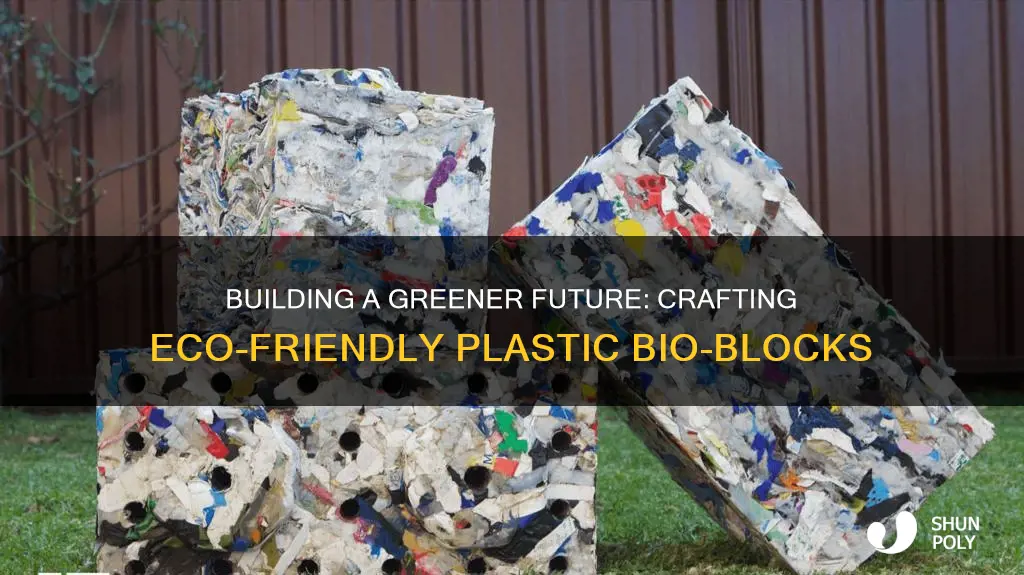
The growing demand for sustainable building materials has led to the exploration of innovative methods to create eco-friendly construction blocks. One such approach involves the manufacturing of recycled plastic bio-building blocks, which offer a unique blend of environmental benefits and structural advantages. This process begins with the collection and sorting of plastic waste, followed by a meticulous recycling procedure to transform it into a raw material suitable for block production. The key innovation lies in incorporating natural ingredients, such as plant fibers or bio-based additives, to enhance the material's strength and durability while reducing its environmental impact. By combining recycled plastic with these organic components, manufacturers can create lightweight, durable blocks that are not only eco-conscious but also contribute to the development of sustainable construction practices. This method not only reduces plastic waste but also provides a cost-effective and renewable alternative to traditional building materials, making it an exciting prospect for the construction industry's future.
What You'll Learn
- Plastic Collection: Gather and sort plastic waste for recycling
- Cleaning & Shredding: Clean, shred, and melt plastic into flakes
- Moulding & Forming: Mold and form recycled plastic into building blocks
- Biological Treatment: Use microorganisms to break down plastic waste
- Sustainable Construction: Build structures using bio-based plastic blocks
Plastic Collection: Gather and sort plastic waste for recycling
The first crucial step in the process of manufacturing recycled plastic bio-building blocks is efficient plastic collection and sorting. This phase is essential to ensure the quality and sustainability of the final product. Here's a detailed guide on how to effectively gather and sort plastic waste for recycling:
Collection Methods:
- Public Awareness and Drop-off Points: Educate the community about the importance of recycling plastic. Set up designated drop-off locations in public areas, such as community centers, schools, or local government offices. Provide clear instructions on what types of plastic are accepted to encourage proper sorting.
- Curbside Collection: Implement a curbside recycling program where residents can place their plastic waste in designated bins. Ensure that the collection schedule is well-communicated to avoid contamination from non-recyclable items.
- Commercial and Industrial Sources: Engage with businesses and industries that generate significant plastic waste. Encourage them to separate and collect their plastic scraps, bottles, and packaging for recycling. Offer incentives or partnerships to facilitate this process.
Sorting Process:
- Manual Sorting: Employ trained personnel to manually sort the collected plastic waste. This step is crucial for high-quality recycling. Workers should be skilled in identifying different types of plastics based on their resin identification codes (e.g., PET, HDPE, LDPE).
- Color Sorting: Plastic items can also be sorted by color to maintain aesthetic consistency in the final product. This is especially important for building blocks, as color uniformity can be a design requirement.
- Machine Sorting: Invest in advanced sorting machines that use technology like infrared sensors to identify and separate plastics. These machines can process large volumes of waste efficiently, ensuring a faster and more accurate sorting process.
Quality Control:
- Inspect and Reject: Implement a rigorous inspection process to identify and remove non-recyclable or contaminated plastic items. This step ensures that only suitable materials proceed to the manufacturing stage.
- Shredding and Granulation: After sorting, plastic waste can be shredded into small pieces or granulated to create a consistent raw material for the next phase of production.
By following these collection and sorting practices, you can establish a robust foundation for manufacturing recycled plastic bio-building blocks, contributing to a more sustainable and environmentally friendly construction industry.
Recycled Plastic Deck Mats: Heat Retention and Comfort
You may want to see also
Cleaning & Shredding: Clean, shred, and melt plastic into flakes
The process of manufacturing recycled plastic bio-building blocks begins with thorough cleaning and preparation of the plastic waste. This initial step is crucial to ensure the quality and integrity of the final product. Here's a detailed guide on how to clean, shred, and melt plastic into flakes:
Cleaning: The first step is to collect and sort plastic waste. This waste can come from various sources, such as post-consumer plastic items, industrial scrap, or even agricultural waste. It is essential to separate different types of plastics to facilitate the recycling process. Start by removing any non-plastic contaminants like metal, glass, or paper. For example, if you have plastic bottles, remove the caps and rinse them to eliminate any food residue. Use a washing machine or a large sink to clean the plastics, ensuring they are free from dirt and debris. This step might require multiple washes to achieve a thorough clean.
Shredding: After cleaning, the plastic needs to be shredded into small pieces. Shredding helps in reducing the size of the plastic, making it easier to process and increasing the surface area, which is beneficial for the next steps. You can use industrial shredders designed for plastic waste. The shredding process should be tailored to the type of plastic and the desired flake size. For instance, PET bottles can be shredded into flakes of approximately 2-3 mm in size. The shredded plastic will now appear as a pile of small, uniform pieces, ready for the next stage.
Melting and Flaking: The shredded plastic is then fed into a melting machine, typically a single or twin-screw extruder. The temperature and pressure inside the extruder are carefully controlled to melt the plastic without degrading its quality. As the plastic melts, it is pushed through a die to create a continuous strand. This strand is then cooled and cut into small, uniform flakes. The melting and flaking process is crucial as it determines the consistency and quality of the final plastic flakes. The flakes should be clean, free from any impurities, and have a consistent size and color.
This cleaning and shredding process is a critical phase in recycling plastic for bio-building blocks. It ensures that the plastic is ready for further processing, where it will be transformed into sustainable building materials. The next steps might involve adding natural fibers or other bio-based materials to create composite structures for construction.
Unraveling the Mystery: Can Plastic Chairs Be Recycled?
You may want to see also
Moulding & Forming: Mold and form recycled plastic into building blocks
The process of molding and forming recycled plastic into building blocks involves several steps to ensure the final product is durable, aesthetically pleasing, and environmentally friendly. Here's a detailed guide on how to achieve this:
Material Preparation: Begin by sourcing high-quality recycled plastic waste, preferably from post-consumer or post-industrial sources. Clean and sort the plastic to remove any contaminants, ensuring it is free from impurities like food residue, labels, or sharp objects. Grinding or shredding the plastic into small pieces will make it easier to handle and process.
Mould Design: Design or select a mold that suits the desired shape and size of the building blocks. The mold should be carefully crafted to ensure proper drainage and release of the formed plastic. Consider using a mold made from durable materials like aluminum or steel to withstand the high temperatures and pressures involved in the molding process.
Heating and Mixing: Melt the recycled plastic using a specialized heating system or an industrial oven. Ensure the temperature is controlled to avoid overheating, which can degrade the plastic's quality. Once melted, mix in any desired additives such as colorants, fillers, or bio-based compounds to enhance the material's properties. This step allows for customization, making the blocks more aesthetically pleasing or providing additional benefits like improved insulation.
Molding Process: Pour the heated and mixed plastic into the prepared mold. Apply pressure evenly to ensure complete filling and proper bonding. The molding process can be done using a hydraulic press or a vacuum-assisted system, depending on the scale and complexity of the blocks. Allow sufficient time for the plastic to cool and solidify within the mold.
Demolding and Finishing: Carefully remove the mold to reveal the formed building blocks. Inspect the blocks for any defects or imperfections and smooth out any rough edges. You can use various finishing techniques such as sanding, grinding, or polishing to achieve a smooth surface. Consider adding texture or patterns to the blocks for improved grip and visual appeal.
Drying and Curing: Place the formed blocks in a controlled environment to ensure proper drying and curing. This step is crucial to remove any residual moisture and ensure the blocks' structural integrity. The duration and temperature of this process will depend on the specific plastic used and the desired hardness of the final product.
By following these molding and forming techniques, you can create recycled plastic building blocks that are not only sustainable but also meet the required standards for construction and architectural applications. This process contributes to a circular economy, reducing waste and promoting the use of renewable resources in the construction industry.
Unraveling California's Plastic Recycling Mystery: A Guide to Knowing What Works
You may want to see also
Biological Treatment: Use microorganisms to break down plastic waste
Biological treatment of plastic waste is an innovative approach that utilizes the natural capabilities of microorganisms to degrade and transform plastic materials. This method offers a sustainable solution to the growing plastic pollution crisis, especially for those seeking eco-friendly alternatives to traditional recycling processes.
The process begins with selecting specific microorganisms, such as bacteria and fungi, which have the unique ability to metabolize and break down plastics. These microbes can be isolated from natural environments, such as soil or water, where they have adapted to degrade various organic compounds. Once identified, the microorganisms are cultivated in a controlled environment, providing them with the necessary nutrients and conditions to thrive and multiply. This cultivation can be done in bioreactors or specialized containers designed to optimize microbial growth.
The chosen microorganisms are then exposed to plastic waste, acting as catalysts in the breakdown of complex plastic polymers. Through their metabolic processes, these microbes secrete enzymes that target and degrade the plastic's chemical bonds. This biological degradation process is slower compared to chemical or mechanical recycling but is considered environmentally friendly and efficient. Over time, the plastic waste is transformed into simpler compounds, such as carbon dioxide, water, and biomass, which can be further utilized or safely disposed of.
One of the advantages of this biological treatment is its ability to handle a wide range of plastic types, including those that are challenging to recycle through other methods. Microorganisms can adapt and target different plastic polymers, making it a versatile solution for various plastic waste streams. Additionally, this process can be implemented at various scales, from small-scale laboratory experiments to large-scale industrial operations, allowing for flexibility in implementation.
In summary, biological treatment using microorganisms provides a promising avenue for addressing plastic waste management. By harnessing the power of nature's own tools, this method offers a sustainable and environmentally conscious approach to breaking down plastic materials, contributing to a circular economy and reducing the environmental impact of plastic pollution. Further research and development in this field can lead to more efficient and widely applicable solutions for recycling and managing plastic waste.
Eco-Friendly Flooring: Crafting Stylish Rugs from Recycled Plastic
You may want to see also
Sustainable Construction: Build structures using bio-based plastic blocks
The concept of using bio-based plastic blocks for construction is an innovative approach to sustainable building, offering an eco-friendly alternative to traditional construction materials. These blocks are designed to be both durable and environmentally friendly, making them an attractive option for those seeking to reduce their carbon footprint. The manufacturing process involves recycling and repurposing plastic waste, which is then transformed into building blocks with various applications.
To begin the manufacturing process, one would typically source plastic waste, which can include post-consumer and post-industrial plastic materials. These plastics are often collected from recycling centers, manufacturing facilities, or even directly from consumers. The key is to ensure that the plastic is clean, sorted, and free from contaminants to maintain the quality of the final product. Common types of plastics used in this process include polypropylene (PP), high-density polyethylene (HDPE), and polystyrene (PS), which are known for their durability and recyclability.
The next step involves processing the plastic waste. This can be achieved through various methods such as granulation, where the plastic is shredded and then melted to form small pellets. These pellets can then be used as a raw material for block production. Alternatively, the plastic can be processed into a moldable form, such as a paste or a liquid, which can be shaped into blocks using molds. This step requires careful consideration of the plastic's properties to ensure it can withstand the manufacturing process and the structural demands of building blocks.
Bio-based plastic blocks can be produced through extrusion or molding techniques. Extrusion involves melting the plastic pellets and forcing them through a die to create a continuous shape, which is then cut into blocks. This method is efficient and allows for the production of blocks with consistent dimensions. Molding, on the other hand, uses a mold to shape the plastic into the desired block form, offering more design flexibility. Both methods can be optimized to produce blocks that meet the required structural integrity and aesthetic appeal.
Once the blocks are manufactured, they can be used in various construction applications. These blocks can be stacked to form walls, floors, and even roofs, providing a sturdy and lightweight building solution. The bio-based nature of the plastic ensures that the blocks are biodegradable and have a reduced environmental impact compared to traditional concrete or brick blocks. Additionally, these blocks can be designed with integrated features such as windows, doors, and ventilation slots, making them versatile for different construction needs.
In summary, the manufacturing of recycle plastic bio-building blocks involves a process that begins with waste plastic collection and ends with the creation of sustainable construction materials. By utilizing recycled plastics and employing appropriate manufacturing techniques, these blocks can be produced efficiently and cost-effectively. This approach to sustainable construction not only reduces the demand for non-renewable resources but also minimizes waste, making it an essential step towards a greener and more environmentally conscious building industry.
Unraveling the Mystery: Can Plastic 6-Pack Rings Be Recycled?
You may want to see also
Frequently asked questions
The main raw material is recycled plastic, often sourced from post-consumer waste, such as plastic bottles, containers, and packaging. This plastic is then processed to create a sustainable building block.
The recycling process typically involves sorting and cleaning the plastic waste, followed by shredding or granulating it into small pieces. These pieces are then melted and molded into the desired block shape through an injection molding or extrusion process. Advanced recycling techniques may also include chemical processes to break down the plastic into its original monomers.
Commonly used plastics include PET (polyethylene terephthalate) and HDPE (high-density polyethylene), which are widely available and have good recycling potential. The choice of plastic depends on the desired properties of the building blocks, such as strength, durability, and biodegradability. Blending different types of plastics can also be employed to achieve specific characteristics.
These blocks are considered eco-friendly for several reasons. Firstly, they utilize recycled plastic, reducing waste and giving new life to materials that might otherwise end up in landfills. Secondly, some manufacturers use bio-based additives or natural fibers to enhance the blocks' sustainability, making them biodegradable and reducing their environmental impact over time.
Absolutely! Recycled plastic bio-building blocks can be used for various construction purposes, including wall panels, flooring, and even structural elements. They offer several benefits, such as lightweight design, excellent insulation properties, and resistance to rot and insect damage. Additionally, their production process often results in less energy consumption and lower carbon emissions compared to traditional building materials.