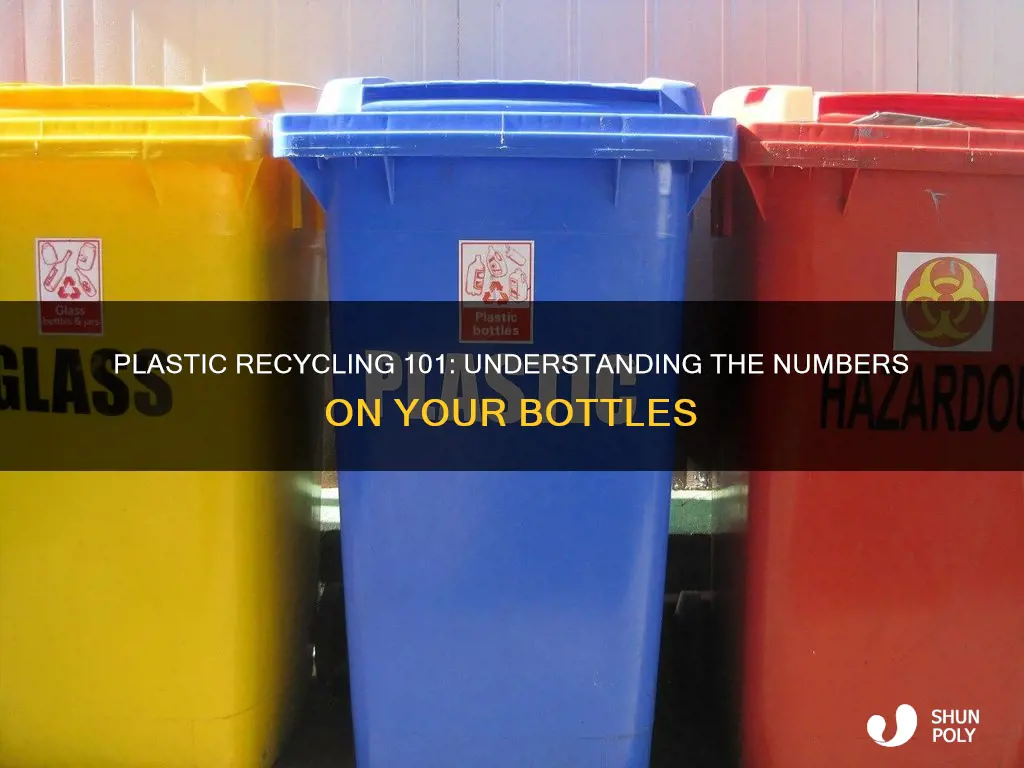
Recycling plastic is a crucial step towards a more sustainable future, and understanding the process based on numerical categories can greatly enhance its effectiveness. Plastic recycling involves sorting and processing various types of plastic materials, which are identified by a numerical code on their bottom, known as the Resin Identification Code (RIC). These codes, ranging from 1 to 7, indicate the type of plastic and its suitability for recycling. For instance, PET (polyethylene terephthalate) is commonly used for beverage bottles and has a code of 1, while HDPE (high-density polyethylene) is often found in milk jugs and carries code 2. Knowing these codes allows individuals and industries to properly recycle plastic, ensuring it is directed to the right facilities for processing and transformation into new products.
What You'll Learn
- Sorting and Collection: Separate plastics by type and number for efficient recycling
- Cleaning and Preparation: Rinse and remove contaminants to ensure quality
- Processing and Shredding: Break down plastic into flakes or pellets for reuse
- Melting and Molding: Heat and shape plastic for new products
- End-of-Life Management: Dispose of non-recyclable plastics responsibly
Sorting and Collection: Separate plastics by type and number for efficient recycling
The process of recycling plastic begins with proper sorting and collection, which is a crucial step to ensure efficient and effective recycling. Plastic recycling is a complex process, and the success of it heavily relies on the initial separation of different types of plastics. This practice is essential to streamline the recycling process and maximize the potential for successful recycling.
When it comes to sorting plastics, it is imperative to separate them based on their type and resin identification code, often indicated by a number inside a triangle on the bottom of the plastic item. This code, known as the Resin Identification Code (RIC), is a universal system used to identify different types of plastics. Understanding these codes is key to proper sorting. For instance, common plastic types include PET (polyethylene terephthalate, code 1), HDPE (high-density polyethylene, code 2), PVC (polyvinyl chloride, code 3), LDPE (low-density polyethylene, code 4), PP (polypropylene, code 5), and PS (polystyrene, code 6). Each of these plastics has unique properties and recycling methods.
The collection process should be organized and well-structured. Different types of plastics should be collected separately to avoid contamination. For example, PET bottles and containers should be placed in one collection stream, while HDPE milk jugs and shampoo bottles go into another. This ensures that the recycled material remains pure and does not compromise the quality of the new products. Clear labeling or color-coding of collection bins can greatly assist in this process, making it easier for individuals and facilities to sort plastics accurately.
In residential areas, public awareness and education play a vital role in promoting proper sorting. Providing clear guidelines and resources to residents can significantly improve recycling rates. Local governments and waste management companies can implement color-coded recycling bins in public spaces, making it convenient for people to separate their plastics. Additionally, encouraging the use of recycling centers or drop-off points specifically for different types of plastics can further enhance the efficiency of the sorting process.
For commercial and industrial facilities, implementing comprehensive recycling programs is essential. These programs should include on-site sorting systems, where employees are trained to identify and separate plastics according to their RICs. Providing dedicated collection bins for each type of plastic and educating staff about the importance of proper sorting can significantly improve recycling rates within these settings. Furthermore, businesses can also explore the option of partnering with specialized recycling companies that offer customized solutions for efficient plastic waste management.
In summary, efficient recycling of plastics starts with proper sorting and collection. By understanding the Resin Identification Codes and separating plastics accordingly, we can ensure that the recycling process is streamlined and effective. Whether it's in residential areas or commercial facilities, implementing structured collection systems and educating individuals about the importance of proper sorting will contribute to a more sustainable approach to plastic recycling.
Crafting Eco-Chic: A Guide to Recycled Plastic Sunglasses
You may want to see also
Cleaning and Preparation: Rinse and remove contaminants to ensure quality
The process of recycling plastic begins with proper cleaning and preparation to ensure the quality of the recycled material. This initial step is crucial as it directly impacts the efficiency and effectiveness of the recycling process. Here's a detailed guide on how to approach this stage:
Rinsing Plastic Items: Begin by thoroughly rinsing all plastic items to remove any visible contaminants. This includes food residue, labels, and any other debris. Use warm water and a gentle detergent to ensure a thorough clean. The goal is to eliminate any potential impurities that could compromise the quality of the recycled plastic. For instance, food particles can attract moisture, leading to mold growth during storage and processing, while labels and stickers might contain inks or glues that can interfere with the recycling process.
Removing Contaminants: After rinsing, carefully inspect each plastic item. Remove any non-plastic components such as caps, lids, or attached labels. These parts often require different recycling processes and can contaminate the main plastic stream if not separated. For example, plastic caps are often made of a different material (like polypropylene) and may not be recyclable in the same stream as the main plastic body. Additionally, ensure that no sharp objects or heavy debris remain attached to the plastic, as these can cause damage during the recycling process.
Drying and Sorting: Once cleaned, allow the plastic items to air dry completely. Moisture can affect the bonding and processing of the plastic during recycling. After drying, sort the plastic items based on their type and number, as indicated by the recycling symbol (resin identification code). Common plastic types include PET (polyethylene terephthalate), HDPE (high-density polyethylene), PVC (polyvinyl chloride), LDPE (low-density polyethylene), and PP (polypropylene). Proper sorting ensures that each type of plastic is recycled appropriately, maximizing the quality of the final product.
Special Considerations: It's important to note that not all plastic items are created equal. Avoid recycling items that have been heavily contaminated with chemicals or oils, as these can leach into the recycling process. Additionally, broken or severely damaged plastic items may not be recyclable and should be disposed of appropriately. Always check local recycling guidelines to ensure you are recycling the right items and in the correct manner.
By following these cleaning and preparation steps, you contribute to a more efficient and effective recycling process, ultimately leading to higher-quality recycled plastic products. This initial stage is a critical foundation for successful plastic recycling, ensuring that the material is clean, sorted, and ready for the next steps in the recycling journey.
Can Plastic Containers with Paper Labels Be Recycled?
You may want to see also
Processing and Shredding: Break down plastic into flakes or pellets for reuse
The process of recycling plastic begins with the collection and sorting of various plastic types, which is crucial for effective recycling. Once sorted, the plastic waste undergoes a transformation through a process known as processing and shredding. This step is essential as it prepares the plastic for further recycling and ensures it can be reused in new products.
In this stage, the plastic items, such as bottles, containers, or packaging, are fed into a shredding machine. The machine's powerful blades or rotating drums break down the plastic into smaller pieces, typically in the form of flakes or pellets. The shredding process aims to reduce the volume of plastic waste, making it easier to handle and transport while also creating a more uniform material.
Shredding machines can vary in design and functionality. Some machines use a single-stage process, where the plastic is shredded into flakes directly. These flakes are then cleaned and sorted to remove any contaminants. Alternatively, a two-stage process might be employed, where the initial shredding produces larger flakes, which are then further processed to create smaller, more refined pellets. The choice of shredding method depends on the desired end product and the specific recycling process.
After shredding, the plastic flakes or pellets are carefully inspected and sorted. This step is critical to ensure the quality and purity of the recycled material. Any non-plastic contaminants, such as labels, caps, or other foreign materials, are removed to prevent them from affecting the recycling process. The sorted and cleaned plastic flakes are then ready for the next stage of recycling, where they can be melted, reformed, and used to create new products.
This initial processing and shredding phase is a fundamental step in the recycling journey, as it sets the foundation for the entire recycling process. It requires specialized equipment and skilled operators to handle the material effectively. By breaking down plastic into flakes or pellets, this stage prepares the material for its reuse, contributing to a more sustainable and circular economy.
Sustainable Solutions: Recycling Impact Plastics for a Greener Future
You may want to see also
Melting and Molding: Heat and shape plastic for new products
The process of recycling plastic involves various methods to transform used plastic items into new products, and one of the most common techniques is melting and molding. This method is particularly useful for creating new products from a wide range of plastic types, allowing for the production of new items with various shapes and sizes. Here's a detailed guide on how this process works:
Melting Process: The first step in recycling plastic through this method is melting. Different types of plastic require specific temperatures to melt, so it's crucial to identify the plastic type before proceeding. For example, common plastic numbers (resin identification codes) include PET (1), HDPE (2), PVC (3), LDPE (4), PP (5), and PS (6). Each of these plastics has a unique melting point. PET, used in beverage bottles, typically melts at around 230-250°C (446-482°F), while HDPE, found in milk jugs, melts at a lower temperature of approximately 120-140°C (248-284°F). Accurate temperature control is essential to ensure the plastic is melted without burning or degrading. Specialized equipment like industrial ovens or melters is used to heat the plastic to its specific melting point.
Once the plastic is melted, it becomes a viscous liquid, often referred to as a 'plastic paste' or 'plastic resin.' This molten state allows for easy manipulation and shaping. The melting process also helps to remove any impurities or contaminants from the plastic, ensuring a higher-quality final product.
Molding and Shaping: After melting, the plastic is ready for molding and shaping. This step involves pouring the molten plastic into a mold, which gives the material its desired form. Molding can be done using various techniques, including injection molding, blow molding, and compression molding, each suitable for different product requirements. For instance, injection molding is ideal for producing intricate shapes with fine details, while blow molding is commonly used for creating hollow objects like bottles.
The mold is designed to match the desired shape of the final product. Once the plastic is poured into the mold, it is heated and cooled in a controlled manner. The cooling process is crucial as it determines the final dimensions and quality of the molded item. After cooling, the mold is opened, and the new product is removed, ready for further processing or use.
This recycling method is highly versatile and can be adapted to create a wide array of products, from simple household items to complex electronic components. It allows for the effective reuse of plastic, reducing waste and promoting a more sustainable approach to manufacturing. By understanding the specific melting points and molding techniques for different plastic types, recyclers can efficiently transform used plastic items into new, valuable products.
Unraveling the Mystery: Can Chinese Plastic Containers Be Recycled?
You may want to see also
End-of-Life Management: Dispose of non-recyclable plastics responsibly
When it comes to managing the end-of-life of plastics, especially those that are not recyclable through conventional means, it's crucial to handle them responsibly to minimize environmental impact. Here's a guide on how to dispose of non-recyclable plastics in an eco-conscious manner:
- Understand Plastic Types: Begin by recognizing the different types of plastics. The most common identification numbers used for plastics are 1 (PET), 2 (HDPE), 3 (PVC), 4 (LDPE), 5 (PP), 6 (PS), and 7 (Other). Non-recyclable plastics often include those marked with the number 7, which includes a wide range of materials like polycarbonate and bioplastics. Understanding these codes can help you make informed decisions about disposal.
- Check Local Recycling Guidelines: Every region has its own recycling guidelines and infrastructure. Contact your local waste management authority or check their website to understand what types of plastics they accept in their recycling programs. Some areas might have specific drop-off points or collection services for non-recyclable plastics. Knowing these details will ensure you dispose of these materials correctly.
- Explore Specialized Recycling Options: For non-recyclable plastics, consider specialized recycling programs. Some companies and organizations focus on recycling hard-to-recycle plastics. These programs often require specific collection methods, such as mail-in programs or drop-off events. Research and identify such initiatives in your area, as they provide a responsible way to manage these plastics.
- Proper Waste Segregation: At home or in your workplace, ensure proper waste segregation. Designate a bin or container specifically for non-recyclable plastics. Clearly label it to avoid confusion. This practice encourages responsible disposal and can also help educate others on proper waste management.
- Incineration and Energy Recovery: In some cases, non-recyclable plastics can be incinerated, especially if they are hazardous or contain toxic materials. Incineration can generate energy, reducing the need for fossil fuels. However, it's essential to ensure that these incineration facilities meet environmental standards to minimize air pollution.
- Education and Awareness: Spread awareness about responsible plastic disposal among your community. Educate others on the importance of proper waste management, especially for non-recyclable plastics. This collective effort can significantly contribute to reducing environmental pollution and promoting a more sustainable approach to plastic waste.
Remember, responsible end-of-life management of plastics is a collective responsibility. By following these guidelines, you can play a crucial role in minimizing the environmental impact of non-recyclable plastics.
The Recycling Process: Transforming Plastic Cups into New Products
You may want to see also
Frequently asked questions
Plastic recycling is often categorized by a resin identification code, which is a number inside a triangle on the bottom of the product. These codes, ranging from 1 to 7, indicate the type of plastic and its properties. For example, PET (polyethylene terephthalate) is commonly used for water bottles and has the number 1. HDPE (high-density polyethylene) is found in milk jugs and has code 2. These numbers help recycling centers and facilities determine the appropriate processing methods for each type of plastic.
Before recycling plastic, it's essential to clean and dry the items. Remove any non-plastic components like caps or labels. Rinse the plastic to remove food residue or liquids. Flatten or break down large items to save space in recycling bins. This preparation ensures that the plastic is recyclable and reduces the risk of contamination.
Not all plastic types are accepted in every recycling program. It's important to check with your local waste management authority or recycling center to understand their specific guidelines. Some areas may have restrictions or limitations on certain plastic numbers. For instance, code 6 and 7 plastics are often not widely accepted due to their lower recycling value and potential for contamination. Always refer to your local recycling guidelines to ensure proper disposal.
After plastic is collected and sorted, it undergoes a series of processes. It is cleaned, shredded, or granulated to create small pieces called 'flakes' or 'pellets'. These plastic flakes are then sold to manufacturers who use them to produce new products. The process may involve melting and reforming the plastic, which can be used in various industries, such as automotive, construction, and consumer goods. Recycling plastic helps reduce waste, conserve resources, and minimize environmental impact.
Plastic bags and film plastics, such as wrappings from toilet paper or paper towels, can be recycled, but they require special handling. These items should be placed in a separate bin or collected at designated drop-off points. Some grocery stores or retail chains provide collection bins for plastic bags to encourage recycling. It's important to avoid putting these items in regular recycling bins as they can cause issues in the recycling process. Always check with your local recycling guidelines for specific instructions on recycling plastic bags and film plastics.