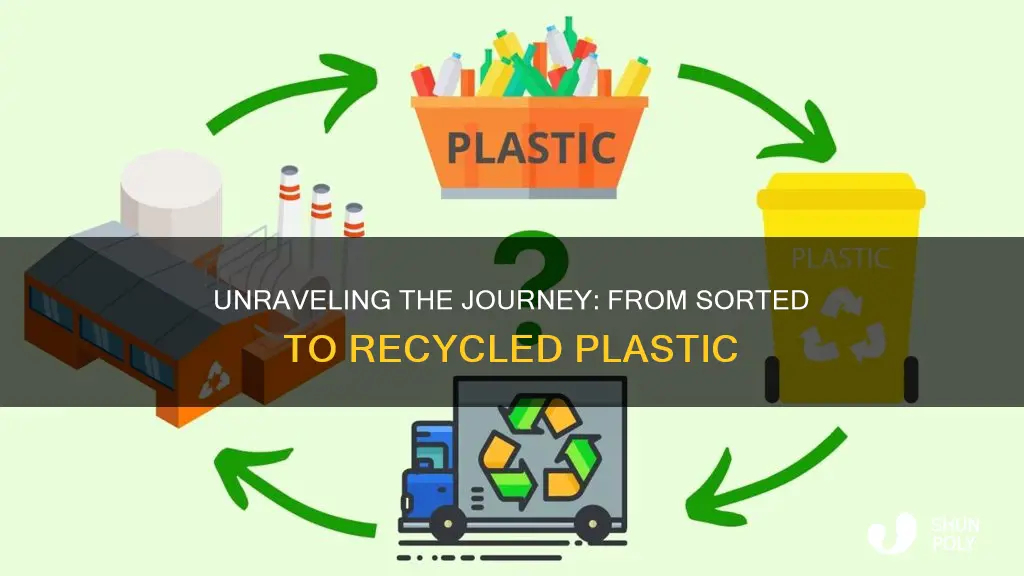
Plastics recycling is a complex process that begins with sorting different types of plastics. Once sorted, the plastics are cleaned and prepared for recycling. This involves removing any contaminants and ensuring the plastics are in a usable form. The next step is to break down the plastics into smaller pieces, which can be done through various methods such as shredding or grinding. These small pieces are then melted and molded into new products, such as plastic pellets or new containers. The final stage involves transforming these recycled materials into new products, completing the recycling loop and reducing the demand for virgin plastic production.
What You'll Learn
- Collection and Sorting: Materials are gathered and separated by type
- Shredding and Grinding: Plastic waste is reduced to flakes or pellets
- Cleaning and Sorting: Contaminants are removed to ensure purity
- Melting and Forming: Processed into new products like fibers or pellets
- Manufacturing: Recycled plastics are used in new products
Collection and Sorting: Materials are gathered and separated by type
The initial step in the plastic recycling process is the collection and sorting of plastic materials, a crucial phase that sets the foundation for efficient recycling. This process begins with the gathering of plastic waste from various sources, including residential areas, commercial facilities, and industrial sites. Waste collection is a critical aspect, as it ensures that plastic materials are not contaminated with other substances, which can compromise the recycling process. Once collected, the waste is transported to specialized facilities where the sorting process takes place.
Sorting is a meticulous task that involves separating different types of plastics based on their chemical composition and properties. This is essential because not all plastics are recyclable in the same way, and some may have different recycling methods. Common methods of sorting include manual separation, where trained workers identify and categorize plastics by their colors and types, and automated sorting systems that use advanced technologies. For instance, optical scanners can detect the color and type of plastic, while eddy current separators use electromagnetic fields to identify and separate ferrous and non-ferrous materials.
Manual sorting is a labor-intensive process and is often employed for more specialized or complex recycling streams. Workers are trained to identify various plastic types, such as PET (polyethylene terephthalate), HDPE (high-density polyethylene), PVC (polyvinyl chloride), and LDPE (low-density polyethylene), by their feel, appearance, and sometimes, by using chemical tests. Each type of plastic has unique characteristics, such as flexibility, rigidity, and melting point, which aid in their identification. For example, PET is known for its crisp feel and transparency, while HDPE is stiffer and often has a high-density feel.
Automated sorting systems, on the other hand, are designed to handle large volumes of waste efficiently. These systems use a combination of technologies, such as near-infrared (NIR) spectroscopy and X-ray fluorescence (XRF) analysis, to identify and separate plastics. NIR spectroscopy can provide detailed information about the chemical composition of plastics, allowing for precise sorting. XRF analysis is used to identify the presence of heavy metals in certain plastics, which is crucial for ensuring the safety and quality of the recycled material. These advanced technologies enable the sorting process to be faster, more accurate, and less reliant on manual labor.
The sorted plastics are then grouped into categories, such as PET bottles, HDPE containers, and PVC pipes, among others. This categorization is essential for the next stage of recycling, as different types of plastics may have specific recycling processes or end-uses. For instance, PET bottles are often recycled into polyester fibers for clothing, while HDPE containers are suitable for producing new containers or other durable goods. Proper sorting ensures that the recycling process is efficient, cost-effective, and environmentally friendly, contributing to a more sustainable approach to waste management.
Building Trump's Wall: A Green Revolution with Recycled Plastics
You may want to see also
Shredding and Grinding: Plastic waste is reduced to flakes or pellets
The process of recycling plastic waste begins with the sorting of different types of plastics, which is a crucial step to ensure the efficiency and effectiveness of the recycling process. Once sorted, the plastic waste undergoes a series of physical transformations to be transformed into reusable materials. One of the initial steps in this process is shredding and grinding, which plays a vital role in reducing the size of the plastic waste and preparing it for further processing.
Shredding is the first mechanical step in this process. Plastic waste, which can include items like bottles, containers, and even larger objects, is fed into a shredding machine. These machines are designed to cut and tear the plastic into smaller pieces, typically in the form of flakes or strips. The shredding process helps to break down the plastic items, making them easier to handle and process further. It also serves to remove any non-plastic contaminants, such as labels or caps, which can interfere with the recycling process.
After shredding, the plastic flakes are then subjected to a grinding process. Grinding involves further reducing the size of the plastic flakes by breaking them down into even smaller particles. This is often done using specialized grinding machines that can handle the unique properties of different types of plastics. The grinding process aims to create a consistent and uniform size of plastic particles, which is essential for the next stages of recycling. The ground plastic can range from fine powder to larger flakes, depending on the desired end product.
The combination of shredding and grinding is crucial as it transforms the plastic waste into a more manageable and standardized form. This step is particularly important for the production of recycled plastic pellets, which are small, uniform plastic particles. By reducing the plastic waste to flakes or pellets, the material becomes more suitable for various recycling techniques, such as injection molding, blow molding, or even creating new products like composite materials.
This initial shredding and grinding process is a fundamental step in the mechanical recycling of plastics, setting the foundation for the subsequent stages of recycling, including washing, drying, and pelletizing. It ensures that the plastic waste is prepared in a way that maximizes its potential for reuse, contributing to a more sustainable approach to plastic waste management.
The Journey of Plastic: From Waste to New Life
You may want to see also
Cleaning and Sorting: Contaminants are removed to ensure purity
The process of recycling plastics begins with the collection and sorting of plastic waste, which is a crucial step to ensure the quality and efficiency of the recycling process. Once sorted, the next critical phase is cleaning and sorting to remove contaminants and ensure the purity of the plastic materials. This step is essential as it directly impacts the recyclability and the final product's quality.
Cleaning the plastic waste is a meticulous process that involves removing any foreign matter, contaminants, and impurities. This can include food residue, labels, stickers, and other non-plastic materials that may be attached to the plastic items. For instance, single-use plastic containers often have labels and caps that need to be separated and recycled separately. These contaminants can hinder the recycling process and even render the plastic unusable if not removed. Specialized cleaning techniques are employed, such as using water jets to wash away food particles or employing air knives to remove excess moisture and debris.
Sorting the cleaned plastic materials is another vital aspect of this stage. Plastic waste is typically sorted by resin type or color to facilitate the recycling process. Resin identification codes, often seen as a small number inside the recycling symbol on plastic products, are used to categorize plastics. For example, PET (polyethylene terephthalate) is commonly used for beverage bottles and has the number 1 inside the recycling symbol. HDPE (high-density polyethylene) is used for milk jugs and has the number 2. Sorting by resin type ensures that the recycled plastics can be processed into specific products, maintaining their integrity and quality.
Advanced sorting technologies are utilized to streamline this process. Optical sorters use light to identify different colors and types of plastics based on their unique light absorption properties. These machines can separate plastics with high accuracy, ensuring that only the desired types are collected. Additionally, eddy current separators are employed to detect and separate non-magnetic materials like plastics from ferrous metals, further enhancing the purity of the sorted plastics.
After cleaning and sorting, the plastic materials are ready for the next stage of recycling, which may involve shredding, melting, or reforming into new products. This process ensures that the recycled plastics meet the required standards and can be used in various industries, contributing to a more sustainable and circular economy. Proper cleaning and sorting are fundamental to the success of plastic recycling, allowing for the creation of high-quality recycled products and reducing the environmental impact of plastic waste.
Unraveling the Mystery: Can Plastic Wrappers Be Recycled?
You may want to see also
Melting and Forming: Processed into new products like fibers or pellets
The process of recycling plastics after they have been sorted involves several steps, and one crucial phase is the melting and forming stage, where the sorted plastics are transformed into new products. This stage is a critical part of the recycling process, as it allows for the creation of new materials with various applications. Here's an overview of this process:
Once the plastics are sorted based on their types and colors, the next step is to melt them down. This is typically done using specialized equipment designed for plastic recycling. The sorted plastics are fed into a melting machine, which can vary in size and design depending on the scale of the recycling operation. In this machine, the plastics are heated to their melting point, which is a specific temperature for each type of plastic. For example, high-density polyethylene (HDPE) melts at around 129°C (264°F), while polypropylene (PP) melts at approximately 165°C (329°F). The melting process ensures that the plastic is in a liquid state, ready for further processing.
After melting, the plastic material is often cooled and solidified to form a uniform, consistent product. This can be achieved through various cooling methods, such as air cooling or water cooling, depending on the desired outcome. The solidified plastic is then cut or chopped into small pieces or pellets, which are essentially the raw materials for creating new products. These pellets are often referred to as 'reprocessed plastic' or 'recycled plastic resin'.
The next step in the recycling chain is the formation of these pellets into new products. One common method is spinning or extrusion, where the plastic pellets are heated and drawn out into thin strands or fibers. This process is used to create various textiles, such as clothing, carpets, and ropes, from recycled plastic bottles and containers. For example, PET (polyethylene terephthalate) bottles can be recycled into polyester fibers, which are then used in the textile industry.
Additionally, the melted and formed plastic can be used to produce new containers, packaging materials, and even construction materials. By adding colorants, stabilizers, and other additives during the melting process, recycled plastics can be customized for specific applications. This versatility allows for the creation of a wide range of products, ensuring that recycled plastics find new life in various industries, contributing to a more sustainable and circular economy.
Unraveling Recycling Myths: Do Labels Matter for Plastic?
You may want to see also
Manufacturing: Recycled plastics are used in new products
Once plastics are sorted and collected, the recycling process begins with the goal of transforming these materials into new products. The first step in this process is cleaning and preparing the plastic waste. This involves removing any contaminants, such as food residue, labels, or non-plastic items, to ensure the material is clean and suitable for recycling. This cleaning process is crucial as it directly impacts the quality of the final recycled product.
After cleaning, the sorted plastics are shredded or ground into small pieces, often referred to as 'flakes' or 'pellets'. This step reduces the volume of the plastic waste and prepares it for further processing. The size and shape of these flakes can vary depending on the specific recycling process and the desired end product. For example, high-density polyethylene (HDPE) bottles might be shredded into small, uniform pieces, while larger, more complex items like furniture or automotive parts may require different processing techniques.
The next stage in the manufacturing process is the actual recycling and transformation of these plastic flakes. There are several methods to achieve this, including chemical recycling, mechanical recycling, and advanced recycling techniques. Mechanical recycling is the most common and involves heating the plastic flakes to a specific temperature, then molding or extruding them into new shapes. This process is energy-intensive and often requires the addition of new plastic or other materials to create a usable product.
Chemical recycling, on the other hand, uses chemical processes to break down the plastic into its original monomers or building blocks. This method can produce high-quality recycled materials that are identical to their virgin counterparts. However, it is currently more expensive and less common due to the specialized equipment and processes required. Advanced recycling techniques, such as gasification and pyrolysis, are also being explored to convert plastic waste into valuable resources like oil and gas.
The use of recycled plastics in manufacturing has numerous benefits. Firstly, it reduces the demand for virgin plastic production, which often relies on fossil fuels and can have significant environmental impacts. By utilizing recycled materials, manufacturers can decrease their carbon footprint and contribute to a more sustainable production cycle. Additionally, recycled plastics can often be more cost-effective, especially when large volumes of waste are available, making it an economically viable option for many industries.
In summary, the manufacturing process of recycled plastics involves a series of steps, from initial sorting and cleaning to advanced recycling techniques. These processes ensure that plastic waste is transformed into new products, reducing environmental impact and promoting a circular economy. With the growing demand for sustainable solutions, the use of recycled plastics in manufacturing is becoming increasingly important and widely adopted.
Eco-Friendly Fashion: Unraveling the Environmental Impact of Recycled Plastic Clothing
You may want to see also
Frequently asked questions
After sorting, the plastic waste is processed through a series of steps to be recycled. The first step involves cleaning and removing any contaminants like food residue or non-plastic materials. This is crucial to ensure the quality of the recycled product. Then, the sorted plastics are shredded or granulated into small pieces or pellets, which are the raw materials for manufacturing new products.
Different types of plastics have unique chemical compositions and properties, so their recycling processes vary. For example, PET (polyethylene terephthalate), commonly used in beverage bottles, can be recycled into fibers for clothing or new bottles. HDPE (high-density polyethylene), found in milk jugs, can be recycled into items like outdoor furniture or new containers. PVC (polyvinyl chloride) and LDPE (low-density polyethylene) also have specific recycling streams, often requiring specialized facilities to process them effectively.
Yes, plastic recycling faces several challenges. One major issue is the lack of standardized recycling systems, making it difficult to process different types of plastics together. Additionally, some plastics are more challenging to recycle due to their chemical structure or the presence of additives. For instance, single-use plastics like shopping bags and straws often contain additives that make them unsuitable for certain recycling processes. Furthermore, the quality of recycled plastic can vary, and some materials may degrade during processing, affecting their usability in manufacturing new products.