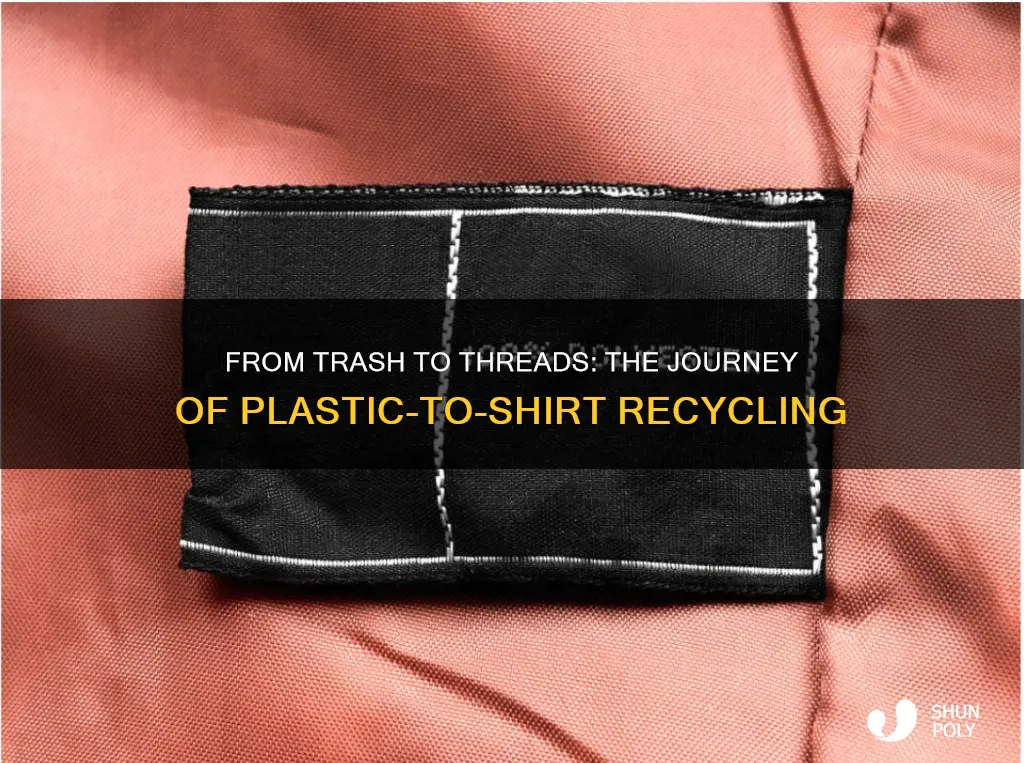
Plastics recycling has become an essential process in the fashion industry, transforming waste materials into sustainable clothing items. One innovative method involves the creation of shirts from recycled plastic bottles, a process that begins with the collection and sorting of plastic waste. These bottles are then shredded and cleaned to remove any contaminants, after which the plastic fibers are spun into yarn. The yarn is then woven or knitted into fabric, which is subsequently cut and sewn into shirts. This entire process not only reduces plastic waste but also minimizes the environmental impact of the fashion industry, offering a unique and eco-friendly alternative to traditional clothing production.
What You'll Learn
- Collection: Plastic waste is gathered from various sources, ensuring it's clean and sorted
- Shredding: Plastic is broken down into small flakes, a process called shredding
- Cleaning: Flakes are washed to remove contaminants, ensuring quality
- Melting: Cleaned flakes are melted into a liquid state for molding
- Spinning: Liquid plastic is extruded into fibers, then woven into fabric for shirts
Collection: Plastic waste is gathered from various sources, ensuring it's clean and sorted
The first step in the journey of transforming plastic waste into shirts is the collection process, which is a critical phase in ensuring the quality and efficiency of the recycling process. Plastic waste, in its various forms, is gathered from multiple sources, including residential areas, commercial establishments, industrial sites, and public spaces. This comprehensive collection effort aims to capture a wide range of plastic materials, such as bottles, containers, packaging, and other plastic items that are commonly discarded.
To ensure a clean and sorted collection, waste management teams employ several strategies. Firstly, public awareness campaigns play a vital role in educating communities about the importance of proper waste segregation. These campaigns encourage residents to separate their plastic waste into different categories, such as PET (polyethylene terephthalate), HDPE (high-density polyethylene), and other types of plastics. By providing clear guidelines and instructions, the goal is to facilitate an organized collection process.
During the collection phase, waste management personnel utilize various methods to gather plastic waste. This includes setting up designated collection points, such as recycling bins and bags, in residential areas, offices, and public spaces. These collection points are strategically placed to ensure easy access for residents and businesses, encouraging them to contribute their plastic waste. Additionally, mobile collection units, such as trucks or vans, may be employed to reach remote areas or neighborhoods with limited access to fixed collection points.
Once the plastic waste is collected, it undergoes a thorough sorting process. This step is crucial to separate different types of plastics, ensuring that only clean and sorted materials proceed to the recycling stage. Waste management experts use their knowledge and experience to identify and categorize plastics based on their resin identification codes (RICs) or types. For instance, PET bottles are separated from HDPE containers, ensuring that each type of plastic is treated appropriately. This meticulous sorting process helps to maintain the quality of the recycled materials and facilitates the production of high-quality recycled products.
In some cases, advanced sorting technologies, such as optical sorters and eddy current separators, may be employed to enhance the efficiency and accuracy of the sorting process. These machines can identify and separate plastics based on their color, shape, and material properties, further ensuring that the collected waste is clean and properly categorized. By investing in these technologies, recycling facilities can optimize their operations and produce a consistent supply of sorted plastics for the next stage of the recycling journey.
Can Hard Plastic Toothpaste Containers Be Recycled in NYC?
You may want to see also
Shredding: Plastic is broken down into small flakes, a process called shredding
The process of recycling plastic into shirts begins with a crucial step known as shredding. This initial stage is a fundamental part of the recycling journey, as it transforms plastic waste into a usable form. Shredding is a mechanical process where plastic materials are broken down into small, uniform flakes. These flakes are the building blocks for creating new products, including clothing items like shirts.
During shredding, plastic items, such as bottles, containers, or even post-consumer plastic waste, are fed into a specialized machine. These machines are designed to handle various types of plastics, ensuring a comprehensive recycling process. The waste is then subjected to intense force and pressure, reducing it to tiny fragments. This process is often facilitated by large industrial shredders that can process tons of plastic waste daily.
The shredded plastic flakes are typically around 1-2 inches in size, resembling tiny, colorful confetti. These flakes are carefully sorted and cleaned to remove any contaminants, such as dirt, labels, or non-plastic materials. This sorting process is crucial to ensure the quality and purity of the recycled plastic. After cleaning, the flakes are ready for the next stage of recycling.
The shredded plastic flakes are now ready to be transformed into a new material. This is achieved through a process called 'pelletizing,' where the flakes are heated and pressed into uniform pellets. These pellets are the final product of the shredding process and serve as the raw material for manufacturing various plastic products, including fibers for clothing.
Shredding is a critical step in plastic recycling as it prepares the material for further processing and gives it a new purpose. It is an energy-intensive process but is essential to breaking down plastic waste and making it recyclable. By shredding plastic, we can contribute to a more sustainable future, reducing the environmental impact of plastic waste and promoting the circular economy.
Unraveling the Dirt-Resistant Magic of Recycled Plastic Clothing
You may want to see also
Cleaning: Flakes are washed to remove contaminants, ensuring quality
The process of recycling plastic flakes into shirts involves a meticulous cleaning step to ensure the final product meets high-quality standards. After the initial collection and sorting of plastic waste, the next crucial phase is cleaning the plastic flakes to remove any contaminants. This step is essential as it directly impacts the quality and durability of the recycled material.
Cleaning begins with a thorough washing process. The plastic flakes are fed into a washing machine or a specialized cleaning system designed for this purpose. The machine uses a combination of water and sometimes a mild detergent to remove any dirt, debris, or impurities that may be present on the flakes. This process helps to ensure that the plastic is clean and free from any unwanted substances that could affect its performance in the final product.
During the washing cycle, the machine's agitation helps to dislodge and wash away contaminants. It is important to use the right amount of water and cleaning agents to avoid any damage to the plastic flakes. Over-washing or using harsh chemicals can lead to degradation of the plastic, so a careful balance must be maintained. The goal is to create a clean and pure environment for the subsequent steps of recycling.
After the washing process, the plastic flakes are typically rinsed thoroughly to remove any remaining detergent or residue. This step ensures that no chemical traces remain, which could potentially affect the material's properties. The cleaned flakes are then carefully dried to eliminate any moisture, as wet plastic can lead to mold or other quality issues.
Quality control is an integral part of this cleaning process. Samples of the cleaned plastic flakes are regularly tested to ensure they meet the required standards. This includes checking for the absence of contaminants, verifying the plastic's purity, and assessing its overall condition. By implementing this rigorous cleaning procedure, the recycled plastic can be transformed into high-quality materials, such as fibers for clothing, ensuring a sustainable and environmentally friendly approach to fashion production.
Unraveling the Mystery: Understanding Plastic Recycling Codes
You may want to see also
Melting: Cleaned flakes are melted into a liquid state for molding
The process of recycling plastic into shirts begins with the collection and sorting of plastic waste. Once the plastic is sorted, the next step is to clean the plastic flakes to remove any contaminants. This is crucial to ensure the quality of the final product. After cleaning, the plastic flakes are then melted into a liquid state using specialized machinery. This process requires precise temperature control to ensure the plastic is melted evenly and thoroughly. The melted plastic is then ready for molding.
Melting is a critical step in the recycling process as it transforms the solid plastic flakes into a usable form. The melted plastic is often in a large, uniform batch, which is then ready to be shaped into the desired form, such as a shirt. The temperature and duration of the melting process are carefully monitored to maintain the integrity of the plastic and prevent any degradation.
In the molding stage, the melted plastic is poured into molds that have been designed to create the specific shape of the shirt. These molds can be of various sizes and styles, depending on the desired outcome. The plastic is then allowed to cool and solidify within the mold, taking on the shape of the shirt. This process is repeated for each shirt to be produced.
The molding process can be done in two main ways: injection molding and blow molding. In injection molding, the melted plastic is injected into a closed mold, where it cools and solidifies. This method is often used for producing solid, uniform pieces. On the other hand, blow molding is used for creating hollow objects, such as the sleeves and body of a shirt, by inflating the plastic within the mold.
After the plastic has been molded, the shirts are carefully removed from the molds and inspected for quality. Any defects or imperfections are identified and addressed, ensuring that the final product meets the required standards. The recycled shirts are then ready for distribution, providing a sustainable and eco-friendly alternative to traditional clothing materials.
Irvine's Plastic Recycling: A Green Revolution or a Myth?
You may want to see also
Spinning: Liquid plastic is extruded into fibers, then woven into fabric for shirts
The process of recycling plastic into shirts begins with the collection and sorting of plastic waste. This waste is then cleaned and prepared for the recycling process. The most common type of plastic used in this process is PET (polyethylene terephthalate), which is widely used in beverage bottles.
Once the plastic is sorted and cleaned, it is shredded into small pieces. These pieces are then melted and extruded through a spinneret, a device that creates small holes. As the molten plastic exits the spinneret, it is cooled and solidifies into thin strands of plastic, known as fibers. This process is called spinning and is a crucial step in transforming plastic into fabric.
The fibers produced through spinning are then wound onto bobbins, creating continuous strands of plastic. These strands are further processed to remove any impurities and ensure the fibers are of high quality. The fibers are then dyed and treated to enhance their color and durability.
After the fibers are prepared, they are woven into fabric using specialized machinery. This weaving process involves interlooping the plastic fibers to create a strong and flexible fabric. The fabric is then cut into the desired shape and size, which in this case, is a shirt.
Finally, the recycled plastic fabric is used to create shirts. These shirts are then washed, finished, and packaged for sale. The entire process, from collecting plastic waste to wearing a shirt made from recycled plastic, can significantly reduce the environmental impact of plastic production and disposal. This method of recycling not only reduces waste but also promotes sustainability and a circular economy in the textile industry.
South Bend's Plastic Recycling: A Community Effort
You may want to see also
Frequently asked questions
The process begins with collecting and sorting plastic waste, which is then cleaned and shredded into small pieces. These plastic flakes are melted and transformed into fibers, which are spun into threads and eventually woven or knitted into fabric. The fabric is then cut and sewn to create shirts.
Plastic items that are commonly recycled into shirts include water bottles, milk jugs, and detergent bottles made from PET (polyethylene terephthalate). These plastics are identified by the recycling symbol #1 or #2. It's important to rinse out containers and remove any labels or non-plastic parts before recycling.
Absolutely! Recycling plastic reduces the demand for virgin resources and decreases the amount of plastic waste that ends up in landfills or the ocean. It also helps conserve energy and water compared to producing new plastic from raw materials. By recycling, we can contribute to a more sustainable and circular economy.
No, not all plastics are suitable for recycling into shirts. The most common and widely accepted types for clothing production are PET and HDPE (high-density polyethylene). Other plastics like PVC or polystyrene may have limited recycling options and are not commonly used in the textile industry.
The recycling process involves multiple stages of cleaning, sorting, and processing to ensure the quality of the final product. Advanced technologies are used to remove contaminants and impurities from the plastic waste. The fibers produced are then tested for strength, colorfastness, and overall quality before being used to manufacture shirts.