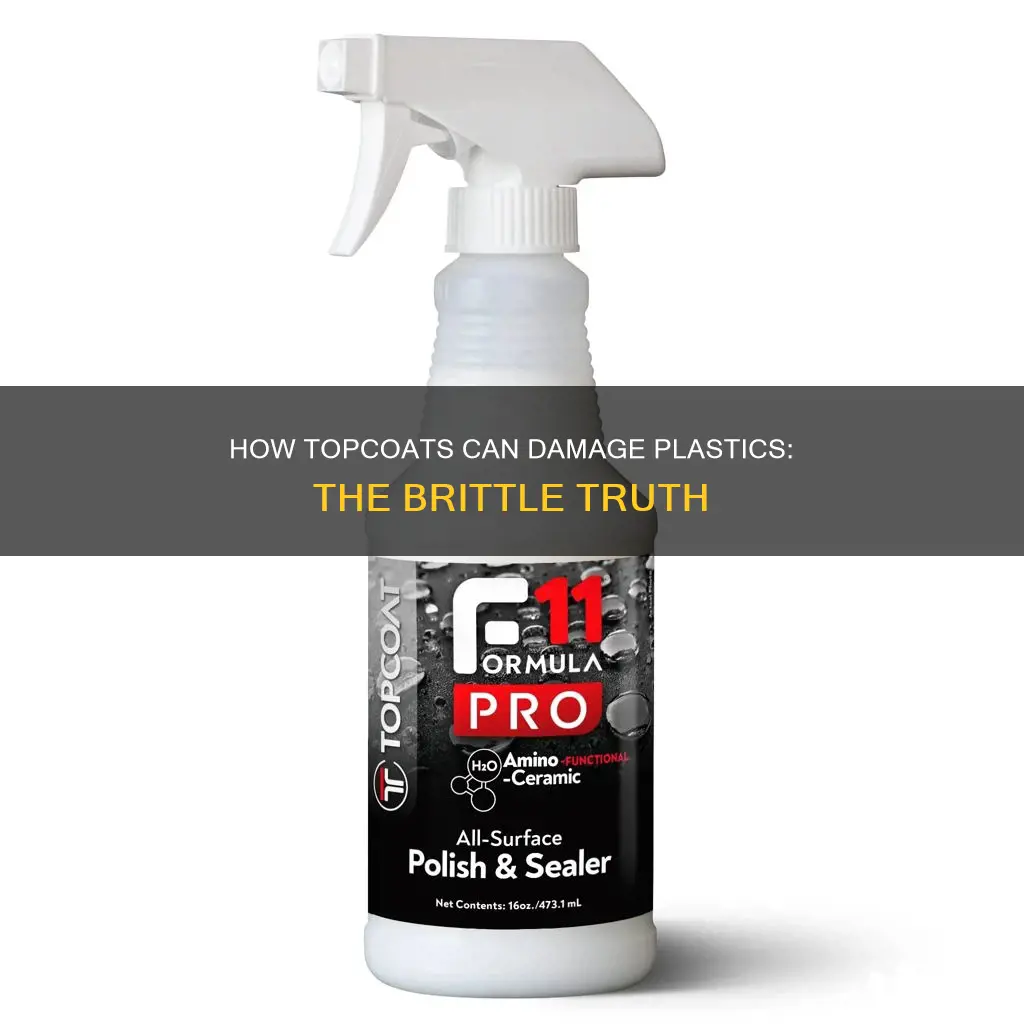
Lacquer-based topcoats can make plastic brittle, but acrylic-based topcoats are a good alternative. This is because an over-exposure to lacquer thinner can make plastic brittle. Brittleness is the tendency of a moulded plastic part to break or crack under conditions in which it would not normally do so. This can be caused by weak molecular bonds in the plastic resin molecules, which can be the result of an injection screw with too low a compression ratio.
Characteristics | Values |
---|---|
Lacquer topcoats | Can make plastic brittle |
Lacquer thinner | Over exposure can make plastic brittle |
Injection screw | A low compression ratio can cause weak bonding of plastic resin molecules, making plastic brittle |
Gates and runners | If too small, they can cause weak molecular bonding, making plastic brittle |
What You'll Learn
Lacquer thinner can make plastic brittle
Brittleness in plastic can be defined as the tendency of a moulded plastic part to break or crack under conditions in which it would not normally do so. At times, the part may also shatter. Some common causes of brittleness in plastic include an injection screw with too low a compression ratio, which does not properly mix and melt the material, and gates and runners that are too small, which cause restrictions to the flow of molten plastic. This results in weak molecular bonding and causes the moulded parts to be brittle.
To avoid making plastic brittle, it is recommended to use an acrylic-based topcoat instead of a lacquer-based one.
The Ocean's Daily Rubbish Crisis: An Environmental Catastrophe
You may want to see also
Weak molecular bonds cause plastic to be brittle
It seems that too much topcoat can make plastic brittle. Lacquer-based topcoats, in particular, can cause brittleness in plastic due to overexposure to lacquer thinner.
Brittleness in plastic is caused by weak molecular bonds. This can occur when the material is not properly mixed or melted during the moulding process, resulting in weak bonding of individual plastic resin molecules. The weak molecular bonds cause the moulded part to be brittle and more prone to breaking or cracking.
Gates and runners that are too small can also cause weak molecular bonding and brittleness in plastic parts. These restrictions cause the material to heat up due to shearing friction, leading to thermal degradation and weak molecular bonds.
To prevent brittleness in plastic parts, it is important to ensure proper mixing and melting of the material during the moulding process. This can be achieved by using an injection screw with the correct compression ratio. Additionally, ensuring that the gates and runners are the optimum size and shape for the specific part being moulded can help prevent weak molecular bonding and brittleness.
The Ocean's Daily Trash Intake: A Global Crisis
You may want to see also
Injection screws with a low compression ratio can cause weak molecular bonds
Lacquer-based topcoats can make plastic brittle. This is due to an overexposure to lacquer thinner.
Injection Screws with a Low Compression Ratio
An injection screw with a low compression ratio will not properly mix and melt the material. This results in weak bonding of individual plastic resin molecules. The weak molecular bonds cause the moulded part to be brittle. The solution is to use an injection screw with the proper compression ratio.
The compression ratio is the ratio of the flighted length of the screw divided by its nominal outside diameter. Injection screws usually use a 20:1 L/D ratio. Ensuring that the L/D ratio is correct is essential to maintaining high plastic component quality.
If the compression ratio is too high, the plastic will scorch or become too molten, and the final parts will warp. If the ratio is too low, the plastic will not be properly mixed and melted, resulting in weak molecular bonds and brittleness.
Other causes of weak molecular bonds include increasing the injection pressure, screw speed, and/or injection fill rate beyond recommendations for specific materials, which results in thermal degradation of the plastic through increased shear heat. Gates and runners that are too small will also cause weak molecular bonding due to restrictions to the flow of molten plastic.
Plastic Mold Cost: Understanding the Price of Molding
You may want to see also
Gates and runners that are too small can cause weak molecular bonds
Lacquer topcoats can make plastic brittle, as an overexposure to lacquer thinner can cause this effect.
Brittleness is the tendency of a moulded plastic part to break or crack under conditions in which it would not normally do so. Weak molecular bonds are a common cause of brittleness.
Gates and runners that are too small will cause restrictions to the flow of molten plastic. This restriction causes the material to heat up due to shearing friction, which will cause thermal degradation and weak molecular bonding. This will, in turn, cause the moulded parts to become brittle.
The solution is to examine the gates and runners and, if possible, perform a computer simulation to determine the optimum size and shape of the runner and gate for the specific part being moulded. It is important to note that too large a gate and runner is just as detrimental as too small a gate and runner.
The gate depth is also important, as if it is too deep, the packing phase will take longer than necessary. It is best to start with a shallow gate depth and increase it if the injection pressure is excessively high or if the parts have some sink or burn marks.
The Cost of Making Plastic: Understanding the Price Breakdown
You may want to see also
Too much topcoat can cause thermal degradation
Brittleness is the tendency of a moulded plastic part to break or crack under conditions in which it would not normally do so. At times, the part may also shatter. One cause of this is weak molecular bonds, which can be caused by an injection screw with too low a compression ratio. This results in weak bonding of individual plastic resin molecules. The weak molecular bonds cause the moulded part to be brittle.
Another cause of weak molecular bonds is gates and runners that are too small, which cause restrictions to the flow of molten plastic. These restrictions cause the material to heat up due to shearing friction and the material will thermally degrade. This results in weak molecular bonding and causes the moulded parts to be brittle.
Thermal barrier coatings (TBCs) are one of the best and most economical approaches to preventing the degradation of metal-based structures from high temperatures. A thermally grown oxide layer comes between the bonded coat and the outer layer (topcoat) to prevent oxidation and corrosion. The adhesion of this layer to the metal surface is essential to avoid premature failures of the TBC system. This layer should be stress-free and stable.
The most important cause of TBC spallation failure is the growth of the thermally-grown oxide (TGO) layer, which causes a compressive growth stress associated with volume expansion. Other failure mechanisms include thermal shock, sintering of the top coat, mechanical rumpling of the bond coat during thermal cyclic exposure (especially coatings in aircraft engines), accelerated oxidation at high temperatures, hot corrosion, and molten deposit degradation.
The World's Annual Waste Production: A Troubling Overview
You may want to see also
Frequently asked questions
Yes, too much topcoat can make plastic brittle. This is due to an overexposure to lacquer thinner.
Plastic can become brittle due to weak molecular bonds. This can be caused by an injection screw with too low a compression ratio, which does not properly mix and melt the material.
Weak molecular bonds can cause the plastic to break or crack under conditions in which it would not normally do so.
To prevent weak molecular bonds, ensure that the gates and runners are not too small, as this will cause restrictions to the flow of molten plastic.