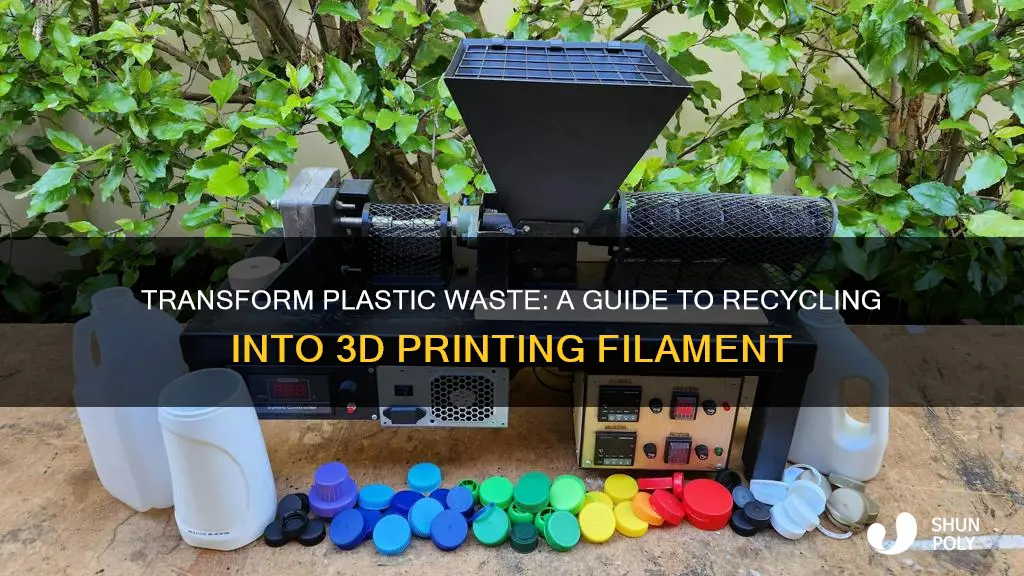
Recycling plastic into filament is an innovative process that transforms waste into a valuable resource. It involves collecting and sorting plastic materials, such as PET bottles or HDPE containers, which are then cleaned and shredded into small pieces. These plastic flakes are further processed through a granulating machine to produce plastic pellets. The real magic happens when these pellets are heated and extruded through an extruder, creating a continuous strand of filament. This filament can be cooled and wound into spools, ready for 3D printing. By recycling plastic, we not only reduce waste but also contribute to a more sustainable and circular economy, making it an eco-friendly and cost-effective solution for creating new products.
What You'll Learn
- Collection: Gather plastic waste from various sources for recycling
- Sorting: Separate different types of plastic to ensure quality
- Cleaning: Rinse and remove contaminants to prepare plastic for processing
- Shredding/Granulating: Break down plastic into small pieces or pellets
- Filament Extrusion: Melt and push plastic through a die to create filament
Collection: Gather plastic waste from various sources for recycling
The first step in recycling plastic into filament is the collection process, which is crucial for the success of the entire project. You can start by gathering plastic waste from various sources, ensuring a steady supply of raw materials for your recycling endeavor. One of the most accessible sources is household waste. Many homes accumulate plastic items like water bottles, milk jugs, and food containers over time. Encourage family members or roommates to set aside these items for recycling, ensuring a consistent flow of raw material.
For a more organized approach, consider partnering with local businesses or community organizations. Many offices, restaurants, and grocery stores generate significant amounts of plastic waste daily. Reach out to these establishments and propose a recycling program where they can set aside their plastic waste for you to collect. You could even offer to provide a dedicated bin for their use, making it a convenient and visible part of their daily operations.
Another valuable source is community recycling events or clean-up drives. These initiatives often collect plastic waste from public spaces, parks, and beaches, ensuring that hard-to-reach areas are also included in the recycling process. By participating in or organizing such events, you can gather a diverse range of plastic items, from single-use packaging to larger items like plastic furniture or construction debris.
When collecting plastic waste, it's essential to be thorough and systematic. Sort the plastic items by type and color to ensure they can be processed correctly later. For example, separate PET (polyethylene terephthalate) bottles from HDPE (high-density polyethylene) containers, as they have different melting points and uses in filament production. Additionally, remove any non-plastic components, such as caps, labels, or metal screws, to ensure a clean and consistent feed for the recycling process.
Remember, the quality of the collected plastic waste directly impacts the final product's strength and durability. Therefore, it's crucial to maintain high standards during the collection phase to ensure a successful transition from waste to filament.
Mastering Mass Recycling: A Guide to Plastic Waste Management
You may want to see also
Sorting: Separate different types of plastic to ensure quality
The process of recycling plastic into filament is a fascinating journey that requires careful attention to detail, especially when it comes to sorting. Proper sorting is a critical step to ensure the quality and success of the filament production. Here's a detailed guide on why and how to separate different types of plastics:
Understanding Plastic Types: Plastic recycling is a complex task due to the vast number of plastic types available. Each type has unique properties and chemical compositions, making them unsuitable for mixing. Common plastic types include PET (polyethylene terephthalate), HDPE (high-density polyethylene), LDPE (low-density polyethylene), PVC (polyvinyl chloride), and PP (polypropylene). These plastics are often identified by their resin identification codes, which are usually found on the bottom of containers. Understanding these codes is essential for proper sorting.
Sorting Process: Sorting plastic waste begins with a comprehensive collection process. Different colors and types of plastic should be separated to facilitate the recycling process. Here's a step-by-step approach:
- Color Sorting: Start by separating plastics based on color. For example, clear PET bottles, green HDPE milk jugs, and black PP containers. This initial sorting helps in creating a more organized stream of materials.
- Type Identification: After color sorting, identify the specific types of plastic. PET is commonly used in beverage bottles and food packaging. HDPE is found in milk jugs, shampoo bottles, and some containers. LDPE is often used for shopping bags and film packaging. PVC is used in pipes, electrical cables, and some food packaging. PP is known for its durability and is used in yogurt cups and bottle caps. Each type has its own recycling challenges and applications.
- Manual Sorting: For a more precise separation, manual sorting is ideal. This involves trained personnel who can identify and separate plastics based on their experience and knowledge of plastic types. They can also remove any contaminants like labels, caps, or non-plastic items. Manual sorting ensures that only clean and pure plastic types are used for filament production.
- Automated Sorting: Modern recycling facilities often employ automated systems for efficient sorting. These machines use infrared sensors, near-infrared spectroscopy, or eddy current technology to identify and separate plastics based on their unique properties. Automated sorting increases speed and accuracy, especially when dealing with large volumes of waste.
Benefits of Proper Sorting: Sorting different types of plastics is crucial for several reasons. Firstly, it ensures the quality of the recycled filament. Each plastic type has its own melting point, strength, and flexibility, which are essential considerations for filament manufacturing. Mixing incompatible plastics can result in a weak and inconsistent product. Secondly, proper sorting allows for the creation of specific plastic blends, catering to various applications. For example, a blend of PET and PP can produce a durable and flexible filament suitable for 3D printing.
Challenges and Solutions: Sorting plastics can be challenging due to the complexity of the task. Contaminants like food residue or labels can make identification difficult. To overcome this, advanced sorting techniques and training can be implemented. Additionally, educating the public about proper waste segregation at the source can significantly improve the recycling process.
In summary, sorting different types of plastics is a critical step in recycling them into high-quality filament. It requires a combination of color sorting, manual identification, and automated systems to ensure purity and consistency. By following these practices, we can maximize the potential of plastic recycling and contribute to a more sustainable future.
New Orleans Recycling: Unveiling the Truth Behind Plastic Drop-Off
You may want to see also
Cleaning: Rinse and remove contaminants to prepare plastic for processing
Cleaning and preparing plastic for the filament-making process is a crucial step to ensure the quality and success of your recycled material. This step involves removing any contaminants and ensuring the plastic is clean and ready for further processing. Here's a detailed guide on how to effectively clean and prepare your plastic:
Rinsing Process: Begin by thoroughly rinsing the collected plastic waste. This initial step is essential to eliminate any loose dirt, debris, or contaminants that may be present on the surface of the plastic. Use clean water and a gentle stream to wash the plastic items. For larger plastic items or those with intricate shapes, consider using a soft-bristled brush to remove any stubborn dirt. Ensure that you rinse both sides and all surfaces of the plastic to ensure a comprehensive clean.
Contaminant Removal: After rinsing, it's crucial to remove any remaining contaminants. Start by separating the plastic into different types if you have a mixed batch. Common types of plastic include PET, HDPE, PVC, and more. You can use a plastic identification guide to help with this process. Then, for each type of plastic, use a suitable cleaning method. For example, you can soak the plastic in a mild detergent solution to break down any remaining grime. Alternatively, for more stubborn stains, consider using a vinegar and water mixture, which is effective and eco-friendly. Ensure that you follow the appropriate safety precautions when handling chemicals.
Drying: Proper drying is essential to prevent moisture-related issues during the filament processing. After cleaning, thoroughly rinse the plastic again to remove any detergent residue. Then, spread the cleaned and sorted plastic items out on a clean, dry surface. Allow them to air-dry completely. You can speed up the drying process by using fans or a well-ventilated oven set to a low temperature. Ensure that the plastic is completely dry before proceeding to the next step, as moisture can affect the filament's performance.
Sorting and Categorization: As you clean and dry the plastic, take the opportunity to sort and categorize it. This step is vital for organizing your recycled material and ensuring a consistent filament output. Group similar types of plastic together and consider their colors and sizes. Proper sorting will make the subsequent steps more efficient and enable you to create specific filament colors or sizes if desired.
By following these cleaning and preparation steps, you'll be well-prepared to process the plastic and create high-quality, recycled filaments. This process not only ensures the longevity of your filament but also contributes to a more sustainable and environmentally friendly approach to recycling.
Unraveling the Mystery: Can Plastic Tablecloths Be Recycled?
You may want to see also
Shredding/Granulating: Break down plastic into small pieces or pellets
Shredding and granulating are crucial steps in the process of recycling plastic into filament, a process that transforms waste plastic into a usable material for 3D printing and other applications. This method involves breaking down the plastic into smaller pieces or pellets, which can then be further processed into filament.
The first step in this process is shredding, which involves reducing the plastic waste into smaller, manageable pieces. This can be done using a shredder, which is a machine designed to cut and tear plastic into thin strips or flakes. The shredder's blades are sharp and designed to handle various plastic types, ensuring that the plastic is broken down effectively. It is important to use a shredder specifically designed for plastic recycling to avoid damaging the machine or the plastic itself. The shredded plastic can then be further processed, often through a granulating process.
Granulating is the next step, where the shredded plastic is transformed into small, uniform pellets. This process involves feeding the shredded plastic into a granulator, which is a machine with a rotating drum or a set of blades. As the plastic is fed, it is heated and compressed, causing it to melt and form small, solid pellets. These pellets are the raw material for filament production. The granulator's design and settings are crucial to ensure the plastic is properly processed and the pellets are of good quality. The temperature and duration of the heating process should be carefully controlled to avoid overheating or underheating the plastic.
The shredded and granulated plastic is now ready for the next stage, which could involve further cleaning, drying, and sorting to ensure the highest quality of the final filament. This process requires precision and attention to detail to produce a consistent and reliable product. The size and shape of the pellets can vary depending on the desired application and the specific requirements of the filament production process.
In summary, shredding and granulating are essential techniques in recycling plastic into filament. These processes break down plastic waste into smaller, more manageable pieces, making it easier to work with and process further. By employing the right equipment and techniques, it is possible to produce high-quality plastic pellets, which are the foundation for creating useful and sustainable filament.
Tyler, Texas: Plastic Recycling Options Available in Stores?
You may want to see also
Filament Extrusion: Melt and push plastic through a die to create filament
Filament extrusion is a crucial process in recycling plastic into a usable form for 3D printing. This method involves melting and pushing plastic through a die to create a continuous filament, which can then be used to print various objects. Here's a detailed guide on how to achieve this:
Process Overview:
Filament extrusion begins with the selection of a suitable plastic material, typically a type commonly used in 3D printing, such as ABS, PLA, or PETG. The chosen plastic is then fed into the extruder, which is the heart of the process. The extruder heats the plastic to its melting point, ensuring it becomes a viscous liquid. This is a critical step, as the plastic must be heated to the right temperature to facilitate the extrusion process without burning or damaging the material. Once melted, the plastic is pushed through a heated extrusion nozzle, which acts as a die. The nozzle's temperature is carefully controlled to maintain the plastic's viscosity and ensure a smooth flow.
Extruder Setup:
The extruder is a complex machine with several components. It consists of a heating element, a motor, and a drive gear system. The heating element is responsible for melting the plastic, and its temperature can be adjusted to suit different materials. The motor drives the gear system, which in turn pushes the plastic through the nozzle. It's essential to calibrate the extruder's temperature and speed to ensure consistent filament production. Many 3D printers come with pre-set temperature profiles for various plastics, making this step more accessible.
Die and Nozzle:
The die, or extrusion nozzle, is a critical component in shaping the plastic. It has a small orifice through which the melted plastic is pushed. The size and design of the die determine the diameter and strength of the resulting filament. Different nozzles can be used to create filaments of various sizes, allowing for customization in the printing process. For instance, a larger nozzle might be used for creating thicker filaments, while a smaller one is suitable for finer details.
Filament Collection and Cooling:
As the plastic exits the die, it is collected on a cooling platform or take-up reel. This rapid cooling solidifies the plastic, forming a continuous strand of filament. The cooling process is vital to ensure the filament's stability and prevent it from becoming too soft or malleable. The cooling platform's temperature and speed are adjustable, allowing for control over the filament's final properties.
Post-Processing:
After extrusion, the filament may undergo additional post-processing steps. This can include trimming, cutting, or further cooling to improve its quality and consistency. Proper handling and storage of the recycled filament are essential to maintain its integrity and ensure successful 3D printing.
Plastic Recycling: Unraveling the Mystery of Envelopes: To Tear or Not to Tear?
You may want to see also
Frequently asked questions
Recycling plastic into filament, also known as 3D printing filament, involves a process called extrusion. It starts with collecting and sorting plastic waste, which is then cleaned and shredded into small pieces. These pieces are melted and pushed through a die to create a continuous strand of filament. The filament is cooled and wound onto a spool, ready for 3D printing.
Common plastics used for this purpose include PET (polyethylene terephthalate), found in beverage bottles, and HDPE (high-density polyethylene), used for milk jugs and shampoo bottles. Other types like PLA (polylactic acid), made from renewable resources, and ABS (acrylonitrile butadiene styrene) are also recycled and used to create filament.
The quality can vary depending on the recycling process and the type of plastic. Recycled filament may have some limitations, such as reduced strength and durability compared to virgin filament. However, with advancements in recycling technology, the quality is improving, and many manufacturers now produce high-quality recycled filament that is suitable for various applications.
Absolutely! Recycling plastic reduces the demand for virgin plastic production, which often relies on fossil fuels. It helps conserve natural resources, lowers energy consumption, and minimizes the environmental impact associated with plastic manufacturing. Additionally, it diverts plastic waste from landfills or incinerators, contributing to a more sustainable waste management system.
While it is possible to recycle certain types of plastic at home, it's important to note that not all plastics are suitable for this process. PET and HDPE are commonly recycled at home. However, for more complex recycling, specialized equipment and knowledge are required. It's recommended to check local recycling guidelines and consider sending your plastic waste to specialized recycling facilities for better results.