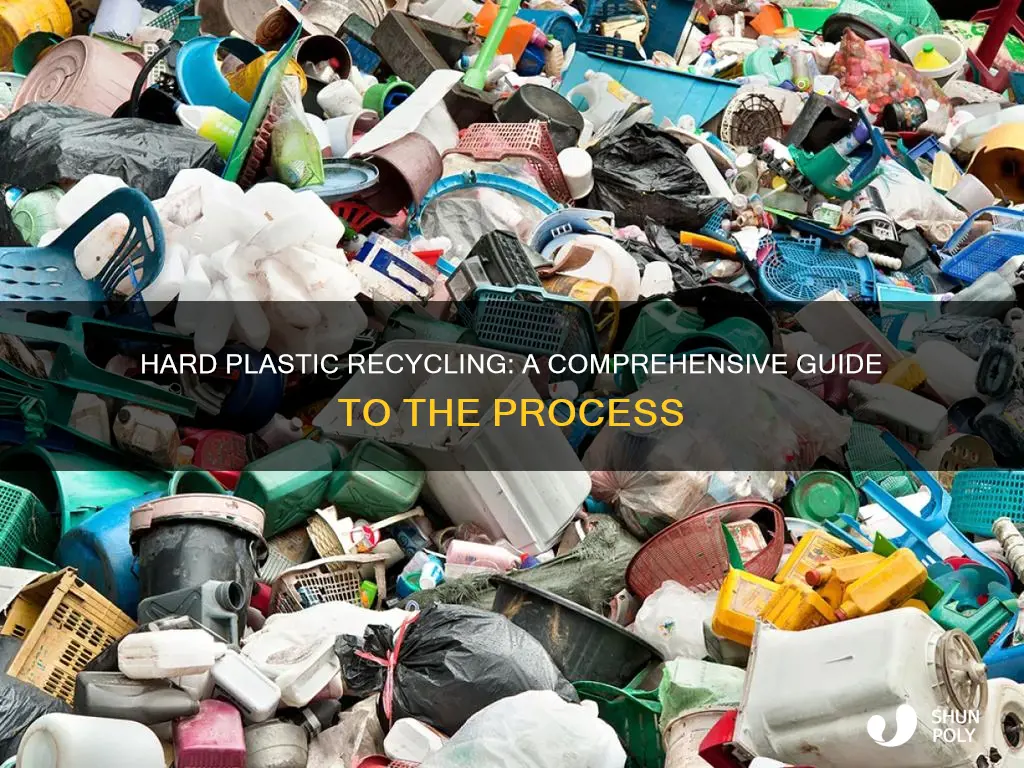
Hard plastics recycling is a crucial process in managing waste and reducing environmental impact. It involves transforming used plastic items into new materials, ensuring a sustainable approach to waste management. This process begins with the collection of hard plastics, such as those found in packaging, containers, and various household items. The collected plastics are then sorted based on their type and color to ensure efficient recycling. After sorting, the plastics undergo cleaning and shredding to break them down into smaller pieces. These shredded plastics are melted and processed to create new products like pellets or granulates, which can be used in manufacturing various items, from new packaging to construction materials. Understanding the recycling process for hard plastics is essential for promoting a circular economy and minimizing the environmental footprint of plastic waste.
What You'll Learn
- Collection: Sorting and collecting hard plastics from various sources
- Cleaning: Removing contaminants and debris from collected plastic waste
- Shredding: Breaking down hard plastics into small pieces or flakes
- Melting: Heating and transforming plastic flakes into a molten state
- Molding: Forming recycled plastic into new products through injection or blow molding
Collection: Sorting and collecting hard plastics from various sources
The first step in the recycling process of hard plastics is the collection and sorting phase, which is crucial for the efficiency and success of the entire recycling program. This stage involves gathering hard plastic materials from various sources and organizing them in a structured manner to facilitate the recycling process.
Collection centers or facilities are set up to receive hard plastics from households, businesses, and public spaces. These centers often have designated bins or containers labeled with specific types of hard plastics, such as PET (polyethylene terephthalate) bottles, HDPE (high-density polyethylene) containers, and PVC (polyvinyl chloride) pipes. Educating the public about the importance of proper waste segregation is essential to ensure that hard plastics are directed to the correct collection points.
When collecting hard plastics, it is important to consider the source and condition of the materials. For instance, PET bottles from beverage containers are highly recyclable and can be processed into new products. Similarly, HDPE containers, commonly used for milk and detergent bottles, are valuable for recycling. On the other hand, PVC pipes, often found in construction and plumbing, require specialized recycling processes due to their unique chemical composition.
During the collection process, it is crucial to maintain a clean and organized system. Contaminated or mixed plastics can compromise the recycling process and reduce the quality of the recycled material. Therefore, proper sorting and cleaning of hard plastics are essential. Sorting can be done manually or through automated systems, where machines separate plastics based on their type and color.
After collection and sorting, the hard plastics are prepared for the next stage of recycling, which may involve further processing, such as shredding or melting, to create new products or raw materials for manufacturing. This initial collection and sorting step is fundamental to the entire recycling chain, ensuring that hard plastics are managed effectively and contribute to a sustainable circular economy.
Unraveling the Mystery: Which Plastics Can Be Recycled?
You may want to see also
Cleaning: Removing contaminants and debris from collected plastic waste
The initial step in the recycling process for hard plastics is cleaning, which is crucial to ensure the quality of the recycled material. This process involves removing contaminants and debris from the collected plastic waste, which can significantly impact the efficiency and effectiveness of the recycling procedure. Here's a detailed guide on how this cleaning process is carried out:
Sorting and Separation: The first line of defense in cleaning hard plastics is proper sorting and separation. Plastic waste is often collected from various sources, including households, businesses, and recycling centers. During collection, it is essential to separate different types of plastics to facilitate the cleaning process. Common types of hard plastics include PET (polyethylene terephthalate), HDPE (high-density polyethylene), and PVC (polyvinyl chloride). Each type of plastic has unique properties and may require specific cleaning methods. For instance, PET bottles are widely used for beverages and can be identified by their resin identification code (1). HDPE, often found in milk jugs and shampoo bottles, is coded as 2. PVC, used in pipes and construction materials, is coded as 3. Proper sorting ensures that each type of plastic is handled appropriately, making the cleaning process more efficient.
Physical Cleaning Techniques: After sorting, physical cleaning methods are employed to remove contaminants. This step involves several techniques:
- Screening and Sieving: Large debris, such as pieces of metal, glass, or other plastics, can be removed through screening and sieving processes. Vibrating screens or sieves are used to separate contaminants based on size, ensuring that only clean plastic particles remain.
- Washing: Cleaning hard plastics often involves washing to eliminate dirt, labels, and other attached materials. This can be done using various washing systems, such as gravity-fed washing machines or water flotation systems. The washing process helps to break down and remove any non-plastic substances, making the material cleaner and more suitable for recycling.
- Air Classifying: This method utilizes air currents to separate light and heavy materials. Contaminants like paper, cardboard, or lightweight plastic bags can be separated from the plastic particles, ensuring a more thorough cleaning process.
Chemical Cleaning: In some cases, chemical cleaning may be necessary to remove stubborn contaminants. This process involves using specific chemicals to dissolve or break down certain substances. For instance, oils and greases can be removed using organic solvents, while more complex contaminants might require specialized chemical treatments. It is crucial to handle chemical cleaning with care, following safety protocols to ensure the well-being of workers and the environment.
Drying and Preparation: After cleaning, the plastic waste must be thoroughly dried to remove any moisture. Moisture can lead to mold growth and affect the recycling process. Drying can be achieved through various methods, including air drying, using industrial dryers, or even specialized drying chambers. Once dry, the cleaned and sorted plastic materials are ready for the next stage of recycling, where they will be processed into new products.
The cleaning process is a critical aspect of hard plastic recycling, ensuring that the final recycled product meets quality standards and can be utilized in various industries. By employing these cleaning techniques, recycling facilities can produce high-quality recycled materials, contributing to a more sustainable and environmentally friendly approach to waste management.
Master the Art of Plastic Recycling: A DIY Guide
You may want to see also
Shredding: Breaking down hard plastics into small pieces or flakes
Shredding is a crucial step in the recycling process for hard plastics, as it prepares the material for further processing and ensures efficient recovery of valuable resources. This method involves breaking down large plastic items or sheets into smaller, more manageable pieces, which can then be sorted, cleaned, and potentially sold to manufacturers for new product creation. The shredding process is designed to handle a variety of hard plastics, including those commonly found in packaging, automotive parts, and consumer goods.
The shredding process typically begins with the collection of hard plastics from various sources, such as recycling centers, manufacturing facilities, or directly from consumers. These plastics are then sorted based on their type and color to ensure proper recycling. Once sorted, the plastics are fed into a shredding machine, which can vary in design depending on the specific requirements and scale of the operation. Some shredders use rotating blades to cut the plastics into thin strips or flakes, while others employ a combination of cutting and crushing mechanisms to achieve the desired particle size.
The shredding machine's blades are carefully calibrated to produce a consistent and controlled output. This is crucial because the size and shape of the shredded plastic pieces will influence the subsequent recycling steps. Smaller flakes, for example, might be more suitable for creating new products like composite materials or pellets, while larger pieces could be used for applications requiring more substantial plastic fragments. The shredded plastic is then conveyed through the machine, often with the aid of a conveyor belt, to ensure a continuous and efficient process.
After shredding, the plastic flakes are typically separated from any remaining contaminants, such as non-plastic materials or debris. This separation is often achieved through a combination of screening, washing, and drying processes. Screening helps to remove larger impurities, while washing and drying ensure that the plastic flakes are clean and free from any residual contaminants. The cleaned plastic flakes are then ready for further processing, such as compounding or pelletizing, which transforms them into a form suitable for manufacturing new products.
In summary, shredding is a vital step in the recycling of hard plastics, enabling the material to be reduced to a manageable size and prepared for subsequent processing. This method ensures that the plastic can be effectively sorted, cleaned, and potentially sold to manufacturers, contributing to a circular economy and the sustainable use of resources. By employing specialized shredding machines and following proper sorting and cleaning procedures, the recycling process can be optimized, making it more efficient and environmentally friendly.
The Surprising Truth: What Happens to Your Single Plastic Item?
You may want to see also
Melting: Heating and transforming plastic flakes into a molten state
The process of recycling hard plastics begins with the collection and sorting of these materials, ensuring they are free from contaminants. Once sorted, the hard plastics are typically shredded or granulated to reduce their size and facilitate further processing. This initial step is crucial as it prepares the plastic for the subsequent stages of recycling.
One of the primary methods for recycling hard plastics is melting, a process that involves heating the shredded or granulated plastic to a molten state. This technique is employed to transform the solid plastic flakes into a liquid form, which can then be molded or shaped into new products. The melting process requires precise temperature control to ensure the plastic's chemical composition remains intact. Typically, the plastic flakes are heated to temperatures ranging from 200°C to 300°C (392°F to 572°F), depending on the type of plastic being processed. This high-temperature environment causes the plastic molecules to break free from their original structure and rearrange, forming a new, molten state.
During the melting process, the plastic flakes are often agitated or mixed to ensure even heating and to prevent the formation of large, uneven molten masses. This mixing can be achieved through various methods, such as using mechanical agitators or specialized heating equipment designed to distribute heat uniformly. The goal is to create a consistent molten plastic that can be easily molded or extruded into various shapes and forms.
Once the plastic reaches the desired molten state, it can be poured into molds or fed into an extruder, a machine that shapes the molten plastic into specific profiles or forms. This stage allows for the creation of a wide range of products, including new plastic containers, automotive parts, and even construction materials. The molten plastic is then cooled and solidified, either in the mold or through a cooling process, to form the final recycled product.
The melting process is a critical step in hard plastic recycling, as it enables the transformation of waste materials into valuable resources. By heating and reshaping the plastic flakes, recyclers can create new products, reducing the demand for virgin plastic production and contributing to a more sustainable and circular economy. This method of recycling is particularly important for hard plastics, which are known for their durability and resistance to heat, making them suitable for various industrial and consumer applications.
Microwaveable Plastic: Unlocking the Mystery of Its Recycling Potential
You may want to see also
Molding: Forming recycled plastic into new products through injection or blow molding
The process of recycling hard plastics and transforming them into new products is a fascinating journey that involves several stages, with molding being a crucial step. Molding is a manufacturing process that utilizes heat and pressure to shape recycled plastic into various forms, creating new products with diverse applications. This method is particularly effective for hard plastics, which are known for their durability and strength.
Injection molding is one of the most common techniques used in this process. It involves heating the recycled plastic material until it becomes a molten state, then injecting it into a mold cavity under high pressure. The mold is typically made of metal and designed with a specific shape to create the desired product. As the plastic cools and solidifies, it takes the form of the mold, resulting in a precise and consistent product. This method is highly versatile and can produce a wide range of items, from small components to large machinery parts. The process begins with collecting and sorting hard plastic waste, ensuring it is clean and free from contaminants. The sorted plastic is then shredded or granulated into small pieces, making it easier to handle and process. These plastic flakes are further cleaned and dried to remove any remaining impurities.
Once the plastic is prepared, it is fed into the injection molding machine. The machine's barrel is heated to melt the plastic, and a plunger is used to inject the molten material into the mold. The mold is then closed, and the plastic is cooled and solidified under controlled conditions. After a set period, the mold opens, revealing the newly formed product. This process can be repeated multiple times, allowing for the mass production of items with consistent quality.
Blow molding, another popular molding technique, is particularly useful for creating hollow objects. It involves two main stages: the parison stage and the blow stage. In the parison stage, a heated plastic tube, known as a parison, is created by injecting molten plastic into a mold. This parison is then transferred to the blow station, where it is expanded to take the shape of the mold. The mold is typically open at one end, allowing the parison to be inflated. As the plastic cools, it forms a hollow object, such as a bottle or a container. This method is energy-efficient and can produce lightweight, hollow products with excellent structural integrity.
Both injection and blow molding offer unique advantages in recycling hard plastics. Injection molding provides precise control over the product's dimensions and is ideal for creating intricate shapes and detailed designs. It is commonly used for manufacturing automotive parts, electronics enclosures, and consumer goods. On the other hand, blow molding is excellent for producing large, hollow items like bottles, containers, and even furniture. This process can handle a wide range of plastic types and is known for its efficiency and cost-effectiveness.
In summary, molding plays a vital role in the recycling and transformation of hard plastics. Through injection and blow molding techniques, recycled plastic can be shaped into new products with various applications. These processes ensure that hard plastics are given new life, reducing waste and contributing to a more sustainable future. With advancements in technology, the recycling industry continues to explore innovative ways to utilize and repurpose these materials, driving the circular economy forward.
Unraveling the Mystery: Can Plastic Blocks Be Recycled?
You may want to see also
Frequently asked questions
Recycling hard plastics involves a series of steps to process and transform used plastic items into new materials. It typically begins with the collection of plastic waste, which is then sorted based on the type of plastic (e.g., PET, HDPE, PVC). The sorted plastics are cleaned to remove contaminants and impurities. After cleaning, the plastics are shredded or granulated into small pieces or pellets. These plastic flakes or pellets are then melted and molded into new products or used as raw materials for manufacturing.
Identifying the type of hard plastic is crucial for proper recycling. Common types of hard plastics include Polyethylene Terephthalate (PET), High-Density Polyethylene (HDPE), Polyvinyl Chloride (PVC), and Polypropylene (PP). PET is often used in beverage bottles and can be identified by the recycling symbol #1. HDPE is found in milk jugs and detergent bottles, marked with #2. PVC is used in construction materials and has the symbol #3. PP is used in food containers and has the symbol #5. Proper identification ensures that the recycling process is efficient and effective.
Recycling hard plastics can present several challenges. One major issue is the potential for contamination, as hard plastics can be mixed with other materials or have non-plastic components attached. This contamination can make the recycling process more complex and may lead to lower-quality recycled products. Additionally, some hard plastics, like PVC, can release toxic chemicals during processing, requiring careful handling and specialized equipment. Another challenge is the lack of standardized recycling systems, making it difficult to ensure the proper disposal and processing of all types of hard plastics.
Yes, researchers and companies are exploring innovative approaches to recycle hard plastics more effectively. One such method is chemical recycling, which involves breaking down plastic polymers into their original monomers or building blocks using chemical processes. This allows for the creation of high-purity recycled materials that can be used in various applications. Another innovative technique is the use of enzymes to degrade certain types of plastics, offering a more sustainable and environmentally friendly recycling solution. These advancements aim to improve the efficiency and sustainability of hard plastic recycling processes.