involves collecting and sorting plastic waste, cleaning and shredding it, and then melting and pelletizing the plastic to create granules. This method ensures a consistent and reusable material for various applications.
No, not all plastics are suitable for recycling into granules. Common types like PET (polyethylene terephthalate) and HDPE (high-density polyethylene) are widely accepted and can be easily recycled. However, some plastics, such as styrene or certain blends, may have limitations and require specific processing methods.
You can contribute by properly disposing of your plastic waste and ensuring it is clean and sorted. Many recycling programs and initiatives accept plastic items like bottles, containers, and packaging. Additionally, supporting local recycling facilities and businesses that specialize in plastic recycling can help promote the production of recycled plastic granules.