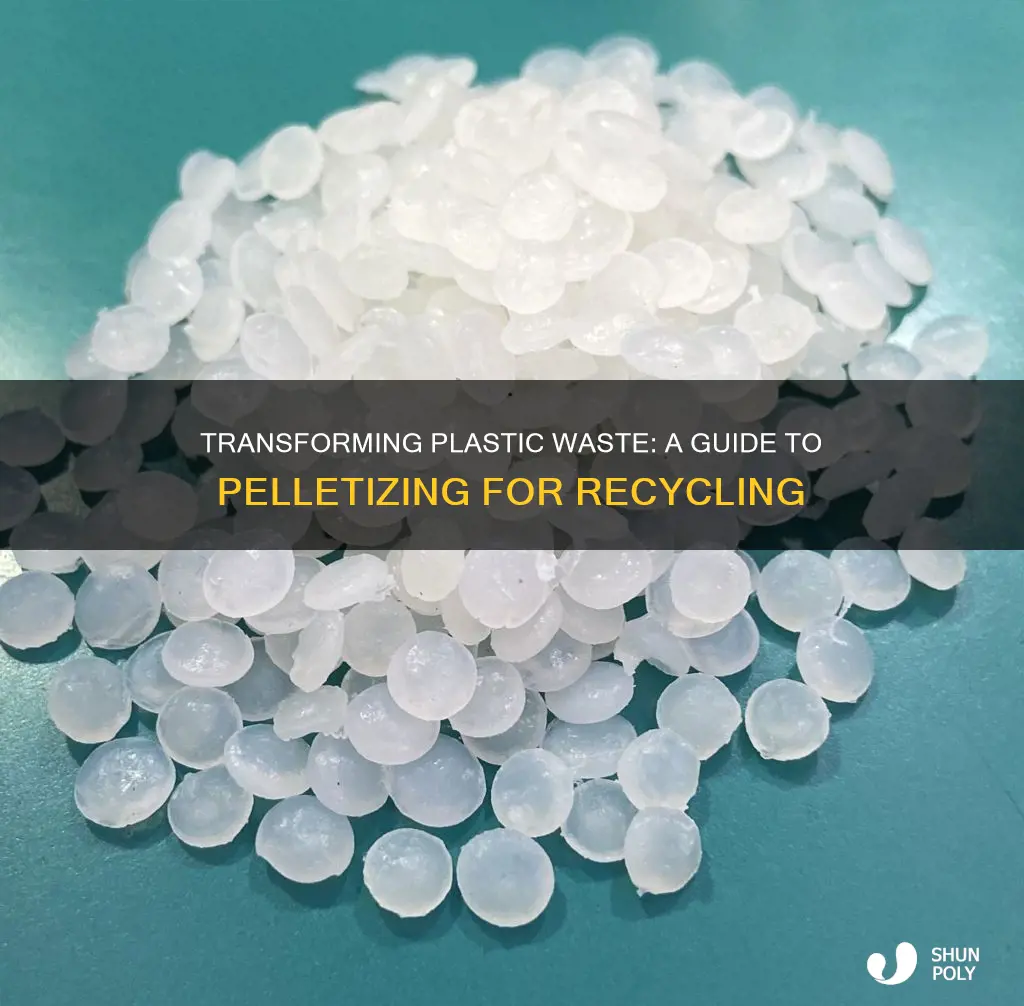
Recycling plastic is an essential process to reduce waste and promote sustainability. One effective method to transform plastic waste into a valuable resource is through the process of pelletization. Plastic pellets, also known as plastic resin pellets, are created by shredding and drying plastic materials, which are then ground into small, uniform particles. This process involves several steps, including sorting and cleaning the plastic, shredding it into flakes, washing and drying the flakes to remove impurities, and finally, pelletizing the dried material. Plastic pellets serve as a raw material for manufacturing various products, such as packaging, textiles, and construction materials, contributing to a circular economy and reducing the environmental impact of plastic waste.
What You'll Learn
- Collection: Gather plastic waste, ensuring it's clean and sorted by type
- Shredding: Break down plastic into small pieces for easier processing
- Cleaning: Remove contaminants like labels and caps for quality pellets
- Drying: Dry the shredded plastic to prevent moisture-related issues during pelletizing
- Pelletizing: Use an extruder to melt and shape plastic into uniform pellets
Collection: Gather plastic waste, ensuring it's clean and sorted by type
The first step in the recycling process is collection, and it is crucial to start with high-quality raw materials to ensure the efficiency and success of the entire recycling journey. When it comes to collecting plastic waste for pellet production, the goal is to gather clean and properly sorted plastic materials. This initial stage sets the foundation for the entire recycling process and significantly impacts the final product's quality.
Begin by identifying and setting up collection points in your community or organization. These collection centers should be easily accessible to encourage participation and ensure a steady supply of plastic waste. It is essential to promote a culture of responsible waste management and recycling. Educate the community about the importance of clean and sorted plastic waste. Provide clear guidelines and instructions on what types of plastic are acceptable for recycling. Common household plastics like PET (polyethylene terephthalate), HDPE (high-density polyethylene), and PP (polypropylene) are often accepted, but it's crucial to check local recycling guidelines.
During the collection process, ensure that the plastic waste is free from contaminants such as food residue, labels, and non-plastic items. Rinse out containers to remove any remaining liquids or food particles. This step is vital as it prevents contamination and ensures the plastic can be effectively recycled. For example, PET bottles should be empty and rinsed to remove any liquid residues. Additionally, separate the plastic waste into different categories based on the type of plastic. This sorting process is essential as it allows for more efficient recycling and the production of specific pellet types.
For instance, PET bottles can be collected separately from other plastic items like containers or packaging. This separation ensures that the recycling process can be tailored to the specific requirements of each plastic type. It also enables the production of customized pellets for various applications. By sorting the plastic waste, you create a more organized and manageable stream of materials, making it easier to process and recycle effectively.
In summary, the collection phase is a critical step in recycling plastic into pellets. It requires a well-organized system that encourages participation and promotes responsible waste management. By collecting clean and sorted plastic waste, you lay the groundwork for a successful recycling process, ultimately leading to the production of high-quality plastic pellets for various industrial and commercial applications. This initial step is a key enabler in the journey towards a more sustainable and environmentally friendly future.
Eco-Friendly Choices: Can USPS Plastic Mailers Be Recycled?
You may want to see also
Shredding: Break down plastic into small pieces for easier processing
Shredding is a crucial step in the process of recycling plastic into pellets, as it significantly reduces the size of the plastic waste, making it easier to handle and process. This initial stage of recycling involves breaking down larger plastic items or sheets into smaller, manageable pieces, which can then be further processed into the desired pellet form. The shredding process is designed to minimize the volume of plastic waste, making it more cost-effective and efficient to transport and store.
To begin shredding, you'll need specialized equipment such as a shredder or granulator, which can be either manual or automated. The choice of equipment depends on the scale of the operation and the specific requirements of your recycling facility. For smaller-scale recycling, a manual shredder might be sufficient, while larger operations may require automated machinery. The shredder's blades are designed to cut through the plastic, breaking it down into thin strips or flakes. This process is highly efficient and ensures that the plastic is reduced to a consistent size, which is essential for the subsequent steps in pellet production.
When shredding, it's important to consider the type of plastic you are working with. Different types of plastic have varying properties and melting points, so the shredding process should be tailored accordingly. For instance, high-density polyethylene (HDPE) and low-density polyethylene (LDPE) have different shredding requirements compared to polypropylene (PP) or polystyrene (PS). Proper identification and sorting of plastic types are crucial to ensure the quality of the final product.
The shredded plastic material is then typically sorted to separate any contaminants or non-plastic items that may have been included in the initial waste stream. This step is vital to maintain the purity of the recycled plastic and ensure that the final pellets meet the required standards. After sorting, the shredded plastic is often washed to remove any remaining impurities, such as dirt or residual chemicals. This washing process helps to improve the overall quality and appearance of the recycled material.
Once the shredded plastic has been cleaned and sorted, it is ready for the next stage of the recycling process, which involves further processing to create the final pellet form. The shredded material is fed into a machine that melts and extrudes the plastic, shaping it into small, uniform pellets. These pellets can then be used as raw materials for manufacturing various plastic products, contributing to a more sustainable and circular economy.
Unraveling the Mystery: Can Plastic Balloons Be Recycled?
You may want to see also
Cleaning: Remove contaminants like labels and caps for quality pellets
The process of recycling plastic into pellets involves several steps to ensure the final product is of high quality and free from contaminants. One crucial aspect is cleaning the plastic waste to remove any impurities that could affect the pellet's performance and durability. This step is essential to guarantee that the recycled pellets meet the required standards for various applications.
When cleaning plastic waste, the first step is to separate the different types of plastics. This process, known as sorting, is vital as it allows for more efficient cleaning and recycling. For instance, PET (polyethylene terephthalate) and HDPE (high-density polyethylene) plastics have distinct properties and uses, so keeping them separate ensures that the cleaning process is tailored to each type. This can be done manually or through automated systems, where sensors identify the plastic type based on its color and material characteristics.
After sorting, the plastic waste needs to be cleaned to remove any remaining contaminants. This includes taking off labels, caps, and any other non-plastic materials attached to the waste. Labels, for example, often contain inks and glues that can be harmful to the recycling process and the final product. Caps, which are typically made of a different type of plastic, should be separated and recycled accordingly. This step requires careful handling to avoid damaging the plastic itself.
One effective method for removing labels and caps is through a process called 'washing'. This involves soaking the plastic waste in a detergent solution to loosen and remove any attached contaminants. The detergent helps to break down the glue or adhesive used in labels, making it easier to separate. After soaking, the plastic can be scrubbed manually or using specialized cleaning equipment to ensure all contaminants are removed. This process should be repeated until the plastic is clean and free from any visible impurities.
Once the cleaning process is complete, the plastic waste is ready for the next stage of recycling, which involves shredding or granulating the material into smaller pieces. These pieces are then dried to remove any moisture, which is crucial for the subsequent pelletization process. By following these cleaning procedures, the recycled plastic pellets will be of higher quality, ensuring they can be used in various industries, such as manufacturing, construction, and packaging, without compromising performance or safety.
Unraveling the Mystery: A Guide to Recycling Plastic
You may want to see also
Drying: Dry the shredded plastic to prevent moisture-related issues during pelletizing
The process of recycling plastic into pellets involves several crucial steps, and one of the most important is drying the shredded plastic material. Moisture content in the plastic can lead to significant problems during the pelletizing process, affecting the quality and performance of the final product. Here's a detailed guide on why and how to dry the shredded plastic effectively:
Understanding the Issue with Moisture:
Plastic, especially when exposed to humid environments, can absorb moisture over time. This moisture absorption can cause several issues. Firstly, it may lead to the formation of water droplets on the plastic surface, which can interfere with the pelletizing process. During pelletizing, the plastic is heated and compressed to create small pellets. Moisture can cause the plastic to become sticky, making it challenging to form uniform pellets. Secondly, high moisture content can result in uneven melting and cooling of the plastic, leading to inconsistent pellet size and quality.
Drying Techniques:
To address this issue, proper drying methods are essential. Here's a step-by-step approach:
- Initial Drying: After shredding the plastic waste, it's crucial to remove surface moisture immediately. This can be achieved by using a simple air knife or a brief exposure to warm air. This initial step ensures that the shredded plastic is ready for further processing without excessive moisture.
- Vacuum Drying: For more effective drying, consider using a vacuum system. Place the shredded plastic in a sealed container and apply a vacuum to remove moisture. This method is particularly useful for larger quantities of plastic waste. The vacuum helps to accelerate the drying process by drawing out moisture from the material.
- Oven Drying: For more precise control, an oven can be employed. Preheat the oven to an appropriate temperature, typically around 150-180°C (300-350°F), depending on the type of plastic. Place the shredded plastic in the oven for a controlled duration to ensure thorough drying. This method is ideal for small batches or when specific moisture levels need to be achieved.
- Monitoring Moisture Content: It is essential to monitor the moisture content of the dried plastic regularly. Moisture meters or similar devices can be used to ensure the plastic meets the required dryness standards. This step guarantees that the plastic is ready for the pelletizing process without any moisture-related complications.
By implementing these drying techniques, you can effectively manage moisture in the shredded plastic, ensuring a smooth and efficient transition to the pelletizing stage of the recycling process. Proper drying is a critical factor in producing high-quality plastic pellets for various applications.
Cracker Barrel's Plastic Checkers: A Green Revolution or a Misleading Trend?
You may want to see also
Pelletizing: Use an extruder to melt and shape plastic into uniform pellets
Pelletizing is a crucial process in recycling plastic waste, transforming it into a valuable resource with numerous applications. This method involves using an extruder, a machine designed to melt and shape plastic materials into uniform pellets, which can then be used for various purposes, including manufacturing new products. Here's a detailed guide on how to pelletize plastic waste effectively:
The process begins with collecting and sorting plastic waste. It is essential to ensure that the plastic is clean and free from contaminants. Different types of plastics have varying melting points and properties, so proper sorting is critical. Common plastic types include PET (polyethylene terephthalate), HDPE (high-density polyethylene), and PVC (polyvinyl chloride), each requiring specific handling. After sorting, the plastic is shredded or granulated to reduce its size, making it easier to process.
Once the plastic is prepared, it is fed into the extruder, a key component in the pelletizing process. The extruder consists of a heating chamber and a shaping mechanism. As the plastic enters the chamber, it is heated to its melting point, typically around 200-300 degrees Celsius, depending on the type of plastic. The heat softens the plastic, allowing it to be shaped and formed. The extruder's shaping mechanism, often a die or a screen, then transforms the molten plastic into uniform pellets. This shaping process ensures that the final product has a consistent size and quality.
The temperature and speed of the extruder are critical factors in this process. Too high a temperature can cause the plastic to burn or degrade, while too low a temperature may result in uneven melting. Similarly, adjusting the speed of the extruder's shaping mechanism is essential to control the pellet size and ensure uniformity. The pellets produced are then cooled rapidly to solidify them, often using air or water cooling systems.
After the pellets are formed, they are cooled and dried to remove any moisture. This step is vital to prevent moisture absorption during storage or transportation, which could affect the quality of the final product. The dried pellets are then packaged and stored for future use. These pellets can be sold to manufacturers who use them as raw materials for producing various plastic products, such as packaging, furniture, and construction materials.
Pelletizing offers several advantages in plastic recycling. It allows for the creation of a standardized product, making it easier to transport and store. The process also enables the recycling of plastic waste on a larger scale, as the pellets can be used in manufacturing processes that require specific plastic inputs. Additionally, pelletizing helps reduce the volume of plastic waste, making it more environmentally friendly and cost-effective.
Seattle's Plastic 5: Unraveling Waste Management's Recycling Mystery
You may want to see also
Frequently asked questions
Plastic recycling involves collecting, sorting, and processing plastic waste to create a usable material. The process typically begins with the collection of various types of plastic, which are then sorted based on their resin types (e.g., PET, HDPE, LDPE). The sorted plastics are cleaned, shredded, or granulated to reduce their size. This material is then melted and extruded through a die to form small, uniform pellets. These pellets can be used as a raw material for manufacturing new products.
Proper preparation of plastic waste is crucial for efficient recycling. Start by cleaning the plastic items to remove any contaminants like food residue or labels. Rinse the items if necessary, especially for food-grade plastics. Flatten or break down large items to make them more manageable. Ensure that the plastic is dry and free from any debris. Different types of plastics have specific recycling codes (resin identification codes) on them, so separate them accordingly to ensure proper processing.
Many types of plastic can be recycled into pellets, including:
- PET (Polyethylene Terephthalate): Commonly used in beverage bottles and food containers.
- HDPE (High-Density Polyethylene): Found in milk jugs, shampoo bottles, and some containers.
- LDPE (Low-Density Polyethylene): Used in grocery bags, film wraps, and some containers.
- PP (Polypropylene): Used in food containers, bottle caps, and packaging.
- PS (Polystyrene): Often used in disposable cups, containers, and packaging materials.
- PVC (Polyvinyl Chloride): Used in construction materials, pipes, and some packaging.
Yes, recycling plastic into pellets offers several environmental advantages. It helps reduce the amount of plastic waste sent to landfills or incinerators, thus preventing the release of harmful greenhouse gases. Recycling plastic conserves natural resources as it reduces the need for virgin plastic production, which often relies on fossil fuels. It also minimizes energy consumption compared to manufacturing new plastic from raw materials. Additionally, the production of plastic pellets can create jobs and support the development of a circular economy, promoting sustainability and reducing environmental impact.