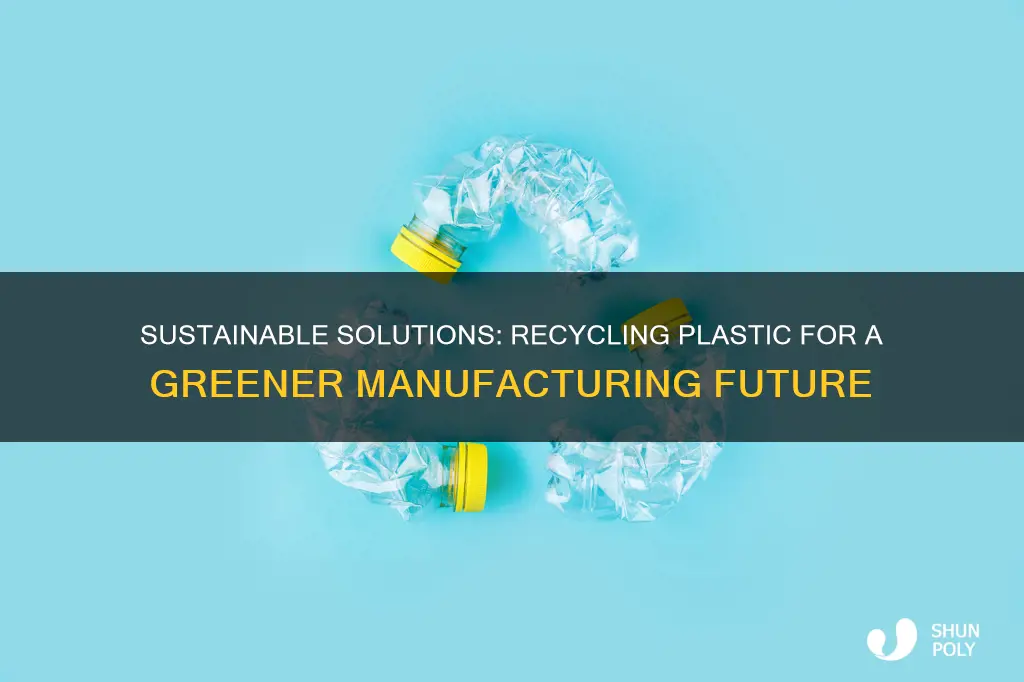
Recycling plastic in manufacturing is an essential practice to promote sustainability and reduce environmental impact. Plastic recycling involves processing used plastic materials to create new products, offering an eco-friendly alternative to virgin plastic production. This process not only helps conserve natural resources but also minimizes waste and reduces pollution. The manufacturing industry plays a crucial role in this recycling process by adopting innovative techniques to transform recycled plastic into various products, from packaging materials to automotive components. By implementing effective recycling methods, manufacturers can contribute to a circular economy, ensuring a more sustainable future for both the environment and the industry.
What You'll Learn
- Collection: Source and gather plastic waste from various streams
- Sorting: Separate plastics by type and color for efficient processing
- Cleaning: Remove contaminants to ensure high-quality recycled material
- Shredding/Grinding: Break down plastic into small pieces for easier processing
- Pelletizing: Melt and extrude plastic into uniform pellets for reuse
Collection: Source and gather plastic waste from various streams
The first step in the recycling process is the collection and sourcing of plastic waste, which is a critical phase that determines the success and efficiency of the entire recycling program. Effective collection methods are essential to ensure a steady supply of plastic materials for recycling, and they can significantly impact the quality and quantity of recycled products.
One primary source of plastic waste is household garbage. Implementing a comprehensive recycling program at the residential level is crucial. This can be achieved by providing clear guidelines and infrastructure to households, such as color-coded bins for different types of plastics, ensuring that residents understand which plastics are recyclable and how to sort them properly. Local governments and waste management companies can play a vital role in educating the public and providing the necessary tools for effective waste separation. For instance, offering free recycling bags or containers specifically designed for plastic waste can encourage participation and make the process more accessible.
Another stream to target is commercial and industrial waste. Many businesses, including restaurants, grocery stores, and manufacturing plants, generate substantial amounts of plastic waste. Establishing partnerships with these organizations can be beneficial. For example, restaurants can be encouraged to provide leftover food containers and packaging for recycling, while grocery stores can set up dedicated recycling bins for their customers. Industrial facilities, such as factories and warehouses, often have larger volumes of plastic waste, and implementing on-site recycling programs can significantly reduce their environmental impact. These businesses can also contribute by providing their employees with training on proper waste segregation.
Additionally, public spaces like parks, beaches, and streets should be considered for waste collection. These areas often accumulate plastic waste, especially in the form of single-use items like water bottles, shopping bags, and food containers. Implementing public recycling bins in these locations can encourage responsible behavior and contribute to a cleaner environment. Community initiatives, such as beach cleanups or street recycling drives, can also be organized to engage citizens in the collection process and foster a sense of environmental responsibility.
When collecting plastic waste, it is essential to ensure that the materials are clean and dry to maintain the quality of the recycled product. Contaminants like food residue, labels, and non-plastic items should be removed to facilitate the recycling process. Providing clear instructions on proper waste handling and offering resources for cleaning and sorting can significantly improve the efficiency of the collection process. Furthermore, establishing partnerships with local recycling centers or waste management companies can help in the transportation and processing of the collected plastic waste, ensuring it reaches the recycling facilities in good condition.
Unraveling the Mystery: Can Plastic Spools of Thread be Recycled?
You may want to see also
Sorting: Separate plastics by type and color for efficient processing
The process of recycling plastic in manufacturing begins with meticulous sorting, a critical step to ensure efficient and effective recycling. This initial phase involves separating plastics into distinct categories based on their type and color, a practice that significantly enhances the quality of the recycled material. The primary goal is to streamline the recycling process, making it more efficient and cost-effective.
Separation by Type:
Plastics are categorized into several types, each with unique chemical compositions and properties. The most common types include Polyethylene Terephthalate (PET), High-Density Polyethylene (HDPE), Polyvinyl Chloride (PVC), Low-Density Polyethylene (LDPE), and Polypropylene (PP). PET, for instance, is commonly found in beverage bottles, while HDPE is used in milk jugs and shampoo bottles. PVC is used in construction and electrical applications, LDPE in grocery bags, and PP in food containers. Sorting by type is crucial because different plastics have varying melting points and chemical properties, which affect their recyclability and the quality of the recycled product.
For example, PET and HDPE are generally easier to recycle and can be used to create new containers or other products. In contrast, PVC and PP often require more specialized recycling processes due to their unique chemical structures. By separating these plastics, recycling facilities can focus on specific processes for each type, ensuring that the recycled material meets the required standards.
Color Sorting:
Color is another essential factor in the sorting process. Plastic items can vary widely in color, from clear and transparent to various shades of blue, green, and even black. Sorting by color is important because it helps to maintain the integrity of the recycled material. For instance, clear PET bottles can be recycled into clear containers, maintaining their original appearance. However, mixing different colors can lead to a less aesthetically pleasing and less valuable product.
Advanced color-sorting techniques, such as optical sorting, use machines equipped with sensors that can detect and separate plastics based on color. This method is highly efficient and can process large volumes of plastic waste quickly. By removing the need for manual sorting, optical sorting reduces the risk of human error and increases the overall efficiency of the recycling process.
Benefits of Efficient Sorting:
Efficient sorting by type and color offers several advantages. Firstly, it allows recycling facilities to produce a more consistent and high-quality recycled plastic. This consistency is crucial for manufacturers who use recycled materials, as it ensures that the final product meets their specifications. Secondly, proper sorting reduces the likelihood of contamination, where one type of plastic is mixed with another, which can lead to processing issues and lower-quality end products.
Moreover, efficient sorting can lead to cost savings. By processing plastics in a more targeted manner, recycling facilities can reduce the energy and resources required for recycling, making the process more economically viable. This, in turn, can encourage more plastic waste to be recycled, contributing to a more sustainable and circular economy.
In summary, the initial step of sorting plastics by type and color is a fundamental and indispensable part of the recycling process in manufacturing. It sets the foundation for efficient recycling, ensuring that the final product is of high quality and meets the needs of various industries. As the demand for sustainable practices grows, efficient sorting will play an increasingly vital role in the global effort to recycle and reuse plastic materials.
Can Plastic Sheds Be Recycled? Unraveling the Mystery
You may want to see also
Cleaning: Remove contaminants to ensure high-quality recycled material
The process of recycling plastic in manufacturing begins with cleaning, a crucial step to ensure the quality and purity of the recycled material. This step involves removing any contaminants that may have accumulated during the collection and sorting process, as well as any residual impurities that could compromise the final product. Here's a detailed guide on how to effectively clean plastic for recycling:
Sorting and Segregation: The first step in cleaning is proper sorting and segregation of different types of plastics. Plastic materials are often identified by their resin identification codes (RICs), which are typically found on the bottom of the item. Common RICs include PET (polyethylene terephthalate), HDPE (high-density polyethylene), PVC (polyvinyl chloride), LDPE (low-density polyethylene), and PP (polypropylene). Each type of plastic has unique properties and requires specific cleaning methods. For instance, PET bottles are generally easier to recycle and can be cleaned with water, while HDPE containers may require more aggressive cleaning methods.
Physical Cleaning: After sorting, the plastic materials need to be physically cleaned to remove visible contaminants. This can be done through various methods:
- Washing: The most common method is washing, which involves soaking the plastic in water to dissolve and remove any attached labels, stickers, or other non-plastic materials. This process can be enhanced by using detergents or surfactants to break down and lift away contaminants. After washing, the plastic should be thoroughly rinsed to remove any chemical residues.
- Shredding and Pulping: For larger plastic items or those with complex shapes, shredding or pulping can be employed. Shredding involves breaking down the plastic into small pieces, which can then be washed and sorted. Pulping, on the other hand, is a process where the plastic is ground into a pulp, which can be cleaned and then reformed into new products.
- Air Classification: This method is particularly useful for separating different types of plastics based on their density. By using air currents, lighter plastics like PET can be separated from heavier ones like HDPE, ensuring a more efficient cleaning process.
Chemical Cleaning: In some cases, physical cleaning may not be sufficient, and chemical cleaning becomes necessary. This process involves using specific chemicals to dissolve or remove contaminants:
- Solvent Treatment: Certain solvents can be applied to dissolve and remove labels, glues, and other adhesives from plastic containers. This method is often used for HDPE and PET containers.
- Oxidizing Agents: These agents can be used to break down and remove organic contaminants, such as food residues or oils, from plastic surfaces.
- Ultrasonic Cleaning: This non-chemical cleaning method uses high-frequency sound waves to create small bubbles that vibrate and dislodge contaminants from the plastic surface.
Drying and Handling: After cleaning, the plastic materials must be thoroughly dried to prevent moisture-related issues during the recycling process. Proper drying ensures that the plastic is free from water, which can lead to mold growth or other quality issues. Drying can be done using air blowers or industrial dryers. Once dried, the plastic should be handled carefully to avoid contamination from dust or other external factors.
Quality Control: Throughout the cleaning process, quality control measures should be implemented to ensure the effectiveness of the cleaning methods. This includes regular testing of the cleaned plastic to verify its purity and quality. Visual inspections, moisture content testing, and chemical analysis can all be part of the quality control process.
By following these cleaning procedures, manufacturers can ensure that the recycled plastic materials meet the required standards, contributing to the production of high-quality recycled products. Effective cleaning is a critical step in the recycling process, as it directly impacts the performance and durability of the final recycled goods.
Understanding the Plastic Recycling Symbol: Does It Mean No BPA?
You may want to see also
Shredding/Grinding: Break down plastic into small pieces for easier processing
The process of shredding and grinding is a crucial step in plastic recycling, especially in manufacturing, as it prepares the plastic for further processing and recycling. This method involves breaking down larger plastic items or materials into smaller, more manageable pieces, which simplifies the recycling process and increases efficiency. Here's a detailed guide on how this process works:
Shredding Process:
Shredding is the initial step to reduce the size of plastic waste. It involves feeding plastic materials into a specialized machine designed for this purpose. These machines, often called shredders or plastic shredding systems, are engineered to handle various plastic types. The shredding process typically includes the following stages: First, the plastic is loaded into the shredder, where it is fed into a rotating drum or a series of blades. The drum rotates at high speed, tearing and shredding the plastic into thin strips or flakes. This process is designed to create a uniform size reduction, ensuring consistency in the shredded material. The shredded plastic can then be further processed or used directly in certain applications.
Grinding Technique:
Grinding is an additional step that takes the shredded plastic and reduces it even further. This process is particularly useful for creating a fine, powder-like substance, which is essential for certain recycling methods. Grinding machines use high-speed blades or impact mills to break down the shredded plastic into extremely small particles. The grinding process involves feeding the shredded plastic into the grinding chamber, where it is subjected to intense friction and impact. As the plastic particles collide with the grinding mechanism, they are reduced in size, often resulting in a fine, consistent powder. This fine-ground plastic can then be used in various recycling processes, such as compounding or creating new plastic products.
The combination of shredding and grinding offers several advantages. Firstly, it allows for the efficient separation of different types of plastics, as the process can be tailored to handle specific materials. Secondly, it reduces the volume of plastic waste, making it more cost-effective to transport and store during the recycling process. Moreover, the smaller particle size created by grinding enables better mixing and compounding, leading to improved material properties in the recycled products.
In the manufacturing industry, this process is often followed by additional steps such as washing, drying, and sorting to ensure high-quality recycled plastic. The shredded and ground plastic can then be used in various applications, including the production of new plastic products, composite materials, or even as a fuel source in some specialized recycling facilities. This method of recycling plastic is an essential part of sustainable manufacturing practices, contributing to a circular economy and reducing the environmental impact of plastic waste.
Sustainable Style: Unveiling the Cost of Recycled Plastic Fashion
You may want to see also
Pelletizing: Melt and extrude plastic into uniform pellets for reuse
Pelletizing is a crucial process in plastic recycling, transforming post-consumer or post-industrial plastic waste into a valuable raw material for manufacturing. This method involves a series of steps to melt and extrude plastic into uniform pellets, which can then be used to create new products. Here's a detailed breakdown of the pelletizing process:
Melt and Extrusion: The first step is to melt the collected plastic waste. This can be done using various heating methods, such as melters or extruders. The plastic is heated to its melting point, ensuring it becomes a viscous liquid. Once melted, the plastic is then extruded, a process where it is forced through a die or a small opening to create a continuous strand or sheet. This extrusion step is critical as it determines the size and shape of the final pellets.
Cooling and Cutting: After extrusion, the molten plastic strand is rapidly cooled to solidify it. This is typically done by immersing the strand in a cooling bath, often water or oil, to achieve a controlled cooling rate. The cooled strand is then cut into small, uniform pellets using a cutting mechanism. The size of these pellets can vary depending on the desired application, with smaller pellets being more common for injection molding and larger ones for fiber production.
Washing and Drying: To ensure the quality and purity of the pellets, washing and drying processes are essential. Washing removes any remaining contaminants, such as residual plasticizers or additives, from the pellets. This is often done using washing machines or centrifugal separators. After washing, the pellets are dried to remove moisture, which can affect their performance. Drying can be achieved through various methods, including air drying, vacuum drying, or using specialized drying equipment.
Sorting and Quality Control: Pelletizing also involves sorting the pellets based on their color, size, and quality. This step ensures that the final product meets the required specifications. Advanced sorting techniques, such as optical sorting or near-infrared spectroscopy, can be employed to separate different types of plastics or identify contaminated pellets. Quality control checks are performed to verify the consistency and integrity of the pellets.
Storage and Transportation: The uniform pellets are then stored in silos or containers, ready for transportation to manufacturers. Proper storage is crucial to maintain the quality and prevent contamination. These pellets can be sold directly to industries or used as feedstock for further processing, such as compounding or blending, to create specialized plastic materials.
Pelletizing offers a sustainable approach to managing plastic waste, allowing for its reuse in various applications. This process not only reduces environmental impact but also contributes to a circular economy by transforming waste into valuable resources.
Sustainable Solutions: Recycling Plastic Film in Eugene, Oregon
You may want to see also
Frequently asked questions
Manufacturing processes often utilize various plastic types, including PET (polyethylene terephthalate), HDPE (high-density polyethylene), PVC (polyvinyl chloride), and PP (polypropylene). Recycling these plastics typically involves collecting and sorting them by type, then using specialized processes like melting and reforming to create new products.
Manufacturers should establish a comprehensive recycling program that includes waste segregation at the source, providing clear guidelines to employees, and partnering with reputable recycling facilities. Regular audits and monitoring can ensure compliance and identify areas for improvement.
Recycling plastic can be challenging due to contamination, especially when different types of plastics are mixed. Additionally, some manufacturing processes may generate plastic waste with low-quality or non-recyclable materials. Advanced recycling technologies and proper waste management practices are essential to overcome these challenges.
Yes, recycled plastic can often be used in similar manufacturing processes as virgin plastic. However, the quality and properties of recycled plastic may vary depending on the recycling process and the original plastic type. Manufacturers can utilize recycled content in various applications, but it might require adjustments in processing and product design.
Manufacturers can implement several strategies to minimize plastic waste. These include adopting circular economy principles, such as designing products for longevity and recyclability, exploring alternative materials, and optimizing production processes to reduce waste generation. Collaboration with recycling experts and industry partners can also drive innovation in sustainable manufacturing.