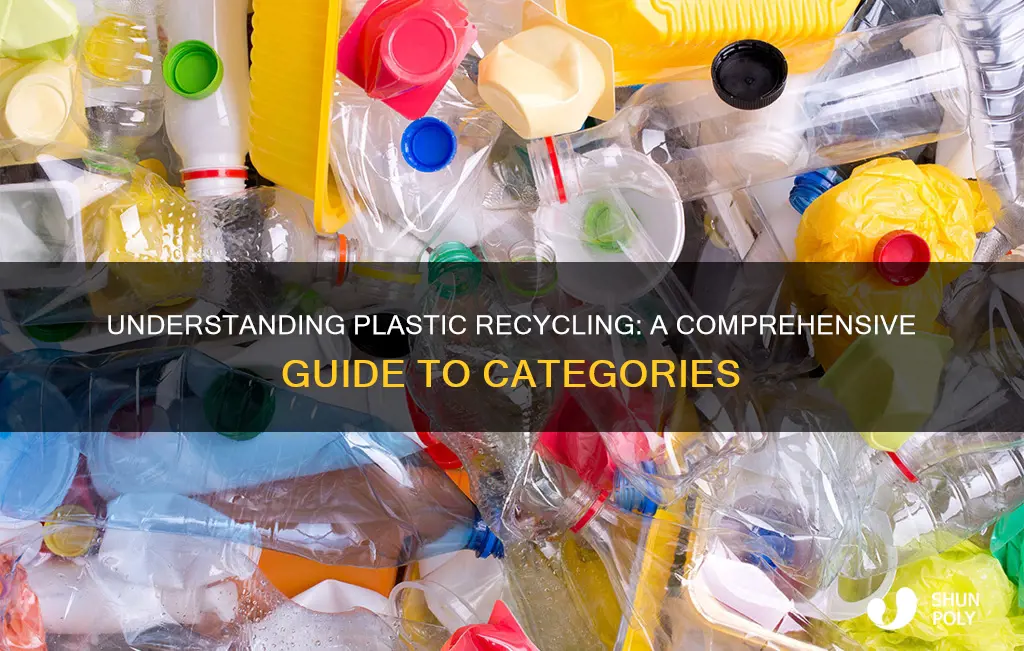
Plastics are a diverse group of materials, and their recycling process is complex. They are categorized into several types based on their chemical composition and properties, which is crucial for effective recycling. These categories include thermoplastics, thermosets, and elastomers, each with unique characteristics that determine their recyclability and the methods used to process them. Understanding these categories is essential for optimizing recycling practices and ensuring that plastic waste is managed sustainably.
Characteristics | Values |
---|---|
Resin Identification Code (RIC) | A numerical code (1-7) used to identify the type of plastic. 1: PET (polyethylene terephthalate), 2: HDPE (high-density polyethylene), 3: PVC (polyvinyl chloride), 4: LDPE (low-density polyethylene), 5: PP (polypropylene), 6: PS (polystyrene), 7: Other (e.g., polycarbonate, bioplastics). |
Melt Index (MI) | Measures the flow characteristics of plastic. Higher MI indicates easier flow and processing. |
Density | Plastics can be categorized based on their density, often measured in grams per cubic centimeter (g/cm³). Lighter plastics like polypropylene (0.89-0.92 g/cm³) and heavier ones like polycarbonate (1.22 g/cm³). |
Color | While not a primary factor, color can influence recycling processes. Some colors may be more challenging to process due to impurities or dyes. |
Chemical Composition | Different plastics have distinct chemical structures, affecting their recyclability. For example, PET is highly recyclable, while polystyrene (PS) can be challenging due to its expanded form and potential contamination. |
Processability | Some plastics are easier to process in recycling facilities due to their melt temperature, flow properties, and compatibility with other materials. |
End-Use Applications | The intended use of the recycled plastic can influence categorization. For instance, food-grade plastics have stricter requirements for purity. |
Market Demand | The availability of markets for specific recycled plastics can impact their categorization and collection. |
Geographic Location | Recycling systems and accepted plastics can vary by region due to local regulations and infrastructure. |
Contamination | Plastics with high contamination levels (e.g., food residue, labels) may be sorted into different streams for specialized processing. |
What You'll Learn
- Resin Identification Code: Plastic types are identified by a number (1-7) on the bottom of the item
- Color and Contamination: Sorting by color and removing contaminants is crucial for efficient recycling
- Density and Melting Point: Different plastics have distinct density and melting points, aiding in separation
- Chemical Composition: Analyzing the chemical structure helps determine the recyclability and processing methods
- Market Demand: Understanding the demand for recycled plastics influences the categorization and processing process
Resin Identification Code: Plastic types are identified by a number (1-7) on the bottom of the item
The Resin Identification Code, often referred to as the 'resin number' or 'resin identification code', is a system used to identify different types of plastic. This code is a numerical value ranging from 1 to 7, which is typically found on the bottom of plastic products, often in the form of a small triangle or symbol. It was introduced to help consumers and recycling facilities understand the type of plastic they are dealing with, which is crucial for proper recycling and waste management.
Each number corresponds to a specific type of plastic resin, and this classification is essential for recycling processes. For instance, when you see a number 1, it indicates that the plastic is made from Polyethylene Terephthalate (PET), which is commonly used in beverage bottles. Similarly, number 2 represents High-Density Polyethylene (HDPE), often found in milk jugs and some shampoo bottles. These codes ensure that the recycling process is efficient and effective, as different types of plastics require specific recycling methods.
Understanding these codes is vital for both consumers and recycling centers. Consumers can use the Resin Identification Code to make informed decisions about the items they use and dispose of, ensuring they are recycling the right plastics in the right way. Recycling facilities can also use these codes to sort and process plastics efficiently, optimizing the recycling process.
The system provides a standardized way to communicate the plastic type, which is especially important in the recycling industry. It allows for better organization and management of the vast array of plastic materials that are collected and processed daily. By having a universal language for plastic identification, the recycling process becomes more streamlined and environmentally friendly.
In summary, the Resin Identification Code is a simple yet powerful tool that plays a significant role in the proper categorization and recycling of plastics. It empowers individuals and recycling facilities to make informed choices, contributing to a more sustainable approach to waste management. Knowing these codes can help ensure that your plastic waste is recycled correctly, promoting a healthier environment.
BIC White-Out EZcorrect Plastic Case: Can It Be Recycled?
You may want to see also
Color and Contamination: Sorting by color and removing contaminants is crucial for efficient recycling
The process of recycling plastics is a complex task that requires careful categorization and sorting to ensure efficiency and effectiveness. One critical aspect of this process is the sorting of plastics by color and the removal of contaminants. This step is essential as it directly impacts the quality and marketability of the recycled materials.
Color sorting is a fundamental practice in plastic recycling facilities. Different colors of plastic often have distinct chemical compositions and are used in various applications. For instance, clear plastics like PET (polyethylene terephthalate) are commonly used for beverage bottles, while black plastics, such as those found in electronic devices, are made from different polymers. By sorting plastics by color, recyclers can group materials with similar properties, making the recycling process more streamlined. This practice also helps to prevent the mixing of incompatible plastics, which could lead to decreased product quality.
Contaminants, such as labels, caps, and other non-plastic materials, pose significant challenges in plastic recycling. These items can interfere with the recycling process and reduce the value of the final product. For example, a plastic bottle with a metal cap and a label made of paper or glue cannot be recycled together. The metal and paper contaminants must be removed to ensure the purity of the plastic resin. To address this issue, advanced sorting techniques are employed, including optical sorters that can identify and separate different colors of plastics and mechanical sorters that use air or water jets to separate contaminants.
The removal of contaminants is a critical step in the recycling process, as it ensures that the recycled plastics meet the required standards. Contaminants can compromise the integrity of the recycled material, leading to decreased strength, durability, and appearance. For instance, food residue on plastic containers can affect their reuse in the food industry. By removing these contaminants, recyclers can produce high-quality recycled plastics that are suitable for various applications, including manufacturing new containers, textiles, and automotive parts.
In summary, sorting plastics by color and removing contaminants are vital practices in the recycling process. These steps enable efficient recycling, improve the quality of recycled materials, and increase the likelihood of successful reuse. As the demand for sustainable practices grows, mastering these techniques will be essential in maximizing the potential of plastic recycling and contributing to a more circular economy.
Recycling Soft Plastic Tubes: Unraveling the Mystery of Their Sustainability
You may want to see also
Density and Melting Point: Different plastics have distinct density and melting points, aiding in separation
Plastics are a diverse group of materials, and their unique properties play a crucial role in the recycling process. One of the most important characteristics for recycling is the density and melting point of different plastic types. These physical properties provide a natural means of separating various plastics, making the recycling process more efficient and effective.
Density is a measure of mass per unit volume, and it varies significantly among different plastics. For instance, high-density polyethylene (HDPE) has a relatively high density, typically around 0.95 g/cm³, while polystyrene (PS) is much less dense, with a value of approximately 0.05 g/cm³. This significant difference in density allows for easy separation using mechanical methods. When plastics are sorted by density, HDPE can be collected separately from PS, ensuring that each type of plastic is processed appropriately.
Melting points are another critical factor in plastic recycling. Each plastic material has a specific temperature range at which it transitions from a solid to a liquid state. For example, polypropylene (PP) has a melting point of around 165-170°C, while polyvinyl chloride (PVC) melts at a higher temperature, typically between 150-200°C. By utilizing this property, recyclers can employ thermal methods to separate plastics. Materials with lower melting points can be melted and remolded separately from those with higher melting points, ensuring a more precise and controlled recycling process.
The density and melting point differences between plastics are nature's way of providing a built-in sorting system. This natural separation makes it easier for recyclers to handle and process different plastic types. For instance, in a recycling facility, HDPE and PS can be separated by their distinct densities, with HDPE being denser and PS being lighter. This initial separation can be followed by more specialized processes, such as melting and remolding, to create new products.
Furthermore, the density and melting point properties of plastics enable the development of innovative recycling technologies. For example, some advanced recycling systems use density-based separation techniques, where plastics are sorted into different streams based on their density. This approach ensures that each plastic type is processed according to its specific requirements, maximizing the efficiency of the recycling process.
In summary, the density and melting point characteristics of different plastics are essential for their proper categorization and recycling. These properties facilitate the separation of plastics using mechanical and thermal methods, allowing for a more organized and sustainable approach to waste management. Understanding and utilizing these natural differences can significantly contribute to the advancement of plastic recycling technologies and the overall environmental impact of plastic waste.
Unraveling the Mystery: Can Plastic Loofahs Be Recycled?
You may want to see also
Chemical Composition: Analyzing the chemical structure helps determine the recyclability and processing methods
The chemical composition of plastics is a critical factor in determining their recyclability and the appropriate processing methods. Different types of plastics are composed of various polymers, each with unique molecular structures and properties. Understanding these chemical structures is essential for effective recycling and waste management.
One way to categorize plastics is by their polymer type. Common plastic polymers include polyethylene (PE), polypropylene (PP), polyvinyl chloride (PVC), polystyrene (PS), and polycarbonate (PC). Each polymer has distinct chemical characteristics that influence its recyclability. For example, PE is known for its excellent processability and is widely used in packaging, while PP is valued for its high strength and heat resistance. PVC, on the other hand, is often used in construction due to its durability but can be challenging to recycle due to its complex chemical structure.
Analyzing the chemical composition also involves assessing the presence of additives and modifiers. These substances are added to plastics to enhance specific properties, such as color, flexibility, or stability. For instance, some plastics may contain plasticizers, which improve flexibility, or stabilizers to prevent degradation. The identification of these additives is crucial because they can impact the recyclability of the material. Some additives may interfere with the recycling process or make it more challenging to separate the plastic from contaminants.
Furthermore, the degree of polymerization and molecular weight distribution play a significant role in recyclability. Plastics with higher molecular weights and more uniform distributions are generally easier to recycle. These plastics can be more effectively processed and transformed into new products without losing their structural integrity. In contrast, plastics with lower molecular weights or uneven distributions may require specialized recycling techniques or may not be suitable for certain recycling streams.
In summary, the chemical composition of plastics is a key consideration in recycling. By understanding the polymer types, additives, and molecular structures, recycling facilities can determine the most appropriate processing methods. This knowledge enables efficient sorting, processing, and repurposing of plastics, contributing to a more sustainable waste management system. Proper categorization and analysis of chemical structures are essential steps in the recycling process to ensure the effective utilization of resources and minimize environmental impact.
Unveiling the Energy Cost: Recycling vs. Manufacturing Plastic
You may want to see also
Market Demand: Understanding the demand for recycled plastics influences the categorization and processing process
Understanding the market demand for recycled plastics is crucial as it significantly influences how plastics are categorized and processed for recycling. The demand for recycled materials is driven by various factors, including environmental concerns, government regulations, and the growing awareness of sustainable practices among consumers and businesses. As a result, the recycling industry has seen a shift towards more stringent standards and a greater emphasis on the quality and usability of recycled plastics.
In the past, recycled plastics were often downcycled, meaning they were used to create lower-quality products, such as construction materials or outdoor furniture. However, with increasing market demand, there is a growing preference for high-quality recycled plastics that can be used in a wide range of applications, including packaging, automotive, and electronics. This shift in demand has led to the development of more advanced recycling technologies and processes that can produce materials that meet the required specifications.
The categorization of plastics for recycling is directly linked to market demand. Different types of plastics have varying levels of demand and applications. For example, PET (polyethylene terephthalate) is highly sought after for its use in beverage bottles and food packaging due to its transparency, lightweight, and food-safe properties. HDPE (high-density polyethylene), on the other hand, is commonly recycled for its use in milk jugs and detergent bottles. Understanding these demand patterns helps recycling facilities categorize plastics more effectively, ensuring that the right materials are directed to the appropriate processing streams.
Market demand also influences the processing methods employed in recycling. For instance, some recycled plastics may require additional processing steps to meet the desired quality standards. This could include cleaning, sorting, and even chemical treatments to remove contaminants or enhance properties. Advanced recycling techniques, such as chemical recycling, are gaining popularity to produce high-purity recycled plastics that can be used in sensitive applications like medical devices or electronics. These processes are designed to cater to the specific demands of various industries, ensuring that the recycled materials are valuable and usable.
Moreover, the demand for recycled plastics can vary across different regions and industries. Local markets may have unique requirements or preferences, influencing the types of plastics that are prioritized for recycling. For instance, a region with a strong automotive industry might demand a higher volume of recycled ABS (acrylonitrile butadiene styrene) for interior components. By understanding these regional variations in market demand, recycling facilities can optimize their processes and cater to specific industry needs, ensuring a more efficient and effective recycling system.
Can Plastic 3-Ring Binders Be Recycled? Unraveling the Mystery
You may want to see also
Frequently asked questions
Plastics are typically categorized into seven main types, known as the Resin Identification Codes (RICs) or the Numbered Resin System. These codes are usually found on the bottom of plastic containers and help identify the type of plastic used. The seven categories are: PET (Polyethylene Terephthalate), HDPE (High-Density Polyethylene), PVC (Polyvinyl Chloride), LDPE (Low-Density Polyethylene), PP (Polypropylene), PS (Polystyrene), and Other (a catch-all category for plastics that don't fit into the previous six).
The recycling process for each plastic category varies due to their unique chemical structures and properties. For example, PET is widely accepted in most recycling programs and can be recycled into new containers, fibers for clothing, or even liquid containers. HDPE is also commonly recycled and can be used to make new containers, furniture, and even outdoor equipment. PVC, due to its chlorine content, can be challenging to recycle and often requires specialized facilities. LDPE is flexible and can be recycled into items like grocery bags, bin liners, and some durable goods. PP is heat-resistant and can be recycled into food containers, brooms, and even automotive parts. PS is often used for disposable cups and food containers and can be recycled into new packaging or insulation.
Not all plastics are recyclable, and the recyclability depends on various factors, including the type of plastic, local recycling infrastructure, and market demand for recycled materials. For instance, while PET and HDPE are widely accepted, materials like polystyrene (PS) and certain types of PVC might have limited recycling options due to their complexity or specialized processing requirements. Additionally, mixed-material items, such as plastic straws with a different resin attached, can be challenging to recycle and may require specialized sorting processes.
Recycling symbols and labels, often found on the bottom of plastic containers, provide a standardized way to identify the type of plastic used. These symbols typically consist of a number inside a triangle, known as the Resin Identification Code (RIC). For example, a PET bottle will have the number 1 inside the recycling symbol, while an HDPE milk jug will display the number 2. These codes help recycling facilities and consumers understand which plastics are recyclable and can be processed accordingly. It's important to note that the presence of a recycling symbol alone doesn't guarantee that an item is recyclable, as some items might not be accepted by local recycling programs.