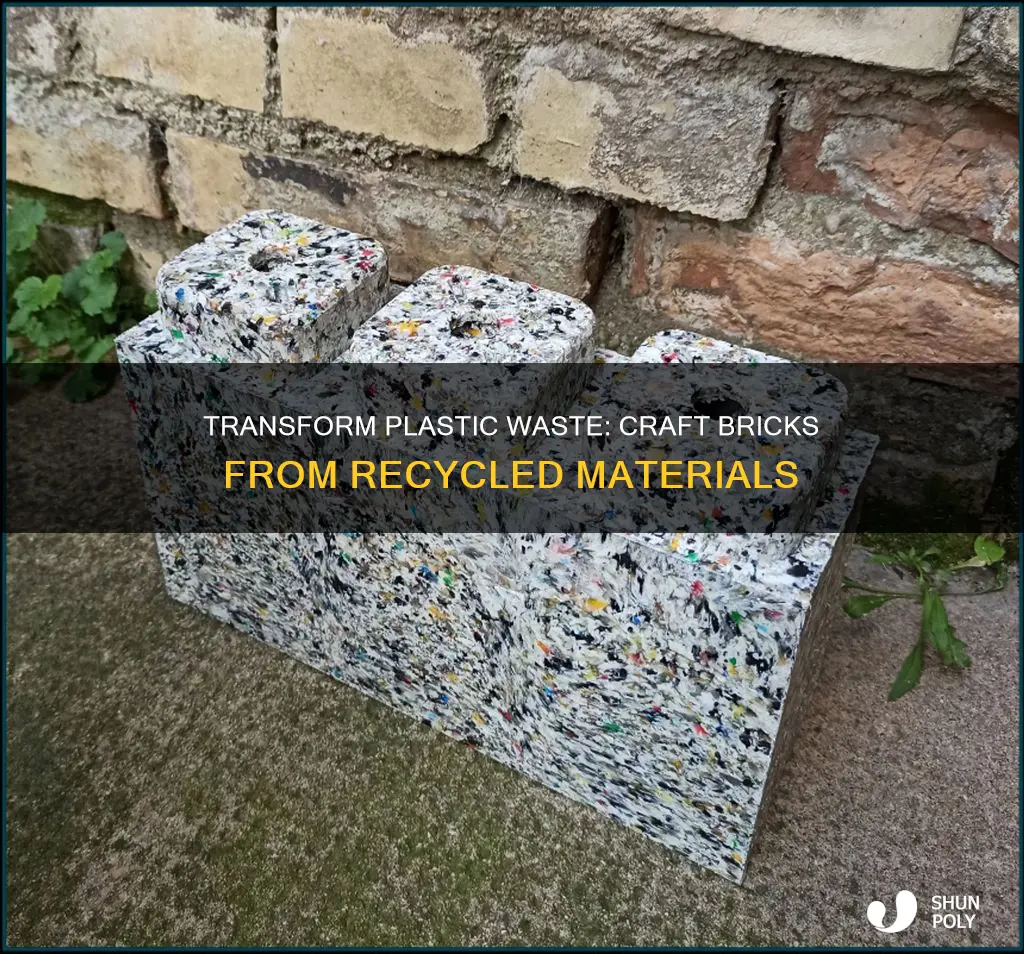
Recycling plastic into bricks is an innovative and sustainable approach to waste management. This process involves transforming plastic waste into a durable building material, offering a unique solution to the growing plastic pollution crisis. By utilizing plastic, which is often challenging to recycle due to its lightweight nature, we can create a sturdy and eco-friendly alternative to traditional bricks. This method not only reduces the amount of plastic in landfills and the environment but also provides a cost-effective and environmentally conscious building material, making it an attractive option for construction projects and a step towards a greener future.
What You'll Learn
- Collection and Sorting: Gather and separate plastic waste by type and color for efficient recycling
- Melt and Mold: Heat plastic to a molten state, then pour and shape into brick forms
- Reinforcement and Strength: Add fillers or fibers to enhance durability and structural integrity
- Curing and Hardening: Allow bricks to cool and harden, ensuring proper setting and stability
- Testing and Quality Control: Inspect bricks for strength, appearance, and adherence to specifications
Collection and Sorting: Gather and separate plastic waste by type and color for efficient recycling
The process of recycling plastic into bricks begins with a crucial step: collection and sorting. This initial phase is essential to ensure the efficiency and effectiveness of the entire recycling process. Here's a detailed guide on how to approach this stage:
Collection: The first step is to gather plastic waste from various sources. This can include household items, such as water bottles, milk jugs, and food containers, as well as larger items like furniture, electronics, and construction debris. It is important to collect plastic waste separately from other recyclables to maintain a clean and organized stream of materials. Local recycling centers or waste management facilities often have designated areas or bins for plastic collection, making it easier for the public to participate.
Sorting by Type: Plastic recycling requires careful sorting to ensure that different types of plastic are processed appropriately. Common types of plastic include PET (polyethylene terephthalate), HDPE (high-density polyethylene), PVC (polyvinyl chloride), LDPE (low-density polyethylene), and PP (polypropylene). Each type has unique properties and applications, and recycling them together can lead to contamination. For instance, PET is commonly used for beverage bottles and can be recycled into fibers for clothing or new containers. HDPE is often found in milk jugs and shampoo bottles and can be recycled into outdoor furniture or compost bins. Sorting these plastics by type ensures that they can be processed further without interference.
Sorting by Color: In addition to sorting by type, it is also beneficial to separate plastics by color. Different colors may have varying levels of contamination or require specific processing methods. For example, clear and green PET bottles are often highly valued for their purity and can be recycled into high-quality products. On the other hand, black or blue PET may contain more contaminants and might be recycled into lower-grade materials. By sorting plastics by color, you can optimize the recycling process and potentially increase the value of the recycled material.
Manual and Automated Sorting: Sorting plastic waste can be done through both manual and automated processes. Manual sorting involves trained personnel who visually inspect and separate the plastics. This method is often used for small-scale recycling operations or when dealing with complex plastic mixtures. Automated sorting, on the other hand, utilizes machines like optical sorters and air classifiers. Optical sorters can identify different types of plastic based on their color and shape, while air classifiers use air currents to separate plastics by density. Automated sorting is more efficient and can handle large volumes of waste, making it a preferred method for large-scale recycling operations.
Efficient collection and sorting are fundamental to the success of plastic recycling into bricks. By following these steps, recycling centers can ensure that the incoming plastic waste is clean, sorted correctly, and ready for the next stage of the recycling process, ultimately contributing to a more sustainable and environmentally friendly approach to waste management.
Unraveling Plastic Recycling: A Guide to Finding Codes
You may want to see also
Melt and Mold: Heat plastic to a molten state, then pour and shape into brick forms
The process of recycling plastic into bricks through the melt and mold method is a fascinating and sustainable approach to waste management. This technique involves transforming plastic waste into a valuable building material, offering an eco-friendly alternative to traditional bricks. Here's a step-by-step guide to achieving this:
Step 1: Collection and Sorting
Begin by collecting plastic waste, ensuring it is clean and sorted by type. Common household plastics like PET (polyethylene terephthalate) and HDPE (high-density polyethylene) are ideal. Proper sorting is crucial as it determines the quality of the final bricks.
Step 2: Shredding and Grinding
Once sorted, the plastic needs to be processed. Shred the plastic into small pieces to increase the surface area, making it easier to melt. Then, grind these pieces into a fine powder. This step ensures that the plastic can be effectively mixed with other materials and molded into the desired shape.
Step 3: Melting and Mixing
In this critical phase, the plastic powder is heated to a molten state. Specialized equipment like a plastic melter or a furnace can be used for this purpose. As the plastic melts, it becomes a viscous liquid. At this stage, you can add other materials such as sand, clay, or even recycled glass to enhance the brick's strength and appearance. Proper mixing ensures a homogeneous mixture, which is essential for consistent brick production.
Step 4: Pouring and Shaping
With the molten plastic ready, it's time to shape it into bricks. Prepare the brick forms by placing them in a mold or a custom-made frame. Carefully pour the molten plastic into the forms, ensuring it fills the entire space. The plastic will start to cool and solidify as it comes into contact with the air. This cooling process is crucial for the brick's structural integrity.
Step 5: Curing and Finishing
After the plastic has set, remove the bricks from the forms. Allow them to cure further by placing them in a controlled environment with optimal temperature and humidity. This step ensures the bricks reach their full strength. Once cured, you can sand and finish the bricks to achieve a smooth surface. This method allows for customization, enabling you to create bricks in various colors and textures by adding different pigments or materials during the melting process.
This melt and mold technique is a powerful way to recycle plastic, offering a second life to waste while contributing to sustainable construction practices. It provides an innovative solution to the growing plastic waste problem, all while creating a durable and eco-conscious building material.
Plastic Hanger Recycling: Where to Find the Right Drop-Off Points
You may want to see also
Reinforcement and Strength: Add fillers or fibers to enhance durability and structural integrity
When it comes to recycling plastic into bricks, reinforcement and strength are crucial aspects to ensure the structural integrity and durability of the final product. One effective method to achieve this is by incorporating fillers or fibers into the plastic mixture. These additives play a vital role in enhancing the material's properties, making it more robust and suitable for various applications.
Fillers, such as clay, sand, or calcium carbonate, can be added to the plastic composition to increase its density and overall strength. Clay, for instance, is a common choice due to its natural binding properties. When mixed with plastic, it helps improve the material's compressive strength and reduces the likelihood of cracking or breaking. Sand, on the other hand, provides additional structural support and can be particularly useful in creating a more uniform and consistent brick texture. These fillers act as a reinforcement, distributing the load more evenly and preventing the plastic from becoming brittle.
Fiber reinforcement is another powerful technique to consider. Natural fibers like hemp, flax, or jute, or synthetic fibers such as glass or carbon fiber, can be blended into the plastic mixture. These fibers provide exceptional tensile strength, making the plastic bricks more resistant to external forces and impact. The addition of fibers also contributes to the material's flexibility, allowing it to withstand slight deformations without permanent damage. This is especially beneficial for outdoor applications where the bricks might be exposed to varying environmental conditions.
The process of incorporating fillers or fibers requires careful consideration of the plastic's melting point and the compatibility of the additives. It is essential to ensure that the fillers and fibers are thoroughly mixed and evenly distributed throughout the plastic matrix. This can be achieved through various mixing techniques, such as using specialized equipment or employing specific mixing procedures to guarantee a homogeneous blend. By doing so, you create a consistent and reinforced plastic brick that meets the desired strength requirements.
In summary, adding fillers or fibers to the plastic recycling process is a strategic approach to enhance the durability and structural integrity of plastic bricks. These additives provide much-needed reinforcement, improving the material's strength, flexibility, and overall performance. With the right combination of fillers and fibers, recycled plastic bricks can become a viable and sustainable building material, offering both environmental benefits and structural reliability.
Ottawa's Plastic Utensil Recycling: What You Need to Know
You may want to see also
Curing and Hardening: Allow bricks to cool and harden, ensuring proper setting and stability
The process of recycling plastic into bricks involves several crucial steps, and one of the most important is the curing and hardening phase. This stage is essential to ensure the structural integrity and longevity of the bricks. After the plastic is melted and molded into brick shapes, it needs to be allowed to cool and set properly.
Curing is a critical process that begins immediately after the bricks are formed. It involves maintaining a controlled environment to facilitate the chemical reactions that transform the molten plastic into a solid, durable material. The bricks should be placed in a cool, dry area, away from direct sunlight or heat sources, as excessive temperatures can cause the plastic to degrade or melt. During this phase, it is crucial to monitor the temperature and humidity to create an optimal curing environment.
Hardening is the subsequent step that follows the initial cooling period. As the bricks cool, they undergo a transformation where the plastic becomes more rigid and less pliable. This hardening process can take several hours or even days, depending on the size and thickness of the bricks. Proper hardening ensures that the bricks gain sufficient strength and durability to withstand various environmental conditions. It is important to note that the hardening process should be gradual, allowing the plastic to set and interlock with the aggregate, creating a strong bond.
To ensure proper setting and stability, it is recommended to stack the bricks in a controlled manner, allowing them to support each other's weight. This practice helps distribute the stress evenly and prevents any potential cracking or warping. Additionally, providing a protective covering or sealant to the bricks can further enhance their protection against moisture and environmental factors, ensuring their long-term stability.
In summary, the curing and hardening process is a critical aspect of recycling plastic into bricks, requiring careful monitoring of temperature and humidity. By allowing the bricks to cool and harden gradually, you ensure that the plastic solidifies and interlocks with the aggregate, resulting in strong and durable bricks. This step is fundamental to the overall success of the project, ensuring the bricks' stability and performance in various applications.
Can Plastic Flowers Be Recycled? Unveiling the Truth
You may want to see also
Testing and Quality Control: Inspect bricks for strength, appearance, and adherence to specifications
The process of transforming recycled plastic into bricks requires rigorous testing and quality control to ensure the final product meets the desired standards. This step is crucial to guarantee the structural integrity and overall performance of the bricks. Here's an overview of the testing and quality control procedures:
Strength Testing: One of the primary concerns when using recycled materials is the structural strength of the bricks. To assess this, a compression test can be conducted. In this test, bricks are subjected to increasing pressure until they fail. The test results provide valuable data on the brick's compressive strength, which should meet or exceed industry standards for building materials. Engineers can also perform bending tests to evaluate the brick's ability to withstand loads without breaking or deforming. These tests are essential to ensure the bricks can support the weight of structures and resist structural failures.
Appearance and Visual Inspection: The visual appeal of the bricks is another critical aspect of quality control. Inspectors should check for any visible defects, such as cracks, voids, or uneven surfaces. Bricks with a consistent color and texture that resemble traditional clay bricks are preferred. Any visible signs of contamination or improper mixing of materials should be noted. The goal is to produce bricks that are aesthetically pleasing and blend seamlessly with other construction materials.
Adherence to Specifications: Quality control also involves verifying that the bricks comply with the specified dimensions, weight, and performance criteria. Each batch of bricks should be measured and weighed to ensure they meet the required specifications. This includes checking the length, width, height, and weight of individual bricks, as well as the overall batch consistency. Adherence to specifications is vital for construction projects, as it ensures compatibility with other building materials and facilitates proper assembly.
During the testing and quality control process, it is essential to document all findings and observations. This documentation should include detailed reports on the test methods, results, and any deviations from the expected standards. By maintaining comprehensive records, manufacturers can identify patterns, address potential issues, and make necessary adjustments to their production processes.
Furthermore, regular audits and inspections should be conducted to ensure consistent quality. This may involve sending samples to independent laboratories for additional testing and certification. By combining in-house quality control with external validation, manufacturers can build a strong reputation for producing reliable and sustainable building materials.
Unraveling California's Plastic Straw Recycling Conundrum: What You Need to Know
You may want to see also
Frequently asked questions
The process involves collecting and sorting plastic waste, which is then cleaned and shredded into small pieces. These plastic flakes are heated and mixed with a binding agent to create a malleable mixture. The mixture is then pressed and molded into brick shapes and left to cool and harden. Finally, the bricks are cut to size and can be used for various construction purposes.
Yes, certain types of plastic are more suitable for brick production. High-density polyethylene (HDPE) and polypropylene (PP) are commonly used due to their durability and ease of processing. These plastics are often chosen because they can withstand the heat and pressure required to form bricks without compromising their structural integrity.
Absolutely! Recycled plastic bricks have gained popularity in the construction industry as an eco-friendly alternative to traditional bricks. They are lightweight, making them easier to handle and transport, and can provide excellent insulation properties. These bricks can be used for various applications, including wall construction, flooring, and even decorative elements in modern architecture.
Recycling plastic into bricks offers multiple environmental advantages. Firstly, it diverts plastic waste from landfills or incinerators, reducing the strain on these resources. By reusing plastic, we can conserve natural resources and decrease the demand for new raw materials. Additionally, the production of plastic bricks often requires less energy compared to conventional brick-making processes, resulting in lower carbon emissions and a smaller environmental footprint.